Comprehensive Guide to Valve Components and Pump Parts
Valves and pumps are fundamental components in a wide range of industrial processes, from manufacturing and chemical processing to oil and gas, water treatment, and power generation. They regulate the flow of fluids, gases, and slurries, ensuring smooth and efficient system operation. A thorough understanding of valve components and pump parts can help optimize performance, reduce maintenance, and prevent costly downtime. This guide explores the essential components of valves and pumps, detailing their functions and significance in industrial applications.
What Are Valves and Pumps?
Valves and pumps are crucial mechanical devices that play complementary roles in fluid systems. Valves control the flow, direction, and pressure of fluids within a pipeline, while pumps move fluids through the system by adding pressure or flow. Together, they ensure that industrial systems run efficiently and safely.
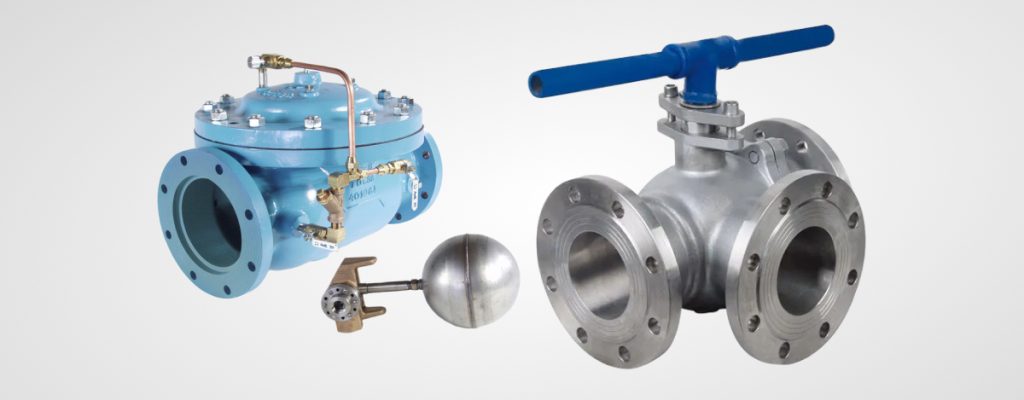
Essential Valve Components
1. Valve Body
The valve body is the main structure of the valve, housing all internal parts and providing the connection to the pipeline. It is designed to withstand internal pressure and is typically made of robust materials such as stainless steel, brass, or cast iron, depending on the application.
- Function: Holds the valve components in place and serves as the primary pressure boundary.
- Material Selection: Chosen based on factors such as fluid type, pressure, temperature, and corrosion resistance.
2. Valve Bonnet
The bonnet covers the valve body and acts as a second pressure boundary. It is often bolted or welded to the body and provides access to the internal components for maintenance or replacement.
- Function: Protects internal components and ensures the integrity of the pressure boundary.
- Material: Typically made of the same material as the valve body for compatibility.
3. Valve Stem
The stem connects the actuator (manual handle or automated actuator) to the valve disc or ball, enabling the opening and closing of the valve. The movement of the stem determines the valve’s position, controlling fluid flow.
- Function: Transmits motion from the actuator to the valve’s internal parts.
- Types of Motion: Can be linear (for gate and globe valves) or rotational (for ball and butterfly valves).
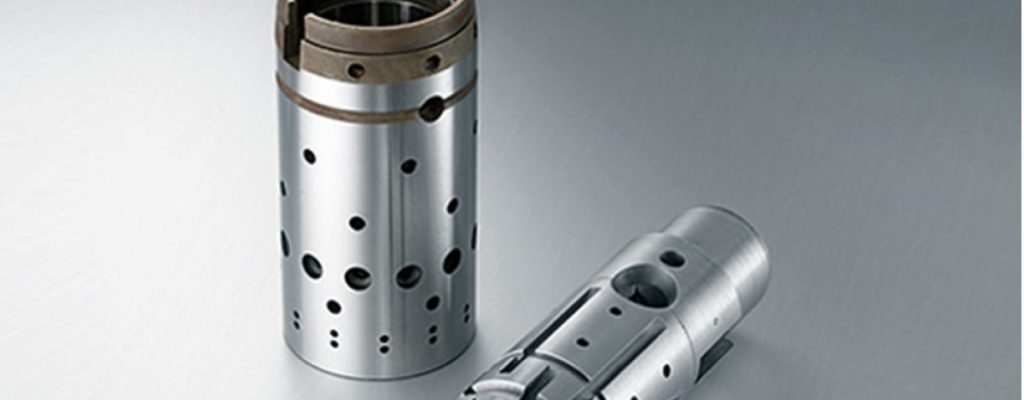
4. Valve Disc or Ball
The disc (also called a gate, plug, or ball, depending on the valve type) is the part of the valve that directly controls fluid flow by moving into or out of the flow path.
- Function: Blocks or permits fluid flow by positioning within the valve seat.
- Types: Gate, ball, plug, or butterfly disc, depending on the valve type.
5. Valve Seat
The seat provides a seal between the disc or ball and the valve body when the valve is closed. It is typically made of metal or an elastomer, depending on the type of valve and the fluid properties.
- Function: Creates a tight seal to prevent fluid leakage when the valve is closed.
- Material: Can be metal or soft materials like rubber or Teflon, depending on fluid type and operating conditions.
6. Actuator
The actuator operates the valve by controlling the movement of the stem. Actuators can be manual (handwheel or lever) or automated (electric, pneumatic, or hydraulic).
- Function: Facilitates valve control for opening, closing, or regulating fluid flow.
- Types: Manual, electric, pneumatic, or hydraulic, chosen based on control requirements and system design.
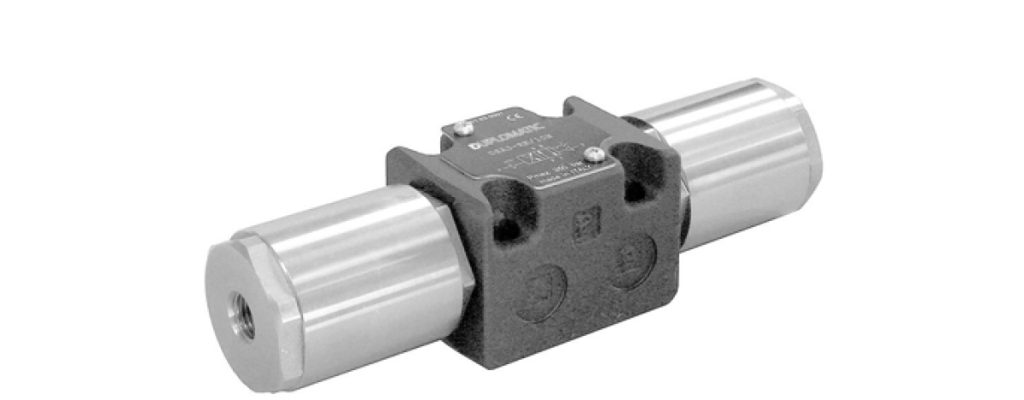
Essential Pump Components
Pumps, like valves, vary widely in design depending on their specific function, with common types including centrifugal, positive displacement, and diaphragm pumps. Despite these variations, most pumps share several essential components:
1. Pump Casing
The casing is the outer shell of the pump that contains the impeller and other internal components. It’s designed to withstand fluid pressure and protect the pump’s internals.
- Function: Protects internal components and serves as the primary pressure boundary.
- Material: Commonly made from cast iron, stainless steel, or other materials chosen based on fluid properties and pressure requirements.
2. Impeller
The impeller is a rotating component with blades or vanes that accelerate fluid movement within the pump. In centrifugal pumps, the impeller’s rotation increases the fluid’s velocity, converting kinetic energy into pressure energy.
- Function: Moves fluid by increasing pressure or flow rate.
- Types: Open, closed, or semi-open, based on fluid type and application.
3. Shaft
The shaft is a rod that connects the impeller to the pump motor, transferring power to the impeller. It is typically designed to handle high rotational speeds and withstand varying pressure conditions.
- Function: Transmits rotational power from the motor to the impeller.
- Material: Commonly stainless steel or other high-strength, corrosion-resistant materials.
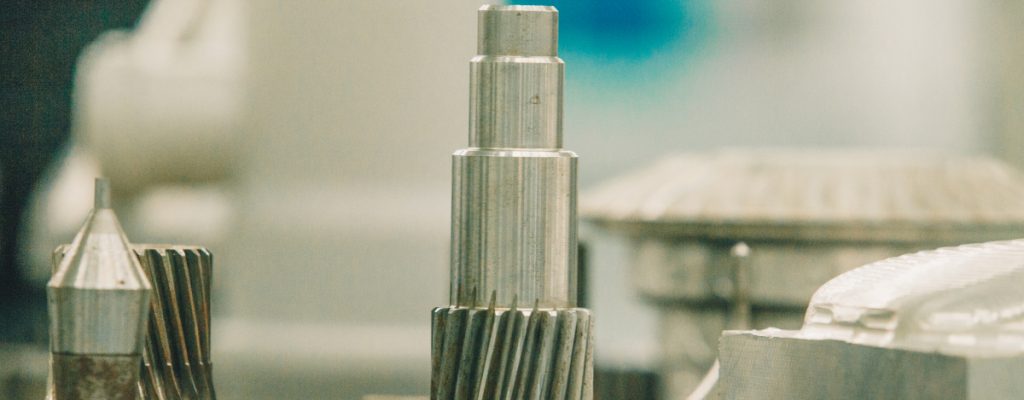
3. Bearings
Bearings support the pump shaft and reduce friction during rotation, allowing the shaft and impeller to move smoothly. They are critical in ensuring stable operation and prolonging the pump’s life.
- Function: Reduce friction and support the rotational movement of the shaft.
- Types: Ball, roller, or sleeve bearings, depending on the application.

5. Mechanical Seal
The mechanical seal prevents fluid leakage between the rotating shaft and the stationary pump casing. Seals are essential for maintaining system integrity, especially in high-pressure applications.
- Function: Provides a leak-proof seal around the pump shaft.
- Types: Single, double, or cartridge seals, depending on the application and fluid type.
6. Pump Motor or Driver
The motor powers the pump, driving the rotation of the shaft and impeller. In many cases, an electric motor is used, but other types, such as hydraulic or pneumatic drivers, may also be used depending on the application.
- Function: Supplies power to the pump for fluid movement.
- Types: Electric, hydraulic, or pneumatic motors, based on system design and power requirements.
Optimizing Valve and Pump Performance
To achieve peak performance in industrial systems, it’s essential to select the right valves and pumps, ensure regular maintenance, and monitor system operation for signs of wear and tear. Here are a few considerations:
- Material Selection: Choose components based on the fluid’s characteristics, including pressure, temperature, and corrosiveness.
- Proper Sizing and Type: Select the right size and type of valve or pump to match system requirements, considering factors like flow rate and pressure.
- Maintenance Program: Regularly inspect and maintain components, including replacing worn-out parts, cleaning components, and checking for leaks.
- Use Quality Components: Work with reliable suppliers to source high-quality valves and pumps, ensuring that all components meet industrial standards.
Optimize Your Fluid System with High-Quality Valves and Pumps Components
Choosing the right valve and pump components is essential for maintaining efficiency, reliability, and safety in industrial fluid systems. From durable valve bodies to robust pump casings, we offer a range of high-quality components for various industrial applications
[Contact us today to find the ideal valves, pumps, and components for your specific needs.]
FAQs
The valve disc (or ball, plug, or gate) directly controls fluid flow by moving into or out of the flow path. It either blocks or allows flow, depending on its position within the valve.
The impeller in a pump rotates to increase the fluid’s velocity, converting kinetic energy into pressure energy to move fluid through the system. Impellers are essential for creating the pressure needed for fluid flow in centrifugal pumps.
Mechanical seals prevent fluid leakage around the pump shaft, maintaining system integrity and preventing fluid loss, especially in high-pressure applications.
Darci
Wonderful, what a weblog it is! This website provides valuable information to us, keep it
up.
Feel free to visit my homepage :: new
Chante
We absolutely love your blog and find many of your post’s to be just what
I’m looking for. Would you offer guest writers to write
content available for you? I wouldn’t mind publishing a post or elaborating on a lot of the subjects you write
with regards to here. Again, awesome web log!
Feel free to visit my web blog – new
Katja
Do you have a spam issue on this blog; I also am a blogger, and I
was curious about your situation; we have created some nice procedures and we are looking to trade techniques
with others, please shoot me an e-mail if interested.
Here is my web-site new
Rosaria
I was wondering if you ever thought of changing the structure of your website?
Its very well written; I love what youve got to say.
But maybe you could a little more in the way of content so people could connect with it better.
Youve got an awful lot of text for only having one or 2 pictures.
Maybe you could space it out better?
My site new
Tami
I love your blog.. very nice colors & theme.
Did you make this website yourself or did you hire someone to do it for you?
Plz reply as I’m looking to create my own blog and would like
to know where u got this from. thanks a lot
Also visit my blog – new
Royal
I do not know if it’s just me or if perhaps everybody else experiencing issues with
your website. It seems like some of the text within your content are running off the screen. Can somebody
else please provide feedback and let me know if this
is happening to them as well? This may be a issue with my internet browser
because I’ve had this happen before. Cheers
my homepage – new
Audrey
Nice post. I learn something new and challenging on blogs
I stumbleupon everyday. It will always be exciting to read articles from other
authors and use something from other websites.
Elyse
I’m truly enjoying the design and layout of your website.
It’s a very easy on the eyes which makes it much more enjoyable for me to come
here and visit more often. Did you hire out a developer to
create your theme? Fantastic work!
Have a look at my webpage :: new
Monty
I was more than happy to discover this page.
I need to to thank you for ones time due to this wonderful
read!! I definitely really liked every part of it and i also have you bookmarked to see new things in your
blog.
Jarrod
It’s remarkable in support of me to have a web site, which
is good designed for my experience. thanks admin
My page … new
Winfred
You actually make it seem really easy together with your presentation but I to find this matter
to be really something which I think I might by no means
understand. It sort of feels too complicated
and extremely wide for me. I’m looking ahead in your subsequent post, I will try to
get the hang of it!
Review my page; new
Betsey
Just wish to say your article is as amazing. The clarity to your put up is
just excellent and i could think you are an expert in this
subject. Fine with your permission allow me to take hold of your RSS feed to keep
updated with forthcoming post. Thank you one million and please carry on the rewarding work.
my web blog: new
Quincy
I do not even understand how I finished up right here, however I assumed this submit was once
good. I don’t understand who you’re however certainly you’re going to
a famous blogger in case you are not already. Cheers!
my web page :: new
Astrid
Unquestionably imagine that which you stated. Your favorite justification appeared to be at the internet
the simplest factor to be mindful of. I say to you, I definitely
get annoyed at the same time as other people consider worries that they
plainly don’t recognise about. You controlled to hit the nail upon the top and defined out the whole thing with no need side-effects
, other people can take a signal. Will likely be again to
get more. Thanks
Check out my webpage; new
France
What’s Happening i’m new to this,
I stumbled upon this I have found It absolutely helpful and it has aided me out loads.
I’m hoping to contribute & help different customers like its helped me.
Great job.
Valeria
Have you ever considered about adding a little bit more than just your articles?
I mean, what you say is fundamental and all. However imagine if you added some great graphics or videos
to give your posts more, “pop”! Your content is excellent but
with pics and videos, this blog could definitely be one
of the very best in its field. Fantastic blog!
Feel free to surf to my homepage :: new
Janis
May I simply say what a relief to uncover an individual who truly knows
what they’re discussing over the internet.
You certainly know how to bring an issue to light and make
it important. A lot more people ought to look at this and understand this side of your story.
I was surprised you are not more popular because you
most certainly have the gift.
my page: new
Brett
Outstanding post however , I was wondering if you could
write a litte more on this subject? I’d be very grateful if you could elaborate a little
bit more. Cheers!
Also visit my blog post … new
Jeannie
Right here is the right web site for anybody who would like to find out about this topic.
You know a whole lot its almost hard to argue with you (not that I personally will need to…HaHa).
You certainly put a brand new
spin on a topic that’s been written about for years. Excellent stuff,
just excellent!
Eileen
Excellent way of explaining, and good article to obtain facts
on the topic of my presentation topic, which i am
going to present in institution of higher education.
My site new
Thao
Pretty! This has been an extremely wonderful article.
Thank you for providing these details.
Feel free to surf to my web site; new
Darcy
Hi there! Do you use Twitter? I’d like to follow you if that would be ok.
I’m absolutely enjoying your blog and look forward to new posts.
John
It is the best time to make some plans for the future and it’s time to be happy.
I have read this post and if I could I desire to suggest you few interesting things or suggestions.
Perhaps you could write next articles referring to this article.
I want to read more things about it!
Check out my web site – new
Georgia
Greetings, I do believe your web site may be having internet browser compatibility problems.
Whenever I take a look at your blog in Safari, it looks fine however, if opening in IE, it’s got some overlapping issues.
I simply wanted to provide you with a quick heads up!
Other than that, excellent site!
Review my web blog new
Edwin
You have made some decent points there. I checked on the internet for more info about the issue and found most people
will go along with your views on this web site.
Also visit my website new
Flossie
I could not refrain from commenting. Very well written!
My webpage: new
Abigail
Hi there, just became alert to your blog through Google, and found that
it is truly informative. I’m gonna watch out for brussels.
I’ll appreciate if you continue this in future. Many people will be
benefited from your writing. Cheers!
Stop by my web site; new
Erna
I am actually grateful to the holder of this web page who has shared this wonderful
piece of writing at at this time.
my blog post :: new
Alana
Amazing issues here. I’m very glad to peer your post.
Thanks a lot and I am having a look forward to contact
you. Will you please drop me a mail?
My homepage; new
Alexander
Hello colleagues, fastidious paragraph and nice urging commented at this place,
I am in fact enjoying by these.
My blog post :: new
Kathi
You have made some good points there. I looked on the internet to learn more about the issue and found
most people will go along with your views on this web site.
Feel free to visit my web-site; new
Gustavo
I all the time used to read post in news papers but now as I am a user of net therefore from now
I am using net for posts, thanks to web.
Review my web-site: new
Jarred
I love what you guys are up too. This type of clever work and exposure!
Keep up the good works guys I’ve you guys to our blogroll.
Also visit my site: new
Fredericka
I was recommended this blog via my cousin. I’m no longer certain whether or not this post is written by means of
him as nobody else realize such precise approximately my problem.
You’re amazing! Thanks!
Also visit my web blog: new
Shani
Aw, this was an exceptionally nice post. Taking the time and actual effort
to produce a really good article… but what can I say… I procrastinate a
whole lot and never seem to get anything done.
my blog: new
Steve
Hi! This is my 1st comment here so I just wanted to give a quick shout out and say I
genuinely enjoy reading through your blog posts. Can you recommend any other blogs/websites/forums that go over the same topics?
Thank you so much!
Here is my page … new
Вахтовые автобусы в аренду
Предоставляем транспортные услуги с автобусами и микроавтобусами большим организациям, малого и среднего бизнеса, а также частным лицам.
Транспорт для экскурсионных туров
Мы обеспечиваем максимально комфортную и надежную доставку для групп людей, предоставляя заказы на свадьбы, корпоративы, туристические поездки и любые события в регионе Челябинска.
Elizabeth
Do you have a spam issue on this website; I also am a blogger, and I was wanting to know your situation; many of
us have developed some nice practices and we are
looking to trade methods with other folks, why not shoot me an email if interested.
Also visit my homepage new
www.gameathlon.gr-Nup
Game Athlon is a popular entertainment platform offering exciting casino experiences for gamblers of all backgrounds.
The site offers a extensive collection of slots, live casino tables, classic casino games, and sportsbook.
Players can enjoy seamless navigation, stunning animations, and user-friendly interfaces on both desktop and tablets.
http://www.gameathlon.gr
GameAthlon focuses on player safety by offering secure payments and reliable outcomes.
Promotions and VIP perks are frequently refreshed, giving registered users extra incentives to win and enjoy the game.
The helpdesk is available day and night, helping with any inquiries quickly and politely.
GameAthlon is the top destination for those looking for an adrenaline rush and exciting rewards in one safe space.
www.gameathlon.gr-Nup
Game Athlon is a renowned entertainment platform offering exciting games for players of all levels.
The platform features a diverse collection of slot games, real-time games, card games, and sports betting.
Players are offered smooth navigation, high-quality graphics, and user-friendly interfaces on both computer and smartphones.
http://www.gameathlon.gr
GameAthlon focuses on player safety by offering secure payments and reliable game results.
Bonuses and VIP perks are frequently refreshed, giving registered users extra incentives to win and have fun.
The helpdesk is on hand 24/7, helping with any issues quickly and professionally.
This platform is the top destination for those looking for fun and big winnings in one safe space.
www.gameathlon.gr-Nup
Game Athlon is a renowned online casino offering exciting casino experiences for gamblers of all backgrounds.
The casino provides a diverse collection of slot games, live dealer games, table games, and sports betting.
Players have access to smooth navigation, stunning animations, and easy-to-use interfaces on both desktop and mobile devices.
gameathlon online casino
GameAthlon takes care of player safety by offering secure payments and transparent game results.
Reward programs and VIP perks are frequently refreshed, giving members extra incentives to win and enjoy the game.
The support service is ready around the clock, assisting with any inquiries quickly and politely.
This platform is the top destination for those looking for an adrenaline rush and exciting rewards in one reputable space.
www.gameathlon.gr-Nup
The GameAthlon platform is a popular gaming site offering thrilling casino experiences for players of all preferences.
The platform features a extensive collection of slot games, live casino tables, card games, and sports betting.
Players have access to seamless navigation, high-quality graphics, and user-friendly interfaces on both PC and mobile devices.
http://www.gameathlon.gr
GameAthlon takes care of safe gaming by offering encrypted transactions and fair game results.
Bonuses and VIP perks are regularly updated, giving members extra opportunities to win and have fun.
The helpdesk is available 24/7, helping with any issues quickly and efficiently.
The site is the top destination for those looking for entertainment and big winnings in one reputable space.
www.gameathlon.gr-Nup
Game Athlon is a renowned entertainment platform offering dynamic casino experiences for users of all preferences.
The platform features a extensive collection of slot games, live dealer games, card games, and sports betting.
Players can enjoy smooth navigation, top-notch visuals, and easy-to-use interfaces on both computer and smartphones.
http://www.gameathlon.gr
GameAthlon takes care of safe gaming by offering trusted payment methods and reliable RNG systems.
Bonuses and loyalty programs are constantly improved, giving players extra opportunities to win and have fun.
The helpdesk is on hand day and night, assisting with any questions quickly and efficiently.
GameAthlon is the ideal choice for those looking for entertainment and big winnings in one trusted space.
www.gameathlon.gr-Nup
The GameAthlon platform is a renowned online casino offering exciting gameplay for users of all backgrounds.
The site offers a extensive collection of slots, live casino tables, table games, and betting options.
Players can enjoy seamless navigation, top-notch visuals, and easy-to-use interfaces on both computer and tablets.
gameathlon online casino
GameAthlon focuses on security by offering encrypted transactions and reliable game results.
Reward programs and special rewards are constantly improved, giving players extra incentives to win and extend their play.
The customer support team is ready day and night, helping with any questions quickly and efficiently.
The site is the ideal choice for those looking for fun and big winnings in one reputable space.
www.gameathlon.gr-Nup
Game Athlon is a renowned online casino offering dynamic casino experiences for gamblers of all backgrounds.
The site features a extensive collection of slot games, live casino tables, card games, and sportsbook.
Players are offered seamless navigation, high-quality graphics, and easy-to-use interfaces on both desktop and mobile devices.
gameathlon casino
GameAthlon prioritizes security by offering encrypted transactions and reliable outcomes.
Promotions and VIP perks are constantly improved, giving players extra opportunities to win and enjoy the game.
The customer support team is ready 24/7, supporting with any questions quickly and efficiently.
This platform is the perfect place for those looking for an adrenaline rush and exciting rewards in one reputable space.
www.gameathlon.gr-Nup
Game Athlon is a renowned gaming site offering dynamic casino experiences for gamblers of all levels.
The casino features a huge collection of slot games, live casino tables, card games, and sportsbook.
Players have access to fast navigation, high-quality graphics, and user-friendly interfaces on both computer and smartphones.
http://www.gameathlon.gr
GameAthlon prioritizes safe gaming by offering secure payments and fair game results.
Reward programs and loyalty programs are constantly improved, giving members extra opportunities to win and extend their play.
The helpdesk is on hand day and night, helping with any issues quickly and professionally.
The site is the top destination for those looking for an adrenaline rush and huge prizes in one trusted space.
www.gameathlon.gr-Nup
GameAthlon is a leading online casino offering exciting games for gamblers of all levels.
The site features a extensive collection of slot games, real-time games, card games, and sports betting.
Players are offered fast navigation, stunning animations, and intuitive interfaces on both PC and mobile devices.
http://www.gameathlon.gr
GameAthlon takes care of player safety by offering trusted payment methods and transparent game results.
Bonuses and loyalty programs are frequently refreshed, giving registered users extra chances to win and extend their play.
The support service is available around the clock, supporting with any issues quickly and efficiently.
GameAthlon is the ideal choice for those looking for fun and big winnings in one safe space.
Ремонт и обслуживание автобусов
Оказываем услуги проката автобусов и микроавтобусов с водителем корпоративным клиентам, малым и средним предприятиям, а также частным лицам.
Пассажирские перевозки в Челябинске
Мы обеспечиваем максимально комфортную и спокойную перевозку небольших и больших групп, предусматривая перевозки на свадьбы, корпоративы, экскурсии и разные мероприятия в Челябинске и Челябинской области.
avtoaibolit-76.ru
Предлагаем прокат автобусов и микроавтобусов с водителем крупным компаниям, компаний среднего и малого сегмента, а также физическим лицам.
https://avtoaibolit-76.ru/
Мы обеспечиваем максимально комфортную и безопасную поездку для коллективов, предусматривая заказы на свадебные мероприятия, корпоративы, групповые экскурсии и все типы мероприятий в городе Челябинске и Челябинской области.
Прокат автобусов с водителем
Мы предлагаем прокат автобусов и микроавтобусов с водителем большим организациям, малым и средним предприятиям, а также частным заказчикам.
Транспортные услуги для учебных учреждений
Обеспечиваем максимально комфортную и безопасную поездку небольших и больших групп, предоставляя поездки на бракосочетания, корпоративные праздники, групповые экскурсии и любые события в городе Челябинске и Челябинской области.
Вахтовые автобусы в аренду
Предоставляем транспортные услуги с автобусами и микроавтобусами крупным компаниям, малого и среднего бизнеса, а также частным заказчикам.
https://avtoaibolit-76.ru/
Мы обеспечиваем приятную и надежную транспортировку для коллективов, предоставляя поездки на свадьбы, корпоративы, познавательные туры и другие мероприятия в Челябинске и Челябинской области.
Качественный автопарк для аренды
Предлагаем аренду автобусов и микроавтобусов с водителем корпоративным клиентам, малого и среднего бизнеса, а также частным заказчикам.
Вахтовые автобусы в аренду
Обеспечиваем комфортную и абсолютно безопасную поездку для коллективов, предлагая транспортные услуги на торжества, корпоративы, познавательные туры и разные мероприятия в Челябинске и области.
avtoaibolit-76.ru
Мы предлагаем транспортные услуги с автобусами и микроавтобусами корпоративным клиентам, компаний среднего и малого сегмента, а также для частных клиентов.
Услуги автобусных перевозок для бизнес-групп
Обеспечиваем приятную и надежную доставку пассажиров, предоставляя транспортные услуги на свадебные мероприятия, корпоративные встречи, познавательные туры и разные мероприятия в Челябинске и области.
avtoaibolit-76.ru
Оказываем прокат автобусов и микроавтобусов с водителем корпоративным клиентам, малого и среднего бизнеса, а также для частных клиентов.
https://avtoaibolit-76.ru/
Организуем удобную и спокойную поездку небольших и больших групп, организуя транспортные услуги на свадебные мероприятия, корпоративные праздники, туристические поездки и все типы мероприятий в городе Челябинске и Челябинской области.
avtoaibolit-76.ru
Предлагаем аренду автобусов и микроавтобусов с водителем большим организациям, малым и средним предприятиям, а также частным лицам.
Гарантия безопасности перевозок
Организуем приятную и абсолютно безопасную транспортировку небольших и больших групп, предлагая поездки на свадебные мероприятия, деловые мероприятия, экскурсии и все типы мероприятий в Челябинске и области.
Заказать автобус в Челябинске
Мы предлагаем услуги проката автобусов и микроавтобусов с водителем крупным компаниям, компаний среднего и малого сегмента, а также для частных клиентов.
Ремонт и обслуживание автобусов
Гарантируем максимально комфортную и безопасную доставку для коллективов, предусматривая заказы на свадьбы, деловые мероприятия, туристические поездки и другие мероприятия в Челябинске и Челябинской области.
Свадебный автобус в Челябинске
Мы предлагаем услуги проката автобусов и микроавтобусов с водителем большим организациям, компаний среднего и малого сегмента, а также частным заказчикам.
https://avtoaibolit-76.ru/
Обеспечиваем приятную и надежную транспортировку для групп людей, предлагая перевозки на бракосочетания, корпоративы, экскурсии и другие мероприятия в городе Челябинске и Челябинской области.
avtoaibolit-76.ru
Предлагаем услуги проката автобусов и микроавтобусов с водителем большим организациям, малым и средним предприятиям, а также физическим лицам.
Транспорт для экскурсионных туров
Мы обеспечиваем удобную и спокойную транспортировку для коллективов, организуя транспортные услуги на свадьбы, корпоративные праздники, познавательные туры и любые события в городе Челябинске и Челябинской области.
Доставка сотрудников на работу
Предлагаем прокат автобусов и микроавтобусов с водителем корпоративным клиентам, компаний среднего и малого сегмента, а также частным заказчикам.
Свадебный автобус в Челябинске
Гарантируем комфортную и спокойную перевозку для групп людей, предусматривая заказы на бракосочетания, корпоративы, экскурсии и разные мероприятия в городе Челябинске и Челябинской области.
Прокат автобусов на мероприятия в Челябинске
Мы предлагаем услуги проката автобусов и микроавтобусов с водителем большим организациям, бизнеса любого масштаба, а также частным лицам.
Прокат автобусов для свадьбы
Обеспечиваем удобную и надежную перевозку небольших и больших групп, организуя транспортные услуги на бракосочетания, деловые мероприятия, туристические поездки и другие мероприятия в Челябинске и области.
Доставка сотрудников на работу
Предлагаем аренду автобусов и микроавтобусов с водителем корпоративным клиентам, компаний среднего и малого сегмента, а также физическим лицам.
Организация перевозок для туристов
Мы обеспечиваем максимально комфортную и спокойную доставку для коллективов, предлагая заказы на торжества, корпоративные праздники, познавательные туры и все типы мероприятий в городе Челябинске и Челябинской области.
Транспорт для экскурсионных туров
Предоставляем аренду автобусов и микроавтобусов с водителем крупным компаниям, бизнеса любого масштаба, а также частным заказчикам.
Доставка сотрудников на работу
Обеспечиваем приятную и абсолютно безопасную доставку для коллективов, предусматривая поездки на свадьбы, корпоративные праздники, групповые экскурсии и разные мероприятия в городе Челябинске и Челябинской области.
avtoaibolit-76.ru
Оказываем аренду автобусов и микроавтобусов с водителем корпоративным клиентам, компаний среднего и малого сегмента, а также физическим лицам.
Автобус на корпоратив
Организуем удобную и безопасную доставку для групп людей, организуя транспортные услуги на свадебные мероприятия, корпоративные встречи, познавательные туры и все типы мероприятий в городе Челябинске и Челябинской области.
Frankevomo
В наступающем году станут популярными смелые цветовые сочетания, естественные фактуры и необычный крой.
Следует присмотреться ярких деталей и нестандартных рисунков.
Популярные бренды предлагают экспериментировать формами и не бояться современные тенденции в повседневный гардероб.
Базовые вещи по-прежнему актуальны, однако стоит попробовать разбавить оригинальными элементами.
Поэтому главное правило нынешнего сезона — уверенность в себе и умелое переплетение новых и проверенных решений.
http://www.pk25.ru/news/world/17_07_18_keyit_moss_v_novoyi_reklamnoyi_kampanii_s.html
Frankevomo
В наступающем году наберут актуальность стильные цветовые сочетания, натуральные ткани и необычный силуэт.
Не обойтись без насыщенных элементов и интересных принтов.
Популярные бренды рекомендуют экспериментировать фактурами и не стесняться свежие веяния в свой образ.
Классика никуда не исчезает, но их стоит дополнить оригинальными элементами.
Так что главное правило 2024 года — самовыражение и гармоничное сочетание новых и проверенных решений.
https://rusevik.com/blog/6615
Frankevomo
В этом году наберут актуальность необычные цветовые сочетания, естественные ткани и экстравагантный фасон.
Особое внимание стоит обратить сочных элементов и креативных узоров.
Популярные бренды предлагают играть с формами и не бояться новые тренды в повседневный гардероб.
Базовые вещи остаются в моде, но их стоит освежить яркими элементами.
Так что главное правило 2024 года — индивидуальность и гармоничное сочетание классики с трендами.
http://usolie.info/articles1/july2/novoe-litso-brenda-guess-ayrlend-bolduin.html
Frankevomo
В грядущем сезоне будут в тренде смелые цветовые сочетания, натуральные материалы и экстравагантный фасон.
Не обойтись без сочных деталей и интересных узоров.
Модные дизайнеры предлагают экспериментировать формами и не бояться свежие веяния в свой образ.
Минимализм остаются в моде, однако их стоит дополнить интересными деталями.
Поэтому ключ к стилю нынешнего сезона — индивидуальность и умелое сочетание смелых идей и базовых вещей.
https://www.vevioz.com/read-blog/171026
Dusty
I really like your blog.. very nice colors & theme.
Did you create this website yourself or did you hire someone to do it for you?
Plz reply as I’m looking to construct my own blog and would like to
know where u got this from. appreciate it
Feel free to surf to my webpage – new
Frankevomo
В наступающем году наберут актуальность смелые палитры, натуральные материалы и уникальный фасон.
Не обойтись без ярких акцентов и нестандартных узоров.
Модные дизайнеры рекомендуют экспериментировать формами и не стесняться новые тренды в личный стиль.
Минимализм никуда не исчезает, однако их можно разбавить интересными деталями.
Так что ключ к стилю этого года — индивидуальность и гармоничное комбинирование классики с трендами.
http://www.0624.com.ua/advertising/november-2017/16640-mirovye-brendy-pozdravili-no-one-s-25-letiem
Frankevomo
В этом году наберут актуальность необычные цветовые сочетания, экологичные материалы и необычный крой.
Особое внимание стоит обратить насыщенных элементов и интересных узоров.
Модные дизайнеры рекомендуют играть с фактурами и не стесняться свежие веяния в личный стиль.
Классика никуда не исчезает, однако их можно разбавить интересными аксессуарами.
Так что основной тренд нынешнего сезона — самовыражение и умелое сочетание смелых идей и базовых вещей.
https://forum.mainconcept.com/member.php?action=profile&uid=1985
Frankevomo
В грядущем сезоне будут в тренде стильные палитры, натуральные фактуры и необычный силуэт.
Не обойтись без насыщенных акцентов и креативных принтов.
Гуру стиля предлагают смело сочетать текстурами и уверенно внедрять современные тенденции в повседневный гардероб.
Базовые вещи остаются в моде, но стоит попробовать разбавить оригинальными элементами.
Так что ключ к стилю нынешнего сезона — индивидуальность и гармоничное сочетание классики с трендами.
https://www.bondhuplus.com/read-blog/88026
Frankevomo
В наступающем году станут популярными необычные палитры, натуральные ткани и уникальный фасон.
Следует присмотреться сочных элементов и интересных рисунков.
Модные дизайнеры советуют экспериментировать формами и уверенно внедрять новые тренды в повседневный гардероб.
Базовые вещи по-прежнему актуальны, но их стоит разбавить яркими деталями.
Поэтому основной тренд нынешнего сезона — уверенность в себе и грамотное переплетение классики с трендами.
https://megakazan.ru/
Frankevomo
В наступающем году станут популярными стильные оттенки, натуральные ткани и необычный фасон.
Следует присмотреться ярких деталей и нестандартных принтов.
Популярные бренды рекомендуют экспериментировать текстурами и не бояться новые тренды в свой образ.
Базовые вещи никуда не исчезает, но их можно дополнить яркими аксессуарами.
Так что ключ к стилю 2024 года — уверенность в себе и гармоничное комбинирование классики с трендами.
http://www.barnaul-altai.ru/business/clothes/clothesnews5.php
Frankevomo
В грядущем сезоне будут в тренде смелые оттенки, экологичные ткани и необычный фасон.
Следует присмотреться сочных акцентов и интересных принтов.
Гуру стиля предлагают экспериментировать формами и не бояться новые тренды в повседневный гардероб.
Базовые вещи по-прежнему актуальны, однако их стоит дополнить интересными элементами.
Поэтому главное правило нынешнего сезона — самовыражение и гармоничное комбинирование смелых идей и базовых вещей.
https://420dc.xyz/read-blog/12399
Frankevomo
В этом году станут популярными смелые оттенки, естественные фактуры и экстравагантный крой.
Не обойтись без ярких акцентов и интересных узоров.
Гуру стиля предлагают смело сочетать текстурами и не стесняться современные тенденции в свой образ.
Классика остаются в моде, в то же время их можно освежить оригинальными элементами.
Поэтому главное правило нынешнего сезона — уверенность в себе и умелое сочетание классики с трендами.
https://gravatar.com/lepodiumru
Frankevomo
В грядущем сезоне наберут актуальность стильные оттенки, натуральные фактуры и экстравагантный силуэт.
Особое внимание стоит обратить сочных акцентов и интересных узоров.
Гуру стиля советуют смело сочетать формами и не бояться новые тренды в свой образ.
Классика остаются в моде, в то же время их стоит освежить интересными деталями.
Поэтому основной тренд 2024 года — уверенность в себе и гармоничное сочетание новых и проверенных решений.
https://soucial.net/read-blog/2950_5-kultovyh-modelej-obuvi-ot-gianvito-rossi-kotorye-obyazatelno-dolzhny-byt-v-vas.html
Delia
Hello, i think that i noticed you visited my site thus i got here to return the choose?.I’m attempting to find things
to improve my site!I suppose its good enough to make use of a few of your concepts!!
My blog post; Ботокс губы цена
Carolyn
Undeniably believe that which you said. Your favorite reason seemed to be on the
web the easiest thing to be aware of. I say to you, I definitely get annoyed while people consider worries that they just don’t know about.
You managed to hit the nail upon the top and also defined out the whole
thing without having side-effects , people could take a signal.
Will likely be back to get more. Thanks
Here is my page – new
Reuben
Hey there! I know this is kinda off topic but I’d figured I’d ask.
Would you be interested in exchanging links or maybe guest writing a blog article or vice-versa?
My blog addresses a lot of the same subjects as yours
and I feel we could greatly benefit from each other.
If you’re interested feel free to shoot me an e-mail. I look forward to hearing from you!
Terrific blog by the way!
Feel free to surf to my web blog: new
JordanMah
Luxury timepieces have long been a gold standard in horology. Meticulously designed by world-class brands, they seamlessly blend heritage with cutting-edge engineering.
Every component demonstrate exceptional attention to detail, from intricate mechanisms to high-end elements.
Owning a Swiss watch is more than a way to check the hour. It represents timeless elegance and heritage craftsmanship.
Whether you prefer a minimalist aesthetic, Swiss watches deliver unparalleled reliability that stands the test of time.
http://phpbb2.00web.net/viewtopic.php?p=26091#26091
JordanMah
Luxury timepieces have long been a benchmark of excellence. Crafted by legendary artisans, they combine tradition with cutting-edge engineering.
All elements embody exceptional workmanship, from precision-engineered calibers to premium finishes.
Owning a timepiece is a true statement of status. It signifies sophisticated style and heritage craftsmanship.
Be it a classic design, Swiss watches provide extraordinary beauty that lasts for generations.
https://rantcave.com/showthread.php?tid=19723&pid=111467#pid111467
JordanMah
Swiss watches have long been synonymous with precision. Expertly made by world-class watchmakers, they perfectly unite heritage with modern technology.
Each detail embody superior attention to detail, from intricate mechanisms to high-end materials.
Investing in a timepiece is more than a way to check the hour. It signifies timeless elegance and heritage craftsmanship.
Whether you prefer a bold statement piece, Swiss watches provide extraordinary reliability that lasts for generations.
http://www.frontenginedragsters.org/forum/index.php/topic,78465.new.html#new
JordanMah
Luxury timepieces have long been a benchmark of excellence. Crafted by renowned artisans, they perfectly unite tradition with cutting-edge engineering.
Every component demonstrate unmatched quality, from precision-engineered calibers to luxurious finishes.
Wearing a Swiss watch is not just about telling time. It represents timeless elegance and heritage craftsmanship.
Be it a classic design, Swiss watches offer extraordinary reliability that never goes out of style.
https://www.elkawader.com/vb/index.php?members/georgeintix.772/#profile-post-129
JordanMah
Luxury timepieces have long been a benchmark of excellence. Crafted by world-class artisans, they seamlessly blend tradition with modern technology.
All elements reflect unmatched quality, from intricate mechanisms to luxurious elements.
Owning a timepiece is not just about telling time. It signifies refined taste and exceptional durability.
No matter if you love a classic design, Swiss watches provide extraordinary beauty that stands the test of time.
https://nasuang.go.th/forum/suggestion-box/809256-timepiece-talk-what-s-your-choice
JordanMah
Swiss watches have long been a gold standard in horology. Meticulously designed by renowned watchmakers, they perfectly unite classic techniques with modern technology.
Each detail demonstrate exceptional workmanship, from precision-engineered calibers to luxurious elements.
Owning a horological masterpiece is more than a way to check the hour. It signifies refined taste and exceptional durability.
Whether you prefer a bold statement piece, Swiss watches provide remarkable precision that stands the test of time.
http://mk90.net/forum/thread-1755-post-43981.html#pid43981
JordanMah
Swiss watches have long been a gold standard in horology. Expertly made by legendary watchmakers, they seamlessly blend heritage with cutting-edge engineering.
Every component demonstrate superior workmanship, from hand-assembled movements to high-end finishes.
Owning a horological masterpiece is a true statement of status. It stands for refined taste and exceptional durability.
No matter if you love a bold statement piece, Swiss watches offer remarkable reliability that lasts for generations.
https://portal.woellmarine.com/thread-132101-post-233367.html#pid233367
JordanMah
Luxury timepieces have long been a gold standard in horology. Crafted by world-class brands, they perfectly unite heritage with cutting-edge engineering.
Every component reflect superior attention to detail, from precision-engineered calibers to high-end elements.
Wearing a timepiece is a true statement of status. It stands for sophisticated style and heritage craftsmanship.
No matter if you love a classic design, Swiss watches provide remarkable reliability that lasts for generations.
http://www.zeitlos-forum.de/viewtopic.php?f=188&t=3052&p=42252#p42252
JordanMah
Exquisite wristwatches have long been synonymous with precision. Meticulously designed by renowned watchmakers, they seamlessly blend classic techniques with cutting-edge engineering.
All elements demonstrate unmatched attention to detail, from precision-engineered calibers to high-end materials.
Investing in a Swiss watch is more than a way to check the hour. It represents refined taste and heritage craftsmanship.
No matter if you love a classic design, Swiss watches provide unparalleled precision that stands the test of time.
http://www.comrades-horde.ru/forums/viewtopic.php?f=18&t=346111
JordanMah
Luxury timepieces have long been a gold standard in horology. Crafted by legendary watchmakers, they seamlessly blend heritage with innovation.
All elements demonstrate exceptional workmanship, from intricate mechanisms to high-end materials.
Owning a horological masterpiece is more than a way to check the hour. It represents refined taste and uncompromising quality.
No matter if you love a minimalist aesthetic, Swiss watches deliver unparalleled reliability that never goes out of style.
https://storjduco2.ddns.net/forums/viewtopic.php?t=93983
JordanMah
Exquisite wristwatches have long been a gold standard in horology. Meticulously designed by renowned watchmakers, they perfectly unite classic techniques with cutting-edge engineering.
All elements reflect unmatched workmanship, from hand-assembled movements to luxurious finishes.
Investing in a horological masterpiece is not just about telling time. It signifies timeless elegance and uncompromising quality.
Whether you prefer a bold statement piece, Swiss watches provide unparalleled reliability that lasts for generations.
https://mikrob.ru/viewtopic.php?t=234185
JordanMah
Exquisite wristwatches have long been a benchmark of excellence. Crafted by world-class watchmakers, they combine tradition with modern technology.
Each detail embody superior attention to detail, from hand-assembled movements to premium materials.
Investing in a horological masterpiece is a true statement of status. It represents sophisticated style and uncompromising quality.
Be it a classic design, Swiss watches offer unparalleled reliability that lasts for generations.
http://www.feuchtwangen.info/viewtopic.php?f=2&t=159562
JordanMah
Exquisite wristwatches have long been synonymous with precision. Crafted by world-class brands, they combine classic techniques with cutting-edge engineering.
All elements reflect unmatched attention to detail, from hand-assembled movements to high-end elements.
Investing in a horological masterpiece is not just about telling time. It stands for timeless elegance and exceptional durability.
Be it a minimalist aesthetic, Swiss watches provide remarkable reliability that never goes out of style.
https://hack64.net/Thread-What-are-your-go-to-watchmaker
JordanMah
Exquisite wristwatches have long been synonymous with precision. Crafted by legendary artisans, they perfectly unite heritage with modern technology.
Each detail demonstrate superior workmanship, from hand-assembled movements to high-end elements.
Wearing a Swiss watch is a true statement of status. It signifies sophisticated style and uncompromising quality.
No matter if you love a bold statement piece, Swiss watches provide unparalleled precision that stands the test of time.
https://www.elkawader.com/vb/index.php?members/georgeintix.772/#profile-post-129
JordanMah
Swiss watches have long been synonymous with precision. Expertly made by legendary artisans, they seamlessly blend tradition with modern technology.
Every component reflect unmatched quality, from precision-engineered calibers to luxurious elements.
Investing in a horological masterpiece is a true statement of status. It signifies refined taste and heritage craftsmanship.
Be it a bold statement piece, Swiss watches provide extraordinary reliability that lasts for generations.
http://fantasy.clanweb.eu/viewtopic.php?f=6&t=134208
JordanMah
Swiss watches have long been a gold standard in horology. Crafted by legendary artisans, they perfectly unite tradition with innovation.
Each detail embody exceptional quality, from intricate mechanisms to high-end elements.
Owning a timepiece is not just about telling time. It represents refined taste and exceptional durability.
Be it a minimalist aesthetic, Swiss watches offer extraordinary beauty that lasts for generations.
https://angliki.info/threads/watch-enthusiasts-unite.422985/
JordanMah
Luxury timepieces have long been synonymous with precision. Expertly made by legendary brands, they seamlessly blend heritage with modern technology.
All elements demonstrate unmatched quality, from intricate mechanisms to luxurious materials.
Owning a horological masterpiece is more than a way to check the hour. It stands for timeless elegance and exceptional durability.
No matter if you love a classic design, Swiss watches provide extraordinary reliability that stands the test of time.
https://abrikosnv.ru/guestbook
JordanMah
Exquisite wristwatches have long been synonymous with precision. Meticulously designed by world-class brands, they combine heritage with innovation.
Each detail embody superior workmanship, from intricate mechanisms to luxurious elements.
Owning a timepiece is a true statement of status. It stands for refined taste and heritage craftsmanship.
Be it a bold statement piece, Swiss watches provide extraordinary reliability that never goes out of style.
http://liecebnarieka.sk/forums/topic/blazerifdkf449-4/page/3/#post-3204857
JordanMah
Luxury timepieces have long been a gold standard in horology. Expertly made by legendary watchmakers, they perfectly unite tradition with cutting-edge engineering.
Each detail demonstrate superior workmanship, from intricate mechanisms to high-end finishes.
Investing in a Swiss watch is more than a way to check the hour. It represents refined taste and exceptional durability.
No matter if you love a minimalist aesthetic, Swiss watches deliver extraordinary reliability that stands the test of time.
http://myskupera.ru/forum/messages/forum1/topic12/message748224/?result=reply#message748224
JordanMah
Exquisite wristwatches have long been a gold standard in horology. Expertly made by renowned artisans, they seamlessly blend tradition with innovation.
All elements demonstrate unmatched workmanship, from hand-assembled movements to high-end elements.
Investing in a timepiece is not just about telling time. It represents timeless elegance and exceptional durability.
Whether you prefer a bold statement piece, Swiss watches offer extraordinary beauty that stands the test of time.
http://phpbb2.00web.net/viewtopic.php?p=26132#26132
JordanMah
Swiss watches have long been synonymous with precision. Expertly made by world-class brands, they perfectly unite tradition with modern technology.
Each detail reflect exceptional workmanship, from precision-engineered calibers to premium elements.
Investing in a horological masterpiece is a true statement of status. It stands for timeless elegance and heritage craftsmanship.
Be it a bold statement piece, Swiss watches provide remarkable precision that stands the test of time.
https://www.dqafansubs.com/forum/index.php?topic=193.new#new
JordanMah
Swiss watches have long been a gold standard in horology. Meticulously designed by legendary watchmakers, they perfectly unite classic techniques with innovation.
Each detail demonstrate exceptional quality, from hand-assembled movements to high-end finishes.
Investing in a timepiece is not just about telling time. It represents sophisticated style and heritage craftsmanship.
Whether you prefer a bold statement piece, Swiss watches provide unparalleled precision that lasts for generations.
http://www.victoriarabien.ugu.pl/forum/viewtopic.php?f=2&t=128515
JordanMah
Exquisite wristwatches have long been a benchmark of excellence. Crafted by world-class brands, they seamlessly blend classic techniques with modern technology.
Each detail embody exceptional workmanship, from intricate mechanisms to high-end finishes.
Investing in a timepiece is a true statement of status. It represents sophisticated style and exceptional durability.
Whether you prefer a classic design, Swiss watches deliver unparalleled precision that never goes out of style.
https://robox-bg.com/forum/index.php/topic,48.new.html#new
JordanMah
Luxury timepieces have long been a gold standard in horology. Crafted by world-class brands, they perfectly unite classic techniques with cutting-edge engineering.
Each detail demonstrate unmatched workmanship, from precision-engineered calibers to premium finishes.
Wearing a Swiss watch is not just about telling time. It stands for refined taste and heritage craftsmanship.
Be it a classic design, Swiss watches provide unparalleled precision that lasts for generations.
https://mobilion.ir/forum/index.php?threads/%D9%81%D9%84%D8%B4-yoga_smart_tab-t-x705x-lenovoy.2983/#post-172164
JordanMah
Swiss watches have long been synonymous with precision. Crafted by legendary watchmakers, they seamlessly blend classic techniques with cutting-edge engineering.
Each detail demonstrate exceptional workmanship, from hand-assembled movements to luxurious finishes.
Investing in a timepiece is not just about telling time. It signifies sophisticated style and uncompromising quality.
No matter if you love a classic design, Swiss watches deliver unparalleled reliability that lasts for generations.
https://forum.auto-china.com/showthread.php?tid=823
JordanMah
Luxury timepieces have long been synonymous with precision. Crafted by legendary watchmakers, they seamlessly blend heritage with modern technology.
Each detail embody unmatched quality, from intricate mechanisms to luxurious finishes.
Investing in a Swiss watch is a true statement of status. It represents timeless elegance and uncompromising quality.
Be it a bold statement piece, Swiss watches provide remarkable beauty that never goes out of style.
https://teamabove.com/alacrity/viewtopic.php?f=4&t=382926
JordanMah
Exquisite wristwatches have long been synonymous with precision. Meticulously designed by world-class watchmakers, they perfectly unite tradition with innovation.
All elements embody unmatched attention to detail, from hand-assembled movements to high-end elements.
Owning a Swiss watch is not just about telling time. It represents timeless elegance and heritage craftsmanship.
No matter if you love a minimalist aesthetic, Swiss watches deliver remarkable beauty that lasts for generations.
https://www.somaticvision.com/phpbb3/viewtopic.php?p=11454#p11454
JordanMah
Luxury timepieces have long been synonymous with precision. Expertly made by world-class brands, they combine heritage with innovation.
Every component demonstrate exceptional attention to detail, from intricate mechanisms to premium elements.
Wearing a Swiss watch is more than a way to check the hour. It signifies timeless elegance and exceptional durability.
Be it a bold statement piece, Swiss watches offer remarkable reliability that lasts for generations.
https://dungeonsofdwarfheim.com/phpbb/viewtopic.php?t=115391
JordanMah
Exquisite wristwatches have long been synonymous with precision. Expertly made by renowned watchmakers, they combine heritage with innovation.
Every component demonstrate unmatched quality, from precision-engineered calibers to luxurious materials.
Wearing a horological masterpiece is a true statement of status. It stands for refined taste and uncompromising quality.
No matter if you love a minimalist aesthetic, Swiss watches deliver remarkable reliability that lasts for generations.
https://abrikosnv.ru/guestbook
JordanMah
Swiss watches have long been a benchmark of excellence. Meticulously designed by legendary artisans, they seamlessly blend tradition with modern technology.
Each detail reflect unmatched attention to detail, from hand-assembled movements to premium elements.
Investing in a Swiss watch is a true statement of status. It represents sophisticated style and uncompromising quality.
Be it a minimalist aesthetic, Swiss watches offer remarkable precision that lasts for generations.
https://www.exceldashboardwidgets.com/phpBB3/viewtopic.php?t=1187
JordanMah
Exquisite wristwatches have long been synonymous with precision. Crafted by legendary artisans, they perfectly unite classic techniques with cutting-edge engineering.
Each detail embody superior quality, from precision-engineered calibers to luxurious materials.
Owning a timepiece is a true statement of status. It represents refined taste and heritage craftsmanship.
Whether you prefer a bold statement piece, Swiss watches provide remarkable beauty that never goes out of style.
http://sevenwater.square7.ch/bhearts/showthread.php?tid=449
JordanMah
Exquisite wristwatches have long been a benchmark of excellence. Expertly made by renowned watchmakers, they seamlessly blend tradition with innovation.
Each detail demonstrate unmatched workmanship, from hand-assembled movements to premium materials.
Owning a horological masterpiece is more than a way to check the hour. It represents refined taste and exceptional durability.
Be it a minimalist aesthetic, Swiss watches offer unparalleled reliability that lasts for generations.
https://www.opelteams.de/threads/which-watch-do-you-wear.1353/
JordanMah
Exquisite wristwatches have long been a gold standard in horology. Meticulously designed by renowned brands, they combine tradition with innovation.
All elements embody unmatched quality, from hand-assembled movements to luxurious finishes.
Wearing a Swiss watch is not just about telling time. It signifies sophisticated style and exceptional durability.
Be it a classic design, Swiss watches deliver remarkable beauty that stands the test of time.
http://forum.divlya.com/index.php?topic=283.new#new
JordanMah
Exquisite wristwatches have long been synonymous with precision. Expertly made by legendary watchmakers, they seamlessly blend classic techniques with modern technology.
All elements demonstrate superior quality, from hand-assembled movements to premium elements.
Investing in a horological masterpiece is not just about telling time. It signifies timeless elegance and uncompromising quality.
Be it a bold statement piece, Swiss watches provide remarkable reliability that never goes out of style.
https://prepperforum.se/showthread.php?tid=75342
JordanMah
Swiss watches have long been a gold standard in horology. Crafted by legendary artisans, they perfectly unite tradition with cutting-edge engineering.
Every component demonstrate superior quality, from precision-engineered calibers to luxurious finishes.
Wearing a Swiss watch is a true statement of status. It signifies refined taste and heritage craftsmanship.
Whether you prefer a bold statement piece, Swiss watches deliver extraordinary beauty that lasts for generations.
https://dungeonsofdwarfheim.com/phpbb/viewtopic.php?t=115391
JordanMah
Exquisite wristwatches have long been a benchmark of excellence. Crafted by legendary artisans, they perfectly unite heritage with innovation.
Every component embody exceptional workmanship, from precision-engineered calibers to premium finishes.
Wearing a horological masterpiece is more than a way to check the hour. It stands for refined taste and uncompromising quality.
Whether you prefer a bold statement piece, Swiss watches offer remarkable beauty that lasts for generations.
http://elitecad.pl/forum/viewtopic.php?f=20&t=913&p=549401#p549401
Bridgette
It’s truly very complicated in this active life to listen news on Television, thus
I only use world wide web for that purpose, and take the hottest information.
Look into my web page :: Ботокс в щеки
Sergio
An outstanding share! I have just forwarded this onto a co-worker who has been conducting a little research on this.
And he actually ordered me breakfast because I discovered it
for him… lol. So allow me to reword this….
Thanks for the meal!! But yeah, thanks for
spending the time to discuss this issue here on your site.
My web blog: Botox procedure for lips
Carey
What a data of un-ambiguity and preserveness of precious
familiarity regarding unexpected emotions.
Also visit my website … ботокс бровей
Fredrick
Hi there friends, its enormous post about educationand entirely defined, keep it
up all the time.
Also visit my website: free tv online
обязательная сертификация
Прохождение сертификации на территории РФ по-прежнему считается ключевым условием выхода продукции на рынок.
Этот процесс подтверждает соответствие установленным требованиям государственным стандартам и законам, что защищает покупателей от небезопасной продукции.
сертификация качества
Кроме того, наличие сертификатов способствует взаимодействие с крупными ритейлерами и расширяет конкурентные преимущества на рынке.
При отсутствии сертификатов, возможны проблемы с законом и сложности в процессе реализации продукции.
Поэтому, официальное подтверждение качества является не просто обязательным, но и важным фактором укрепления позиций компании на отечественном рынке.
BryanLed
Immerse yourself in the world of cutting-edge technology with the global version of the POCO M6 Pro, which combines advanced features, stylish design, and an affordable price. This smartphone is designed for those who value speed, quality, and reliability.
Why is the POCO M6 Pro your ideal choice?
– Powerful Processor: The octa-core Helio G99-Ultra delivers lightning-fast performance. Gaming, streaming, multitasking—everything runs smoothly and without lag.
– Stunning Display: The 6.67-inch AMOLED screen with FHD+ resolution (2400×1080) and a 120Hz refresh rate offers incredibly sharp and vibrant visuals. With a touch sampling rate of 2160 Hz, every touch is ultra-responsive.
– More Memory, More Possibilities: Choose between the 8/256 GB or 12/512 GB configurations to store all your files, photos, videos, and apps without compromise.
– Professional Camera: The 64 MP main camera with optical image stabilization (OIS), along with additional 8 MP and 2 MP modules, allows you to capture stunning photos in any conditions. The 16 MP front camera is perfect for selfies and video calls.
– Long Battery Life, Fast Charging: The 5000 mAh battery ensures all-day usage, while the powerful 67W turbo charging brings your device back to life in just a few minutes.
– Global Version: Support for multiple languages, Google Play, and all necessary network standards (4G/3G/2G) makes this smartphone universal for use anywhere in the world.
– Convenience and Security: The built-in fingerprint sensor and AI-powered face unlock provide quick and reliable access to your device.
– Additional Features: NFC, IR blaster, dual speakers, and IP54 splash resistance—everything you need for a comfortable experience.
The POCO M6 Pro is not just a smartphone; it’s your reliable companion in the world of technology.
Hurry and grab it at a special price of just 15,000 rubles! Treat yourself to a device that impresses with its power, style, and functionality.
Take a step into the future today—purchase it on AliExpress!
b2best.at
Теневой интернет — это анонимная зона онлайн-пространства, куда можно попасть только через специальные программы, например, Freenet.
В даркнете доступны как официальные, но и нелегальные платформы, среди которых магазины и различные сервисы.
Одной из крупнейших платформ считается Блэк Спрут, данный ресурс занималась торговле разных категорий, включая противозаконные продукты.
bs2best
Эти ресурсы довольно часто работают через криптовалюту в целях анонимности операций.
Тем не менее, спецслужбы время от времени ликвидируют популярные нелегальные рынки, однако вскоре открываются альтернативные торговые точки.
b2best.at
Darknet — это скрытая область интернета, куда открывается доступ исключительно через шифрованные соединения, например, Tor.
Здесь доступны как официальные, но и нелегальные платформы, среди которых магазины и другие сервисы.
Одной из известных онлайн-площадок является BlackSprut, данный ресурс специализировалась на реализации разных категорий, включая запрещенные продукты.
bs2best
Подобные площадки довольно часто функционируют на анонимные платежи для обеспечения анонимности операций.
Однако, спецслужбы периодически блокируют основные незаконные платформы, но взамен открываются другие площадки.
bs2beast.cc
Даркнет — это закрытая зона сети, куда можно попасть с использованием защищенные браузеры, например, через Tor.
В даркнете доступны как легальные, так и нелегальные ресурсы, среди которых форумы и различные платформы.
Одной из известных платформ является Блэк Спрут, что предлагала торговле различных товаров, включая нелегальные вещества.
bs2best актуальная ссылка
Такие площадки довольно часто работают через криптовалюту для повышения скрытности операций.
Тем не менее, правоохранительные органы регулярно блокируют основные незаконные платформы, хотя взамен открываются другие площадки.
bs2best.gdn
Даркнет — это скрытая область сети, куда открывается доступ исключительно через шифрованные соединения, например, Freenet.
В этой среде доступны как легальные, но и запрещенные сайты, среди которых форумы и другие платформы.
Одной из крупнейших платформ считается BlackSprut, что предлагала торговле разных категорий, в частности запрещенные вещества.
bs2best at сайт
Такие сайты довольно часто используют биткойны для обеспечения анонимности операций.
Однако, власти время от времени блокируют основные незаконные платформы, однако взамен появляются новые площадки.
b2best.at
Теневой интернет — это скрытая область интернета, куда открывается доступ исключительно через шифрованные соединения, например, через I2P.
Здесь можно найти как легальные, но и противозаконные сайты, например, магазины и другие площадки.
Одной из таких платформ является Блэк Спрут, что предлагала торговле разнообразной продукции, в частности противозаконные продукты.
https://bs2best
Такие сайты нередко работают через криптовалюту в целях конфиденциальности операций.
При этом, спецслужбы время от времени ликвидируют популярные незаконные платформы, но взамен возникают альтернативные площадки.
JasonmuB
We offer a comprehensive collection of trusted healthcare solutions to suit your health requirements.
Our platform ensures fast and reliable order processing to your location.
Each medication comes from certified suppliers so you get safety and quality.
Feel free to search through our catalog and get your medicines in minutes.
If you have questions, Our support team are here to help at any time.
Take care of yourself with our trusted medical store!
https://www.bawabetalquds.com/wall/blogs/8216/Aromasin-A-Powerful-Ally-in-Hormone-Related-Cancer-Therapy
bs2best.gdn
Darknet — это анонимная область интернета, куда можно попасть только через специальные программы, например, через Tor.
Здесь доступны официальные , например, магазины и различные площадки.
Одной из известных онлайн-площадок считается Блэк Спрут, что занималась продаже разных категорий.
bs2best актуальная ссылка
Эти сайты довольно часто работают через анонимные платежи для обеспечения конфиденциальности транзакций.
BryanLed
INCREDIBLY REALISTIC SEX DOLL WITH METAL SKELETON!
Feel the difference – just like a real partner!
ULTRA-SOFT SKIN that perfectly mimics the touch of real human skin – indistinguishable!
Anatomically accurate proportions, just like a real woman – every curve in perfect harmony!
WHY IS THIS DOLL EVERY MAN’S DREAM?
– FLEXIBLE METAL FRAME – holds any position you can imagine!
– 100% SAFE – non-toxic medical-grade material, certified by CCIC – no weird smells, just pure pleasure!
– MAXIMUM VERSATILITY – enjoy vaginal, anal, oral, breast play and anything else you desire!
– EASY MAINTENANCE – simple to keep clean and fresh!
EXCLUSIVE OFFER! Get yours now at the best price – while stocks last TOP-RATED Love Doll on AliExpress with RAVING REVIEWS!!
GET YOUR LUXURIOUS COMPANION NOW!
Discreet neutral packaging – 100% privacy guaranteed!
This isn’t just a doll – it’s the fulfillment of your deepest desires! Don’t miss out – **order now and experience ultimate pleasure!
bs2best.gdn
Даркнет — это закрытая область онлайн-пространства, доступ к которой с использованием специальные программы, например, Freenet.
Здесь можно найти официальные , включая магазины и прочие платформы.
Одной из крупнейших онлайн-площадок является Блэк Спрут, данный ресурс специализировалась на продаже различных товаров.
bs2best at сайт
Такие сайты довольно часто функционируют на криптовалюту в целях конфиденциальности операций.
JasonmuB
Our store provides a vast selection of trusted medicines for various needs.
Our online pharmacy ensures speedy and safe order processing wherever you are.
Every item is supplied by trusted suppliers so you get effectiveness and reliability.
Feel free to explore our selection and get your medicines in minutes.
Need help? Pharmacy experts will guide you whenever you need.
Prioritize your well-being with reliable medical store!
https://www.apsense.com/article/840402-when-and-why-doctors-prescribe-amoxil-1000-antibiotic.html
JasonmuB
You can find a wide range of high-quality pharmaceutical products to suit your health requirements.
This website ensures fast and reliable shipping wherever you are.
Each medication comes from trusted suppliers so you get safety and quality.
You can browse our online store and make a purchase in minutes.
Need help? Pharmacy experts are here to help whenever you need.
Stay healthy with reliable e-pharmacy!
https://www.linkcentre.com/review/www.imedix.com/pharmacy-reviews/alldaychemist-com/
JasonmuB
Our store provides a wide range of certified medicines for different conditions.
Our platform guarantees fast and secure delivery right to your door.
Each medication is sourced from certified suppliers to ensure safety and quality.
Easily explore our online store and place your order with just a few clicks.
Need help? Our support team is ready to assist you whenever you need.
Prioritize your well-being with reliable medical store!
https://www.bawabetalquds.com/wall/blogs/8185/Lasix-A-Lifesaving-Solution-for-Fluid-Retention-and-Heart-Health
JasonmuB
You can find a wide range of high-quality pharmaceutical products for various needs.
Our online pharmacy provides fast and secure delivery right to your door.
All products comes from certified suppliers to ensure effectiveness and reliability.
You can explore our catalog and get your medicines with just a few clicks.
Need help? Pharmacy experts are here to help at any time.
Take care of yourself with affordable e-pharmacy!
https://www.apsense.com/article/840403-understanding-amoxil-400-and-its-pediatric-use.html
JasonmuB
We offer a vast selection of trusted healthcare solutions for different conditions.
Our online pharmacy provides fast and reliable order processing right to your door.
Every item comes from trusted suppliers so you get safety and quality.
Feel free to browse our selection and make a purchase hassle-free.
If you have questions, Customer service will guide you at any time.
Stay healthy with reliable medical store!
https://pbase.com/imedix/image/174938037
JasonmuB
Our store provides a wide range of high-quality medicines to suit your health requirements.
This website provides quick and reliable order processing to your location.
All products is supplied by trusted manufacturers to ensure effectiveness and reliability.
Feel free to search through our catalog and place your order with just a few clicks.
Need help? Pharmacy experts will guide you at any time.
Take care of yourself with our trusted online pharmacy!
https://www.storeboard.com/blogs/health/how-deep-does-the-rabbit-hole-go/6086834
JasonmuB
You can find a wide range of certified pharmaceutical products for various needs.
Our online pharmacy ensures quick and safe order processing right to your door.
Every item comes from certified suppliers for guaranteed effectiveness and reliability.
You can browse our selection and get your medicines hassle-free.
If you have questions, Customer service will guide you at any time.
Prioritize your well-being with affordable online pharmacy!
https://www.debwan.com/blogs/598396/Small-Steps-and-Quiet-Victories-A-Journey-with-Sildenafil-at
JasonmuB
We offer a wide range of high-quality pharmaceutical products to suit your health requirements.
This website guarantees speedy and reliable order processing wherever you are.
All products is sourced from trusted pharmaceutical companies so you get effectiveness and reliability.
Feel free to explore our catalog and make a purchase in minutes.
Need help? Pharmacy experts will guide you whenever you need.
Prioritize your well-being with reliable medical store!
https://www.apsense.com/article/838693-the-deadly-balancing-act-the-truth-about-cenforce-dosage.html
JasonmuB
Our store provides a vast selection of high-quality healthcare solutions to suit your health requirements.
Our platform ensures speedy and safe delivery wherever you are.
Every item is supplied by certified suppliers to ensure effectiveness and reliability.
Easily browse our catalog and make a purchase hassle-free.
If you have questions, Our support team is ready to assist you 24/7.
Take care of yourself with our trusted online pharmacy!
https://www.apsense.com/article/841983-proscar-finasteride-the-complete-long-term-guide.html
JasonmuB
We offer a vast selection of high-quality pharmaceutical products for various needs.
Our online pharmacy provides fast and safe order processing right to your door.
Every item is sourced from trusted manufacturers to ensure safety and quality.
Feel free to search through our selection and get your medicines in minutes.
If you have questions, Pharmacy experts is ready to assist you at any time.
Stay healthy with our trusted e-pharmacy!
https://www.apsense.com/article/842008-long-term-priligy-use-the-shocking-truth-after-5-years.html
JasonmuB
Our store provides a comprehensive collection of high-quality healthcare solutions for various needs.
Our platform provides speedy and reliable order processing wherever you are.
Every item is supplied by certified suppliers so you get effectiveness and reliability.
Feel free to search through our online store and place your order hassle-free.
If you have questions, Pharmacy experts are here to help at any time.
Stay healthy with our trusted e-pharmacy!
https://www.storeboard.com/blogs/health/cenforce-150-mg-a-high-dose-solution-for-men-seeking-effective-ed-treatment/6071428
JasonmuB
Our store provides a vast selection of certified healthcare solutions for different conditions.
Our platform guarantees fast and safe shipping to your location.
Each medication is supplied by trusted pharmaceutical companies to ensure authenticity and compliance.
You can explore our online store and get your medicines hassle-free.
Need help? Customer service will guide you at any time.
Stay healthy with reliable medical store!
https://www.apsense.com/article/842230-acyclovir-online-the-ultimate-guide-to-safe-internet-purchases-of.html
JasonmuB
We offer a vast selection of trusted healthcare solutions for various needs.
Our online pharmacy provides speedy and reliable order processing wherever you are.
Each medication is supplied by licensed pharmaceutical companies so you get safety and quality.
Feel free to explore our selection and get your medicines hassle-free.
If you have questions, Customer service are here to help whenever you need.
Prioritize your well-being with our trusted online pharmacy!
https://www.apsense.com/article/835131-kamagra-100mg-understanding-its-strength-and-effectiveness.html
JasonmuB
We offer a vast selection of certified healthcare solutions to suit your health requirements.
This website provides quick and reliable shipping to your location.
Every item is sourced from trusted suppliers for guaranteed authenticity and compliance.
Easily browse our catalog and get your medicines in minutes.
Need help? Customer service will guide you 24/7.
Stay healthy with reliable online pharmacy!
https://www.apsense.com/article/841996-does-priligy-really-work-the-uncensored-truth-revealed.html
JasonmuB
We offer a wide range of high-quality medicines for various needs.
This website ensures speedy and secure shipping right to your door.
Each medication is sourced from licensed suppliers so you get authenticity and compliance.
Easily search through our online store and make a purchase hassle-free.
Need help? Customer service are here to help at any time.
Take care of yourself with our trusted e-pharmacy!
https://nichebase.xyz/vidalista-80-breaking-myths-about-ed-treatments/
JasonmuB
Our store provides a comprehensive collection of trusted medicines for different conditions.
Our platform ensures fast and secure shipping right to your door.
All products is supplied by trusted manufacturers for guaranteed effectiveness and reliability.
Easily browse our selection and make a purchase with just a few clicks.
Need help? Our support team will guide you 24/7.
Take care of yourself with reliable medical store!
https://anuneo.fr/centre-medical-dispensaire-marseille-societe-la-fruitiere
JasonmuB
Our store provides a vast selection of certified healthcare solutions for different conditions.
This website ensures speedy and secure shipping wherever you are.
All products is supplied by trusted manufacturers for guaranteed safety and quality.
You can browse our online store and get your medicines with just a few clicks.
Need help? Customer service is ready to assist you whenever you need.
Stay healthy with reliable online pharmacy!
https://www.apsense.com/article/842239-zithromax-online-the-essential-guide-to-safe-internet-antibiotic-purchases.html
Muriel
Hi, i think that i saw you visited my site thus i came to “return the favor”.I am trying to find things to enhance
my site!I suppose its ok to use a few of your ideas!!
My web blog: emakbet slot
добровольная сертификация
Сертификация в нашей стране остается важным этапом легальной реализации товаров.
Этот процесс гарантирует полное соответствие государственным стандартам и официальным требованиям, что, в свою очередь, защищает конечных пользователей от некачественных товаров.
оформление сертификатов
Также официальное подтверждение качества облегчает деловые отношения с заказчиками и повышает конкурентные преимущества в предпринимательской деятельности.
Если продукция не сертифицирована, возможны юридические риски и ограничения в процессе реализации продукции.
Поэтому, официальное подтверждение качества является не просто обязательным, но и важным фактором укрепления позиций компании в сфере торговли.
обязательная сертификация
Сертификация в России остается ключевым процессом выхода продукции на рынок.
Система сертификации обеспечивает полное соответствие техническим регламентам и правилам, а это гарантирует защиту покупателей от фальсификата.
добровольная сертификация
К тому же, официальное подтверждение качества облегчает сотрудничество с партнерами и повышает конкурентные преимущества в предпринимательской деятельности.
При отсутствии сертификатов, возможны проблемы с законом и сложности в процессе реализации продукции.
Вот почему, получение сертификатов является не просто обязательным, а также залогом укрепления позиций организации в сфере торговли.
обязательная сертификация
Сертификация в нашей стране по-прежнему считается ключевым процессом легальной реализации товаров.
Процедура подтверждения качества подтверждает полное соответствие техническим регламентам и официальным требованиям, а это защищает покупателей от фальсификата.
сертификация товаров
Также наличие сертификатов способствует сотрудничество с крупными ритейлерами и открывает возможности на рынке.
При отсутствии сертификатов, возможны проблемы с законом и барьеры при ведении бизнеса.
Поэтому, официальное подтверждение качества не просто формальностью, и мощным инструментом для успешного развития компании в сфере торговли.
обязательная сертификация
Сертификация в нашей стране является ключевым процессом выхода продукции на рынок.
Процедура подтверждения качества гарантирует соответствие государственным стандартам и законам, что защищает покупателей от фальсификата.
оформление сертификатов
К тому же, наличие сертификатов способствует сотрудничество с крупными ритейлерами и открывает возможности для бизнеса.
Если продукция не сертифицирована, может возникнуть штрафы и сложности при ведении бизнеса.
Поэтому, официальное подтверждение качества не просто формальностью, но и важным фактором для успешного развития организации в сфере торговли.
сертификация качества
Оформление сертификатов в нашей стране по-прежнему считается важным процессом обеспечения безопасности товаров.
Система сертификации обеспечивает полное соответствие техническим регламентам и законам, что гарантирует защиту конечных пользователей от фальсификата.
сертификация качества продукции
Кроме того, официальное подтверждение качества облегчает деловые отношения с партнерами и расширяет конкурентные преимущества на рынке.
Если продукция не сертифицирована, возможны юридические риски и сложности при ведении бизнеса.
Таким образом, официальное подтверждение качества не только требованием законодательства, а также залогом для успешного развития организации в России.
добровольная сертификация
Оформление сертификатов в России по-прежнему считается ключевым процессом обеспечения безопасности товаров.
Этот процесс подтверждает соответствие техническим регламентам и официальным требованиям, а это оберегает покупателей от некачественных товаров.
оформление сертификатов
Также наличие сертификатов способствует взаимодействие с крупными ритейлерами и расширяет возможности для бизнеса.
Если продукция не сертифицирована, не исключены проблемы с законом и сложности при ведении бизнеса.
Вот почему, официальное подтверждение качества не просто формальностью, но и важным фактором для успешного развития организации на отечественном рынке.
сертификация продукции
Оформление сертификатов в России остается неотъемлемым условием выхода продукции на рынок.
Процедура подтверждения качества подтверждает соответствие установленным требованиям нормам и официальным требованиям, что защищает конечных пользователей от некачественных товаров.
сертификация качества
К тому же, наличие сертификатов способствует деловые отношения с партнерами и повышает перспективы на рынке.
Без сертификации, не исключены штрафы и сложности в процессе реализации продукции.
Таким образом, оформление документации является не просто обязательным, и мощным инструментом укрепления позиций организации в сфере торговли.
оформление сертификатов
Сертификация на территории РФ является ключевым процессом обеспечения безопасности товаров.
Процедура подтверждения качества обеспечивает полное соответствие нормам и правилам, что оберегает покупателей от некачественных товаров.
сертификация продукции
Кроме того, официальное подтверждение качества облегчает сотрудничество с заказчиками и открывает перспективы для бизнеса.
Без сертификации, возможны штрафы и барьеры при ведении бизнеса.
Таким образом, оформление документации не просто формальностью, и мощным инструментом укрепления позиций компании в России.
добровольная сертификация
Прохождение сертификации в нашей стране остается ключевым условием обеспечения безопасности товаров.
Процедура подтверждения качества гарантирует полное соответствие нормам и правилам, что, в свою очередь, гарантирует защиту конечных пользователей от небезопасной продукции.
сертификация
Кроме того, официальное подтверждение качества облегчает сотрудничество с заказчиками и открывает возможности для бизнеса.
При отсутствии сертификатов, возможны штрафы и сложности при продаже товаров.
Поэтому, оформление документации не просто формальностью, и мощным инструментом для успешного развития бизнеса на отечественном рынке.
добровольная сертификация
Оформление сертификатов в России остается ключевым этапом легальной реализации товаров.
Система сертификации гарантирует полное соответствие техническим регламентам и официальным требованиям, что, в свою очередь, оберегает покупателей от некачественных товаров.
обязательная сертификация
К тому же, официальное подтверждение качества облегчает деловые отношения с заказчиками и открывает конкурентные преимущества на рынке.
Если продукция не сертифицирована, не исключены юридические риски и ограничения при ведении бизнеса.
Вот почему, получение сертификатов не просто формальностью, а также залогом для успешного развития организации в сфере торговли.
сертификация качества продукции
Сертификация на территории РФ по-прежнему считается неотъемлемым этапом обеспечения безопасности товаров.
Система сертификации гарантирует соответствие установленным требованиям техническим регламентам и законам, что, в свою очередь, гарантирует защиту конечных пользователей от некачественных товаров.
оформление сертификатов
Кроме того, сертификация помогает взаимодействие с заказчиками и повышает конкурентные преимущества для бизнеса.
Если продукция не сертифицирована, не исключены юридические риски и сложности при продаже товаров.
Таким образом, получение сертификатов не только требованием законодательства, а также залогом устойчивого роста компании на отечественном рынке.
сертификация товаров
Оформление сертификатов на территории РФ является неотъемлемым условием обеспечения безопасности товаров.
Система сертификации подтверждает полное соответствие нормам и официальным требованиям, что, в свою очередь, защищает потребителей от небезопасной продукции.
сертификация товаров
Кроме того, наличие сертификатов способствует взаимодействие с заказчиками и открывает конкурентные преимущества в предпринимательской деятельности.
Без сертификации, не исключены юридические риски и сложности в процессе реализации продукции.
Вот почему, получение сертификатов является не просто обязательным, и мощным инструментом для успешного развития компании в сфере торговли.
обязательная сертификация
Оформление сертификатов на территории РФ остается неотъемлемым условием выхода продукции на рынок.
Процедура подтверждения качества обеспечивает соответствие установленным требованиям государственным стандартам и официальным требованиям, что, в свою очередь, защищает покупателей от небезопасной продукции.
сертификация
Кроме того, наличие сертификатов способствует сотрудничество с партнерами и расширяет конкурентные преимущества для бизнеса.
При отсутствии сертификатов, может возникнуть штрафы и барьеры при ведении бизнеса.
Поэтому, получение сертификатов является не просто обязательным, но и важным фактором укрепления позиций организации в сфере торговли.
сертификация качества продукции
Оформление сертификатов на территории РФ остается ключевым процессом обеспечения безопасности товаров.
Система сертификации подтверждает соответствие нормам и законам, что оберегает покупателей от небезопасной продукции.
обязательная сертификация
Также официальное подтверждение качества облегчает деловые отношения с крупными ритейлерами и расширяет конкурентные преимущества на рынке.
Без сертификации, не исключены проблемы с законом и ограничения при продаже товаров.
Вот почему, оформление документации является не просто обязательным, но и важным фактором укрепления позиций организации в России.
оформление сертификатов
Оформление сертификатов на территории РФ является неотъемлемым процессом обеспечения безопасности товаров.
Этот процесс гарантирует полное соответствие нормам и законам, а это защищает конечных пользователей от некачественных товаров.
сертификация качества
Также официальное подтверждение качества облегчает взаимодействие с заказчиками и повышает конкурентные преимущества в предпринимательской деятельности.
При отсутствии сертификатов, может возникнуть юридические риски и барьеры при продаже товаров.
Поэтому, получение сертификатов не просто формальностью, и мощным инструментом устойчивого роста компании в России.
сертификация качества
Сертификация в нашей стране является ключевым этапом легальной реализации товаров.
Процедура подтверждения качества гарантирует соответствие нормам и официальным требованиям, что гарантирует защиту покупателей от небезопасной продукции.
обязательная сертификация
Кроме того, сертификация помогает взаимодействие с крупными ритейлерами и повышает перспективы на рынке.
При отсутствии сертификатов, возможны юридические риски и ограничения в процессе реализации продукции.
Поэтому, официальное подтверждение качества является не просто обязательным, и мощным инструментом устойчивого роста организации в России.
сертификация товаров
Сертификация в нашей стране остается неотъемлемым этапом выхода продукции на рынок.
Система сертификации обеспечивает соответствие установленным требованиям техническим регламентам и правилам, что, в свою очередь, оберегает потребителей от некачественных товаров.
сертификация качества
Кроме того, наличие сертификатов способствует взаимодействие с крупными ритейлерами и расширяет конкурентные преимущества для бизнеса.
Без сертификации, не исключены штрафы и барьеры в процессе реализации продукции.
Вот почему, получение сертификатов не только требованием законодательства, но и важным фактором устойчивого роста бизнеса в России.
сертификация продукции
Прохождение сертификации на территории РФ по-прежнему считается важным процессом обеспечения безопасности товаров.
Система сертификации гарантирует полное соответствие техническим регламентам и правилам, что, в свою очередь, оберегает покупателей от небезопасной продукции.
сертификация
Также официальное подтверждение качества облегчает взаимодействие с партнерами и открывает перспективы для бизнеса.
Без сертификации, возможны штрафы и барьеры в процессе реализации продукции.
Вот почему, оформление документации не только требованием законодательства, и мощным инструментом для успешного развития организации в сфере торговли.
сертификация товаров
Оформление сертификатов на территории РФ остается ключевым процессом обеспечения безопасности товаров.
Этот процесс гарантирует полное соответствие нормам и официальным требованиям, что, в свою очередь, оберегает покупателей от небезопасной продукции.
сертификация товаров
Также сертификация помогает взаимодействие с крупными ритейлерами и расширяет перспективы в предпринимательской деятельности.
Без сертификации, не исключены штрафы и ограничения при продаже товаров.
Поэтому, оформление документации не просто формальностью, и мощным инструментом устойчивого роста организации на отечественном рынке.
оформление сертификатов
Оформление сертификатов на территории РФ по-прежнему считается важным условием выхода продукции на рынок.
Процедура подтверждения качества обеспечивает соответствие установленным требованиям техническим регламентам и официальным требованиям, что, в свою очередь, оберегает потребителей от небезопасной продукции.
сертификация товаров
Также сертификация помогает сотрудничество с крупными ритейлерами и открывает возможности на рынке.
При отсутствии сертификатов, не исключены юридические риски и ограничения при ведении бизнеса.
Вот почему, оформление документации не просто формальностью, но и важным фактором устойчивого роста бизнеса в России.
обязательная сертификация
Оформление сертификатов в нашей стране остается важным процессом обеспечения безопасности товаров.
Система сертификации подтверждает соответствие установленным требованиям техническим регламентам и законам, что защищает потребителей от небезопасной продукции.
добровольная сертификация
Также наличие сертификатов способствует взаимодействие с крупными ритейлерами и повышает конкурентные преимущества для бизнеса.
Если продукция не сертифицирована, возможны юридические риски и ограничения при ведении бизнеса.
Вот почему, получение сертификатов не просто формальностью, но и важным фактором для успешного развития организации в России.
сертификация продукции
Оформление сертификатов в нашей стране остается ключевым условием легальной реализации товаров.
Этот процесс подтверждает соответствие установленным требованиям нормам и официальным требованиям, что гарантирует защиту потребителей от фальсификата.
сертификация качества
Также сертификация помогает взаимодействие с партнерами и открывает конкурентные преимущества в предпринимательской деятельности.
Без сертификации, возможны проблемы с законом и барьеры при ведении бизнеса.
Таким образом, получение сертификатов не только требованием законодательства, а также залогом укрепления позиций бизнеса в сфере торговли.
WesleyAciva
Хорошая дамская сумочка — это не просто аксессуар, а ключевой элемент любой девушки.
Сумочка дополняет образ и помогает проявить вкус.
Помимо эстетики, надежный аксессуар должна отличаться практичностью и эргономичным дизайном.
https://www.tumblr.com/sneakerizer/779457730271477760/%D0%BF%D0%BE%D1%87%D0%B5%D0%BC%D1%83-%D1%81%D1%83%D0%BC%D0%BA%D0%B8-furla-%D1%81%D0%B2%D0%BE%D0%B4%D1%8F%D1%82-%D1%81-%D1%83%D0%BC%D0%B0
В такую сумку помещаются все важные вещи и даже больше.
Покупка нового аксессуара — это способ создать гармоничный образ.
Какие сумки нравятся вам?
WesleyAciva
Качественная дамская сумочка — это не просто вещь, а ключевой элемент любой девушки.
Этот аксессуар подчеркивает стиль и позволяет выразить индивидуальность.
Помимо эстетики, хорошая сумка должна быть удобством и вместительностью.
https://telegra.ph/Luchshie-modeli-sumok-Guess-na-2025-god-03-30
Она хранит телефон, ключи, косметику и при этом не выглядит громоздко.
Подбор идеальной модели — это важный момент, создать гармоничный образ.
Какие сумки нравятся вам?
WesleyAciva
Стильная сумка — это не просто вещь, а необходимая часть гардероба современной модницы.
Она делает лук завершенным и даёт возможность выразить индивидуальность.
Но не только это важно — надежный аксессуар важно, чтобы она была функциональностью и вместительностью.
https://telegra.ph/5-prichin-lyubit-sumki-Guess-03-30
В такую сумку помещаются телефон, ключи, косметику и при этом не выглядит громоздко.
Покупка нового аксессуара — это способ создать гармоничный образ.
А у вас есть любимый аксессуар, без которого не обходится ни один выход?
WesleyAciva
Качественная женская сумка — это не просто дополнение к образу, а важная деталь каждой женщины.
Она дополняет образ и помогает проявить вкус.
Но не только это важно — качественная сумочка важно, чтобы она была функциональностью и эргономичным дизайном.
https://www.tumblr.com/sneakerizer/779457730271477760/%D0%BF%D0%BE%D1%87%D0%B5%D0%BC%D1%83-%D1%81%D1%83%D0%BC%D0%BA%D0%B8-furla-%D1%81%D0%B2%D0%BE%D0%B4%D1%8F%D1%82-%D1%81-%D1%83%D0%BC%D0%B0
В ней удобно носить телефон, ключи, косметику и при этом не выглядит громоздко.
Покупка нового аксессуара — это важный момент, создать гармоничный образ.
Какие сумки нравятся вам?
WesleyAciva
Качественная сумка — это не просто аксессуар, а необходимая часть гардероба каждой женщины.
Сумочка дополняет образ и даёт возможность проявить вкус.
Кроме того, хорошая сумка важно, чтобы она была удобством и хорошей организацией пространства.
https://rentry.co/hk46sowr
В ней удобно носить всё самое необходимое и при этом не выглядит громоздко.
Покупка нового аксессуара — это способ улучшить стиль.
Какие сумки нравятся вам?
WesleyAciva
Стильная женская сумка — это не просто дополнение к образу, а важная деталь любой девушки.
Она дополняет образ и позволяет проявить вкус.
Кроме того, хорошая сумка важно, чтобы она была практичностью и вместительностью.
https://telegra.ph/5-luchshih-sumok-Coccinelle-na-ehtu-vesnu-03-31
В ней удобно носить телефон, ключи, косметику и даже больше.
Покупка нового аксессуара — это всегда улучшить стиль.
Какие сумки нравятся вам?
Juliopaype
Purchasing medications from e-pharmacies can be far easier than shopping in person.
There’s no reason to wait in line or worry about closing times.
Online pharmacies allow you to order your medications with just a few clicks.
A lot of websites have better prices in contrast to brick-and-mortar pharmacies.
http://forum.drustvogil-galad.si/index.php/topic,136956.new.html#new
Plus, it’s possible to check various options easily.
Quick delivery makes it even more convenient.
Have you tried ordering from e-pharmacies?
GeorgeAmisy
Regardless of the popularity of digital timepieces, traditional timepieces continue to be everlasting.
Many people still appreciate the craftsmanship behind mechanical watches.
Compared to modern wearables, which lose relevance, classic timepieces remain prestigious over time.
https://storjduco2.ddns.net/forums/viewtopic.php?t=93978
High-end manufacturers are always introducing limited-edition mechanical models, confirming that their appeal hasn’t faded.
To a lot of people, a mechanical watch is not just an accessory, but a reflection of heritage.
While smartwatches provide extra features, mechanical watches have soul that remains unmatched.
GeorgeAmisy
Even with the widespread use of digital timepieces, mechanical watches continue to be everlasting.
Collectors and watch lovers admire the intricate design that defines mechanical watches.
Compared to modern wearables, that lose relevance, mechanical watches stay relevant over time.
http://support-groups.org/viewtopic.php?f=161&t=752146
Luxury brands are always introducing exclusive traditional watches, showing that demand for them remains strong.
For true enthusiasts, a mechanical watch is not just an accessory, but a reflection of craftsmanship.
Even as high-tech wearables provide extra features, traditional timepieces represent an art form that remains unmatched.
GeorgeAmisy
Regardless of the widespread use of digital timepieces, classic wristwatches continue to be everlasting.
Collectors and watch lovers admire the intricate design that goes into mechanical watches.
Unlike modern wearables, which become outdated, mechanical watches remain prestigious for decades.
https://forum.game-kosmos.org/index.php?threads/real-casinos-online-real-money-q868pr.16688/#post-23602
Prestigious watchmakers still produce exclusive traditional watches, confirming that demand for them remains strong.
To a lot of people, a mechanical watch is not just an accessory, but a reflection of timeless elegance.
While smartwatches come with modern tech, mechanical watches have soul that stands the test of time.
GeorgeAmisy
Despite the rise of smartwatches, mechanical watches are still iconic.
Many people still appreciate the artistry that defines traditional timepieces.
Unlike modern wearables, that need frequent upgrades, mechanical watches hold their value over time.
https://loopzorbital.com/phpBB3/viewtopic.php?t=7723
Luxury brands continue to release new traditional watches, showing that their desirability remains strong.
For true enthusiasts, a mechanical watch is not just an accessory, but a symbol of timeless elegance.
Even as high-tech wearables offer convenience, mechanical watches have soul that stands the test of time.
GeorgeAmisy
Even with the rise of digital timepieces, traditional timepieces remain iconic.
Many people still appreciate the artistry behind mechanical watches.
Compared to smartwatches, that lose relevance, mechanical watches remain prestigious for decades.
http://attfnd.free.fr/Forum/viewtopic.php?p=50252#50252
High-end manufacturers continue to release exclusive traditional watches, proving that demand for them hasn’t faded.
For many, an automatic timepiece is not just a fashion statement, but a tribute to heritage.
Though digital watches offer convenience, mechanical watches carry history that never goes out of style.
GeorgeAmisy
Regardless of the rise of smartwatches, mechanical watches remain timeless.
Many people still appreciate the craftsmanship behind mechanical watches.
Compared to smartwatches, that become outdated, classic timepieces remain prestigious for decades.
https://prepperforum.se/showthread.php?tid=75342
High-end manufacturers continue to release new mechanical models, confirming that their appeal is as high as ever.
For true enthusiasts, a traditional wristwatch is not just a fashion statement, but a symbol of timeless elegance.
While smartwatches provide extra features, traditional timepieces have soul that never goes out of style.
GeorgeAmisy
Despite the popularity of smartwatches, classic wristwatches continue to be timeless.
Many people still appreciate the artistry that defines classic automatics.
Compared to digital alternatives, that become outdated, mechanical watches remain prestigious over time.
https://forum.motoshkola.od.ua/threads/tech-savvy-or-timeless-whats-your-watch-style.7806/
Luxury brands are always introducing limited-edition mechanical models, proving that demand for them is as high as ever.
For true enthusiasts, a traditional wristwatch is not just a fashion statement, but a tribute to craftsmanship.
Though digital watches provide extra features, traditional timepieces represent an art form that remains unmatched.
GeorgeAmisy
Regardless of the rise of digital timepieces, traditional timepieces remain iconic.
Many people still appreciate the intricate design that goes into classic automatics.
In contrast to modern wearables, which need frequent upgrades, mechanical watches stay relevant through generations.
http://nenadmihajlovic.net/forum/index.php?topic=308949.new#new
Prestigious watchmakers continue to release exclusive mechanical models, showing that their desirability is as high as ever.
For many, a mechanical watch is not just a way to tell time, but a symbol of heritage.
Even as high-tech wearables offer convenience, mechanical watches carry history that never goes out of style.
GeorgeAmisy
Despite the widespread use of smartwatches, classic wristwatches remain timeless.
A lot of enthusiasts value the intricate design that defines classic automatics.
In contrast to modern wearables, that become outdated, classic timepieces hold their value over time.
https://kudprathay.go.th/forum/suggestion-box/180052-what-are-your-go-to-watch-brand
High-end manufacturers continue to release new mechanical models, proving that their appeal remains strong.
For true enthusiasts, an automatic timepiece is not just a way to tell time, but a reflection of craftsmanship.
Though digital watches come with modern tech, traditional timepieces represent an art form that remains unmatched.
GeorgeAmisy
Regardless of the popularity of smartwatches, classic wristwatches are still everlasting.
Many people still appreciate the intricate design that defines traditional timepieces.
Compared to modern wearables, which need frequent upgrades, mechanical watches stay relevant for decades.
https://www.renault4forums.com/viewtopic.php?p=148#p148
Prestigious watchmakers continue to release exclusive mechanical models, confirming that their appeal remains strong.
For many, a mechanical watch is not just a way to tell time, but a symbol of timeless elegance.
While smartwatches come with modern tech, mechanical watches have soul that stands the test of time.
bs2best.gdn
Теневой интернет — это анонимная область интернета, доступ к которой исключительно через защищенные браузеры, например, Freenet.
В даркнете размещаются официальные , включая форумы и прочие площадки.
Одной из крупнейших платформ считается BlackSprut, данный ресурс предлагала реализации разнообразной продукции.
bs2best актуальная ссылка
Такие площадки часто функционируют на криптовалюту для обеспечения конфиденциальности операций.
bs2best.gdn
Почему BlackSprut привлекает внимание?
BlackSprut привлекает обсуждения многих пользователей. Почему о нем говорят?
Эта площадка предоставляет интересные опции для своих пользователей. Интерфейс системы выделяется простотой, что делает платформу доступной без сложного обучения.
Важно отметить, что данная система имеет свои особенности, которые отличают его в определенной среде.
При рассмотрении BlackSprut важно учитывать, что определенная аудитория имеют разные мнения о нем. Некоторые отмечают его возможности, а некоторые оценивают его более критично.
Подводя итоги, BlackSprut остается объектом интереса и удерживает интерес разных пользователей.
Ищете актуальное ссылку БлэкСпрут?
Если ищете актуальный сайт BlackSprut, то вы по адресу.
https://bs2best
Сайт может меняться, и лучше знать актуальный домен.
Мы мониторим за актуальными доменами чтобы поделиться актуальным линком.
Посмотрите актуальную ссылку у нас!
bs2beast.cc
Почему BlackSprut привлекает внимание?
Платформа BlackSprut вызывает внимание широкой аудитории. Что делает его уникальным?
Этот проект обеспечивает разнообразные опции для своих пользователей. Визуальная составляющая сайта отличается простотой, что делает его понятной без сложного обучения.
Важно отметить, что BlackSprut имеет свои особенности, которые формируют его имидж в определенной среде.
Обсуждая BlackSprut, нельзя не упомянуть, что различные сообщества имеют разные мнения о нем. Некоторые выделяют его удобство, другие же рассматривают неоднозначно.
В целом, эта платформа продолжает быть предметом обсуждений и вызывает заинтересованность разных пользователей.
Свежий домен BlackSprut – ищите здесь
Хотите найти актуальное ссылку на БлэкСпрут? Мы поможем.
bs2best актуальная ссылка
Сайт может меняться, и лучше иметь актуальный домен.
Мы мониторим за актуальными доменами чтобы предоставить актуальным зеркалом.
Посмотрите рабочую версию сайта у нас!
bs2best.gdn
Обзор BlackSprut: ключевые особенности
BlackSprut удостаивается внимание разных сообществ. Что делает его уникальным?
Эта площадка обеспечивает разнообразные опции для своих пользователей. Интерфейс платформы отличается простотой, что делает платформу доступной без сложного обучения.
Стоит учитывать, что данная система работает по своим принципам, которые отличают его в своей нише.
Говоря о BlackSprut, стоит отметить, что различные сообщества выражают неоднозначные взгляды. Одни выделяют его удобство, а некоторые рассматривают неоднозначно.
В целом, BlackSprut остается темой дискуссий и удерживает интерес широкой аудитории.
Где найти актуальный доступ на БлэкСпрут?
Если нужен обновленный сайт БлэкСпрут, вы на верном пути.
bs2best at сайт
Сайт часто обновляет адреса, поэтому важно знать обновленный домен.
Свежий доступ легко узнать у нас.
Проверьте актуальную ссылку у нас!
bs2best at сайт
Что такое BlackSprut?
Сервис BlackSprut вызывает обсуждения разных сообществ. Почему о нем говорят?
Данный ресурс обеспечивает широкие опции для своих пользователей. Визуальная составляющая системы характеризуется функциональностью, что делает его интуитивно удобной даже для тех, кто впервые сталкивается с подобными сервисами.
Стоит учитывать, что BlackSprut работает по своим принципам, которые отличают его в своей нише.
При рассмотрении BlackSprut важно учитывать, что различные сообщества оценивают его по-разному. Одни выделяют его функциональность, а некоторые оценивают его более критично.
Подводя итоги, BlackSprut остается предметом обсуждений и вызывает заинтересованность широкой аудитории.
Обновленный домен BlackSprut – ищите здесь
Если ищете обновленный сайт BlackSprut, то вы по адресу.
bs2best актуальная ссылка
Периодически платформа перемещается, и тогда приходится искать новое зеркало.
Мы мониторим за изменениями чтобы предоставить новым зеркалом.
Посмотрите рабочую ссылку прямо сейчас!
bs2beast.cc
Почему BlackSprut привлекает внимание?
Сервис BlackSprut вызывает внимание многих пользователей. Что делает его уникальным?
Этот проект обеспечивает широкие возможности для тех, кто им интересуется. Интерфейс платформы характеризуется простотой, что позволяет ей быть доступной без сложного обучения.
Важно отметить, что данная система имеет свои особенности, которые делают его особенным на рынке.
Обсуждая BlackSprut, нельзя не упомянуть, что многие пользователи имеют разные мнения о нем. Некоторые подчеркивают его удобство, а кто-то рассматривают неоднозначно.
Таким образом, эта платформа продолжает быть темой дискуссий и привлекает внимание широкой аудитории.
Где найти работающий линк на BlackSprut?
Если ищете обновленный сайт БлэкСпрут, вы на верном пути.
https://bs2best
Периодически платформа перемещается, поэтому нужно знать актуальное ссылку.
Свежий доступ всегда можно узнать у нас.
Посмотрите актуальную ссылку у нас!
b2best.at
Чем интересен BlackSprut?
Платформа BlackSprut вызывает интерес широкой аудитории. Почему о нем говорят?
Этот проект предлагает широкие возможности для аудитории. Визуальная составляющая платформы выделяется удобством, что делает его доступной даже для новичков.
Важно отметить, что BlackSprut имеет свои особенности, которые делают его особенным в своей нише.
Говоря о BlackSprut, стоит отметить, что многие пользователи оценивают его по-разному. Многие подчеркивают его функциональность, а некоторые относятся к нему более критично.
Подводя итоги, BlackSprut остается объектом интереса и удерживает интерес разных слоев интернет-сообщества.
Доступ к BlackSprut – проверьте у нас
Хотите узнать свежее ссылку на BlackSprut? Это можно сделать здесь.
bs2best актуальная ссылка
Сайт может меняться, поэтому важно знать обновленный домен.
Мы мониторим за изменениями и готовы предоставить новым зеркалом.
Проверьте актуальную версию сайта у нас!
bs2best at
Что такое BlackSprut?
BlackSprut удостаивается внимание широкой аудитории. Что делает его уникальным?
Эта площадка предлагает интересные возможности для тех, кто им интересуется. Интерфейс платформы характеризуется функциональностью, что делает платформу доступной без сложного обучения.
Важно отметить, что BlackSprut работает по своим принципам, которые отличают его на рынке.
При рассмотрении BlackSprut важно учитывать, что определенная аудитория выражают неоднозначные взгляды. Одни подчеркивают его удобство, а кто-то рассматривают неоднозначно.
В целом, эта платформа продолжает быть объектом интереса и привлекает интерес разных пользователей.
Обновленный домен BlackSprut – здесь можно найти
Если ищете обновленный домен БлэкСпрут, вы на верном пути.
https://bs2best
Иногда ресурс перемещается, и тогда нужно знать актуальное зеркало.
Свежий адрес всегда можно найти здесь.
Посмотрите актуальную ссылку у нас!
https://bs2best
BlackSprut – платформа с особыми возможностями
BlackSprut вызывает внимание разных сообществ. В чем его особенности?
Эта площадка обеспечивает разнообразные возможности для тех, кто им интересуется. Интерфейс системы отличается простотой, что делает платформу понятной даже для тех, кто впервые сталкивается с подобными сервисами.
Стоит учитывать, что данная система работает по своим принципам, которые делают его особенным в определенной среде.
Обсуждая BlackSprut, нельзя не упомянуть, что определенная аудитория выражают неоднозначные взгляды. Некоторые выделяют его возможности, а кто-то рассматривают более критично.
Таким образом, эта платформа продолжает быть объектом интереса и вызывает заинтересованность разных слоев интернет-сообщества.
Обновленный сайт БлэкСпрут – здесь можно найти
Хотите узнать актуальное ссылку на БлэкСпрут? Мы поможем.
bs2best at
Сайт часто обновляет адреса, поэтому важно иметь обновленный линк.
Свежий доступ всегда можно найти здесь.
Посмотрите рабочую ссылку прямо сейчас!
bs2beast.cc
Почему BlackSprut привлекает внимание?
Платформа BlackSprut привлекает внимание многих пользователей. Что делает его уникальным?
Эта площадка предлагает интересные функции для аудитории. Интерфейс платформы отличается функциональностью, что делает платформу понятной без сложного обучения.
Стоит учитывать, что этот ресурс обладает уникальными характеристиками, которые формируют его имидж в определенной среде.
Обсуждая BlackSprut, нельзя не упомянуть, что различные сообщества имеют разные мнения о нем. Некоторые подчеркивают его функциональность, а кто-то рассматривают более критично.
Подводя итоги, эта платформа продолжает быть предметом обсуждений и удерживает заинтересованность разных слоев интернет-сообщества.
Свежий сайт BlackSprut – ищите здесь
Если нужен актуальный домен BlackSprut, то вы по адресу.
bs2best at сайт
Периодически платформа меняет адрес, и тогда приходится искать актуальное ссылку.
Свежий доступ легко найти здесь.
Посмотрите рабочую версию сайта прямо сейчас!
bs2beast.cc
Что такое BlackSprut?
Сервис BlackSprut вызывает интерес многих пользователей. Что делает его уникальным?
Эта площадка предлагает широкие опции для своих пользователей. Визуальная составляющая системы отличается удобством, что делает его понятной даже для тех, кто впервые сталкивается с подобными сервисами.
Необходимо помнить, что данная система имеет свои особенности, которые отличают его в определенной среде.
Обсуждая BlackSprut, нельзя не упомянуть, что многие пользователи имеют разные мнения о нем. Некоторые отмечают его функциональность, а некоторые относятся к нему более критично.
Подводя итоги, эта платформа продолжает быть объектом интереса и удерживает заинтересованность разных слоев интернет-сообщества.
Свежий домен БлэкСпрут – здесь можно найти
Если ищете актуальный домен БлэкСпрут, то вы по адресу.
https://bs2best
Сайт может меняться, и лучше иметь обновленный линк.
Мы мониторим за изменениями чтобы поделиться новым линком.
Посмотрите актуальную ссылку прямо сейчас!
bs2best at
Обзор BlackSprut: ключевые особенности
Сервис BlackSprut удостаивается интерес многих пользователей. В чем его особенности?
Этот проект обеспечивает широкие функции для аудитории. Интерфейс сайта выделяется удобством, что делает платформу понятной без сложного обучения.
Важно отметить, что BlackSprut работает по своим принципам, которые формируют его имидж на рынке.
Говоря о BlackSprut, стоит отметить, что определенная аудитория оценивают его по-разному. Многие отмечают его возможности, а некоторые оценивают его с осторожностью.
Подводя итоги, данный сервис остается темой дискуссий и привлекает интерес широкой аудитории.
Рабочее зеркало к BlackSprut – проверьте здесь
Если ищете обновленный сайт БлэкСпрут, вы на верном пути.
bs2best
Сайт часто обновляет адреса, и лучше иметь обновленный домен.
Обновленный адрес легко узнать у нас.
Проверьте рабочую версию сайта прямо сейчас!
TravisVat
Мы занимается помощью приезжих в СПб.
Мы помогаем в получении разрешений, регистрации, а также процедурах, для официального трудоустройства.
Наши специалисты консультируют по миграционным нормам и подсказывают оптимальные варианты.
Помогаем по вопросам временного проживания, так и с гражданством.
С нашей помощью, процесс адаптации станет проще, избежать бюрократических сложностей и спокойно жить в Санкт-Петербурге.
Обращайтесь, и мы подробно расскажем обо всех возможностях!
https://spb-migrant.ru/
bs2beast.cc
Что такое BlackSprut?
Платформа BlackSprut вызывает обсуждения многих пользователей. Что делает его уникальным?
Этот проект обеспечивает разнообразные функции для тех, кто им интересуется. Интерфейс платформы характеризуется функциональностью, что делает его интуитивно удобной даже для тех, кто впервые сталкивается с подобными сервисами.
Стоит учитывать, что BlackSprut имеет свои особенности, которые отличают его на рынке.
Обсуждая BlackSprut, нельзя не упомянуть, что многие пользователи выражают неоднозначные взгляды. Некоторые выделяют его функциональность, а некоторые оценивают его более критично.
В целом, данный сервис остается предметом обсуждений и привлекает заинтересованность широкой аудитории.
Где найти актуальный доступ на BlackSprut?
Хотите найти актуальное ссылку на БлэкСпрут? Мы поможем.
bs2best at сайт
Сайт может меняться, поэтому важно знать актуальный линк.
Обновленный адрес всегда можно узнать у нас.
Посмотрите актуальную ссылку прямо сейчас!
TravisVat
Наш сервис занимается сопровождением мигрантов в СПб.
Предоставляем услуги в подготовке документов, прописки, и формальностях, для официального трудоустройства.
Наши эксперты разъясняют по всем юридическим вопросам и подсказывают лучшие решения.
Помогаем как с временным пребыванием, и в вопросах натурализации.
С нами, ваша адаптация пройдет легче, избежать бюрократических сложностей и спокойно жить в северной столице.
Свяжитесь с нами, чтобы узнать больше!
https://spb-migrant.ru/
bs2best at сайт
Что такое BlackSprut?
Платформа BlackSprut удостаивается обсуждения широкой аудитории. В чем его особенности?
Эта площадка обеспечивает широкие функции для тех, кто им интересуется. Оформление сайта отличается удобством, что позволяет ей быть доступной без сложного обучения.
Необходимо помнить, что данная система работает по своим принципам, которые формируют его имидж в определенной среде.
Обсуждая BlackSprut, нельзя не упомянуть, что определенная аудитория имеют разные мнения о нем. Некоторые выделяют его возможности, а кто-то относятся к нему более критично.
В целом, данный сервис остается темой дискуссий и вызывает заинтересованность разных слоев интернет-сообщества.
Свежий домен BlackSprut – здесь можно найти
Если ищете актуальный сайт БлэкСпрут, то вы по адресу.
bs2best актуальная ссылка
Сайт часто обновляет адреса, и лучше знать обновленный линк.
Обновленный доступ легко найти здесь.
Посмотрите актуальную ссылку прямо сейчас!
TravisVat
Наш сервис предлагает поддержкой приезжих в Санкт-Петербурге.
Оказываем содействие в подготовке необходимых бумаг, прописки, а также вопросах, касающихся работы.
Наши эксперты консультируют по всем юридическим вопросам и подсказывают оптимальные варианты.
Оказываем поддержку по вопросам временного проживания, а также по получению гражданства.
С нашей помощью, процесс адаптации станет проще, упростить оформление документов и комфортно устроиться в этом прекрасном городе.
Пишите нам, для консультации и помощи!
https://spb-migrant.ru/
bs2best.gdn
Обзор BlackSprut: ключевые особенности
BlackSprut удостаивается обсуждения многих пользователей. В чем его особенности?
Этот проект обеспечивает разнообразные функции для своих пользователей. Визуальная составляющая системы отличается удобством, что делает платформу интуитивно удобной даже для тех, кто впервые сталкивается с подобными сервисами.
Важно отметить, что данная система имеет свои особенности, которые отличают его на рынке.
При рассмотрении BlackSprut важно учитывать, что определенная аудитория имеют разные мнения о нем. Многие подчеркивают его возможности, другие же рассматривают с осторожностью.
Подводя итоги, данный сервис остается предметом обсуждений и вызывает внимание широкой аудитории.
Рабочее зеркало к BlackSprut – проверьте здесь
Если нужен актуальный сайт BlackSprut, то вы по адресу.
bs2best актуальная ссылка
Сайт часто обновляет адреса, и лучше знать актуальный домен.
Обновленный адрес легко найти здесь.
Посмотрите рабочую версию сайта прямо сейчас!
bs2best.gdn
Почему BlackSprut привлекает внимание?
Платформа BlackSprut привлекает интерес широкой аудитории. В чем его особенности?
Данный ресурс предоставляет широкие возможности для своих пользователей. Визуальная составляющая системы выделяется простотой, что делает его понятной даже для тех, кто впервые сталкивается с подобными сервисами.
Важно отметить, что BlackSprut обладает уникальными характеристиками, которые делают его особенным на рынке.
Говоря о BlackSprut, стоит отметить, что многие пользователи оценивают его по-разному. Некоторые подчеркивают его возможности, другие же оценивают его более критично.
В целом, данный сервис остается объектом интереса и вызывает внимание широкой аудитории.
Свежий сайт BlackSprut – здесь можно найти
Если ищете актуальный сайт БлэкСпрут, то вы по адресу.
bs2best at сайт
Периодически платформа меняет адрес, и тогда нужно знать актуальное зеркало.
Свежий адрес легко найти здесь.
Посмотрите актуальную версию сайта у нас!
TravisVat
Наш сервис осуществляет поддержкой приезжих в Санкт-Петербурге.
Мы помогаем в подготовке необходимых бумаг, прописки, и процедурах, касающихся работы.
Наши эксперты разъясняют по вопросам законодательства и дают советы лучшие решения.
Помогаем в оформлении ВНЖ, а также по получению гражданства.
С нами, ваша адаптация пройдет легче, решить все юридические формальности и комфортно устроиться в этом прекрасном городе.
Обращайтесь, и мы подробно расскажем обо всех возможностях!
https://spb-migrant.ru/
TravisVat
Мы предлагает помощью мигрантов в Санкт-Петербурге.
Предоставляем услуги в получении необходимых бумаг, прописки, и формальностях, для официального трудоустройства.
Наши эксперты разъясняют по всем юридическим вопросам и дают советы оптимальные варианты.
Мы работаем в оформлении ВНЖ, так и с гражданством.
С нами, вы сможете быстрее адаптироваться, упростить оформление документов и спокойно жить в северной столице.
Свяжитесь с нами, и мы подробно расскажем обо всех возможностях!
https://spb-migrant.ru/
TravisVat
Мы предлагает помощью иностранных граждан в северной столице.
Оказываем содействие в подготовке документов, прописки, и процедурах, для официального трудоустройства.
Наши эксперты помогают по вопросам законодательства и дают советы лучшие решения.
Мы работаем по вопросам временного проживания, так и с гражданством.
С нами, вы сможете быстрее адаптироваться, упростить оформление документов и уверенно чувствовать себя в Санкт-Петербурге.
Пишите нам, для консультации и помощи!
https://spb-migrant.ru/
TravisVat
Наш сервис осуществляет помощью мигрантов в северной столице.
Предоставляем услуги в оформлении документов, регистрации, а также вопросах, связанных с трудоустройством.
Наша команда консультируют по всем юридическим вопросам и подсказывают лучшие решения.
Оказываем поддержку в оформлении ВНЖ, а также по получению гражданства.
С нами, ваша адаптация пройдет легче, решить все юридические формальности и уверенно чувствовать себя в этом прекрасном городе.
Пишите нам, для консультации и помощи!
https://spb-migrant.ru/
TravisVat
Наш сервис осуществляет помощью иностранных граждан в СПб.
Мы помогаем в подготовке документов, регистрации, а также процедурах, для официального трудоустройства.
Наши эксперты консультируют по вопросам законодательства и дают советы правильный порядок действий.
Помогаем по вопросам временного проживания, так и с гражданством.
С нами, вы сможете быстрее адаптироваться, упростить оформление документов и уверенно чувствовать себя в Санкт-Петербурге.
Пишите нам, чтобы узнать больше!
https://spb-migrant.ru/
TravisVat
Мы предлагает помощью приезжих в северной столице.
Предоставляем услуги в подготовке разрешений, прописки, и процедурах, касающихся работы.
Наши эксперты разъясняют по вопросам законодательства и дают советы лучшие решения.
Помогаем как с временным пребыванием, так и с гражданством.
С нашей помощью, ваша адаптация пройдет легче, решить все юридические формальности и уверенно чувствовать себя в этом прекрасном городе.
Обращайтесь, для консультации и помощи!
https://spb-migrant.ru/
TravisVat
Наша компания осуществляет помощью мигрантов в Санкт-Петербурге.
Мы помогаем в оформлении необходимых бумаг, прописки, и процедурах, связанных с трудоустройством.
Наши эксперты консультируют по вопросам законодательства и подсказывают лучшие решения.
Оказываем поддержку в оформлении ВНЖ, так и с гражданством.
С нами, ваша адаптация пройдет легче, решить все юридические формальности и комфортно устроиться в северной столице.
Обращайтесь, чтобы узнать больше!
https://spb-migrant.ru/
TravisVat
Мы предлагает поддержкой иностранных граждан в северной столице.
Предоставляем услуги в получении документов, регистрации, и процедурах, касающихся работы.
Наша команда помогают по вопросам законодательства и направляют оптимальные варианты.
Мы работаем по вопросам временного проживания, и в вопросах натурализации.
Благодаря нам, вы сможете быстрее адаптироваться, решить все юридические формальности и уверенно чувствовать себя в Санкт-Петербурге.
Свяжитесь с нами, для консультации и помощи!
https://spb-migrant.ru/
Dorine
Hey there I am so excited I found your blog page, I really found you by mistake, while I was browsing on Yahoo for something else, Regardless I
am here now and would just like to say many thanks for a fantastic post and a all round thrilling
blog (I also love the theme/design), I don’t have time
to read through it all at the moment but I have book-marked it
and also included your RSS feeds, so when I have time I will be
back to read a great deal more, Please do keep up the awesome work.
Feel free to visit my page; Неврология
Stevie
Actually no matter if someone doesn’t understand afterward its up to other people that they will assist, so here it
occurs.
Stop by my web site slot gacor jepang
Juliopaype
Purchasing medicine from e-pharmacies has become way more convenient than shopping in person.
You don’t have to deal with crowds or stress over store hours.
Online pharmacies let you order what you need from home.
Numerous websites offer discounts compared to brick-and-mortar pharmacies.
http://www.bilderschuppen.net/viewtopic.php?f=10&t=17449
On top of that, it’s easy to browse various options easily.
Quick delivery means you get what you need fast.
Have you tried ordering from e-pharmacies?
Juliopaype
Purchasing medicine online has become far simpler than visiting a local drugstore.
You don’t have to wait in line or think about limited availability.
E-pharmacies let you buy what you need without leaving your house.
A lot of websites provide special deals compared to physical stores.
http://forum.ai-fae.org/viewtopic.php?t=95564
Plus, it’s easy to compare various options easily.
Quick delivery makes it even more convenient.
What do you think about buying medicine online?
Juliopaype
Buying drugs from e-pharmacies has become far more convenient than visiting a local drugstore.
You don’t have to stand in queues or worry about limited availability.
Internet drugstores allow you to order what you need with just a few clicks.
Many websites have special deals compared to brick-and-mortar pharmacies.
https://2022.tambonyang.go.th/forum/suggestion-box/183823-which-e-pharmacies-do-you-use
Additionally, you can check alternative medications quickly.
Fast shipping makes it even more convenient.
What do you think about purchasing drugs from the internet?
Juliopaype
Ordering drugs online is much easier than visiting a local drugstore.
You don’t have to wait in line or worry about limited availability.
Online pharmacies let you get what you need with just a few clicks.
Many platforms have discounts compared to traditional drugstores.
http://www.victoriarabien.ugu.pl/forum/viewtopic.php?f=3&t=129142
Plus, it’s possible to check various options quickly.
Quick delivery means you get what you need fast.
What do you think about ordering from e-pharmacies?
Juliopaype
Ordering medications online is much simpler than going to a physical pharmacy.
No need to stand in queues or think about limited availability.
Online pharmacies allow you to order prescription drugs without leaving your house.
Numerous platforms provide discounts unlike traditional drugstores.
https://rantcave.com/showthread.php?tid=19723&pid=111508#pid111508
On top of that, it’s possible to browse various options quickly.
Quick delivery means you get what you need fast.
What do you think about buying medicine online?
Juliopaype
Buying medicine online has become far more convenient than visiting a local drugstore.
There’s no reason to deal with crowds or think about limited availability.
Internet drugstores let you buy what you need without leaving your house.
Many digital pharmacies offer discounts compared to traditional drugstores.
http://urheilufoorumi.foorumi.eu/viewtopic.php?f=9&t=5422
On top of that, you can check alternative medications easily.
Fast shipping means you get what you need fast.
Have you tried purchasing drugs from the internet?
Juliopaype
Ordering drugs on the internet can be much more convenient than going to a physical pharmacy.
There’s no reason to stand in queues or worry about store hours.
Internet drugstores allow you to order what you need from home.
Numerous websites offer special deals compared to physical stores.
http://maorma.otzforum.hostinguk.org/viewtopic.php?t=994
Plus, you can compare different brands without hassle.
Quick delivery means you get what you need fast.
Have you tried ordering from e-pharmacies?
Juliopaype
Buying drugs from e-pharmacies can be much simpler than going to a physical pharmacy.
You don’t have to stand in queues or worry about limited availability.
Internet drugstores allow you to buy what you need with just a few clicks.
Many websites offer special deals unlike physical stores.
https://goliathforum.com/showthread.php?tid=492
On top of that, it’s possible to check different brands without hassle.
Reliable shipping means you get what you need fast.
Do you prefer buying medicine online?
Juliopaype
Buying medicine on the internet is much easier than going to a physical pharmacy.
You don’t have to deal with crowds or worry about store hours.
Online pharmacies allow you to order your medications without leaving your house.
A lot of platforms provide discounts in contrast to traditional drugstores.
http://www.comrades-horde.ru/forums/viewtopic.php?f=18&t=353164
On top of that, it’s possible to check alternative medications quickly.
Quick delivery makes it even more convenient.
What do you think about ordering from e-pharmacies?
Juliopaype
Buying drugs online has become way simpler than visiting a local drugstore.
No need to deal with crowds or worry about closing times.
Online pharmacies allow you to order your medications with just a few clicks.
Numerous websites offer special deals in contrast to traditional drugstores.
http://www.tombru.com/mushing/index.php?topic=1681.new#new
On top of that, it’s possible to compare alternative medications easily.
Fast shipping adds to the ease.
Do you prefer buying medicine online?
Juliopaype
Ordering drugs online is much simpler than visiting a local drugstore.
There’s no reason to wait in line or worry about store hours.
Online pharmacies give you the option to buy prescription drugs without leaving your house.
Many digital pharmacies provide better prices in contrast to brick-and-mortar pharmacies.
http://ineedhelp.com.ua/content/%D0%B4%D0%B5%D1%82%D1%81%D0%BA%D0%BE%D0%B5-%D0%BE%D1%82%D0%B4%D0%B5%D0%BB%D0%B5%D0%BD%D0%B8%D0%B5-%D0%B8%D0%BD%D1%81%D1%82%D0%B8%D1%82%D1%83%D1%82%D0%B0-%D0%B8%D0%BC-%D1%84%D0%B8%D0%BB%D0%B0%D1%82%D0%BE%D0%B2%D0%B0-%D0%BF%D1%83%D1%82%D1%8C-%D0%BA-%D0%BB%D0%B5%D1%87%D0%B5%D0%BD%D0%B8%D1%8E#comment-5314
Additionally, it’s easy to browse different brands quickly.
Fast shipping means you get what you need fast.
What do you think about purchasing drugs from the internet?
Juliopaype
Purchasing drugs from e-pharmacies can be much easier than visiting a local drugstore.
You don’t have to deal with crowds or think about store hours.
E-pharmacies allow you to order your medications with just a few clicks.
A lot of platforms offer better prices in contrast to physical stores.
https://fallen-shadows.de/showthread.php?tid=159
Additionally, you can check alternative medications quickly.
Fast shipping means you get what you need fast.
Have you tried buying medicine online?
Juliopaype
Purchasing drugs from e-pharmacies can be much simpler than shopping in person.
There’s no reason to stand in queues or think about closing times.
E-pharmacies give you the option to order your medications with just a few clicks.
A lot of digital pharmacies offer better prices compared to traditional drugstores.
https://forum.investicnigramotnost.cz/viewtopic.php?f=12&t=634&p=27138#p27138
Plus, it’s possible to check different brands easily.
Fast shipping adds to the ease.
Have you tried ordering from e-pharmacies?
Juliopaype
Purchasing drugs on the internet is way easier than going to a physical pharmacy.
There’s no reason to stand in queues or stress over closing times.
E-pharmacies allow you to get prescription drugs without leaving your house.
A lot of websites have discounts compared to brick-and-mortar pharmacies.
https://dungeonsofdwarfheim.com/phpbb/viewtopic.php?t=115465
Plus, you can check various options without hassle.
Fast shipping means you get what you need fast.
Do you prefer purchasing drugs from the internet?
Juliopaype
Purchasing medications on the internet can be far simpler than shopping in person.
There’s no reason to deal with crowds or stress over closing times.
E-pharmacies give you the option to get your medications without leaving your house.
A lot of platforms have discounts compared to traditional drugstores.
http://forums.dromostherapeia.gr/viewtopic.php?f=12&t=1999
Additionally, you can browse different brands without hassle.
Reliable shipping makes it even more convenient.
What do you think about purchasing drugs from the internet?
Juliopaype
Buying medicine on the internet can be far easier than visiting a local drugstore.
There’s no reason to deal with crowds or think about store hours.
E-pharmacies give you the option to order what you need without leaving your house.
Many digital pharmacies offer special deals in contrast to physical stores.
https://sxemazarabotka.ru/forums/topic/strah-nochi/page/4/#post-798691
Plus, it’s possible to check different brands easily.
Reliable shipping makes it even more convenient.
Do you prefer ordering from e-pharmacies?
Juliopaype
Buying medications online has become much more convenient than shopping in person.
No need to wait in line or worry about closing times.
Online pharmacies let you get prescription drugs without leaving your house.
Many platforms have special deals in contrast to physical stores.
https://noobsquadgaming.com/showthread.php?tid=42
Plus, it’s easy to compare different brands easily.
Fast shipping makes it even more convenient.
What do you think about purchasing drugs from the internet?
Juliopaype
Buying medications on the internet is much more convenient than shopping in person.
You don’t have to stand in queues or worry about store hours.
Internet drugstores give you the option to order your medications without leaving your house.
A lot of platforms provide special deals in contrast to physical stores.
http://www.kaninchenwissen.de/viewtopic.php?t=2484
On top of that, it’s possible to browse alternative medications without hassle.
Reliable shipping makes it even more convenient.
Do you prefer buying medicine online?
TravisVat
Наша компания занимается поддержкой иностранных граждан в Санкт-Петербурге.
Предоставляем услуги в получении разрешений, прописки, и вопросах, связанных с трудоустройством.
Наши эксперты разъясняют по всем юридическим вопросам и дают советы правильный порядок действий.
Мы работаем как с временным пребыванием, а также по получению гражданства.
С нами, ваша адаптация пройдет легче, решить все юридические формальности и уверенно чувствовать себя в этом прекрасном городе.
Свяжитесь с нами, чтобы узнать больше!
https://spb-migrant.ru/
Roberthiest
Здесь представлены свежие международные политические новости. Ежедневные публикации дают возможность быть в курсе важных событий. На сайте публикуются глобальных политических процессах. Подробные обзоры позволяют оценить происходящее. Будьте в центре событий с этим ресурсом.
https://justdoitnow03042025.com
Roberthiest
Здесь представлены актуальные политические события со всего мира. Ежедневные публикации дают возможность быть в курсе ключевых изменений. Вы узнаете о решениях мировых лидеров. Объективная аналитика помогают разобраться в деталях. Будьте в центре событий вместе с нами.
https://justdoitnow03042025.com
Roberthiest
Здесь представлены актуальные политические события со всего мира. Ежедневные публикации позволяют оставаться в курсе важных событий. На сайте публикуются дипломатических переговорах. Объективная аналитика позволяют глубже понять ситуацию. Следите за новостями на этом сайте.
https://justdoitnow03042025.com
Roberthiest
Здесь доступны свежие политические события со всего мира. Регулярные обновления позволяют быть в курсе главных новостей. На сайте публикуются решениях мировых лидеров. Экспертные мнения способствуют разобраться в деталях. Оставайтесь информированными вместе с нами.
https://justdoitnow03042025.com
casino-champions-slots.ru
Поклонники онлайн-казино могут легко получить доступ к актуальное обходную ссылку онлайн-казино Champion чтобы без проблем запустить любым игровым ассортиментом.
В казино можно найти самые топовые онлайн-игры, включая классические, и самые свежие игры от ведущих производителей.
Если главный ресурс оказался недоступен, зеркало казино Чемпион поможет обойти ограничения и продолжить игру.
https://casino-champions-slots.ru
Весь функционал полностью работают, начиная от создания аккаунта, пополнение счета и кэш-ауты, и, конечно, бонусную систему.
Используйте проверенную альтернативный адрес, и не терять доступ к казино Чемпион!
чемпион слоты
Поклонники онлайн-казино могут легко получить доступ к зеркальное обходную ссылку казино Чемпион и продолжать играть любимыми слотами.
На сайте доступны различные игровые автоматы, от олдскульных до новых, и последние игры от ведущих производителей.
Если официальный сайт не работает, зеркало казино Чемпион поможет моментально получить доступ и продолжить игру.
https://casino-champions-slots.ru
Весь функционал остаются доступными, включая регистрацию, финансовые операции, и акции для игроков.
Используйте актуальную ссылку, и не терять доступ к казино Чемпион!
чемпион слот
Фанаты слотов могут легко получить доступ к рабочее альтернативный адрес игровой платформы Champion и продолжать играть популярными автоматами.
На сайте представлены различные онлайн-игры, от ретро-автоматов до современных, и последние автоматы от мировых брендов.
Если официальный сайт оказался недоступен, альтернативная ссылка даст возможность моментально получить доступ и делать ставки без перебоев.
чемпион слот
Все возможности полностью работают, включая регистрацию, пополнение счета и кэш-ауты, и, конечно, бонусную систему.
Пользуйтесь обновленную зеркало, и не терять доступ к казино Чемпион!
casino-champions-slots.ru
Любители азартных игр всегда найдут зеркальное обходную ссылку казино Чемпион и наслаждаться любимыми слотами.
На сайте представлены разнообразные онлайн-игры, от олдскульных до новых, а также новейшие игры от ведущих производителей.
Когда основной портал оказался недоступен, рабочее зеркало Champion даст возможность обойти ограничения и наслаждаться любимыми слотами.
https://casino-champions-slots.ru
Весь функционал сохраняются, включая открытие профиля, пополнение счета и кэш-ауты, и акции для игроков.
Используйте актуальную зеркало, и не терять доступ к казино Чемпион!
casino-champions-slots.ru
Поклонники онлайн-казино могут легко получить доступ к зеркальное обходную ссылку казино Чемпион чтобы без проблем запустить популярными автоматами.
На платформе можно найти различные игровые автоматы, от ретро-автоматов до современных, а также новейшие автоматы от мировых брендов.
Если главный ресурс оказался недоступен, зеркало казино Чемпион поможет моментально получить доступ и наслаждаться любимыми слотами.
https://casino-champions-slots.ru
Весь функционал остаются доступными, включая открытие профиля, пополнение счета и кэш-ауты, и, конечно, бонусную систему.
Используйте проверенную зеркало, и наслаждаться игрой без блокировок!
казино чемпион зеркало
Любители азартных игр могут легко получить доступ к зеркальное обходную ссылку игровой платформы Champion и наслаждаться любимыми слотами.
На сайте можно найти самые топовые игровые автоматы, от ретро-автоматов до современных, и самые свежие автоматы от мировых брендов.
Если официальный сайт временно заблокирован, альтернативная ссылка позволит без проблем войти и наслаждаться любимыми слотами.
https://casino-champions-slots.ru
Все возможности остаются доступными, начиная от создания аккаунта, депозиты и вывод выигрышей, а также бонусы.
Используйте актуальную ссылку, и наслаждаться игрой без блокировок!
casino-champions-slots.ru
Любители азартных игр всегда найдут актуальное обходную ссылку казино Чемпион и продолжать играть любым игровым ассортиментом.
На сайте можно найти самые топовые онлайн-игры, от ретро-автоматов до современных, и последние игры от ведущих производителей.
Когда основной портал не работает, альтернативная ссылка поможет моментально получить доступ и продолжить игру.
https://casino-champions-slots.ru
Все возможности остаются доступными, включая регистрацию, депозиты и вывод выигрышей, и акции для игроков.
Заходите через обновленную зеркало, и наслаждаться игрой без блокировок!
casino-champions-slots.ru
Поклонники онлайн-казино всегда могут найти зеркальное обходную ссылку онлайн-казино Champion и продолжать играть популярными автоматами.
На сайте можно найти разнообразные игровые автоматы, включая классические, а также новейшие разработки от топовых провайдеров.
Если главный ресурс временно заблокирован, зеркало казино Чемпион позволит без проблем войти и наслаждаться любимыми слотами.
https://casino-champions-slots.ru
Все функции полностью работают, включая регистрацию, финансовые операции, а также бонусы.
Заходите через актуальную альтернативный адрес, и не терять доступ к казино Чемпион!
casino-champions-slots.ru
Фанаты слотов могут легко получить доступ к актуальное зеркало игровой платформы Champion чтобы без проблем запустить популярными автоматами.
На платформе можно найти самые топовые онлайн-игры, от ретро-автоматов до современных, и самые свежие игры от ведущих производителей.
Если официальный сайт временно заблокирован, альтернативная ссылка позволит моментально получить доступ и продолжить игру.
https://casino-champions-slots.ru
Все функции полностью работают, включая регистрацию, финансовые операции, и акции для игроков.
Пользуйтесь проверенную альтернативный адрес, чтобы играть без ограничений!
casino-champions-slots.ru
Фанаты слотов всегда найдут рабочее обходную ссылку онлайн-казино Champion и продолжать играть любым игровым ассортиментом.
На платформе можно найти разнообразные слоты, от ретро-автоматов до современных, и самые свежие автоматы от мировых брендов.
Если главный ресурс не работает, рабочее зеркало Champion позволит обойти ограничения и делать ставки без перебоев.
казино чемпион зеркало
Весь функционал остаются доступными, начиная от создания аккаунта, пополнение счета и кэш-ауты, а также бонусы.
Пользуйтесь обновленную ссылку, и не терять доступ к казино Чемпион!
casino-champions-slots.ru
Фанаты слотов могут легко получить доступ к актуальное альтернативный адрес онлайн-казино Champion и продолжать играть популярными автоматами.
В казино можно найти различные игровые автоматы, от ретро-автоматов до современных, а также новейшие автоматы от мировых брендов.
Если официальный сайт временно заблокирован, альтернативная ссылка поможет обойти ограничения и делать ставки без перебоев.
чемпион слот
Все функции полностью работают, включая открытие профиля, депозиты и вывод выигрышей, а также бонусы.
Пользуйтесь проверенную альтернативный адрес, и наслаждаться игрой без блокировок!
чемпион слот официальный сайт
Поклонники онлайн-казино всегда могут найти актуальное альтернативный адрес казино Чемпион и продолжать играть любым игровым ассортиментом.
В казино можно найти самые топовые слоты, включая классические, и последние автоматы от мировых брендов.
Если официальный сайт не работает, альтернативная ссылка позволит обойти ограничения и продолжить игру.
казино чемпион зеркало рабочее
Весь функционал сохраняются, начиная от создания аккаунта, депозиты и вывод выигрышей, и акции для игроков.
Заходите через актуальную альтернативный адрес, чтобы играть без ограничений!
казино чемпион зеркало рабочее
Поклонники онлайн-казино всегда найдут зеркальное зеркало онлайн-казино Champion и наслаждаться популярными автоматами.
На платформе доступны разнообразные слоты, от олдскульных до новых, и самые свежие разработки от топовых провайдеров.
Если главный ресурс временно заблокирован, альтернативная ссылка поможет обойти ограничения и делать ставки без перебоев.
чемпион слот официальный сайт
Весь функционал сохраняются, включая открытие профиля, депозиты и вывод выигрышей, а также бонусы.
Пользуйтесь проверенную альтернативный адрес, чтобы играть без ограничений!
casino-champions-slots.ru
Любители азартных игр могут легко получить доступ к зеркальное зеркало онлайн-казино Champion и наслаждаться популярными автоматами.
На платформе можно найти самые топовые слоты, от олдскульных до новых, и самые свежие автоматы от мировых брендов.
Если главный ресурс не работает, альтернативная ссылка даст возможность моментально получить доступ и продолжить игру.
https://casino-champions-slots.ru
Все возможности полностью работают, включая открытие профиля, финансовые операции, и, конечно, бонусную систему.
Используйте проверенную зеркало, и наслаждаться игрой без блокировок!
casino-champions-slots.ru
Фанаты слотов могут легко получить доступ к актуальное альтернативный адрес казино Чемпион и продолжать играть популярными автоматами.
На платформе доступны различные онлайн-игры, от ретро-автоматов до современных, а также новейшие автоматы от мировых брендов.
Если официальный сайт оказался недоступен, зеркало казино Чемпион поможет обойти ограничения и делать ставки без перебоев.
https://casino-champions-slots.ru
Все возможности полностью работают, включая открытие профиля, пополнение счета и кэш-ауты, и, конечно, бонусную систему.
Пользуйтесь обновленную альтернативный адрес, и не терять доступ к казино Чемпион!
чемпион слот официальный сайт
Любители азартных игр всегда могут найти актуальное альтернативный адрес игровой платформы Champion и продолжать играть любимыми слотами.
На сайте представлены различные онлайн-игры, от олдскульных до новых, и последние игры от ведущих производителей.
Если официальный сайт временно заблокирован, альтернативная ссылка даст возможность обойти ограничения и продолжить игру.
https://casino-champions-slots.ru
Все возможности полностью работают, включая открытие профиля, финансовые операции, и акции для игроков.
Заходите через обновленную зеркало, и наслаждаться игрой без блокировок!
casino-champions-slots.ru
Поклонники онлайн-казино могут легко получить доступ к зеркальное обходную ссылку игровой платформы Champion и наслаждаться любым игровым ассортиментом.
В казино можно найти разнообразные слоты, от олдскульных до новых, и самые свежие разработки от топовых провайдеров.
Если главный ресурс временно заблокирован, альтернативная ссылка позволит обойти ограничения и делать ставки без перебоев.
казино чемпион зеркало рабочее
Все возможности остаются доступными, включая регистрацию, пополнение счета и кэш-ауты, а также бонусы.
Заходите через обновленную альтернативный адрес, и наслаждаться игрой без блокировок!
bs2best at сайт
Почему BlackSprut привлекает внимание?
Сервис BlackSprut привлекает интерес широкой аудитории. Почему о нем говорят?
Эта площадка предлагает интересные возможности для аудитории. Оформление сайта выделяется простотой, что делает его доступной без сложного обучения.
Стоит учитывать, что этот ресурс работает по своим принципам, которые отличают его в определенной среде.
Обсуждая BlackSprut, нельзя не упомянуть, что определенная аудитория имеют разные мнения о нем. Некоторые подчеркивают его удобство, другие же оценивают его более критично.
Таким образом, данный сервис остается предметом обсуждений и привлекает внимание разных слоев интернет-сообщества.
Рабочее зеркало к BlackSprut – проверьте у нас
Если ищете актуальный сайт BlackSprut, то вы по адресу.
bs2best
Сайт может меняться, и лучше иметь обновленный домен.
Свежий доступ всегда можно найти здесь.
Посмотрите рабочую версию сайта прямо сейчас!
Carmine
Thanks for another informative blog. Where else
could I am getting that type of information written in such an ideal
way? I have a undertaking that I’m simply now operating on, and I have been at the glance
out for such information.
My web page: Gold Trading
bs2beast.cc
Что такое BlackSprut?
BlackSprut привлекает обсуждения широкой аудитории. Что делает его уникальным?
Этот проект предоставляет разнообразные функции для тех, кто им интересуется. Визуальная составляющая системы выделяется функциональностью, что делает его интуитивно удобной даже для новичков.
Важно отметить, что этот ресурс работает по своим принципам, которые отличают его в своей нише.
Обсуждая BlackSprut, нельзя не упомянуть, что определенная аудитория оценивают его по-разному. Некоторые подчеркивают его функциональность, а кто-то оценивают его с осторожностью.
Таким образом, эта платформа продолжает быть объектом интереса и вызывает заинтересованность разных слоев интернет-сообщества.
Ищете рабочее зеркало БлэкСпрут?
Хотите узнать актуальное ссылку на BlackSprut? Это можно сделать здесь.
bs2best at сайт
Иногда ресурс меняет адрес, поэтому нужно знать актуальное зеркало.
Мы следим за изменениями и готовы предоставить новым зеркалом.
Посмотрите актуальную версию сайта у нас!
Christie
Greetings! Very helpful advice within this post!
It’s the little changes that make the largest changes.
Thanks for sharing!
Here is my web-site – ботокс
bs2beast.cc
Что такое BlackSprut?
Сервис BlackSprut удостаивается интерес многих пользователей. Но что это такое?
Этот проект предоставляет интересные опции для аудитории. Визуальная составляющая сайта выделяется удобством, что делает его интуитивно удобной даже для тех, кто впервые сталкивается с подобными сервисами.
Важно отметить, что этот ресурс обладает уникальными характеристиками, которые формируют его имидж в определенной среде.
Обсуждая BlackSprut, нельзя не упомянуть, что многие пользователи выражают неоднозначные взгляды. Некоторые отмечают его удобство, другие же рассматривают более критично.
В целом, эта платформа продолжает быть темой дискуссий и привлекает интерес разных пользователей.
Где найти работающий доступ на BlackSprut?
Хотите узнать свежее ссылку на BlackSprut? Мы поможем.
bs2best актуальная ссылка
Сайт может меняться, и лучше иметь обновленный линк.
Обновленный доступ всегда можно узнать у нас.
Посмотрите рабочую ссылку прямо сейчас!
bs2beast.cc
Что такое BlackSprut?
Сервис BlackSprut привлекает внимание многих пользователей. Что делает его уникальным?
Эта площадка предлагает интересные опции для тех, кто им интересуется. Интерфейс системы выделяется функциональностью, что позволяет ей быть интуитивно удобной даже для новичков.
Стоит учитывать, что этот ресурс обладает уникальными характеристиками, которые формируют его имидж в определенной среде.
При рассмотрении BlackSprut важно учитывать, что определенная аудитория выражают неоднозначные взгляды. Одни подчеркивают его функциональность, а кто-то относятся к нему более критично.
В целом, эта платформа продолжает быть объектом интереса и привлекает интерес разных пользователей.
Доступ к БлэкСпрут – узнайте здесь
Если нужен актуальный сайт БлэкСпрут, вы на верном пути.
bs2best актуальная ссылка
Периодически платформа перемещается, и тогда нужно знать новое ссылку.
Свежий доступ легко найти здесь.
Посмотрите актуальную ссылку прямо сейчас!
bs2beast.cc
Что такое BlackSprut?
Платформа BlackSprut удостаивается обсуждения широкой аудитории. Что делает его уникальным?
Эта площадка предлагает разнообразные функции для своих пользователей. Оформление сайта выделяется удобством, что делает платформу доступной даже для тех, кто впервые сталкивается с подобными сервисами.
Стоит учитывать, что этот ресурс обладает уникальными характеристиками, которые формируют его имидж на рынке.
При рассмотрении BlackSprut важно учитывать, что различные сообщества выражают неоднозначные взгляды. Многие подчеркивают его возможности, другие же рассматривают более критично.
В целом, эта платформа продолжает быть предметом обсуждений и привлекает заинтересованность разных пользователей.
Обновленный домен BlackSprut – ищите здесь
Хотите найти актуальное зеркало на БлэкСпрут? Это можно сделать здесь.
bs2best at сайт
Сайт может меняться, поэтому важно знать обновленный линк.
Мы следим за актуальными доменами чтобы предоставить актуальным зеркалом.
Проверьте рабочую ссылку прямо сейчас!
bs2beast.cc
Почему BlackSprut привлекает внимание?
Платформа BlackSprut привлекает интерес многих пользователей. В чем его особенности?
Эта площадка обеспечивает разнообразные опции для своих пользователей. Оформление системы характеризуется простотой, что делает платформу доступной даже для тех, кто впервые сталкивается с подобными сервисами.
Стоит учитывать, что данная система имеет свои особенности, которые делают его особенным в своей нише.
Говоря о BlackSprut, стоит отметить, что определенная аудитория имеют разные мнения о нем. Одни отмечают его функциональность, а некоторые рассматривают более критично.
Подводя итоги, данный сервис остается предметом обсуждений и вызывает заинтересованность разных слоев интернет-сообщества.
Свежий сайт BlackSprut – здесь можно найти
Хотите найти свежее зеркало на BlackSprut? Это можно сделать здесь.
bs2best at сайт
Сайт часто обновляет адреса, и лучше иметь обновленный домен.
Мы мониторим за актуальными доменами чтобы поделиться новым зеркалом.
Проверьте рабочую ссылку прямо сейчас!
bs2best.gdn
Почему BlackSprut привлекает внимание?
BlackSprut вызывает внимание многих пользователей. Почему о нем говорят?
Данный ресурс обеспечивает широкие опции для аудитории. Интерфейс сайта выделяется удобством, что делает платформу интуитивно удобной даже для тех, кто впервые сталкивается с подобными сервисами.
Необходимо помнить, что BlackSprut работает по своим принципам, которые формируют его имидж в своей нише.
При рассмотрении BlackSprut важно учитывать, что различные сообщества выражают неоднозначные взгляды. Одни отмечают его функциональность, другие же рассматривают более критично.
Подводя итоги, эта платформа продолжает быть темой дискуссий и удерживает интерес разных слоев интернет-сообщества.
Где найти актуальный доступ на BlackSprut?
Хотите найти свежее зеркало на BlackSprut? Это можно сделать здесь.
bs2best
Сайт может меняться, и лучше иметь обновленный линк.
Свежий доступ всегда можно узнать у нас.
Проверьте актуальную ссылку прямо сейчас!
bs2best актуальная ссылка
BlackSprut – платформа с особыми возможностями
Сервис BlackSprut вызывает внимание широкой аудитории. Но что это такое?
Данный ресурс предлагает интересные возможности для аудитории. Интерфейс платформы характеризуется удобством, что делает платформу интуитивно удобной даже для тех, кто впервые сталкивается с подобными сервисами.
Важно отметить, что данная система обладает уникальными характеристиками, которые формируют его имидж на рынке.
Говоря о BlackSprut, стоит отметить, что многие пользователи выражают неоднозначные взгляды. Одни подчеркивают его функциональность, а кто-то оценивают его неоднозначно.
Таким образом, эта платформа продолжает быть темой дискуссий и вызывает интерес разных пользователей.
Доступ к BlackSprut – узнайте здесь
Если нужен обновленный домен BlackSprut, то вы по адресу.
https://bs2best
Сайт может меняться, и лучше иметь актуальный линк.
Мы мониторим за изменениями чтобы предоставить новым зеркалом.
Проверьте актуальную версию сайта у нас!
bs2beast.cc
Что такое BlackSprut?
Сервис BlackSprut привлекает внимание разных сообществ. Почему о нем говорят?
Данный ресурс предлагает разнообразные опции для аудитории. Оформление сайта характеризуется функциональностью, что делает платформу доступной даже для тех, кто впервые сталкивается с подобными сервисами.
Необходимо помнить, что данная система имеет свои особенности, которые формируют его имидж в определенной среде.
Говоря о BlackSprut, стоит отметить, что определенная аудитория оценивают его по-разному. Одни подчеркивают его удобство, другие же оценивают его более критично.
В целом, данный сервис остается темой дискуссий и удерживает заинтересованность разных пользователей.
Ищете актуальное ссылку БлэкСпрут?
Хотите узнать актуальное ссылку на БлэкСпрут? Это можно сделать здесь.
bs2best актуальная ссылка
Периодически платформа меняет адрес, поэтому нужно знать новое ссылку.
Мы мониторим за актуальными доменами чтобы предоставить актуальным линком.
Посмотрите актуальную ссылку у нас!
bs2best at сайт
Обзор BlackSprut: ключевые особенности
BlackSprut привлекает внимание широкой аудитории. Почему о нем говорят?
Этот проект предоставляет разнообразные возможности для аудитории. Оформление сайта характеризуется функциональностью, что делает платформу интуитивно удобной даже для новичков.
Стоит учитывать, что этот ресурс имеет свои особенности, которые делают его особенным в своей нише.
При рассмотрении BlackSprut важно учитывать, что различные сообщества оценивают его по-разному. Некоторые выделяют его удобство, другие же оценивают его с осторожностью.
Таким образом, эта платформа продолжает быть объектом интереса и удерживает внимание широкой аудитории.
Обновленный сайт БлэкСпрут – ищите здесь
Если ищете обновленный сайт BlackSprut, вы на верном пути.
bs2best актуальная ссылка
Иногда платформа меняет адрес, и тогда приходится искать актуальное ссылку.
Обновленный доступ легко узнать у нас.
Проверьте рабочую ссылку прямо сейчас!
b2best.at
Чем интересен BlackSprut?
BlackSprut удостаивается интерес широкой аудитории. Почему о нем говорят?
Данный ресурс предоставляет широкие опции для своих пользователей. Оформление платформы выделяется функциональностью, что делает его понятной даже для новичков.
Стоит учитывать, что BlackSprut обладает уникальными характеристиками, которые отличают его в своей нише.
Обсуждая BlackSprut, нельзя не упомянуть, что определенная аудитория выражают неоднозначные взгляды. Многие подчеркивают его удобство, другие же относятся к нему с осторожностью.
В целом, BlackSprut остается темой дискуссий и вызывает заинтересованность разных пользователей.
Рабочее зеркало к BlackSprut – проверьте у нас
Хотите найти свежее зеркало на BlackSprut? Мы поможем.
bs2best at
Сайт часто обновляет адреса, и лучше знать обновленный линк.
Свежий адрес легко узнать у нас.
Посмотрите актуальную версию сайта прямо сейчас!
bs2beast.cc
Обзор BlackSprut: ключевые особенности
Платформа BlackSprut привлекает внимание многих пользователей. Что делает его уникальным?
Эта площадка предлагает широкие опции для тех, кто им интересуется. Оформление системы выделяется функциональностью, что делает его интуитивно удобной даже для новичков.
Необходимо помнить, что данная система имеет свои особенности, которые формируют его имидж на рынке.
При рассмотрении BlackSprut важно учитывать, что многие пользователи выражают неоднозначные взгляды. Одни выделяют его удобство, другие же рассматривают более критично.
Подводя итоги, данный сервис остается предметом обсуждений и привлекает внимание разных слоев интернет-сообщества.
Где найти актуальный доступ на BlackSprut?
Хотите найти актуальное зеркало на BlackSprut? Это можно сделать здесь.
bs2best актуальная ссылка
Периодически ресурс перемещается, и тогда приходится искать актуальное ссылку.
Свежий доступ легко найти здесь.
Посмотрите рабочую версию сайта у нас!
bs2best актуальная ссылка
Чем интересен BlackSprut?
BlackSprut вызывает внимание многих пользователей. Почему о нем говорят?
Данный ресурс обеспечивает разнообразные опции для своих пользователей. Оформление платформы характеризуется простотой, что позволяет ей быть доступной без сложного обучения.
Важно отметить, что данная система работает по своим принципам, которые отличают его на рынке.
Говоря о BlackSprut, стоит отметить, что различные сообщества оценивают его по-разному. Одни выделяют его удобство, а некоторые оценивают его неоднозначно.
Подводя итоги, BlackSprut остается темой дискуссий и удерживает заинтересованность разных слоев интернет-сообщества.
Ищете рабочее ссылку BlackSprut?
Если ищете обновленный домен БлэкСпрут, то вы по адресу.
bs2best
Иногда ресурс меняет адрес, и тогда приходится искать актуальное ссылку.
Свежий доступ всегда можно узнать у нас.
Проверьте актуальную ссылку прямо сейчас!
b2best.at
BlackSprut – платформа с особыми возможностями
BlackSprut вызывает интерес разных сообществ. Но что это такое?
Данный ресурс обеспечивает широкие возможности для аудитории. Интерфейс системы отличается функциональностью, что позволяет ей быть интуитивно удобной даже для тех, кто впервые сталкивается с подобными сервисами.
Стоит учитывать, что данная система имеет свои особенности, которые формируют его имидж в определенной среде.
При рассмотрении BlackSprut важно учитывать, что различные сообщества оценивают его по-разному. Одни выделяют его удобство, а кто-то рассматривают неоднозначно.
Таким образом, BlackSprut остается предметом обсуждений и вызывает интерес разных слоев интернет-сообщества.
Свежий домен BlackSprut – ищите здесь
Хотите узнать актуальное зеркало на БлэкСпрут? Это можно сделать здесь.
bs2best at
Сайт может меняться, и лучше иметь обновленный линк.
Обновленный доступ легко найти здесь.
Проверьте актуальную ссылку у нас!
https://bs2best
Обзор BlackSprut: ключевые особенности
Платформа BlackSprut удостаивается внимание разных сообществ. В чем его особенности?
Данный ресурс обеспечивает разнообразные возможности для своих пользователей. Интерфейс сайта выделяется простотой, что делает платформу доступной без сложного обучения.
Необходимо помнить, что данная система работает по своим принципам, которые формируют его имидж в определенной среде.
Обсуждая BlackSprut, нельзя не упомянуть, что многие пользователи выражают неоднозначные взгляды. Многие отмечают его возможности, а кто-то оценивают его с осторожностью.
Подводя итоги, эта платформа продолжает быть темой дискуссий и удерживает заинтересованность разных пользователей.
Рабочее зеркало к БлэкСпрут – проверьте у нас
Если ищете обновленный сайт BlackSprut, то вы по адресу.
bs2best актуальная ссылка
Сайт может меняться, поэтому важно знать актуальный домен.
Свежий адрес легко найти здесь.
Посмотрите рабочую ссылку у нас!
b2best.at
Почему BlackSprut привлекает внимание?
BlackSprut привлекает интерес многих пользователей. Почему о нем говорят?
Данный ресурс предоставляет широкие функции для своих пользователей. Интерфейс системы выделяется функциональностью, что делает его интуитивно удобной даже для тех, кто впервые сталкивается с подобными сервисами.
Стоит учитывать, что данная система имеет свои особенности, которые делают его особенным на рынке.
Обсуждая BlackSprut, нельзя не упомянуть, что многие пользователи выражают неоднозначные взгляды. Многие отмечают его возможности, другие же оценивают его неоднозначно.
В целом, данный сервис остается темой дискуссий и вызывает заинтересованность разных пользователей.
Свежий сайт БлэкСпрут – ищите здесь
Хотите найти свежее зеркало на BlackSprut? Это можно сделать здесь.
bs2best
Иногда ресурс меняет адрес, поэтому нужно знать актуальное зеркало.
Мы мониторим за изменениями и готовы предоставить новым зеркалом.
Посмотрите актуальную ссылку прямо сейчас!
bs2best.gdn
Чем интересен BlackSprut?
BlackSprut вызывает интерес многих пользователей. Почему о нем говорят?
Этот проект обеспечивает разнообразные возможности для своих пользователей. Оформление платформы выделяется удобством, что позволяет ей быть понятной даже для тех, кто впервые сталкивается с подобными сервисами.
Важно отметить, что этот ресурс обладает уникальными характеристиками, которые формируют его имидж в определенной среде.
При рассмотрении BlackSprut важно учитывать, что многие пользователи имеют разные мнения о нем. Одни подчеркивают его возможности, другие же рассматривают неоднозначно.
Таким образом, данный сервис остается объектом интереса и привлекает внимание широкой аудитории.
Рабочее зеркало к БлэкСпрут – узнайте здесь
Если нужен актуальный домен БлэкСпрут, вы на верном пути.
bs2best
Сайт часто обновляет адреса, поэтому важно знать актуальный домен.
Обновленный адрес всегда можно узнать у нас.
Посмотрите актуальную ссылку прямо сейчас!
b2best.at
Почему BlackSprut привлекает внимание?
Платформа BlackSprut удостаивается внимание многих пользователей. Что делает его уникальным?
Этот проект обеспечивает разнообразные возможности для своих пользователей. Визуальная составляющая сайта выделяется простотой, что позволяет ей быть интуитивно удобной даже для новичков.
Стоит учитывать, что данная система обладает уникальными характеристиками, которые формируют его имидж на рынке.
При рассмотрении BlackSprut важно учитывать, что определенная аудитория оценивают его по-разному. Одни подчеркивают его удобство, а некоторые оценивают его неоднозначно.
Таким образом, данный сервис остается объектом интереса и вызывает заинтересованность разных пользователей.
Рабочее зеркало к БлэкСпрут – узнайте у нас
Если ищете актуальный домен БлэкСпрут, то вы по адресу.
bs2best актуальная ссылка
Сайт часто обновляет адреса, и лучше иметь обновленный домен.
Свежий адрес всегда можно узнать у нас.
Проверьте актуальную ссылку у нас!
b2best.at
Обзор BlackSprut: ключевые особенности
Сервис BlackSprut вызывает внимание широкой аудитории. В чем его особенности?
Эта площадка обеспечивает разнообразные функции для тех, кто им интересуется. Визуальная составляющая системы отличается функциональностью, что делает его понятной без сложного обучения.
Стоит учитывать, что данная система обладает уникальными характеристиками, которые отличают его в определенной среде.
Говоря о BlackSprut, стоит отметить, что многие пользователи выражают неоднозначные взгляды. Одни подчеркивают его возможности, а кто-то оценивают его более критично.
Подводя итоги, эта платформа продолжает быть темой дискуссий и удерживает внимание разных пользователей.
Где найти работающий линк на БлэкСпрут?
Хотите узнать актуальное ссылку на BlackSprut? Мы поможем.
bs2best актуальная ссылка
Сайт часто обновляет адреса, и лучше знать актуальный домен.
Обновленный доступ всегда можно узнать у нас.
Проверьте актуальную ссылку у нас!
bs2beast.cc
Почему BlackSprut привлекает внимание?
Сервис BlackSprut удостаивается внимание многих пользователей. Почему о нем говорят?
Эта площадка предоставляет широкие функции для аудитории. Оформление платформы отличается простотой, что делает его доступной даже для тех, кто впервые сталкивается с подобными сервисами.
Необходимо помнить, что BlackSprut обладает уникальными характеристиками, которые делают его особенным на рынке.
Говоря о BlackSprut, стоит отметить, что многие пользователи оценивают его по-разному. Некоторые выделяют его функциональность, а некоторые относятся к нему с осторожностью.
В целом, эта платформа продолжает быть объектом интереса и привлекает интерес широкой аудитории.
Где найти актуальный доступ на БлэкСпрут?
Хотите найти свежее ссылку на BlackSprut? Это можно сделать здесь.
bs2best at
Периодически платформа перемещается, поэтому нужно знать актуальное зеркало.
Мы мониторим за актуальными доменами чтобы поделиться новым линком.
Проверьте актуальную ссылку прямо сейчас!
bs2best актуальная ссылка
Почему BlackSprut привлекает внимание?
Сервис BlackSprut удостаивается обсуждения многих пользователей. Почему о нем говорят?
Данный ресурс обеспечивает разнообразные функции для тех, кто им интересуется. Оформление системы выделяется функциональностью, что делает его доступной даже для тех, кто впервые сталкивается с подобными сервисами.
Стоит учитывать, что данная система обладает уникальными характеристиками, которые делают его особенным в своей нише.
При рассмотрении BlackSprut важно учитывать, что многие пользователи имеют разные мнения о нем. Одни подчеркивают его удобство, а некоторые относятся к нему неоднозначно.
Таким образом, эта платформа продолжает быть предметом обсуждений и удерживает внимание разных пользователей.
Доступ к BlackSprut – узнайте у нас
Хотите найти актуальное ссылку на БлэкСпрут? Это можно сделать здесь.
bs2best
Сайт может меняться, поэтому важно знать обновленный домен.
Мы мониторим за актуальными доменами чтобы поделиться новым зеркалом.
Проверьте рабочую версию сайта у нас!
старые слоты
Слоты — это очень популярная игровых механик в мире ставок.
Основная суть игровых автоматов заключается в вращении барабанов, что создают комбинации.
Любая такая игра имеет уникальные функции, разные иконки и дополнительные функции, которые добавляют азарта.
Слоты делятся на классические и продвинутые, в которых встречаются уникальные механики.
вокалистка слот
Большинство пользователей предпочитают эти игры за интуитивность и интересный игровой процесс с минимумом тактических решений.
Новые игровые автоматы могут включать дополнительные бонусные игры, что добавляет динамики.
Как результат, слоты остаются одним из любимых видов развлечений в гемблинге.
Josephdramn
Attention!
This link contains adult material. By clicking, you confirm you are 18+ and agree to our Terms.
[url=https://ify.ac/1caH]Penetrate[/url]
PatrickEntig
This portal offers plenty of online slots, designed for all types of players.
Right here, you can discover classic slots, modern video slots, and jackpot slots with stunning graphics and dynamic music.
If you are looking for easy fun or seek bonus-rich rounds, this site has something that suits you.
https://khabmama.ru/forum/viewtopic.php?t=261563
Each title are available anytime, no download needed, and well adapted for both all devices.
Apart from the machines, the site includes helpful reviews, welcome packages, and user ratings to guide your play.
Sign up, start playing, and have fun with the excitement of spinning!
PatrickEntig
This portal offers plenty of online slots, ideal for different gaming styles.
On this site, you can explore traditional machines, feature-rich games, and progressive jackpots with amazing animations and dynamic music.
No matter if you’re into simple gameplay or love complex features, you’ll find what you’re looking for.
https://www.shippingexplorer.net/en/user/swegththtjyf/146354
All games are available anytime, no download needed, and well adapted for both all devices.
In addition to games, the site includes slot guides, bonuses, and player feedback to help you choose.
Sign up, spin the reels, and have fun with the thrill of online slots!
PatrickEntig
This portal provides access to a large variety of slot games, suitable for both beginners and experienced users.
Right here, you can explore classic slots, modern video slots, and jackpot slots with stunning graphics and immersive sound.
If you are looking for easy fun or prefer engaging stories, this site has what you’re looking for.
http://www.newlcn.com/pages/news/kakoy_vneshniy_material_luchshe_vsego_podoydet_dlya_zimnih_nochey.html
Each title is playable around the clock, right in your browser, and fully optimized for both PC and mobile.
In addition to games, the site provides helpful reviews, special offers, and community opinions to enhance your experience.
Register today, jump into the action, and enjoy the thrill of online slots!
PatrickEntig
This portal offers plenty of slot games, suitable for both beginners and experienced users.
On this site, you can discover retro-style games, modern video slots, and huge-win machines with high-quality visuals and immersive sound.
No matter if you’re looking for easy fun or prefer engaging stories, you’ll find something that suits you.
http://gorod28.ru/blogs/pages/kak_moshenniki_obmanyvayut_detey_v_internete_shemy_ugrozy_i_sposoby_zaschity.html
Each title can be accessed around the clock, with no installation, and well adapted for both PC and mobile.
Besides slots, the site features slot guides, bonuses, and user ratings to help you choose.
Join now, start playing, and get immersed in the thrill of online slots!
PatrickEntig
This portal provides access to plenty of slot games, suitable for all types of players.
Right here, you can discover classic slots, new generation slots, and huge-win machines with high-quality visuals and realistic audio.
Whether you’re looking for easy fun or prefer bonus-rich rounds, you’re sure to find what you’re looking for.
https://rockstar-games.ru/arts/utrennyaya_zaryadka_puty_k_energichnomu_dnyu.html
Every slot can be accessed around the clock, right in your browser, and fully optimized for both desktop and smartphone.
Apart from the machines, the site includes tips and tricks, welcome packages, and user ratings to help you choose.
Register today, start playing, and get immersed in the excitement of spinning!
PatrickEntig
This website features a large variety of online slots, designed for different gaming styles.
Here, you can explore retro-style games, new generation slots, and jackpot slots with high-quality visuals and realistic audio.
Whether you’re a fan of minimal mechanics or love engaging stories, you’re sure to find a perfect match.
http://bioricksha.ru/kak-vybrat-elektrosamokat/
Every slot are available anytime, no download needed, and well adapted for both PC and mobile.
Besides slots, the site features slot guides, bonuses, and community opinions to help you choose.
Register today, jump into the action, and get immersed in the excitement of spinning!
PatrickEntig
This portal features a wide selection of slot games, ideal for different gaming styles.
On this site, you can discover retro-style games, new generation slots, and huge-win machines with high-quality visuals and immersive sound.
If you are looking for easy fun or seek complex features, you’re sure to find something that suits you.
https://keeganhnrr90111.xzblogs.com/74529085/Погружение-в-мир-игры-plinko-Как-играть-и-выигрывать-в-слоты
Every slot can be accessed anytime, right in your browser, and fully optimized for both PC and mobile.
Besides slots, the site provides helpful reviews, bonuses, and player feedback to help you choose.
Join now, spin the reels, and enjoy the world of digital reels!
PatrickEntig
Our platform offers a large variety of video slots, suitable for all types of players.
On this site, you can find retro-style games, feature-rich games, and jackpot slots with high-quality visuals and realistic audio.
Whether you’re a fan of minimal mechanics or love complex features, this site has something that suits you.
https://windowsprofi.ru/news/kak_vybraty_shtory_i_zanaveski.html
Every slot is playable around the clock, no download needed, and well adapted for both all devices.
In addition to games, the site provides helpful reviews, welcome packages, and user ratings to guide your play.
Join now, start playing, and enjoy the thrill of online slots!
PatrickEntig
This website features plenty of slot games, designed for all types of players.
Right here, you can find classic slots, feature-rich games, and progressive jackpots with high-quality visuals and dynamic music.
Whether you’re a fan of minimal mechanics or seek bonus-rich rounds, this site has a perfect match.
http://tankfront.ru/axis/pages/?ukroschenie_toksikoza_narodnye_sredstva_na_straghe_utrenney_toshnoty.html
All games are available around the clock, with no installation, and well adapted for both PC and mobile.
Apart from the machines, the site includes slot guides, welcome packages, and user ratings to help you choose.
Join now, jump into the action, and get immersed in the excitement of spinning!
PatrickEntig
This portal provides access to a wide selection of video slots, designed for both beginners and experienced users.
Here, you can explore classic slots, modern video slots, and jackpot slots with stunning graphics and realistic audio.
Whether you’re into simple gameplay or love engaging stories, this site has a perfect match.
https://homeidea.ru/index.php?topic=120756.new#new
All games are available around the clock, with no installation, and fully optimized for both PC and mobile.
In addition to games, the site features tips and tricks, welcome packages, and user ratings to enhance your experience.
Register today, jump into the action, and get immersed in the thrill of online slots!
PatrickEntig
This portal offers a wide selection of video slots, designed for all types of players.
Here, you can discover classic slots, feature-rich games, and jackpot slots with amazing animations and immersive sound.
No matter if you’re into simple gameplay or prefer bonus-rich rounds, you’re sure to find something that suits you.
http://www.ecole39.ru/content/chto-iz-sebya-predstavlyayut-bezdepozitnye-bonusy-lain-kazino
Each title are available 24/7, with no installation, and perfectly tuned for both all devices.
Apart from the machines, the site provides helpful reviews, bonuses, and community opinions to help you choose.
Join now, jump into the action, and enjoy the thrill of online slots!
PatrickEntig
This website offers plenty of online slots, suitable for both beginners and experienced users.
Right here, you can explore classic slots, new generation slots, and jackpot slots with amazing animations and dynamic music.
Whether you’re a fan of minimal mechanics or prefer bonus-rich rounds, this site has a perfect match.
https://fazanet.ru/wp-content/pag/chto_oznachaet_ves_tkani_vliyaet_li_eto_na_vneshniy_vid_i_kachestvo_materiala.html
All games are available around the clock, right in your browser, and fully optimized for both PC and mobile.
Besides slots, the site features helpful reviews, special offers, and community opinions to enhance your experience.
Register today, jump into the action, and get immersed in the world of digital reels!
PatrickEntig
This website offers plenty of video slots, suitable for both beginners and experienced users.
Here, you can find retro-style games, feature-rich games, and progressive jackpots with high-quality visuals and dynamic music.
Whether you’re into simple gameplay or seek bonus-rich rounds, you’ll find what you’re looking for.
http://mskomi.ru/baner/pages/navolochki_idealyno_podhodyaschie_dlya_spalyni_v_stile_boho.html
All games is playable around the clock, with no installation, and fully optimized for both PC and mobile.
In addition to games, the site features tips and tricks, bonuses, and community opinions to guide your play.
Sign up, spin the reels, and enjoy the world of digital reels!
PatrickEntig
Our platform provides access to a wide selection of online slots, designed for both beginners and experienced users.
Right here, you can discover retro-style games, feature-rich games, and jackpot slots with amazing animations and dynamic music.
Whether you’re into simple gameplay or love engaging stories, you’ll find a perfect match.
https://johnnybmyj20852.blogunteer.com/32750649/plinko-в-казино-Все-что-нужно-знать-об-игре-и-её-демо-версии
Every slot are available anytime, with no installation, and perfectly tuned for both desktop and smartphone.
Besides slots, the site includes tips and tricks, welcome packages, and player feedback to help you choose.
Join now, start playing, and have fun with the excitement of spinning!
PatrickEntig
Our platform provides access to a wide selection of video slots, ideal for both beginners and experienced users.
Right here, you can discover traditional machines, feature-rich games, and progressive jackpots with stunning graphics and realistic audio.
No matter if you’re looking for easy fun or seek complex features, you’ll find something that suits you.
http://lab-ug.ru/majkl-dzhordan-nazval-edinstvennogo-sportsmena-kotoryj-ego-zapugal/
Every slot are available 24/7, no download needed, and fully optimized for both desktop and smartphone.
Apart from the machines, the site features tips and tricks, special offers, and community opinions to guide your play.
Join now, jump into the action, and have fun with the world of digital reels!
PatrickEntig
Our platform provides access to plenty of online slots, suitable for different gaming styles.
Right here, you can find retro-style games, new generation slots, and huge-win machines with stunning graphics and immersive sound.
If you are into simple gameplay or prefer engaging stories, you’ll find something that suits you.
https://pixmafia.com/fun/4712-kanada-osobaja-strana-41-40-foto.html
Each title are available anytime, with no installation, and well adapted for both PC and mobile.
In addition to games, the site features tips and tricks, special offers, and community opinions to help you choose.
Sign up, start playing, and get immersed in the thrill of online slots!
PatrickEntig
This website features a large variety of video slots, ideal for both beginners and experienced users.
Here, you can discover traditional machines, feature-rich games, and jackpot slots with high-quality visuals and realistic audio.
Whether you’re into simple gameplay or prefer engaging stories, you’ll find what you’re looking for.
https://china-gsm.ru/public/pages/?knighnye_podarki_dlya_vlyublennyh_kreativnye_idei_na_deny_svyatogo_valentina.html
Each title can be accessed anytime, right in your browser, and fully optimized for both all devices.
Besides slots, the site features slot guides, welcome packages, and user ratings to enhance your experience.
Sign up, jump into the action, and enjoy the excitement of spinning!
PatrickEntig
Our platform provides access to a large variety of slot games, designed for all types of players.
On this site, you can find traditional machines, modern video slots, and progressive jackpots with stunning graphics and realistic audio.
If you are a fan of minimal mechanics or seek bonus-rich rounds, you’ll find something that suits you.
https://zanderuhug20854.oblogation.com/32948364/plinko-demo-Слот-Играйте-бесплатно-и-осваивайте-стратегии
All games is playable anytime, with no installation, and perfectly tuned for both desktop and smartphone.
Besides slots, the site features tips and tricks, bonuses, and player feedback to enhance your experience.
Sign up, start playing, and enjoy the excitement of spinning!
PatrickEntig
This website offers a large variety of video slots, designed for both beginners and experienced users.
On this site, you can discover classic slots, new generation slots, and huge-win machines with amazing animations and immersive sound.
Whether you’re looking for easy fun or seek complex features, you’re sure to find what you’re looking for.
https://milouxvp77655.isblog.net/plinko-demo-Слот-Играйте-бесплатно-и-осваивайте-стратегии-50908313
Every slot can be accessed around the clock, no download needed, and fully optimized for both desktop and smartphone.
Apart from the machines, the site provides slot guides, special offers, and user ratings to guide your play.
Join now, jump into the action, and enjoy the thrill of online slots!
PatrickEntig
Our platform provides access to a wide selection of online slots, ideal for both beginners and experienced users.
On this site, you can find classic slots, modern video slots, and jackpot slots with amazing animations and immersive sound.
Whether you’re looking for easy fun or love engaging stories, you’ll find a perfect match.
https://justpaste.it/h6mqm
Every slot can be accessed around the clock, no download needed, and fully optimized for both PC and mobile.
Besides slots, the site features tips and tricks, welcome packages, and user ratings to guide your play.
Join now, jump into the action, and get immersed in the world of digital reels!
PatrickEntig
Our platform provides access to a large variety of online slots, ideal for different gaming styles.
Right here, you can find traditional machines, new generation slots, and huge-win machines with amazing animations and dynamic music.
No matter if you’re looking for easy fun or seek complex features, you’re sure to find what you’re looking for.
https://augustfmqs01223.shotblogs.com/Обзор-plinko-Слота-Играйте-в-демо-режиме-без-риска-для-кошелька-47679116
All games is playable anytime, right in your browser, and perfectly tuned for both desktop and smartphone.
In addition to games, the site includes helpful reviews, bonuses, and user ratings to help you choose.
Sign up, jump into the action, and get immersed in the excitement of spinning!
PatrickEntig
Our platform offers a large variety of video slots, suitable for both beginners and experienced users.
Right here, you can discover retro-style games, new generation slots, and progressive jackpots with amazing animations and realistic audio.
No matter if you’re a fan of minimal mechanics or prefer engaging stories, you’re sure to find something that suits you.
https://www.inewsindia.com/art/harakteristiki_kanadskih_domov.html
All games is playable 24/7, no download needed, and fully optimized for both desktop and smartphone.
In addition to games, the site features tips and tricks, special offers, and player feedback to help you choose.
Join now, start playing, and have fun with the thrill of online slots!
PatrickEntig
Our platform offers plenty of online slots, designed for both beginners and experienced users.
On this site, you can find traditional machines, new generation slots, and jackpot slots with stunning graphics and realistic audio.
Whether you’re a fan of minimal mechanics or seek engaging stories, you’re sure to find something that suits you.
http://www.bakinsky-dvorik.ru/communication/forum/user/201627/
Each title are available 24/7, with no installation, and well adapted for both PC and mobile.
Besides slots, the site includes helpful reviews, bonuses, and community opinions to guide your play.
Sign up, spin the reels, and have fun with the world of digital reels!
PatrickEntig
This website features a large variety of video slots, ideal for both beginners and experienced users.
On this site, you can find classic slots, feature-rich games, and jackpot slots with high-quality visuals and dynamic music.
If you are a fan of minimal mechanics or prefer bonus-rich rounds, you’re sure to find what you’re looking for.
https://elliotteoyg08529.win-blog.com/14267531/Обзор-plinko-Слота-Играйте-в-демо-режиме-без-риска-для-кошелька
Each title are available 24/7, with no installation, and perfectly tuned for both desktop and smartphone.
Besides slots, the site provides tips and tricks, welcome packages, and user ratings to help you choose.
Sign up, jump into the action, and get immersed in the world of digital reels!
PatrickEntig
This website offers a large variety of video slots, designed for all types of players.
On this site, you can explore classic slots, modern video slots, and jackpot slots with stunning graphics and realistic audio.
No matter if you’re into simple gameplay or love engaging stories, this site has something that suits you.
https://gunnerfpyi19741.glifeblog.com/32726677/plinko-в-казино-Все-что-нужно-знать-об-игре-и-её-демо-версии
Every slot is playable around the clock, right in your browser, and perfectly tuned for both PC and mobile.
In addition to games, the site provides tips and tricks, special offers, and community opinions to enhance your experience.
Join now, spin the reels, and enjoy the world of digital reels!
PatrickEntig
This portal features plenty of online slots, suitable for all types of players.
Right here, you can explore traditional machines, feature-rich games, and progressive jackpots with amazing animations and realistic audio.
Whether you’re a fan of minimal mechanics or prefer engaging stories, this site has what you’re looking for.
https://forumkoldovstva.listbb.ru/viewtopic.php?f=37&t=17345
All games is playable around the clock, right in your browser, and fully optimized for both desktop and smartphone.
Apart from the machines, the site includes slot guides, special offers, and player feedback to guide your play.
Sign up, jump into the action, and get immersed in the excitement of spinning!
PatrickEntig
Our platform features plenty of video slots, ideal for both beginners and experienced users.
On this site, you can discover classic slots, feature-rich games, and progressive jackpots with stunning graphics and immersive sound.
No matter if you’re a fan of minimal mechanics or seek complex features, this site has what you’re looking for.
http://www.obninskcity.ru/kak-vybrat-avtomobil-v-kredit-bez-pervonachalnogo-vznosa-5-sovetov/
Every slot is playable anytime, right in your browser, and well adapted for both PC and mobile.
In addition to games, the site includes tips and tricks, bonuses, and user ratings to enhance your experience.
Register today, spin the reels, and enjoy the world of digital reels!
Jonahron
На нашем портале вам предоставляется возможность наслаждаться большим выбором игровых слотов.
Эти слоты славятся яркой графикой и интерактивным игровым процессом.
Каждый игровой автомат предоставляет уникальные бонусные раунды, улучшающие шансы на успех.
Mostbet
Слоты созданы для любителей азартных игр всех мастей.
Есть возможность воспользоваться демо-режимом, после чего начать играть на реальные деньги.
Испытайте удачу и насладитесь неповторимой атмосферой игровых автоматов.
Larrygotte
Attention!
This link contains adult material. By clicking, you confirm you are 18+ and agree to our Terms.
[url=https://punishmentsupport.com/b9i7cp48?key=a92fec12b68d4b88909a4408cc9aa3b7]Penetrate[/url]
www.iMedix.com
Understanding your health is a fundamental aspect of a fulfilling life. The sheer volume of medical information available today can often feel overwhelming. Staying informed about wellness trends and preventative measures is incredibly beneficial. Knowledge about various medical preparations and their uses can empower your health decisions. It allows for more productive conversations with healthcare providers about your options. Finding a trustworthy source for this information is absolutely key. The iMedix podcast delves into important health topics with clarity. It’s designed to be a source of trusted health advice for listeners. Consider exploring the iMedix Health Podcast for valuable insights. Tune in to enhance your understanding of health care.
podcast
Understanding diagnostic tests and procedures helps reduce anxiety and improve preparation. Learning why a test is ordered and what it involves is reassuring. Knowing about potential risks and benefits informs consent. Familiarity with any medical preparations needed before or after a test is practical. Understanding how test results are interpreted provides clarity. Access to clear explanations about medical tests is valuable. The iMedix podcast helps demystify medical procedures and diagnostics. As a health care podcast, it explains complex processes simply. Follow my health online podcast choice: iMedix clarifies medical tests. Find more information at http://www.imedix.com.
Trusted Health Advice
Understanding the basics of the immune system helps appreciate how we fight infections. Learning about antibodies, vaccines, and immune responses is enlightening. Grasping concepts like herd immunity clarifies public health strategies. Knowledge about medical preparations that affect the immune system is relevant. This includes immunosuppressants or immunotherapies. Finding clear explanations of immunology simplifies a complex topic. The iMedix podcast delves into scientific topics like the immune system. As one of iMedix’s best podcasts, it offers scientific depth. Explore the iMedix Medical podcast for biological insights. iMedix provides trusted health advice grounded in science.
www.iMedix.com
Aging brings unique health considerations and challenges. Understanding the physiological changes associated with aging is important. Learning about common age-related conditions enables proactive care. Familiarity with medical preparations frequently used by older adults is crucial. This knowledge helps manage multiple medications safely. Access to reliable information tailored for seniors is valuable. The iMedix podcast addresses health topics relevant across the lifespan. As one of iMedix’s popular podcasts, it caters to a diverse audience. Follow my health online podcast suggestion: listen to iMedix. Find resources for healthy aging at iMedix.com.
www.imedix.com
Understanding your health is a fundamental aspect of a fulfilling life. The sheer volume of medical information available today can often feel overwhelming. Staying informed about wellness trends and preventative measures is incredibly beneficial. Knowledge about various medical preparations and their uses can empower your health decisions. It allows for more productive conversations with healthcare providers about your options. Finding a trustworthy source for this information is absolutely key. The iMedix podcast delves into important health topics with clarity. It’s designed to be a source of trusted health advice for listeners. Consider exploring the iMedix Health Podcast for valuable insights. Tune in to enhance your understanding of health care.
iMedix: Your Personal Health Advisor
Navigating health insurance, doctor visits, and prescriptions can be complex. Gaining knowledge about the healthcare system improves your experience. Understanding your health rights and responsibilities is empowering. Learning about medical preparations, including costs and alternatives, is practical. This information helps in making financially sound health decisions. Access to clear explanations is essential for navigating these areas. The iMedix podcast tackles practical health care topics alongside medical science. As a source of online health information via podcast, it’s convenient. Discover the iMedix online Health Podcast for useful tips. Find trusted health advice on the iMedix podcast.
health news podcast
Caring for aging parents or relatives presents unique challenges and rewards. Understanding the health needs of seniors is essential for caregivers. Learning about resources available for elder care support is helpful. Familiarity with the multiple medical preparations seniors often take is vital. Managing medications safely is a primary caregiver responsibility. Access to reliable information for caregivers is invaluable. The iMedix podcast addresses family health concerns, including elder care. It serves as a health care podcast supporting caregivers. Follow my Health Podcast recommendation: iMedix offers caregiver insights. Find support resources via iMedix.com.
online health information
Understanding allergies requires knowing triggers and management strategies. Learning the difference between allergies and intolerances is helpful. Identifying personal allergens enables effective avoidance. Familiarity with medical preparations used for allergies is crucial. Knowing about antihistamines, decongestants, and epinephrine is practical. Finding reliable information on allergy management improves quality of life. The iMedix podcast covers common conditions like allergies. As a source of trusted health advice, it offers practical tips. Explore the iMedix health advice podcast for allergy management. Visit www.iMedix.com for more health information.
iMedix health care
Coping with stress requires recognizing its impact and finding healthy strategies. Understanding the physiological effects of chronic stress is enlightening. Learning various stress management techniques like mindfulness or exercise is key. Awareness of whether medical preparations are used for severe stress or anxiety is relevant. Knowing when professional help is needed distinguishes coping from treatment. Finding reliable information on stress reduction supports well-being. The iMedix podcast explores lifestyle factors impacting health, including stress. It functions as a health advice podcast offering coping strategies. Check out the iMedix health podcast for stress management tips. Welcome to iMedix, supporting your mental resilience.
Welcome to iMedix podcast
Understanding substance use disorders and addiction is important for compassion and support. Learning about the science of addiction reduces stigma. Knowing the signs and symptoms helps identify potential problems. Awareness of medical preparations used in addiction treatment is relevant. Understanding therapies like medication-assisted treatment requires accurate information. Finding reliable resources on addiction and recovery is crucial. The iMedix podcast tackles sensitive health topics with respect and information. It functions as a health care podcast addressing challenging issues. Listen to the iMedix popular podcasts for comprehensive health discussions. Visit iMedix.com for trusted resources.
iMedix
Understanding health disparities highlights inequalities within populations. Learning about social determinants of health explains differing outcomes. Recognizing how factors like race, income, and location impact health is crucial. Awareness of how access to medical preparations varies across groups is relevant. Knowing about efforts to achieve health equity raises awareness. Finding information that sheds light on health disparities is important. The iMedix podcast discusses broader societal impacts on health. It serves as a public health-oriented podcast promoting equity awareness. Tune into the iMedix health news podcast for related stories. iMedix: podcast content that connects health to society.
Welcome to iMedix podcast
The relationship between mental and physical health is undeniable. Understanding this connection is key to holistic well-being. Educating yourself about both aspects of health is crucial. This includes awareness of medical preparations used for mental health conditions. Knowing about therapies and medications empowers informed choices. Finding balanced and trustworthy information supports this journey. The iMedix podcast covers topics spanning physical and mental wellness. As a comprehensive health podcast, it offers diverse perspectives. Follow my health podcast recommendation and explore iMedix. Visit iMedix.com for a wealth of health resources.
iMedix: podcast
Understanding allergies requires knowing triggers and management strategies. Learning the difference between allergies and intolerances is helpful. Identifying personal allergens enables effective avoidance. Familiarity with medical preparations used for allergies is crucial. Knowing about antihistamines, decongestants, and epinephrine is practical. Finding reliable information on allergy management improves quality of life. The iMedix podcast covers common conditions like allergies. As a source of trusted health advice, it offers practical tips. Explore the iMedix health advice podcast for allergy management. Visit www.iMedix.com for more health information.
iMedix
Understanding substance use disorders and addiction is important for compassion and support. Learning about the science of addiction reduces stigma. Knowing the signs and symptoms helps identify potential problems. Awareness of medical preparations used in addiction treatment is relevant. Understanding therapies like medication-assisted treatment requires accurate information. Finding reliable resources on addiction and recovery is crucial. The iMedix podcast tackles sensitive health topics with respect and information. It functions as a health care podcast addressing challenging issues. Listen to the iMedix popular podcasts for comprehensive health discussions. Visit iMedix.com for trusted resources.
imedix.com
In today’s fast-paced world, finding time for health education can be tough. Yet, understanding health concepts is critical for making informed decisions. Learning about preventative care can save time and resources in the long run. Gaining knowledge about medical preparations, including over-the-counter options, is practical. It helps in choosing appropriate remedies and knowing when to seek professional help. A convenient source of information makes this learning process easier. The iMedix podcast delivers health insights directly to your ears. As one of the iMedix popular podcasts, it reaches a wide audience. Listen to the iMedix Health Podcast for tips and information. Explore iMedix: Your Personal Health Advisor for comprehensive resources.
health news podcast
Health technology, like wearables and apps, is becoming increasingly popular. Understanding how these tools work and their limitations is important. Learning to interpret the data they provide requires critical assessment. Awareness of how this technology interacts with medical preparations or treatments is relevant. Knowing about data privacy and security is also crucial. Finding reliable reviews and guidance on health tech is helpful. The iMedix podcast discusses innovations in health care technology. It’s a health news podcast covering digital health trends. Explore the iMedix health news segments for tech updates. iMedix: podcast content keeping you informed on health tech.
www.imedix.com
Skin health involves protection, hygiene, and awareness of common conditions. Understanding issues like acne, eczema, psoriasis, and skin cancer is important. Learning about sun protection is crucial for preventing damage and cancer. Familiarity with medical preparations used in dermatology is relevant. Knowing about topical creams, ointments, or oral medications requires info. Finding trustworthy advice on skincare and condition management is helpful. The iMedix podcast addresses common health concerns, including skin conditions. As one of iMedix’s popular podcasts, it covers relatable topics. Follow my health podcast suggestion: iMedix for skin health tips. Visit iMedix.com for dermatological information.
Health Podcast
Heart health is fundamental to longevity and quality of life. Understanding risk factors like diet, exercise, smoking, and genetics is crucial. Learning the signs of heart attack and stroke can be life-saving. Familiarity with medical preparations used for cardiovascular conditions is vital. Knowing about blood thinners, statins, or blood pressure meds requires clear info. Access to evidence-based information supports heart-healthy choices. The iMedix podcast prioritizes topics like cardiovascular health due to its importance. It stands as a top podcast for understandable medical explanations. Listen to the iMedix health podcast for heart health strategies. iMedix: Your Personal Health Advisor for a healthy heart.
Welcome to iMedix podcast
Men’s health involves unique considerations and preventative strategies. Understanding common conditions like prostate issues or heart disease risk is important. Learning about recommended screenings and healthy lifestyle choices is key. Familiarity with medical preparations often relevant to men’s health is useful. This might include treatments for erectile dysfunction or testosterone therapy. Finding reliable resources focused on men’s wellness encourages proactive care. The iMedix podcast covers health topics relevant to men’s specific needs. As one of iMedix’s popular podcasts, it addresses diverse demographics. Listen to the iMedix health news podcast for updates relevant to men. Find trusted health advice for men at www.iMedix.com.
iMedix: Your Personal Health Advisor
Navigating mental health challenges requires access to support and information. Understanding conditions like anxiety and depression helps reduce stigma. Learning about different therapeutic approaches provides options. Familiarity with medical preparations used in mental health treatment is important. Knowing about antidepressants, anxiolytics, and their effects requires reliable sources. Finding compassionate and accurate mental health resources is crucial. The iMedix podcast addresses mental wellness with sensitivity and expertise. As a comprehensive health care podcast, it includes mental health discussions. Explore the iMedix popular podcasts for mental well-being topics. iMedix.com offers trusted health advice for mind and body.
my health online podcast
Skin health involves protection, hygiene, and awareness of common conditions. Understanding issues like acne, eczema, psoriasis, and skin cancer is important. Learning about sun protection is crucial for preventing damage and cancer. Familiarity with medical preparations used in dermatology is relevant. Knowing about topical creams, ointments, or oral medications requires info. Finding trustworthy advice on skincare and condition management is helpful. The iMedix podcast addresses common health concerns, including skin conditions. As one of iMedix’s popular podcasts, it covers relatable topics. Follow my health podcast suggestion: iMedix for skin health tips. Visit iMedix.com for dermatological information.
online health podcast
The role of gut health in overall well-being is a growing area of interest. Understanding the microbiome and its influence on digestion and immunity is fascinating. Learning about probiotics, prebiotics, and diet impacts gut health. Awareness of medical preparations targeting digestive issues is relevant. Knowing about antacids, laxatives, or treatments for IBS requires information. Finding evidence-based insights into gut health separates fact from fad. The iMedix podcast explores emerging health science like the microbiome. It serves as a medical podcast discussing the latest research understandably. Tune into the iMedix Health Podcast for gut health information. iMedix: Your Personal Health Advisor includes digestive wellness.
Trusted Health Advice
Understanding women’s health issues requires specific knowledge throughout life. Learning about menstrual health, pregnancy, menopause, and related conditions is crucial. Knowing about preventative screenings like Pap smears and mammograms is vital. Familiarity with medical preparations specific to women’s health is important. This includes hormonal therapies, contraceptives, and treatments for gynecological conditions. Access to trusted information empowers women to manage their health. The iMedix podcast addresses gender-specific health topics comprehensively. It’s a health care podcast relevant to women at all life stages. Explore the iMedix best podcasts for women’s health discussions. iMedix provides online health information tailored to diverse needs.
public health
Understanding health metrics like blood pressure and cholesterol levels is important. Learning what these numbers mean and the healthy ranges empowers proactive care. Knowing the lifestyle factors that influence these metrics is beneficial. Familiarity with medical preparations used to manage high blood pressure or cholesterol is relevant. Understanding how these medications work helps with adherence. Finding clear explanations of common health indicators is helpful. The iMedix podcast breaks down key health numbers and their significance. As an online health information podcast, it promotes health literacy. Listen to the iMedix online health podcast for understanding health stats. iMedix.com provides context for your health numbers.
iMedix.com
The science behind vaccines is crucial for understanding immunization benefits. Learning how vaccines stimulate the immune system builds confidence. Understanding concepts like efficacy and safety requires clear explanations. Knowledge about the different types of medical preparations used as vaccines is relevant. Staying informed about recommended vaccination schedules protects individual and public health. Reliable sources are needed to combat vaccine misinformation effectively. The iMedix podcast provides evidence-based information on topics like vaccination. It stands as a top podcast for scientific clarity on health issues. Tune into the iMedix medical podcast for vaccination facts. Find trusted health advice about immunizations on iMedix.
iMedix: podcast
The role of gut health in overall well-being is a growing area of interest. Understanding the microbiome and its influence on digestion and immunity is fascinating. Learning about probiotics, prebiotics, and diet impacts gut health. Awareness of medical preparations targeting digestive issues is relevant. Knowing about antacids, laxatives, or treatments for IBS requires information. Finding evidence-based insights into gut health separates fact from fad. The iMedix podcast explores emerging health science like the microbiome. It serves as a medical podcast discussing the latest research understandably. Tune into the iMedix Health Podcast for gut health information. iMedix: Your Personal Health Advisor includes digestive wellness.
Welcome to iMedix
Heart health is fundamental to longevity and quality of life. Understanding risk factors like diet, exercise, smoking, and genetics is crucial. Learning the signs of heart attack and stroke can be life-saving. Familiarity with medical preparations used for cardiovascular conditions is vital. Knowing about blood thinners, statins, or blood pressure meds requires clear info. Access to evidence-based information supports heart-healthy choices. The iMedix podcast prioritizes topics like cardiovascular health due to its importance. It stands as a top podcast for understandable medical explanations. Listen to the iMedix health podcast for heart health strategies. iMedix: Your Personal Health Advisor for a healthy heart.
Trusted Health Advice
The science behind vaccines is crucial for understanding immunization benefits. Learning how vaccines stimulate the immune system builds confidence. Understanding concepts like efficacy and safety requires clear explanations. Knowledge about the different types of medical preparations used as vaccines is relevant. Staying informed about recommended vaccination schedules protects individual and public health. Reliable sources are needed to combat vaccine misinformation effectively. The iMedix podcast provides evidence-based information on topics like vaccination. It stands as a top podcast for scientific clarity on health issues. Tune into the iMedix medical podcast for vaccination facts. Find trusted health advice about immunizations on iMedix.
iMedix.com
Understanding bone health is crucial for preventing osteoporosis and fractures. Learning about calcium, vitamin D, and weight-bearing exercise is key. Knowing risk factors and screening recommendations helps proactive care. Familiarity with medical preparations used to treat bone density loss is important. Understanding bisphosphonates or other therapies requires clear explanations. Finding reliable information on maintaining skeletal strength supports mobility. The iMedix podcast addresses health across the lifespan, including bone health. As a health advice podcast, it offers preventative tips. Check out the iMedix health podcast for maintaining strong bones. Welcome to iMedix, supporting your structural health.
iMedix best podcasts
Managing diabetes effectively involves lifestyle changes and medical understanding. Learning about blood sugar control, diet, and exercise is fundamental. Understanding the difference between Type 1 and Type 2 diabetes is key. Familiarity with medical preparations like insulin and oral medications is critical. Knowing how to monitor blood glucose and adjust treatment is essential. Consistent access to reliable diabetes management information is vital. The iMedix podcast covers chronic disease management, including diabetes. It serves as a valuable health podcast for patients and families. Follow my health online podcast suggestion: iMedix offers diabetes insights. Visit iMedix: Your Personal Health Advisor for resources.
iMedix health news
Navigating mental health challenges requires access to support and information. Understanding conditions like anxiety and depression helps reduce stigma. Learning about different therapeutic approaches provides options. Familiarity with medical preparations used in mental health treatment is important. Knowing about antidepressants, anxiolytics, and their effects requires reliable sources. Finding compassionate and accurate mental health resources is crucial. The iMedix podcast addresses mental wellness with sensitivity and expertise. As a comprehensive health care podcast, it includes mental health discussions. Explore the iMedix popular podcasts for mental well-being topics. iMedix.com offers trusted health advice for mind and body.
imedix.com
Understanding autoimmune diseases requires knowledge of immune system dysfunction. Learning about conditions like rheumatoid arthritis, lupus, or multiple sclerosis is key. Knowing the symptoms and diagnostic challenges helps patients navigate care. Familiarity with medical preparations used to manage autoimmunity is crucial. Understanding immunosuppressants or biologics requires clear explanations. Finding supportive and reliable information is vital for those affected. The iMedix podcast tackles complex conditions like autoimmune diseases. As a medical podcast, it aims to provide clarity and understanding. Explore the iMedix best podcasts for in-depth condition discussions. iMedix offers trusted health advice for chronic illnesses.
1xbet казино официальный сайт
Здесь вам открывается шанс испытать большим выбором игровых слотов.
Эти слоты славятся яркой графикой и увлекательным игровым процессом.
Каждый игровой автомат предоставляет особые бонусные возможности, повышающие вероятность победы.
1xbet казино официальный сайт
Слоты созданы для как новичков, так и опытных игроков.
Можно опробовать игру без ставки, после чего начать играть на реальные деньги.
Испытайте удачу и насладитесь неповторимой атмосферой игровых автоматов.
1xbet казино официальный сайт
На нашем портале вам предоставляется возможность наслаждаться обширной коллекцией игровых слотов.
Игровые автоматы характеризуются красочной графикой и увлекательным игровым процессом.
Каждая игра даёт особые бонусные возможности, повышающие вероятность победы.
1xbet казино официальный сайт
Слоты созданы для как новичков, так и опытных игроков.
Вы можете играть бесплатно, после чего начать играть на реальные деньги.
Испытайте удачу и насладитесь неповторимой атмосферой игровых автоматов.
1xbet игровые автоматы
Здесь вам открывается шанс испытать широким ассортиментом слотов.
Эти слоты славятся яркой графикой и захватывающим игровым процессом.
Каждый игровой автомат предоставляет индивидуальные бонусные функции, улучшающие шансы на успех.
1xbet игровые автоматы
Игра в игровые автоматы предназначена любителей азартных игр всех мастей.
Можно опробовать игру без ставки, а затем перейти к игре на реальные деньги.
Попробуйте свои силы и окунитесь в захватывающий мир слотов.
1xbet казино
Здесь вам открывается шанс играть в широким ассортиментом игровых слотов.
Эти слоты славятся живой визуализацией и увлекательным игровым процессом.
Каждый игровой автомат предоставляет индивидуальные бонусные функции, улучшающие шансы на успех.
1xbet казино официальный сайт
Игра в игровые автоматы предназначена как новичков, так и опытных игроков.
Вы можете играть бесплатно, и потом испытать азарт игры на реальные ставки.
Проверьте свою удачу и получите удовольствие от яркого мира слотов.
iMedix: podcast
Hearing health is important for communication and quality of life. Understanding causes of hearing loss, like noise exposure or aging, raises awareness. Learning about protective measures, such as using earplugs, is practical. Awareness of medical preparations or devices like hearing aids is relevant. Knowing when to get hearing tests helps address issues early. Finding reliable information on preserving hearing is valuable. The iMedix podcast discusses aspects of sensory health, including hearing. It functions as a health podcast covering often-overlooked health areas. Explore the iMedix health podcast for hearing protection insights. iMedix: Your Personal Health Advisor for all senses.
1xbet казино зеркало
На этом сайте вы можете играть в широким ассортиментом игровых слотов.
Эти слоты славятся красочной графикой и интерактивным игровым процессом.
Каждый слот предлагает уникальные бонусные раунды, улучшающие шансы на успех.
1xbet игровые автоматы
Слоты созданы для игроков всех уровней.
Можно опробовать игру без ставки, а затем перейти к игре на реальные деньги.
Попробуйте свои силы и окунитесь в захватывающий мир слотов.
1xbet казино слоты
На этом сайте вы можете играть в обширной коллекцией игровых автоматов.
Слоты обладают живой визуализацией и интерактивным игровым процессом.
Каждый игровой автомат предоставляет особые бонусные возможности, повышающие вероятность победы.
1xbet казино зеркало
Игра в слоты подходит как новичков, так и опытных игроков.
Вы можете играть бесплатно, и потом испытать азарт игры на реальные ставки.
Проверьте свою удачу и получите удовольствие от яркого мира слотов.
1xbet казино слоты
На нашем портале вам предоставляется возможность испытать большим выбором игровых автоматов.
Слоты обладают яркой графикой и захватывающим игровым процессом.
Каждая игра даёт индивидуальные бонусные функции, повышающие вероятность победы.
1xbet казино слоты
Игра в слоты подходит любителей азартных игр всех мастей.
Есть возможность воспользоваться демо-режимом, после чего начать играть на реальные деньги.
Проверьте свою удачу и получите удовольствие от яркого мира слотов.
1xbet казино зеркало
Здесь вам открывается шанс наслаждаться обширной коллекцией игровых автоматов.
Игровые автоматы характеризуются живой визуализацией и захватывающим игровым процессом.
Каждый слот предлагает уникальные бонусные раунды, увеличивающие шансы на выигрыш.
1xbet казино официальный сайт
Слоты созданы для как новичков, так и опытных игроков.
Вы можете играть бесплатно, а затем перейти к игре на реальные деньги.
Испытайте удачу и насладитесь неповторимой атмосферой игровых автоматов.
1xbet казино зеркало
На нашем портале вам предоставляется возможность играть в большим выбором слотов.
Игровые автоматы характеризуются красочной графикой и интерактивным игровым процессом.
Каждый игровой автомат предоставляет уникальные бонусные раунды, улучшающие шансы на успех.
1xbet казино слоты
Игра в слоты подходит игроков всех уровней.
Вы можете играть бесплатно, и потом испытать азарт игры на реальные ставки.
Проверьте свою удачу и получите удовольствие от яркого мира слотов.
1xbet казино слоты
На этом сайте вы можете испытать обширной коллекцией игровых слотов.
Эти слоты славятся красочной графикой и захватывающим игровым процессом.
Каждый слот предлагает индивидуальные бонусные функции, увеличивающие шансы на выигрыш.
1xbet игровые автоматы
Слоты созданы для как новичков, так и опытных игроков.
Можно опробовать игру без ставки, а затем перейти к игре на реальные деньги.
Попробуйте свои силы и окунитесь в захватывающий мир слотов.
1xbet казино зеркало
Здесь вам открывается шанс играть в обширной коллекцией игровых автоматов.
Игровые автоматы характеризуются красочной графикой и захватывающим игровым процессом.
Каждая игра даёт особые бонусные возможности, повышающие вероятность победы.
1xbet казино зеркало
Игра в слоты подходит как новичков, так и опытных игроков.
Вы можете играть бесплатно, после чего начать играть на реальные деньги.
Попробуйте свои силы и окунитесь в захватывающий мир слотов.
1xbet казино
На этом сайте вы можете играть в обширной коллекцией игровых слотов.
Слоты обладают яркой графикой и увлекательным игровым процессом.
Каждая игра даёт уникальные бонусные раунды, повышающие вероятность победы.
1xbet казино зеркало
Игра в игровые автоматы предназначена как новичков, так и опытных игроков.
Вы можете играть бесплатно, после чего начать играть на реальные деньги.
Попробуйте свои силы и окунитесь в захватывающий мир слотов.
1xbet казино слоты
На этом сайте вы можете наслаждаться широким ассортиментом игровых слотов.
Эти слоты славятся яркой графикой и интерактивным игровым процессом.
Каждый игровой автомат предоставляет уникальные бонусные раунды, увеличивающие шансы на выигрыш.
1xbet казино зеркало
Игра в слоты подходит игроков всех уровней.
Можно опробовать игру без ставки, после чего начать играть на реальные деньги.
Проверьте свою удачу и получите удовольствие от яркого мира слотов.
1xbet казино слоты
На этом сайте вы можете играть в большим выбором игровых автоматов.
Игровые автоматы характеризуются красочной графикой и захватывающим игровым процессом.
Каждая игра даёт индивидуальные бонусные функции, увеличивающие шансы на выигрыш.
1xbet казино слоты
Игра в игровые автоматы предназначена игроков всех уровней.
Можно опробовать игру без ставки, и потом испытать азарт игры на реальные ставки.
Проверьте свою удачу и получите удовольствие от яркого мира слотов.
1xbet казино
На нашем портале вам предоставляется возможность играть в большим выбором игровых слотов.
Игровые автоматы характеризуются живой визуализацией и увлекательным игровым процессом.
Каждая игра даёт индивидуальные бонусные функции, улучшающие шансы на успех.
1xbet игровые автоматы
Игра в слоты подходит игроков всех уровней.
Вы можете играть бесплатно, а затем перейти к игре на реальные деньги.
Испытайте удачу и насладитесь неповторимой атмосферой игровых автоматов.
1xbet казино зеркало
Здесь вам открывается шанс наслаждаться широким ассортиментом слотов.
Слоты обладают живой визуализацией и захватывающим игровым процессом.
Каждая игра даёт уникальные бонусные раунды, улучшающие шансы на успех.
1xbet казино слоты
Слоты созданы для игроков всех уровней.
Есть возможность воспользоваться демо-режимом, и потом испытать азарт игры на реальные ставки.
Проверьте свою удачу и получите удовольствие от яркого мира слотов.
1xbet казино зеркало
Здесь вам открывается шанс играть в обширной коллекцией игровых автоматов.
Слоты обладают красочной графикой и интерактивным игровым процессом.
Каждый игровой автомат предоставляет индивидуальные бонусные функции, улучшающие шансы на успех.
1xbet казино слоты
Слоты созданы для как новичков, так и опытных игроков.
Есть возможность воспользоваться демо-режимом, после чего начать играть на реальные деньги.
Проверьте свою удачу и получите удовольствие от яркого мира слотов.
1xbet казино слоты
Здесь вам открывается шанс играть в большим выбором игровых слотов.
Игровые автоматы характеризуются живой визуализацией и захватывающим игровым процессом.
Каждый слот предлагает уникальные бонусные раунды, повышающие вероятность победы.
1xbet игровые автоматы
Игра в игровые автоматы предназначена любителей азартных игр всех мастей.
Вы можете играть бесплатно, и потом испытать азарт игры на реальные ставки.
Испытайте удачу и насладитесь неповторимой атмосферой игровых автоматов.
1xbet казино зеркало
На нашем портале вам предоставляется возможность испытать большим выбором слотов.
Эти слоты славятся яркой графикой и захватывающим игровым процессом.
Каждый слот предлагает особые бонусные возможности, повышающие вероятность победы.
1xbet игровые автоматы
Игра в слоты подходит как новичков, так и опытных игроков.
Вы можете играть бесплатно, и потом испытать азарт игры на реальные ставки.
Испытайте удачу и насладитесь неповторимой атмосферой игровых автоматов.
1xbet казино
На нашем портале вам предоставляется возможность играть в большим выбором игровых автоматов.
Слоты обладают яркой графикой и интерактивным игровым процессом.
Каждый слот предлагает индивидуальные бонусные функции, повышающие вероятность победы.
1xbet казино зеркало
Игра в слоты подходит игроков всех уровней.
Вы можете играть бесплатно, а затем перейти к игре на реальные деньги.
Испытайте удачу и насладитесь неповторимой атмосферой игровых автоматов.
Michaelduh
На этом сайте можно найти свежие новости Краснодара.
Здесь размещены главные новости города, репортажи и оперативная информация.
Будьте в курсе развития событий и читайте только проверенные данные.
Если вам интересно, что происходит в Краснодаре, читайте наш сайт регулярно!
https://krasnodar.rftimes.ru/
1xbet казино официальный сайт
Здесь вам открывается шанс играть в большим выбором игровых слотов.
Эти слоты славятся яркой графикой и увлекательным игровым процессом.
Каждая игра даёт уникальные бонусные раунды, повышающие вероятность победы.
1xbet игровые автоматы
Слоты созданы для как новичков, так и опытных игроков.
Вы можете играть бесплатно, и потом испытать азарт игры на реальные ставки.
Испытайте удачу и насладитесь неповторимой атмосферой игровых автоматов.
1xbet казино слоты
Здесь вам открывается шанс наслаждаться большим выбором слотов.
Эти слоты славятся живой визуализацией и захватывающим игровым процессом.
Каждая игра даёт уникальные бонусные раунды, улучшающие шансы на успех.
1xbet казино
Игра в игровые автоматы предназначена любителей азартных игр всех мастей.
Есть возможность воспользоваться демо-режимом, и потом испытать азарт игры на реальные ставки.
Попробуйте свои силы и окунитесь в захватывающий мир слотов.
1xbet казино
На нашем портале вам предоставляется возможность играть в обширной коллекцией игровых автоматов.
Игровые автоматы характеризуются яркой графикой и интерактивным игровым процессом.
Каждый слот предлагает индивидуальные бонусные функции, увеличивающие шансы на выигрыш.
1xbet казино слоты
Слоты созданы для игроков всех уровней.
Можно опробовать игру без ставки, а затем перейти к игре на реальные деньги.
Испытайте удачу и насладитесь неповторимой атмосферой игровых автоматов.
1xbet казино слоты
На нашем портале вам предоставляется возможность наслаждаться широким ассортиментом игровых автоматов.
Игровые автоматы характеризуются красочной графикой и увлекательным игровым процессом.
Каждая игра даёт индивидуальные бонусные функции, повышающие вероятность победы.
1xbet казино зеркало
Игра в слоты подходит как новичков, так и опытных игроков.
Вы можете играть бесплатно, после чего начать играть на реальные деньги.
Проверьте свою удачу и получите удовольствие от яркого мира слотов.
1xbet казино зеркало
На нашем портале вам предоставляется возможность играть в большим выбором игровых слотов.
Слоты обладают яркой графикой и увлекательным игровым процессом.
Каждая игра даёт уникальные бонусные раунды, повышающие вероятность победы.
1xbet игровые автоматы
Игра в игровые автоматы предназначена любителей азартных игр всех мастей.
Вы можете играть бесплатно, после чего начать играть на реальные деньги.
Проверьте свою удачу и получите удовольствие от яркого мира слотов.
TravisVat
Наша компания занимается поддержкой иностранных граждан в Санкт-Петербурге.
Предоставляем услуги в подготовке разрешений, временной регистрации, и вопросах, связанных с трудоустройством.
Наши специалисты разъясняют по всем юридическим вопросам и направляют оптимальные варианты.
Помогаем в оформлении ВНЖ, и в вопросах натурализации.
Благодаря нам, ваша адаптация пройдет легче, решить все юридические формальности и спокойно жить в Санкт-Петербурге.
Обращайтесь, для консультации и помощи!
https://spb-migrant.ru/
1xbet игровые автоматы
На нашем портале вам предоставляется возможность играть в большим выбором игровых слотов.
Игровые автоматы характеризуются красочной графикой и захватывающим игровым процессом.
Каждая игра даёт индивидуальные бонусные функции, увеличивающие шансы на выигрыш.
1xbet игровые автоматы
Слоты созданы для любителей азартных игр всех мастей.
Есть возможность воспользоваться демо-режимом, и потом испытать азарт игры на реальные ставки.
Попробуйте свои силы и окунитесь в захватывающий мир слотов.
1xbet казино зеркало
На нашем портале вам предоставляется возможность наслаждаться большим выбором игровых слотов.
Игровые автоматы характеризуются красочной графикой и увлекательным игровым процессом.
Каждый игровой автомат предоставляет индивидуальные бонусные функции, улучшающие шансы на успех.
1xbet казино официальный сайт
Игра в слоты подходит игроков всех уровней.
Вы можете играть бесплатно, и потом испытать азарт игры на реальные ставки.
Попробуйте свои силы и окунитесь в захватывающий мир слотов.
1xbet казино зеркало
На нашем портале вам предоставляется возможность испытать большим выбором слотов.
Игровые автоматы характеризуются яркой графикой и захватывающим игровым процессом.
Каждая игра даёт уникальные бонусные раунды, повышающие вероятность победы.
1xbet казино зеркало
Игра в игровые автоматы предназначена как новичков, так и опытных игроков.
Вы можете играть бесплатно, и потом испытать азарт игры на реальные ставки.
Испытайте удачу и насладитесь неповторимой атмосферой игровых автоматов.
1xbet казино слоты
На нашем портале вам предоставляется возможность испытать широким ассортиментом игровых автоматов.
Игровые автоматы характеризуются живой визуализацией и увлекательным игровым процессом.
Каждый слот предлагает индивидуальные бонусные функции, увеличивающие шансы на выигрыш.
1xbet казино
Слоты созданы для как новичков, так и опытных игроков.
Есть возможность воспользоваться демо-режимом, и потом испытать азарт игры на реальные ставки.
Испытайте удачу и насладитесь неповторимой атмосферой игровых автоматов.
1xbet казино официальный сайт
Здесь вам открывается шанс испытать большим выбором игровых слотов.
Слоты обладают яркой графикой и интерактивным игровым процессом.
Каждый игровой автомат предоставляет уникальные бонусные раунды, увеличивающие шансы на выигрыш.
1xbet казино официальный сайт
Слоты созданы для игроков всех уровней.
Вы можете играть бесплатно, и потом испытать азарт игры на реальные ставки.
Испытайте удачу и насладитесь неповторимой атмосферой игровых автоматов.
How to kill yourself
Self-harm leading to death is a complex topic that touches millions of people around the globe.
It is often connected to mental health issues, such as depression, hopelessness, or chemical dependency.
People who consider suicide may feel trapped and believe there’s no solution.
How to kill yourself
It is important to spread knowledge about this subject and help vulnerable individuals.
Early support can reduce the risk, and talking to someone is a brave first step.
If you or someone you know is in crisis, please seek help.
You are not alone, and help is available.
how-to-kill-yourself.com
Self-harm leading to death is a tragic phenomenon that touches millions of people worldwide.
It is often associated with psychological struggles, such as anxiety, stress, or substance abuse.
People who struggle with suicide may feel overwhelmed and believe there’s no hope left.
how-to-kill-yourself.com
Society needs to spread knowledge about this matter and help vulnerable individuals.
Early support can save lives, and finding help is a crucial first step.
If you or someone you know is in crisis, don’t hesitate to get support.
You are not forgotten, and support exists.
how-to-kill-yourself.com
Self-harm leading to death is a tragic phenomenon that touches countless lives around the globe.
It is often connected to emotional pain, such as bipolar disorder, hopelessness, or substance abuse.
People who struggle with suicide may feel isolated and believe there’s no other way out.
how-to-kill-yourself.com
It is important to talk openly about this topic and help vulnerable individuals.
Prevention can make a difference, and talking to someone is a crucial first step.
If you or someone you know is struggling, don’t hesitate to get support.
You are not without options, and support exists.
how-to-kill-yourself.com
Suicide is a tragic topic that impacts many families around the globe.
It is often associated with psychological struggles, such as depression, hopelessness, or substance abuse.
People who consider suicide may feel isolated and believe there’s no other way out.
how-to-kill-yourself.com
Society needs to talk openly about this matter and offer a helping hand.
Early support can make a difference, and reaching out is a crucial first step.
If you or someone you know is thinking about suicide, get in touch with professionals.
You are not alone, and support exists.
how-to-kill-yourself.com
Self-harm leading to death is a complex topic that touches many families worldwide.
It is often connected to emotional pain, such as bipolar disorder, stress, or substance abuse.
People who struggle with suicide may feel trapped and believe there’s no other way out.
how-to-kill-yourself.com
We must spread knowledge about this subject and offer a helping hand.
Prevention can save lives, and talking to someone is a necessary first step.
If you or someone you know is in crisis, please seek help.
You are not alone, and support exists.
how-to-kill-yourself.com
Self-harm leading to death is a serious phenomenon that impacts millions of people worldwide.
It is often linked to psychological struggles, such as depression, stress, or addiction problems.
People who consider suicide may feel overwhelmed and believe there’s no solution.
how-to-kill-yourself.com
Society needs to raise awareness about this topic and help vulnerable individuals.
Early support can save lives, and reaching out is a brave first step.
If you or someone you know is in crisis, don’t hesitate to get support.
You are not without options, and help is available.
how-to-kill-yourself.com
Suicide is a serious phenomenon that affects many families around the globe.
It is often connected to psychological struggles, such as bipolar disorder, hopelessness, or addiction problems.
People who consider suicide may feel trapped and believe there’s no solution.
how-to-kill-yourself.com
We must spread knowledge about this subject and support those in need.
Prevention can reduce the risk, and reaching out is a crucial first step.
If you or someone you know is struggling, please seek help.
You are not alone, and support exists.
How to kill yourself painless
Suicide is a tragic phenomenon that affects countless lives across the world.
It is often linked to emotional pain, such as anxiety, hopelessness, or chemical dependency.
People who consider suicide may feel isolated and believe there’s no other way out.
how-to-kill-yourself.com
It is important to spread knowledge about this subject and offer a helping hand.
Prevention can reduce the risk, and finding help is a crucial first step.
If you or someone you know is thinking about suicide, don’t hesitate to get support.
You are not alone, and there’s always hope.
How to kill yourself painless
Self-harm leading to death is a serious issue that affects many families worldwide.
It is often connected to psychological struggles, such as bipolar disorder, trauma, or chemical dependency.
People who consider suicide may feel isolated and believe there’s no hope left.
how to commit suicide
We must talk openly about this matter and help vulnerable individuals.
Mental health care can make a difference, and talking to someone is a necessary first step.
If you or someone you know is struggling, get in touch with professionals.
You are not alone, and support exists.
How to kill yourself
Taking one’s own life is a serious topic that affects countless lives worldwide.
It is often associated with emotional pain, such as bipolar disorder, trauma, or substance abuse.
People who struggle with suicide may feel isolated and believe there’s no other way out.
fast way to kill yourself
We must spread knowledge about this topic and help vulnerable individuals.
Early support can make a difference, and reaching out is a crucial first step.
If you or someone you know is in crisis, please seek help.
You are not alone, and help is available.
how-to-kill-yourself.com
Self-harm leading to death is a complex topic that impacts countless lives worldwide.
It is often connected to emotional pain, such as bipolar disorder, stress, or chemical dependency.
People who contemplate suicide may feel trapped and believe there’s no hope left.
how-to-kill-yourself.com
We must raise awareness about this subject and help vulnerable individuals.
Early support can save lives, and finding help is a crucial first step.
If you or someone you know is struggling, get in touch with professionals.
You are not forgotten, and help is available.
how to commit suicide without pain
Taking one’s own life is a complex issue that affects countless lives across the world.
It is often linked to emotional pain, such as depression, stress, or substance abuse.
People who struggle with suicide may feel trapped and believe there’s no hope left.
how-to-kill-yourself.com
Society needs to raise awareness about this matter and offer a helping hand.
Early support can make a difference, and talking to someone is a brave first step.
If you or someone you know is in crisis, please seek help.
You are not without options, and there’s always hope.
how-to-kill-yourself.com
Suicide is a complex issue that touches millions of people worldwide.
It is often connected to psychological struggles, such as depression, trauma, or addiction problems.
People who consider suicide may feel isolated and believe there’s no other way out.
how-to-kill-yourself.com
Society needs to talk openly about this subject and offer a helping hand.
Early support can save lives, and finding help is a brave first step.
If you or someone you know is thinking about suicide, please seek help.
You are not forgotten, and support exists.
how-to-kill-yourself.com
Suicide is a serious issue that affects millions of people worldwide.
It is often associated with emotional pain, such as anxiety, stress, or addiction problems.
People who contemplate suicide may feel overwhelmed and believe there’s no solution.
how-to-kill-yourself.com
It is important to raise awareness about this matter and offer a helping hand.
Mental health care can reduce the risk, and reaching out is a necessary first step.
If you or someone you know is thinking about suicide, don’t hesitate to get support.
You are not alone, and support exists.
how-to-kill-yourself.com
Suicide is a complex phenomenon that affects millions of people across the world.
It is often associated with psychological struggles, such as depression, trauma, or chemical dependency.
People who contemplate suicide may feel overwhelmed and believe there’s no hope left.
fast way to kill yourself
It is important to raise awareness about this topic and support those in need.
Mental health care can make a difference, and talking to someone is a brave first step.
If you or someone you know is struggling, get in touch with professionals.
You are not alone, and support exists.
fast way to kill yourself
Suicide is a complex topic that touches many families across the world.
It is often connected to psychological struggles, such as bipolar disorder, trauma, or addiction problems.
People who consider suicide may feel overwhelmed and believe there’s no other way out.
How to kill yourself painless
We must spread knowledge about this subject and help vulnerable individuals.
Mental health care can reduce the risk, and finding help is a necessary first step.
If you or someone you know is in crisis, don’t hesitate to get support.
You are not alone, and there’s always hope.
how-to-kill-yourself.com
Taking one’s own life is a serious topic that impacts millions of people around the globe.
It is often linked to mental health issues, such as bipolar disorder, trauma, or chemical dependency.
People who contemplate suicide may feel trapped and believe there’s no solution.
ways to commit suicide
It is important to spread knowledge about this topic and support those in need.
Early support can reduce the risk, and talking to someone is a brave first step.
If you or someone you know is in crisis, don’t hesitate to get support.
You are not without options, and there’s always hope.
how-to-kill-yourself.com
Taking one’s own life is a serious topic that affects countless lives worldwide.
It is often associated with psychological struggles, such as depression, trauma, or chemical dependency.
People who contemplate suicide may feel overwhelmed and believe there’s no hope left.
how-to-kill-yourself.com
Society needs to talk openly about this topic and offer a helping hand.
Early support can reduce the risk, and finding help is a brave first step.
If you or someone you know is struggling, please seek help.
You are not forgotten, and help is available.
1xbet казино зеркало
На нашем портале вам предоставляется возможность наслаждаться обширной коллекцией слотов.
Эти слоты славятся живой визуализацией и интерактивным игровым процессом.
Каждая игра даёт уникальные бонусные раунды, улучшающие шансы на успех.
1xbet казино официальный сайт
Игра в игровые автоматы предназначена игроков всех уровней.
Можно опробовать игру без ставки, а затем перейти к игре на реальные деньги.
Испытайте удачу и насладитесь неповторимой атмосферой игровых автоматов.
1xbet казино зеркало
На этом сайте вы можете испытать широким ассортиментом слотов.
Слоты обладают яркой графикой и увлекательным игровым процессом.
Каждый игровой автомат предоставляет индивидуальные бонусные функции, увеличивающие шансы на выигрыш.
1xbet казино зеркало
Слоты созданы для игроков всех уровней.
Есть возможность воспользоваться демо-режимом, после чего начать играть на реальные деньги.
Испытайте удачу и насладитесь неповторимой атмосферой игровых автоматов.
1xbet казино
На этом сайте вы можете наслаждаться большим выбором слотов.
Игровые автоматы характеризуются яркой графикой и интерактивным игровым процессом.
Каждый игровой автомат предоставляет уникальные бонусные раунды, улучшающие шансы на успех.
1xbet казино
Игра в слоты подходит игроков всех уровней.
Есть возможность воспользоваться демо-режимом, а затем перейти к игре на реальные деньги.
Проверьте свою удачу и получите удовольствие от яркого мира слотов.
1xbet казино
На этом сайте вы можете наслаждаться широким ассортиментом слотов.
Эти слоты славятся красочной графикой и захватывающим игровым процессом.
Каждый игровой автомат предоставляет индивидуальные бонусные функции, улучшающие шансы на успех.
1xbet игровые автоматы
Игра в слоты подходит любителей азартных игр всех мастей.
Можно опробовать игру без ставки, а затем перейти к игре на реальные деньги.
Попробуйте свои силы и окунитесь в захватывающий мир слотов.
1xbet казино зеркало
На этом сайте вы можете наслаждаться широким ассортиментом игровых автоматов.
Эти слоты славятся красочной графикой и интерактивным игровым процессом.
Каждый игровой автомат предоставляет особые бонусные возможности, улучшающие шансы на успех.
1xbet игровые автоматы
Слоты созданы для как новичков, так и опытных игроков.
Можно опробовать игру без ставки, и потом испытать азарт игры на реальные ставки.
Попробуйте свои силы и окунитесь в захватывающий мир слотов.
1xbet игровые автоматы
На нашем портале вам предоставляется возможность испытать большим выбором слотов.
Эти слоты славятся красочной графикой и интерактивным игровым процессом.
Каждая игра даёт особые бонусные возможности, улучшающие шансы на успех.
1xbet казино зеркало
Слоты созданы для любителей азартных игр всех мастей.
Можно опробовать игру без ставки, а затем перейти к игре на реальные деньги.
Проверьте свою удачу и получите удовольствие от яркого мира слотов.
1xbet казино
На нашем портале вам предоставляется возможность наслаждаться широким ассортиментом игровых автоматов.
Слоты обладают яркой графикой и интерактивным игровым процессом.
Каждый игровой автомат предоставляет уникальные бонусные раунды, улучшающие шансы на успех.
1xbet казино
Игра в слоты подходит любителей азартных игр всех мастей.
Есть возможность воспользоваться демо-режимом, а затем перейти к игре на реальные деньги.
Испытайте удачу и насладитесь неповторимой атмосферой игровых автоматов.
1xbet казино слоты
Здесь вам открывается шанс испытать большим выбором слотов.
Эти слоты славятся яркой графикой и интерактивным игровым процессом.
Каждый игровой автомат предоставляет уникальные бонусные раунды, повышающие вероятность победы.
1xbet казино
Игра в слоты подходит как новичков, так и опытных игроков.
Можно опробовать игру без ставки, а затем перейти к игре на реальные деньги.
Испытайте удачу и насладитесь неповторимой атмосферой игровых автоматов.
1xbet казино официальный сайт
На нашем портале вам предоставляется возможность играть в обширной коллекцией игровых автоматов.
Эти слоты славятся красочной графикой и захватывающим игровым процессом.
Каждый слот предлагает уникальные бонусные раунды, улучшающие шансы на успех.
1xbet казино слоты
Слоты созданы для игроков всех уровней.
Есть возможность воспользоваться демо-режимом, после чего начать играть на реальные деньги.
Попробуйте свои силы и окунитесь в захватывающий мир слотов.
1xbet казино зеркало
На нашем портале вам предоставляется возможность наслаждаться обширной коллекцией слотов.
Эти слоты славятся яркой графикой и интерактивным игровым процессом.
Каждая игра даёт индивидуальные бонусные функции, увеличивающие шансы на выигрыш.
1xbet казино зеркало
Игра в игровые автоматы предназначена как новичков, так и опытных игроков.
Есть возможность воспользоваться демо-режимом, после чего начать играть на реальные деньги.
Испытайте удачу и насладитесь неповторимой атмосферой игровых автоматов.
1xbet казино зеркало
На этом сайте вы можете испытать обширной коллекцией игровых автоматов.
Игровые автоматы характеризуются красочной графикой и интерактивным игровым процессом.
Каждый слот предлагает индивидуальные бонусные функции, улучшающие шансы на успех.
1xbet казино слоты
Слоты созданы для игроков всех уровней.
Можно опробовать игру без ставки, и потом испытать азарт игры на реальные ставки.
Испытайте удачу и насладитесь неповторимой атмосферой игровых автоматов.
1xbet казино
На этом сайте вы можете играть в широким ассортиментом слотов.
Эти слоты славятся живой визуализацией и захватывающим игровым процессом.
Каждый слот предлагает уникальные бонусные раунды, улучшающие шансы на успех.
1xbet казино
Слоты созданы для любителей азартных игр всех мастей.
Вы можете играть бесплатно, а затем перейти к игре на реальные деньги.
Проверьте свою удачу и получите удовольствие от яркого мира слотов.
1xbet игровые автоматы
Здесь вам открывается шанс испытать обширной коллекцией слотов.
Эти слоты славятся красочной графикой и увлекательным игровым процессом.
Каждая игра даёт индивидуальные бонусные функции, увеличивающие шансы на выигрыш.
1xbet казино зеркало
Игра в игровые автоматы предназначена игроков всех уровней.
Есть возможность воспользоваться демо-режимом, а затем перейти к игре на реальные деньги.
Попробуйте свои силы и окунитесь в захватывающий мир слотов.
1xbet казино слоты
На этом сайте вы можете наслаждаться большим выбором слотов.
Эти слоты славятся живой визуализацией и интерактивным игровым процессом.
Каждый игровой автомат предоставляет индивидуальные бонусные функции, увеличивающие шансы на выигрыш.
1xbet казино
Слоты созданы для игроков всех уровней.
Есть возможность воспользоваться демо-режимом, и потом испытать азарт игры на реальные ставки.
Проверьте свою удачу и получите удовольствие от яркого мира слотов.
1xbet игровые автоматы
На этом сайте вы можете наслаждаться широким ассортиментом игровых автоматов.
Эти слоты славятся красочной графикой и захватывающим игровым процессом.
Каждый игровой автомат предоставляет уникальные бонусные раунды, улучшающие шансы на успех.
1xbet казино зеркало
Слоты созданы для как новичков, так и опытных игроков.
Есть возможность воспользоваться демо-режимом, и потом испытать азарт игры на реальные ставки.
Попробуйте свои силы и окунитесь в захватывающий мир слотов.
1xbet казино зеркало
Здесь вам открывается шанс играть в широким ассортиментом игровых слотов.
Игровые автоматы характеризуются живой визуализацией и захватывающим игровым процессом.
Каждая игра даёт индивидуальные бонусные функции, повышающие вероятность победы.
1xbet казино официальный сайт
Слоты созданы для игроков всех уровней.
Вы можете играть бесплатно, после чего начать играть на реальные деньги.
Испытайте удачу и насладитесь неповторимой атмосферой игровых автоматов.
1xbet игровые автоматы
На нашем портале вам предоставляется возможность испытать широким ассортиментом игровых слотов.
Эти слоты славятся живой визуализацией и интерактивным игровым процессом.
Каждый слот предлагает индивидуальные бонусные функции, улучшающие шансы на успех.
1xbet игровые автоматы
Игра в игровые автоматы предназначена как новичков, так и опытных игроков.
Можно опробовать игру без ставки, и потом испытать азарт игры на реальные ставки.
Испытайте удачу и насладитесь неповторимой атмосферой игровых автоматов.
1xbet игровые автоматы
На нашем портале вам предоставляется возможность играть в широким ассортиментом слотов.
Игровые автоматы характеризуются живой визуализацией и интерактивным игровым процессом.
Каждый игровой автомат предоставляет особые бонусные возможности, повышающие вероятность победы.
1xbet казино зеркало
Игра в игровые автоматы предназначена игроков всех уровней.
Можно опробовать игру без ставки, после чего начать играть на реальные деньги.
Испытайте удачу и насладитесь неповторимой атмосферой игровых автоматов.
1xbet казино официальный сайт
На нашем портале вам предоставляется возможность наслаждаться широким ассортиментом игровых слотов.
Слоты обладают красочной графикой и увлекательным игровым процессом.
Каждый слот предлагает индивидуальные бонусные функции, увеличивающие шансы на выигрыш.
1xbet казино зеркало
Игра в слоты подходит любителей азартных игр всех мастей.
Можно опробовать игру без ставки, после чего начать играть на реальные деньги.
Проверьте свою удачу и получите удовольствие от яркого мира слотов.
1xbet казино официальный сайт
Здесь вам открывается шанс наслаждаться обширной коллекцией слотов.
Слоты обладают живой визуализацией и интерактивным игровым процессом.
Каждый слот предлагает особые бонусные возможности, повышающие вероятность победы.
1xbet казино официальный сайт
Игра в игровые автоматы предназначена любителей азартных игр всех мастей.
Вы можете играть бесплатно, а затем перейти к игре на реальные деньги.
Испытайте удачу и насладитесь неповторимой атмосферой игровых автоматов.
1xbet казино зеркало
На этом сайте вы можете играть в обширной коллекцией игровых слотов.
Игровые автоматы характеризуются живой визуализацией и увлекательным игровым процессом.
Каждый слот предлагает уникальные бонусные раунды, повышающие вероятность победы.
1xbet казино официальный сайт
Игра в игровые автоматы предназначена как новичков, так и опытных игроков.
Можно опробовать игру без ставки, а затем перейти к игре на реальные деньги.
Испытайте удачу и насладитесь неповторимой атмосферой игровых автоматов.
1xbet казино слоты
Здесь вам открывается шанс играть в широким ассортиментом слотов.
Эти слоты славятся красочной графикой и захватывающим игровым процессом.
Каждый игровой автомат предоставляет индивидуальные бонусные функции, улучшающие шансы на успех.
1xbet игровые автоматы
Слоты созданы для игроков всех уровней.
Есть возможность воспользоваться демо-режимом, и потом испытать азарт игры на реальные ставки.
Попробуйте свои силы и окунитесь в захватывающий мир слотов.
1xbet казино официальный сайт
На нашем портале вам предоставляется возможность испытать обширной коллекцией игровых автоматов.
Слоты обладают яркой графикой и увлекательным игровым процессом.
Каждый слот предлагает особые бонусные возможности, увеличивающие шансы на выигрыш.
1xbet казино зеркало
Слоты созданы для игроков всех уровней.
Вы можете играть бесплатно, после чего начать играть на реальные деньги.
Проверьте свою удачу и получите удовольствие от яркого мира слотов.
1xbet казино зеркало
Здесь вам открывается шанс играть в большим выбором слотов.
Игровые автоматы характеризуются красочной графикой и увлекательным игровым процессом.
Каждая игра даёт особые бонусные возможности, увеличивающие шансы на выигрыш.
1xbet игровые автоматы
Игра в игровые автоматы предназначена как новичков, так и опытных игроков.
Есть возможность воспользоваться демо-режимом, после чего начать играть на реальные деньги.
Испытайте удачу и насладитесь неповторимой атмосферой игровых автоматов.
1xbet казино слоты
Здесь вам открывается шанс наслаждаться обширной коллекцией слотов.
Слоты обладают яркой графикой и захватывающим игровым процессом.
Каждая игра даёт уникальные бонусные раунды, улучшающие шансы на успех.
1xbet казино
Игра в игровые автоматы предназначена игроков всех уровней.
Можно опробовать игру без ставки, после чего начать играть на реальные деньги.
Испытайте удачу и насладитесь неповторимой атмосферой игровых автоматов.
1xbet игровые автоматы
На этом сайте вы можете наслаждаться большим выбором игровых слотов.
Игровые автоматы характеризуются красочной графикой и увлекательным игровым процессом.
Каждый игровой автомат предоставляет индивидуальные бонусные функции, повышающие вероятность победы.
1xbet игровые автоматы
Игра в слоты подходит игроков всех уровней.
Вы можете играть бесплатно, а затем перейти к игре на реальные деньги.
Попробуйте свои силы и окунитесь в захватывающий мир слотов.
1xbet казино официальный сайт
Здесь вам открывается шанс испытать большим выбором игровых автоматов.
Слоты обладают яркой графикой и увлекательным игровым процессом.
Каждая игра даёт особые бонусные возможности, увеличивающие шансы на выигрыш.
1xbet казино
Слоты созданы для как новичков, так и опытных игроков.
Вы можете играть бесплатно, а затем перейти к игре на реальные деньги.
Проверьте свою удачу и получите удовольствие от яркого мира слотов.
1xbet казино официальный сайт
На нашем портале вам предоставляется возможность играть в большим выбором игровых слотов.
Слоты обладают живой визуализацией и интерактивным игровым процессом.
Каждый игровой автомат предоставляет уникальные бонусные раунды, улучшающие шансы на успех.
1xbet казино официальный сайт
Слоты созданы для игроков всех уровней.
Можно опробовать игру без ставки, и потом испытать азарт игры на реальные ставки.
Испытайте удачу и насладитесь неповторимой атмосферой игровых автоматов.
1xbet казино
На нашем портале вам предоставляется возможность испытать большим выбором игровых автоматов.
Эти слоты славятся яркой графикой и захватывающим игровым процессом.
Каждый игровой автомат предоставляет уникальные бонусные раунды, увеличивающие шансы на выигрыш.
1xbet игровые автоматы
Слоты созданы для любителей азартных игр всех мастей.
Вы можете играть бесплатно, и потом испытать азарт игры на реальные ставки.
Проверьте свою удачу и получите удовольствие от яркого мира слотов.
1xbet казино слоты
Здесь вам открывается шанс наслаждаться обширной коллекцией слотов.
Слоты обладают яркой графикой и интерактивным игровым процессом.
Каждая игра даёт уникальные бонусные раунды, увеличивающие шансы на выигрыш.
1xbet казино официальный сайт
Слоты созданы для как новичков, так и опытных игроков.
Есть возможность воспользоваться демо-режимом, и потом испытать азарт игры на реальные ставки.
Испытайте удачу и насладитесь неповторимой атмосферой игровых автоматов.
1xbet казино
На нашем портале вам предоставляется возможность испытать широким ассортиментом игровых автоматов.
Игровые автоматы характеризуются живой визуализацией и захватывающим игровым процессом.
Каждый игровой автомат предоставляет уникальные бонусные раунды, улучшающие шансы на успех.
1xbet казино зеркало
Игра в слоты подходит как новичков, так и опытных игроков.
Есть возможность воспользоваться демо-режимом, и потом испытать азарт игры на реальные ставки.
Попробуйте свои силы и окунитесь в захватывающий мир слотов.
маяк слот
Игровые автоматы — это одна из востребованных разновидностей игр в индустрии азартных игр.
Основная суть слотов заключается в выпадении символов, что создают комбинации.
Любая такая игра включает уникальные особенности, разные иконки и специальные бонусы, которые делают игру интереснее.
Игровые автоматы подразделяются на традиционные и продвинутые, в которых встречаются различные бонусные режимы.
магнит слот
Многие ценят эти игры за интуитивность и способность увлечь с минимумом тактических решений.
Современные игровые механики могут включать различные специальные символы, что делает процесс еще увлекательнее.
Таким образом, игровые автоматы остаются одним из самых востребованных способов весело провести время в индустрии ставок.
слоты игры
Онлайн-слоты — это одна из востребованных игровых механик в индустрии азартных игр.
Смысл слотов основана на вращении барабанов, результат которых формируют выигрышные линии.
Каждый автомат включает уникальные особенности, многочисленные знаки и специальные бонусы, которые добавляют азарта.
Слоты делятся на ретро-стильные и продвинутые, в которых встречаются разные уровни сложности.
слоты вулкан
Многие ценят слоты за простоту правил и интересный игровой процесс без сложных стратегий.
Современные игровые механики могут включать дополнительные бонусные игры, что привлекает новых пользователей.
В итоге, слоты остаются очень популярным вариантов отдыха в индустрии ставок.
PatrickEntig
This portal features plenty of slot games, suitable for all types of players.
On this site, you can find traditional machines, feature-rich games, and huge-win machines with amazing animations and realistic audio.
Whether you’re looking for easy fun or seek bonus-rich rounds, you’re sure to find what you’re looking for.
https://www.shortcut.ru/pag/kak_opticheski_uvelichity_spalynyu_neskolyko_prostyh_sovetov.html
Every slot are available anytime, with no installation, and perfectly tuned for both PC and mobile.
Besides slots, the site provides tips and tricks, bonuses, and user ratings to guide your play.
Register today, spin the reels, and enjoy the world of digital reels!
PatrickEntig
Our platform features a wide selection of video slots, suitable for both beginners and experienced users.
Here, you can discover classic slots, new generation slots, and huge-win machines with amazing animations and immersive sound.
Whether you’re into simple gameplay or seek engaging stories, you’re sure to find something that suits you.
https://tipsforefficiency.com/art/?ekonomim_trafik_na_smartfone_chasty_2.html
Every slot is playable 24/7, right in your browser, and fully optimized for both PC and mobile.
Apart from the machines, the site includes helpful reviews, welcome packages, and user ratings to guide your play.
Sign up, jump into the action, and enjoy the thrill of online slots!
PatrickEntig
Our platform offers a large variety of online slots, suitable for all types of players.
Right here, you can discover retro-style games, feature-rich games, and jackpot slots with stunning graphics and realistic audio.
Whether you’re into simple gameplay or prefer engaging stories, you’ll find something that suits you.
http://myimperia.ru/42228-%D0%BC%D0%BE%D0%BA%D1%80%D1%8B%D0%B5-%D0%BA%D1%80%D0%BE%D1%81%D1%81%D1%8B-%D0%B8-hk416-%D1%81%D0%BF%D0%B5%D1%86%D0%BD%D0%B0%D0%B7-%D0%BD%D0%B8%D0%B4%D0%B5%D1%80%D0%BB%D0%B0%D0%BD%D0%B4%D0%BE%D0%B2.html
Every slot is playable anytime, with no installation, and perfectly tuned for both all devices.
In addition to games, the site features slot guides, special offers, and user ratings to help you choose.
Join now, spin the reels, and enjoy the thrill of online slots!
PatrickEntig
Our platform features plenty of video slots, designed for both beginners and experienced users.
On this site, you can find classic slots, modern video slots, and jackpot slots with high-quality visuals and dynamic music.
No matter if you’re looking for easy fun or prefer bonus-rich rounds, this site has something that suits you.
http://i-no.ru/balans-mezhdu-populyarnostyu-i-riskami-lajki-i-podpischiki.html
Every slot can be accessed 24/7, right in your browser, and fully optimized for both desktop and smartphone.
Besides slots, the site provides tips and tricks, bonuses, and user ratings to guide your play.
Join now, start playing, and get immersed in the excitement of spinning!
PatrickEntig
This portal provides access to a wide selection of slot games, ideal for all types of players.
Right here, you can discover traditional machines, modern video slots, and jackpot slots with high-quality visuals and dynamic music.
Whether you’re into simple gameplay or prefer complex features, you’re sure to find something that suits you.
http://tankfront.ru/axis/pages/?ukroschenie_toksikoza_narodnye_sredstva_na_straghe_utrenney_toshnoty.html
All games is playable anytime, with no installation, and perfectly tuned for both desktop and smartphone.
Apart from the machines, the site includes slot guides, special offers, and user ratings to help you choose.
Join now, spin the reels, and get immersed in the world of digital reels!
PatrickEntig
This portal provides access to a wide selection of slot games, designed for different gaming styles.
On this site, you can discover retro-style games, modern video slots, and progressive jackpots with amazing animations and immersive sound.
If you are into simple gameplay or love complex features, you’ll find a perfect match.
http://forum.vorchun.ru/viewtopic.php?f=2&t=326653
Every slot is playable anytime, no download needed, and fully optimized for both PC and mobile.
Besides slots, the site includes slot guides, bonuses, and community opinions to help you choose.
Register today, jump into the action, and enjoy the excitement of spinning!
PatrickEntig
This portal features plenty of slot games, designed for all types of players.
Here, you can explore classic slots, feature-rich games, and huge-win machines with stunning graphics and dynamic music.
Whether you’re into simple gameplay or seek engaging stories, you’re sure to find a perfect match.
http://dinozavrikus.ru/art/kak_nachaty_ghity_prosche.html
Each title are available around the clock, right in your browser, and well adapted for both all devices.
In addition to games, the site includes tips and tricks, welcome packages, and player feedback to help you choose.
Sign up, jump into the action, and enjoy the excitement of spinning!
PatrickEntig
Our platform provides access to a large variety of video slots, ideal for all types of players.
Here, you can discover traditional machines, new generation slots, and huge-win machines with high-quality visuals and immersive sound.
If you are looking for easy fun or love engaging stories, this site has a perfect match.
https://blogs.rufox.ru/~dimafikas/60640.htm
All games are available anytime, right in your browser, and fully optimized for both desktop and smartphone.
In addition to games, the site features slot guides, special offers, and player feedback to guide your play.
Join now, spin the reels, and get immersed in the world of digital reels!
PatrickEntig
This portal provides access to a wide selection of slot games, suitable for both beginners and experienced users.
On this site, you can discover retro-style games, new generation slots, and jackpot slots with amazing animations and realistic audio.
No matter if you’re a fan of minimal mechanics or prefer bonus-rich rounds, you’ll find a perfect match.
https://online.sktorrent.eu/include/articles/vybiraem_nadeghnoe_i_funkcionalynoe_napolynoe_pokrytie.html
Each title can be accessed around the clock, no download needed, and perfectly tuned for both PC and mobile.
In addition to games, the site provides helpful reviews, special offers, and user ratings to help you choose.
Join now, start playing, and enjoy the excitement of spinning!
Jonahron
На нашем портале вам предоставляется возможность играть в широким ассортиментом игровых слотов.
Игровые автоматы характеризуются яркой графикой и увлекательным игровым процессом.
Каждый игровой автомат предоставляет индивидуальные бонусные функции, увеличивающие шансы на выигрыш.
1win games
Слоты созданы для как новичков, так и опытных игроков.
Можно опробовать игру без ставки, и потом испытать азарт игры на реальные ставки.
Попробуйте свои силы и окунитесь в захватывающий мир слотов.
PatrickEntig
This website offers plenty of slot games, suitable for different gaming styles.
On this site, you can find retro-style games, new generation slots, and jackpot slots with stunning graphics and realistic audio.
Whether you’re looking for easy fun or seek bonus-rich rounds, you’re sure to find what you’re looking for.
https://andresiymr62739.blogadvize.com/41192415/plinko-demo-Слот-Играйте-бесплатно-и-осваивайте-стратегии
Every slot are available around the clock, right in your browser, and perfectly tuned for both PC and mobile.
Besides slots, the site features helpful reviews, bonuses, and community opinions to guide your play.
Join now, start playing, and have fun with the world of digital reels!
Jonahron
На нашем портале вам предоставляется возможность наслаждаться обширной коллекцией слотов.
Игровые автоматы характеризуются живой визуализацией и захватывающим игровым процессом.
Каждый слот предлагает особые бонусные возможности, увеличивающие шансы на выигрыш.
1 win
Слоты созданы для любителей азартных игр всех мастей.
Вы можете играть бесплатно, а затем перейти к игре на реальные деньги.
Испытайте удачу и насладитесь неповторимой атмосферой игровых автоматов.
Jonahron
На нашем портале вам предоставляется возможность играть в широким ассортиментом слотов.
Эти слоты славятся красочной графикой и увлекательным игровым процессом.
Каждый игровой автомат предоставляет индивидуальные бонусные функции, повышающие вероятность победы.
one win
Игра в слоты подходит как новичков, так и опытных игроков.
Вы можете играть бесплатно, после чего начать играть на реальные деньги.
Попробуйте свои силы и окунитесь в захватывающий мир слотов.
Jonahron
На нашем портале вам предоставляется возможность испытать широким ассортиментом слотов.
Эти слоты славятся живой визуализацией и интерактивным игровым процессом.
Каждый слот предлагает уникальные бонусные раунды, улучшающие шансы на успех.
one win
Игра в игровые автоматы предназначена игроков всех уровней.
Есть возможность воспользоваться демо-режимом, после чего начать играть на реальные деньги.
Испытайте удачу и насладитесь неповторимой атмосферой игровых автоматов.
Jonahron
На этом сайте вы можете наслаждаться большим выбором игровых автоматов.
Слоты обладают живой визуализацией и захватывающим игровым процессом.
Каждый слот предлагает уникальные бонусные раунды, повышающие вероятность победы.
1win casino
Слоты созданы для любителей азартных игр всех мастей.
Есть возможность воспользоваться демо-режимом, и потом испытать азарт игры на реальные ставки.
Попробуйте свои силы и окунитесь в захватывающий мир слотов.
Jonahron
На этом сайте вы можете играть в широким ассортиментом игровых слотов.
Игровые автоматы характеризуются живой визуализацией и увлекательным игровым процессом.
Каждая игра даёт особые бонусные возможности, увеличивающие шансы на выигрыш.
one win
Игра в игровые автоматы предназначена любителей азартных игр всех мастей.
Можно опробовать игру без ставки, а затем перейти к игре на реальные деньги.
Проверьте свою удачу и получите удовольствие от яркого мира слотов.
PatrickEntig
This portal provides access to plenty of slot games, ideal for both beginners and experienced users.
On this site, you can explore classic slots, feature-rich games, and huge-win machines with stunning graphics and realistic audio.
No matter if you’re into simple gameplay or seek complex features, you’re sure to find something that suits you.
https://29ru.listbb.ru/viewtopic.php?f=26&t=3595
All games are available anytime, no download needed, and well adapted for both desktop and smartphone.
Besides slots, the site provides tips and tricks, bonuses, and user ratings to help you choose.
Join now, spin the reels, and have fun with the world of digital reels!
Jonahron
На нашем портале вам предоставляется возможность наслаждаться широким ассортиментом слотов.
Эти слоты славятся красочной графикой и захватывающим игровым процессом.
Каждый слот предлагает особые бонусные возможности, улучшающие шансы на успех.
1win casino
Игра в слоты подходит игроков всех уровней.
Есть возможность воспользоваться демо-режимом, а затем перейти к игре на реальные деньги.
Попробуйте свои силы и окунитесь в захватывающий мир слотов.
Jonahron
Здесь вам открывается шанс наслаждаться обширной коллекцией слотов.
Игровые автоматы характеризуются яркой графикой и увлекательным игровым процессом.
Каждая игра даёт уникальные бонусные раунды, повышающие вероятность победы.
1 win
Игра в игровые автоматы предназначена игроков всех уровней.
Есть возможность воспользоваться демо-режимом, после чего начать играть на реальные деньги.
Попробуйте свои силы и окунитесь в захватывающий мир слотов.
Jonahron
На этом сайте вы можете играть в обширной коллекцией игровых автоматов.
Слоты обладают яркой графикой и увлекательным игровым процессом.
Каждая игра даёт индивидуальные бонусные функции, улучшающие шансы на успех.
1win casino
Слоты созданы для игроков всех уровней.
Есть возможность воспользоваться демо-режимом, а затем перейти к игре на реальные деньги.
Проверьте свою удачу и получите удовольствие от яркого мира слотов.
Jonahron
На этом сайте вы можете играть в обширной коллекцией игровых автоматов.
Игровые автоматы характеризуются живой визуализацией и захватывающим игровым процессом.
Каждый игровой автомат предоставляет уникальные бонусные раунды, повышающие вероятность победы.
1 win
Слоты созданы для как новичков, так и опытных игроков.
Вы можете играть бесплатно, после чего начать играть на реальные деньги.
Испытайте удачу и насладитесь неповторимой атмосферой игровых автоматов.
Jonahron
На этом сайте вы можете играть в широким ассортиментом игровых автоматов.
Эти слоты славятся красочной графикой и увлекательным игровым процессом.
Каждая игра даёт особые бонусные возможности, увеличивающие шансы на выигрыш.
1 win
Слоты созданы для как новичков, так и опытных игроков.
Можно опробовать игру без ставки, и потом испытать азарт игры на реальные ставки.
Попробуйте свои силы и окунитесь в захватывающий мир слотов.
Jonahron
На нашем портале вам предоставляется возможность играть в широким ассортиментом слотов.
Эти слоты славятся живой визуализацией и увлекательным игровым процессом.
Каждый игровой автомат предоставляет уникальные бонусные раунды, улучшающие шансы на успех.
1win
Слоты созданы для любителей азартных игр всех мастей.
Можно опробовать игру без ставки, и потом испытать азарт игры на реальные ставки.
Проверьте свою удачу и получите удовольствие от яркого мира слотов.
Jonahron
На нашем портале вам предоставляется возможность испытать широким ассортиментом игровых автоматов.
Игровые автоматы характеризуются красочной графикой и увлекательным игровым процессом.
Каждый игровой автомат предоставляет уникальные бонусные раунды, повышающие вероятность победы.
1 win
Игра в игровые автоматы предназначена любителей азартных игр всех мастей.
Есть возможность воспользоваться демо-режимом, и потом испытать азарт игры на реальные ставки.
Испытайте удачу и насладитесь неповторимой атмосферой игровых автоматов.
Jonahron
Здесь вам открывается шанс наслаждаться широким ассортиментом игровых слотов.
Эти слоты славятся живой визуализацией и захватывающим игровым процессом.
Каждая игра даёт уникальные бонусные раунды, увеличивающие шансы на выигрыш.
1win casino
Игра в игровые автоматы предназначена любителей азартных игр всех мастей.
Есть возможность воспользоваться демо-режимом, и потом испытать азарт игры на реальные ставки.
Попробуйте свои силы и окунитесь в захватывающий мир слотов.
Jonahron
На этом сайте вы можете испытать широким ассортиментом игровых слотов.
Слоты обладают живой визуализацией и захватывающим игровым процессом.
Каждая игра даёт особые бонусные возможности, увеличивающие шансы на выигрыш.
1win
Слоты созданы для игроков всех уровней.
Есть возможность воспользоваться демо-режимом, и потом испытать азарт игры на реальные ставки.
Проверьте свою удачу и получите удовольствие от яркого мира слотов.
Jonahron
Здесь вам открывается шанс испытать большим выбором слотов.
Игровые автоматы характеризуются красочной графикой и захватывающим игровым процессом.
Каждый слот предлагает особые бонусные возможности, повышающие вероятность победы.
1win casino
Игра в игровые автоматы предназначена как новичков, так и опытных игроков.
Есть возможность воспользоваться демо-режимом, после чего начать играть на реальные деньги.
Испытайте удачу и насладитесь неповторимой атмосферой игровых автоматов.
Jonahron
На этом сайте вы можете испытать большим выбором игровых автоматов.
Слоты обладают красочной графикой и захватывающим игровым процессом.
Каждый игровой автомат предоставляет уникальные бонусные раунды, улучшающие шансы на успех.
1win casino
Игра в слоты подходит любителей азартных игр всех мастей.
Есть возможность воспользоваться демо-режимом, а затем перейти к игре на реальные деньги.
Испытайте удачу и насладитесь неповторимой атмосферой игровых автоматов.
Jonahron
На этом сайте вы можете испытать большим выбором слотов.
Слоты обладают живой визуализацией и захватывающим игровым процессом.
Каждый слот предлагает уникальные бонусные раунды, улучшающие шансы на успех.
1win games
Игра в слоты подходит как новичков, так и опытных игроков.
Есть возможность воспользоваться демо-режимом, а затем перейти к игре на реальные деньги.
Проверьте свою удачу и получите удовольствие от яркого мира слотов.
Jonahron
На этом сайте вы можете испытать обширной коллекцией игровых слотов.
Эти слоты славятся яркой графикой и захватывающим игровым процессом.
Каждый игровой автомат предоставляет особые бонусные возможности, увеличивающие шансы на выигрыш.
1win games
Игра в игровые автоматы предназначена любителей азартных игр всех мастей.
Есть возможность воспользоваться демо-режимом, и потом испытать азарт игры на реальные ставки.
Испытайте удачу и насладитесь неповторимой атмосферой игровых автоматов.
Jonahron
На нашем портале вам предоставляется возможность наслаждаться большим выбором игровых автоматов.
Эти слоты славятся живой визуализацией и увлекательным игровым процессом.
Каждая игра даёт уникальные бонусные раунды, повышающие вероятность победы.
1win
Слоты созданы для любителей азартных игр всех мастей.
Есть возможность воспользоваться демо-режимом, после чего начать играть на реальные деньги.
Испытайте удачу и насладитесь неповторимой атмосферой игровых автоматов.
Jonahron
Здесь вам открывается шанс наслаждаться широким ассортиментом игровых слотов.
Эти слоты славятся яркой графикой и интерактивным игровым процессом.
Каждый игровой автомат предоставляет индивидуальные бонусные функции, повышающие вероятность победы.
one win
Слоты созданы для как новичков, так и опытных игроков.
Вы можете играть бесплатно, и потом испытать азарт игры на реальные ставки.
Испытайте удачу и насладитесь неповторимой атмосферой игровых автоматов.
Jonahron
На этом сайте вы можете наслаждаться большим выбором игровых автоматов.
Игровые автоматы характеризуются живой визуализацией и увлекательным игровым процессом.
Каждый слот предлагает особые бонусные возможности, улучшающие шансы на успех.
1win games
Игра в игровые автоматы предназначена как новичков, так и опытных игроков.
Вы можете играть бесплатно, и потом испытать азарт игры на реальные ставки.
Испытайте удачу и насладитесь неповторимой атмосферой игровых автоматов.
Jonahron
На нашем портале вам предоставляется возможность наслаждаться большим выбором слотов.
Слоты обладают живой визуализацией и захватывающим игровым процессом.
Каждый игровой автомат предоставляет уникальные бонусные раунды, увеличивающие шансы на выигрыш.
1win
Игра в игровые автоматы предназначена любителей азартных игр всех мастей.
Есть возможность воспользоваться демо-режимом, а затем перейти к игре на реальные деньги.
Испытайте удачу и насладитесь неповторимой атмосферой игровых автоматов.
Bob
These are genuinely fantastic ideas in regarding blogging.
You have touched some fastidious points here. Any way keep up wrinting.
Have a look at my website – Преимущества пилинга
ways to commit suicide
Self-harm leading to death is a tragic topic that touches millions of people around the globe.
It is often associated with psychological struggles, such as depression, hopelessness, or chemical dependency.
People who contemplate suicide may feel trapped and believe there’s no other way out.
how-to-kill-yourself.com
We must spread knowledge about this topic and support those in need.
Early support can make a difference, and finding help is a crucial first step.
If you or someone you know is in crisis, please seek help.
You are not forgotten, and there’s always hope.
how to commit suicide without pain
Self-harm leading to death is a complex topic that impacts countless lives across the world.
It is often linked to mental health issues, such as depression, trauma, or substance abuse.
People who struggle with suicide may feel isolated and believe there’s no other way out.
how-to-kill-yourself.com
We must talk openly about this subject and offer a helping hand.
Mental health care can reduce the risk, and finding help is a crucial first step.
If you or someone you know is in crisis, get in touch with professionals.
You are not alone, and support exists.
Dominga
Hello, all the time i used to check weblog posts here in the early hours in the break of day, as i like to gain knowledge of
more and more.
Feel free to visit my web blog … Избегаем активности после ботокса
Denniscendy
На данном ресурсе вы можете найти популярные онлайн-слоты.
Мы предлагаем подборку слотов от ведущих провайдеров.
Любой автомат предлагает высоким качеством, дополнительными возможностями и честными шансами на выигрыш.
https://nortonsafe.search.ask.com/web?q=casinoreg.net
Вы сможете тестировать автоматы без вложений или делать реальные ставки.
Меню и структура ресурса интуитивно понятны, что облегчает поиск игр.
Если вас интересуют слоты, данный ресурс стоит посетить.
Попробуйте удачу на сайте — возможно, именно сегодня вам повезёт!
Denniscendy
На этом сайте можно найти различные игровые слоты.
Мы собрали лучшую коллекцию игр от популярных брендов.
Каждая игра обладает уникальной графикой, увлекательными бонусами и максимальной волатильностью.
https://orbitsrises.com/the-buzzing-landscape-of-online-casinos/
Вы сможете играть в демо-режиме или играть на деньги.
Навигация по сайту интуитивно понятны, что облегчает поиск игр.
Если вы любите азартные игры, данный ресурс стоит посетить.
Начинайте играть уже сегодня — тысячи выигрышей ждут вас!
сайт champion casino
На данной платформе вы сможете найти лучшие онлайн-автоматы на платформе Champion.
Ассортимент игр включает традиционные игры и современные слоты с яркой графикой и разнообразными функциями.
Любая игра разработан для максимального удовольствия как на компьютере, так и на смартфонах.
Независимо от опыта, здесь вы найдёте подходящий вариант.
champion casino бонус
Автоматы запускаются в любое время и не требуют скачивания.
Кроме того, сайт предусматривает бонусы и рекомендации, для улучшения опыта.
Попробуйте прямо сейчас и насладитесь азартом с брендом Champion!
champion slots
На этом сайте вы найдёте разнообразные игровые слоты в казино Champion.
Коллекция игр включает традиционные игры и актуальные новинки с яркой графикой и разнообразными функциями.
Всякий автомат разработан для комфортного использования как на десктопе, так и на мобильных устройствах.
Независимо от опыта, здесь вы обязательно подберёте слот по душе.
online
Игры доступны без ограничений и не требуют скачивания.
Также сайт предлагает акции и рекомендации, для удобства пользователей.
Попробуйте прямо сейчас и испытайте удачу с казино Champion!
champion регистрация
Здесь вы найдёте интересные игровые слоты на платформе Champion.
Ассортимент игр содержит проверенные временем слоты и современные слоты с яркой графикой и специальными возможностями.
Каждый слот оптимизирован для комфортного использования как на десктопе, так и на мобильных устройствах.
Независимо от опыта, здесь вы сможете выбрать что-то по вкусу.
champion casino приложение
Слоты работают круглосуточно и не требуют скачивания.
Дополнительно сайт предусматривает акции и рекомендации, чтобы сделать игру ещё интереснее.
Погрузитесь в игру уже сегодня и насладитесь азартом с играми от Champion!
champion casino
На данной платформе вы найдёте лучшие онлайн-автоматы в казино Champion.
Выбор игр представляет традиционные игры и новейшие видеослоты с качественной анимацией и специальными возможностями.
Каждый слот создан для комфортного использования как на компьютере, так и на планшетах.
Независимо от опыта, здесь вы сможете выбрать что-то по вкусу.
champion casino зеркало
Автоматы работают круглосуточно и работают прямо в браузере.
Также сайт предлагает бонусы и полезную информацию, для удобства пользователей.
Погрузитесь в игру уже сегодня и насладитесь азартом с казино Champion!
скачать приложение champion
Здесь вы найдёте лучшие слоты казино в казино Champion.
Ассортимент игр содержит традиционные игры и современные слоты с качественной анимацией и разнообразными функциями.
Любая игра оптимизирован для удобной игры как на десктопе, так и на смартфонах.
Даже если вы впервые играете, здесь вы найдёте подходящий вариант.
приложение champions
Автоматы запускаются в любое время и работают прямо в браузере.
Дополнительно сайт предоставляет бонусы и обзоры игр, для улучшения опыта.
Погрузитесь в игру уже сегодня и испытайте удачу с играми от Champion!
champion casino
На этом сайте вы сможете найти разнообразные игровые слоты в казино Champion.
Выбор игр включает классические автоматы и новейшие видеослоты с яркой графикой и уникальными бонусами.
Любая игра оптимизирован для максимального удовольствия как на компьютере, так и на смартфонах.
Даже если вы впервые играете, здесь вы найдёте подходящий вариант.
сайт champion casino
Слоты доступны без ограничений и не требуют скачивания.
Дополнительно сайт предлагает акции и полезную информацию, для удобства пользователей.
Начните играть прямо сейчас и насладитесь азартом с играми от Champion!
чемпион регистрация
На этом сайте вы обнаружите интересные онлайн-автоматы в казино Champion.
Коллекция игр содержит классические автоматы и актуальные новинки с качественной анимацией и уникальными бонусами.
Любая игра разработан для удобной игры как на компьютере, так и на смартфонах.
Будь вы новичком или профи, здесь вы найдёте подходящий вариант.
рабочее зеркал
Игры работают круглосуточно и не нуждаются в установке.
Кроме того, сайт предусматривает бонусы и обзоры игр, для удобства пользователей.
Начните играть прямо сейчас и насладитесь азартом с брендом Champion!
champion casino бонус
На этом сайте вы найдёте интересные слоты казино на платформе Champion.
Коллекция игр содержит классические автоматы и актуальные новинки с яркой графикой и специальными возможностями.
Любая игра оптимизирован для удобной игры как на ПК, так и на смартфонах.
Будь вы новичком или профи, здесь вы сможете выбрать что-то по вкусу.
официальный
Автоматы работают круглосуточно и не требуют скачивания.
Дополнительно сайт предлагает акции и обзоры игр, для улучшения опыта.
Начните играть прямо сейчас и испытайте удачу с брендом Champion!
champion casino приложение
На этом сайте вы сможете найти лучшие онлайн-автоматы от казино Champion.
Выбор игр содержит традиционные игры и новейшие видеослоты с качественной анимацией и уникальными бонусами.
Любая игра разработан для максимального удовольствия как на компьютере, так и на мобильных устройствах.
Даже если вы впервые играете, здесь вы обязательно подберёте слот по душе.
champion игровые автоматы
Игры запускаются в любое время и не нуждаются в установке.
Дополнительно сайт предлагает бонусы и обзоры игр, чтобы сделать игру ещё интереснее.
Погрузитесь в игру уже сегодня и насладитесь азартом с брендом Champion!
скачать приложение
На этом сайте вы найдёте лучшие онлайн-автоматы от казино Champion.
Выбор игр представляет традиционные игры и актуальные новинки с качественной анимацией и уникальными бонусами.
Всякий автомат разработан для удобной игры как на компьютере, так и на смартфонах.
Независимо от опыта, здесь вы сможете выбрать что-то по вкусу.
сайт champion casino
Автоматы запускаются в любое время и работают прямо в браузере.
Кроме того, сайт предоставляет программы лояльности и рекомендации, для улучшения опыта.
Погрузитесь в игру уже сегодня и насладитесь азартом с казино Champion!
champion slots
На данной платформе вы сможете найти разнообразные игровые слоты в казино Champion.
Коллекция игр представляет традиционные игры и актуальные новинки с захватывающим оформлением и специальными возможностями.
Каждый слот разработан для комфортного использования как на ПК, так и на смартфонах.
Будь вы новичком или профи, здесь вы сможете выбрать что-то по вкусу.
champion casino приложение
Автоматы работают круглосуточно и работают прямо в браузере.
Также сайт предоставляет бонусы и полезную информацию, чтобы сделать игру ещё интереснее.
Погрузитесь в игру уже сегодня и испытайте удачу с казино Champion!
чемпион регистрация
На этом сайте вы обнаружите лучшие слоты казино на платформе Champion.
Ассортимент игр включает классические автоматы и современные слоты с яркой графикой и разнообразными функциями.
Всякий автомат оптимизирован для комфортного использования как на ПК, так и на мобильных устройствах.
Будь вы новичком или профи, здесь вы найдёте подходящий вариант.
casino чемпион
Игры доступны без ограничений и не требуют скачивания.
Кроме того, сайт предусматривает программы лояльности и рекомендации, чтобы сделать игру ещё интереснее.
Начните играть прямо сейчас и насладитесь азартом с казино Champion!
бонус вавада
На данной платформе доступны онлайн-игры из казино Вавада.
Каждый гость может подобрать автомат по интересам — от простых игр до современных разработок с анимацией.
Казино Vavada предоставляет широкий выбор проверенных автоматов, включая слоты с крупными выигрышами.
Все игры работает в любое время и оптимизирован как для компьютеров, так и для планшетов.
игровые автоматы vavada
Каждый геймер ощутит настоящим драйвом, не выходя из квартиры.
Навигация по сайту проста, что обеспечивает без труда начать играть.
Начните прямо сейчас, чтобы почувствовать азарт с Vavada!
официальный сайт vavada
Здесь доступны игровые автоматы от казино Vavada.
Любой игрок может подобрать слот на свой вкус — от простых аппаратов до видеослотов слотов с анимацией.
Vavada предлагает доступ к популярных игр, включая игры с джекпотом.
Любой автомат работает без ограничений и адаптирован как для настольных устройств, так и для мобильных устройств.
вавада бонусы на сегодня
Игроки могут наслаждаться настоящим драйвом, не выходя из любимого кресла.
Структура платформы проста, что обеспечивает моментально приступить к игре.
Присоединяйтесь сейчас, чтобы почувствовать азарт с Vavada!
вавада зеркало рабочее
На данной платформе доступны слоты из казино Вавада.
Каждый гость найдёт слот на свой вкус — от классических одноруких бандитов до новейших слотов с яркой графикой.
Платформа Vavada открывает доступ к проверенных автоматов, включая прогрессивные слоты.
Любой автомат доступен круглосуточно и подходит как для ПК, так и для планшетов.
вавада зеркало сегодня
Игроки могут наслаждаться настоящим драйвом, не выходя из любимого кресла.
Навигация по сайту понятна, что позволяет моментально приступить к игре.
Начните прямо сейчас, чтобы открыть для себя любимые слоты!
вавада регистрация
На этом сайте доступны игровые автоматы от казино Vavada.
Каждый пользователь может подобрать автомат по интересам — от простых игр до новейших слотов с анимацией.
Vavada предлагает широкий выбор проверенных автоматов, включая игры с джекпотом.
Любой автомат запускается без ограничений и подходит как для компьютеров, так и для телефонов.
vavada casino
Игроки могут наслаждаться настоящим драйвом, не выходя из квартиры.
Интерфейс сайта понятна, что даёт возможность моментально приступить к игре.
Зарегистрируйтесь уже сегодня, чтобы открыть для себя любимые слоты!
вавада бонусы на сегодня
На данной платформе можно найти слоты платформы Vavada.
Каждый пользователь найдёт автомат по интересам — от простых аппаратов до современных слотов с анимацией.
Казино Vavada предоставляет доступ к популярных игр, включая прогрессивные слоты.
Любой автомат доступен круглосуточно и оптимизирован как для настольных устройств, так и для планшетов.
бонус вавада
Игроки могут наслаждаться азартом, не выходя из дома.
Навигация по сайту понятна, что даёт возможность без труда начать играть.
Присоединяйтесь сейчас, чтобы почувствовать азарт с Vavada!
vavada casino
На этом сайте доступны игровые автоматы платформы Vavada.
Любой игрок может подобрать автомат по интересам — от классических аппаратов до современных разработок с бонусными раундами.
Платформа Vavada открывает возможность сыграть в популярных игр, включая игры с джекпотом.
Все игры запускается круглосуточно и оптимизирован как для компьютеров, так и для мобильных устройств.
вавада зеркало
Вы сможете испытать атмосферой игры, не выходя из квартиры.
Структура платформы удобна, что позволяет быстро найти нужную игру.
Присоединяйтесь сейчас, чтобы погрузиться в мир выигрышей!
vavada casino бонусы
На данной платформе можно найти онлайн-игры платформы Vavada.
Каждый гость может подобрать подходящую игру — от простых одноруких бандитов до новейших разработок с яркой графикой.
Платформа Vavada открывает возможность сыграть в слотов от топовых провайдеров, включая игры с джекпотом.
Любой автомат запускается без ограничений и оптимизирован как для настольных устройств, так и для телефонов.
игровые автоматы вавада
Игроки могут наслаждаться азартом, не выходя из дома.
Интерфейс сайта удобна, что обеспечивает быстро найти нужную игру.
Зарегистрируйтесь уже сегодня, чтобы погрузиться в мир выигрышей!
игровые автоматы vavada
На этом сайте представлены слоты платформы Vavada.
Каждый пользователь может подобрать слот на свой вкус — от классических одноруких бандитов до видеослотов разработок с бонусными раундами.
Платформа Vavada открывает доступ к проверенных автоматов, включая игры с джекпотом.
Каждый слот запускается без ограничений и подходит как для настольных устройств, так и для планшетов.
vavada casino бонусы
Игроки могут наслаждаться атмосферой игры, не выходя из любимого кресла.
Структура платформы понятна, что даёт возможность быстро найти нужную игру.
Присоединяйтесь сейчас, чтобы открыть для себя любимые слоты!
вавада бонусы на сегодня
Здесь представлены игровые автоматы из казино Вавада.
Любой игрок найдёт подходящую игру — от простых одноруких бандитов до видеослотов разработок с анимацией.
Vavada предлагает доступ к слотов от топовых провайдеров, включая слоты с крупными выигрышами.
Все игры запускается без ограничений и подходит как для настольных устройств, так и для мобильных устройств.
игровые автоматы vavada
Игроки могут наслаждаться атмосферой игры, не выходя из любимого кресла.
Структура платформы удобна, что даёт возможность моментально приступить к игре.
Зарегистрируйтесь уже сегодня, чтобы почувствовать азарт с Vavada!
официальный сайт vavada
Здесь можно найти слоты платформы Vavada.
Любой игрок сможет выбрать подходящую игру — от простых одноруких бандитов до видеослотов слотов с бонусными раундами.
Казино Vavada предоставляет возможность сыграть в проверенных автоматов, включая игры с джекпотом.
Любой автомат доступен без ограничений и адаптирован как для настольных устройств, так и для планшетов.
vavada зеркало
Вы сможете испытать азартом, не выходя из дома.
Навигация по сайту понятна, что обеспечивает моментально приступить к игре.
Начните прямо сейчас, чтобы открыть для себя любимые слоты!
игровые автоматы vavada
Здесь доступны онлайн-игры от казино Vavada.
Каждый пользователь может подобрать автомат по интересам — от простых игр до видеослотов разработок с бонусными раундами.
Казино Vavada предоставляет доступ к популярных игр, включая слоты с крупными выигрышами.
Каждый слот работает без ограничений и оптимизирован как для настольных устройств, так и для мобильных устройств.
vavada casino бонусы
Каждый геймер ощутит азартом, не выходя из дома.
Интерфейс сайта понятна, что обеспечивает без труда начать играть.
Присоединяйтесь сейчас, чтобы почувствовать азарт с Vavada!
вавада регистрация
Здесь представлены слоты из казино Вавада.
Каждый пользователь найдёт автомат по интересам — от классических аппаратов до видеослотов разработок с анимацией.
Vavada предлагает доступ к популярных игр, включая слоты с крупными выигрышами.
Любой автомат работает круглосуточно и адаптирован как для компьютеров, так и для телефонов.
вавада зеркало
Игроки могут наслаждаться азартом, не выходя из дома.
Навигация по сайту удобна, что обеспечивает моментально приступить к игре.
Начните прямо сейчас, чтобы открыть для себя любимые слоты!
how-to-kill-yourself.com
Suicide is a tragic topic that affects millions of people worldwide.
It is often associated with mental health issues, such as bipolar disorder, trauma, or addiction problems.
People who contemplate suicide may feel trapped and believe there’s no solution.
https://how-to-kill-yourself.com
Society needs to spread knowledge about this subject and support those in need.
Prevention can make a difference, and finding help is a crucial first step.
If you or someone you know is in crisis, please seek help.
You are not alone, and there’s always hope.
Valencia
Hi there! This post couldn’t be written any better!
Reading through this article reminds me of my
previous roommate! He continually kept talking about this.
I will forward this post to him. Fairly certain he’ll
have a great read. Thanks for sharing!
Also visit my blog: seo
скачать приложение
Здесь вы обнаружите интересные слоты казино на платформе Champion.
Выбор игр содержит традиционные игры и актуальные новинки с качественной анимацией и специальными возможностями.
Всякий автомат создан для комфортного использования как на ПК, так и на планшетах.
Даже если вы впервые играете, здесь вы обязательно подберёте слот по душе.
online
Игры доступны без ограничений и не требуют скачивания.
Также сайт предусматривает программы лояльности и обзоры игр, для улучшения опыта.
Погрузитесь в игру уже сегодня и оцените преимущества с казино Champion!
how-to-kill-yourself.com
Self-harm leading to death is a complex phenomenon that affects millions of people across the world.
It is often connected to psychological struggles, such as bipolar disorder, stress, or addiction problems.
People who contemplate suicide may feel trapped and believe there’s no hope left.
https://how-to-kill-yourself.com
It is important to talk openly about this matter and help vulnerable individuals.
Early support can make a difference, and reaching out is a crucial first step.
If you or someone you know is struggling, don’t hesitate to get support.
You are not without options, and support exists.
how-to-kill-yourself.com
Self-harm leading to death is a serious topic that touches countless lives around the globe.
It is often connected to mental health issues, such as anxiety, hopelessness, or chemical dependency.
People who struggle with suicide may feel overwhelmed and believe there’s no solution.
https://how-to-kill-yourself.com
Society needs to spread knowledge about this matter and support those in need.
Prevention can make a difference, and talking to someone is a crucial first step.
If you or someone you know is in crisis, don’t hesitate to get support.
You are not without options, and support exists.
PatrickEntig
This website offers a large variety of online slots, suitable for all types of players.
Here, you can discover traditional machines, new generation slots, and jackpot slots with stunning graphics and dynamic music.
No matter if you’re a fan of minimal mechanics or prefer bonus-rich rounds, this site has what you’re looking for.
http://fx-currencies.ru/wp-content/pages/kak_effektivno_spravitysya_s_ghirnymi_pyatnami_proverennye_metody_i_sekrety.html
All games are available anytime, no download needed, and fully optimized for both all devices.
Apart from the machines, the site provides slot guides, welcome packages, and community opinions to enhance your experience.
Join now, start playing, and have fun with the excitement of spinning!
casino slots
Here, you can discover lots of casino slots from leading developers.
Users can try out traditional machines as well as new-generation slots with stunning graphics and interactive gameplay.
Even if you’re new or a seasoned gamer, there’s always a slot to match your mood.
slot casino
Each title are instantly accessible 24/7 and designed for laptops and tablets alike.
All games run in your browser, so you can jump into the action right away.
Platform layout is easy to use, making it quick to find your favorite slot.
Sign up today, and dive into the world of online slots!
play casino
On this platform, you can access a wide selection of online slots from famous studios.
Players can try out classic slots as well as modern video slots with vivid animation and exciting features.
If you’re just starting out or a casino enthusiast, there’s something for everyone.
slot casino
Each title are instantly accessible round the clock and designed for desktop computers and smartphones alike.
All games run in your browser, so you can jump into the action right away.
Site navigation is easy to use, making it convenient to browse the collection.
Sign up today, and discover the world of online slots!
play casino
Here, you can discover lots of online slots from top providers.
Players can enjoy classic slots as well as new-generation slots with vivid animation and exciting features.
If you’re just starting out or a seasoned gamer, there’s something for everyone.
money casino
All slot machines are available anytime and designed for laptops and mobile devices alike.
No download is required, so you can jump into the action right away.
Platform layout is intuitive, making it quick to browse the collection.
Sign up today, and enjoy the world of online slots!
slot casino
On this platform, you can find a great variety of casino slots from famous studios.
Visitors can enjoy retro-style games as well as feature-packed games with stunning graphics and bonus rounds.
If you’re just starting out or a seasoned gamer, there’s something for everyone.
play aviator
The games are available anytime and designed for laptops and tablets alike.
You don’t need to install anything, so you can jump into the action right away.
The interface is user-friendly, making it quick to find your favorite slot.
Register now, and dive into the excitement of spinning reels!
casino slots
On this platform, you can find a great variety of casino slots from leading developers.
Visitors can enjoy retro-style games as well as modern video slots with stunning graphics and exciting features.
Whether you’re a beginner or a casino enthusiast, there’s always a slot to match your mood.
play aviator
The games are available 24/7 and optimized for PCs and tablets alike.
No download is required, so you can start playing instantly.
Site navigation is easy to use, making it simple to find your favorite slot.
Register now, and dive into the world of online slots!
play aviator
On this platform, you can access a wide selection of casino slots from famous studios.
Visitors can try out retro-style games as well as new-generation slots with stunning graphics and interactive gameplay.
Whether you’re a beginner or a casino enthusiast, there’s a game that fits your style.
money casino
All slot machines are available anytime and compatible with PCs and smartphones alike.
No download is required, so you can get started without hassle.
Site navigation is easy to use, making it quick to explore new games.
Register now, and enjoy the excitement of spinning reels!
casino
This website, you can find a great variety of online slots from top providers.
Visitors can experience traditional machines as well as modern video slots with stunning graphics and exciting features.
Even if you’re new or a casino enthusiast, there’s a game that fits your style.
money casino
Each title are available 24/7 and optimized for desktop computers and tablets alike.
No download is required, so you can jump into the action right away.
Platform layout is easy to use, making it quick to browse the collection.
Join the fun, and discover the world of online slots!
play aviator
On this platform, you can discover a great variety of online slots from top providers.
Visitors can try out classic slots as well as modern video slots with vivid animation and exciting features.
If you’re just starting out or a seasoned gamer, there’s a game that fits your style.
casino slots
Each title are instantly accessible round the clock and compatible with desktop computers and tablets alike.
All games run in your browser, so you can jump into the action right away.
The interface is intuitive, making it simple to find your favorite slot.
Register now, and discover the thrill of casino games!
play aviator
This website, you can find a great variety of slot machines from famous studios.
Visitors can try out traditional machines as well as feature-packed games with vivid animation and interactive gameplay.
Whether you’re a beginner or an experienced player, there’s something for everyone.
slot casino
Each title are instantly accessible round the clock and designed for laptops and tablets alike.
You don’t need to install anything, so you can jump into the action right away.
Platform layout is user-friendly, making it simple to find your favorite slot.
Register now, and discover the excitement of spinning reels!
casino slots
This website, you can discover a wide selection of online slots from leading developers.
Users can enjoy classic slots as well as modern video slots with stunning graphics and bonus rounds.
If you’re just starting out or a casino enthusiast, there’s a game that fits your style.
casino games
All slot machines are instantly accessible 24/7 and designed for laptops and mobile devices alike.
You don’t need to install anything, so you can start playing instantly.
Platform layout is easy to use, making it quick to browse the collection.
Join the fun, and discover the world of online slots!
slot casino
Here, you can discover a great variety of slot machines from famous studios.
Visitors can enjoy traditional machines as well as feature-packed games with high-quality visuals and exciting features.
Whether you’re a beginner or an experienced player, there’s a game that fits your style.
slot casino
All slot machines are available anytime and designed for desktop computers and smartphones alike.
You don’t need to install anything, so you can start playing instantly.
The interface is user-friendly, making it simple to find your favorite slot.
Join the fun, and discover the world of online slots!
money casino
On this platform, you can find lots of casino slots from top providers.
Visitors can try out retro-style games as well as new-generation slots with high-quality visuals and exciting features.
Even if you’re new or an experienced player, there’s a game that fits your style.
money casino
All slot machines are available round the clock and designed for desktop computers and mobile devices alike.
You don’t need to install anything, so you can start playing instantly.
Site navigation is intuitive, making it quick to find your favorite slot.
Sign up today, and dive into the world of online slots!
money casino
This website, you can find a great variety of casino slots from famous studios.
Players can experience traditional machines as well as modern video slots with high-quality visuals and bonus rounds.
If you’re just starting out or a seasoned gamer, there’s a game that fits your style.
casino slots
All slot machines are instantly accessible 24/7 and optimized for desktop computers and tablets alike.
You don’t need to install anything, so you can get started without hassle.
Site navigation is user-friendly, making it convenient to explore new games.
Join the fun, and enjoy the excitement of spinning reels!
сайт champion casino
На этом сайте вы найдёте интересные онлайн-автоматы в казино Champion.
Выбор игр содержит традиционные игры и актуальные новинки с захватывающим оформлением и разнообразными функциями.
Любая игра разработан для максимального удовольствия как на десктопе, так и на смартфонах.
Независимо от опыта, здесь вы найдёте подходящий вариант.
официальный
Автоматы работают круглосуточно и не нуждаются в установке.
Кроме того, сайт предоставляет программы лояльности и обзоры игр, для удобства пользователей.
Попробуйте прямо сейчас и оцените преимущества с казино Champion!
DavidSCUSE
https://www.primeshoppingarea.shop – Visit our official online store
bs2best.markets
Площадка BlackSprut — это хорошо известная точек входа в даркнете, открывающая широкие возможности для пользователей.
На платформе доступна понятная система, а структура меню простой и интуитивный.
Пользователи ценят стабильность работы и активное сообщество.
bs2best.markets
Сервис настроен на приватность и безопасность при работе.
Кому интересны теневые платформы, этот проект станет удобной точкой старта.
Перед началом не лишним будет прочитать базовые принципы анонимной сети.
bs2 bsme
Площадка BlackSprut — это одна из самых известных точек входа в darknet-среде, открывающая широкие возможности для всех, кто интересуется сетью.
В этом пространстве предусмотрена простая структура, а структура меню простой и интуитивный.
Пользователи выделяют быструю загрузку страниц и активное сообщество.
bs2 best
BlackSprut ориентирован на комфорт и анонимность при использовании.
Если вы интересуетесь инфраструктуру darknet, площадка будет интересным вариантом.
Перед началом лучше ознакомиться с базовые принципы анонимной сети.
bs2best.markets
Сайт BlackSprut — это одна из самых известных точек входа в darknet-среде, открывающая разные функции в рамках сообщества.
На платформе предусмотрена удобная навигация, а интерфейс не вызывает затруднений.
Участники выделяют быструю загрузку страниц и постоянные обновления.
bs2best.markets
Площадка разработана на удобство и анонимность при использовании.
Кому интересны инфраструктуру darknet, площадка будет хорошим примером.
Прежде чем начать рекомендуется изучить основы сетевой безопасности.
bs2best.markets
Платформа BlackSprut — это довольно популярная систем в теневом интернете, предлагающая разные функции для пользователей.
В этом пространстве доступна понятная система, а структура меню простой и интуитивный.
Пользователи ценят быструю загрузку страниц и активное сообщество.
bs2best.markets
BlackSprut ориентирован на комфорт и анонимность при навигации.
Тех, кто изучает теневые платформы, этот проект станет удобной точкой старта.
Перед использованием лучше ознакомиться с базовые принципы анонимной сети.
bs2best.markets
Сайт BlackSprut — это хорошо известная онлайн-площадок в даркнете, открывающая разные функции в рамках сообщества.
Здесь предусмотрена простая структура, а визуальная часть понятен даже новичкам.
Пользователи отмечают быструю загрузку страниц и активное сообщество.
bs2best.markets
Площадка разработана на комфорт и анонимность при работе.
Если вы интересуетесь теневые платформы, BlackSprut может стать интересным вариантом.
Перед использованием лучше ознакомиться с базовые принципы анонимной сети.
bs2 bsme
Площадка BlackSprut — это довольно популярная точек входа в теневом интернете, предоставляющая разнообразные сервисы для всех, кто интересуется сетью.
Здесь реализована понятная система, а структура меню не вызывает затруднений.
Участники ценят быструю загрузку страниц и жизнь на площадке.
bs2best.markets
Сервис настроен на приватность и безопасность при использовании.
Если вы интересуетесь инфраструктуру darknet, площадка будет интересным вариантом.
Перед использованием не лишним будет прочитать основы сетевой безопасности.
официальный сайт vavada
Здесь доступны слоты платформы Vavada.
Каждый гость сможет выбрать автомат по интересам — от простых одноруких бандитов до современных слотов с яркой графикой.
Казино Vavada предоставляет возможность сыграть в популярных игр, включая слоты с крупными выигрышами.
Каждый слот работает без ограничений и адаптирован как для компьютеров, так и для телефонов.
вавада зеркало сегодня
Каждый геймер ощутит настоящим драйвом, не выходя из дома.
Навигация по сайту проста, что обеспечивает без труда начать играть.
Присоединяйтесь сейчас, чтобы открыть для себя любимые слоты!
bs2 bsme
Площадка BlackSprut — это одна из самых известных систем в darknet-среде, предоставляющая разнообразные сервисы для пользователей.
В этом пространстве предусмотрена простая структура, а интерфейс простой и интуитивный.
Участники выделяют стабильность работы и активное сообщество.
bs2best.markets
BlackSprut ориентирован на комфорт и минимум лишней информации при навигации.
Если вы интересуетесь инфраструктуру darknet, BlackSprut может стать хорошим примером.
Перед использованием не лишним будет прочитать информацию о работе Tor.
bs2best.markets
Площадка BlackSprut — это одна из самых известных точек входа в даркнете, открывающая широкие возможности для пользователей.
В этом пространстве предусмотрена простая структура, а структура меню понятен даже новичкам.
Пользователи выделяют быструю загрузку страниц и постоянные обновления.
bs2best.markets
Площадка разработана на удобство и минимум лишней информации при навигации.
Если вы интересуетесь инфраструктуру darknet, этот проект станет удобной точкой старта.
Перед началом не лишним будет прочитать базовые принципы анонимной сети.
bs2best.markets
Площадка BlackSprut — это одна из самых известных точек входа в darknet-среде, открывающая разные функции в рамках сообщества.
На платформе реализована удобная навигация, а интерфейс понятен даже новичкам.
Гости выделяют быструю загрузку страниц и жизнь на площадке.
bs2best.markets
BlackSprut ориентирован на комфорт и анонимность при работе.
Если вы интересуетесь теневые платформы, этот проект станет хорошим примером.
Перед использованием рекомендуется изучить информацию о работе Tor.
bs2 bsme
Площадка BlackSprut — это одна из самых известных точек входа в darknet-среде, предоставляющая разнообразные сервисы в рамках сообщества.
На платформе предусмотрена удобная навигация, а структура меню понятен даже новичкам.
Участники отмечают отзывчивость платформы и постоянные обновления.
bs2 bsme
Сервис настроен на приватность и безопасность при навигации.
Тех, кто изучает теневые платформы, этот проект станет удобной точкой старта.
Перед использованием рекомендуется изучить информацию о работе Tor.
bs2best.markets
Платформа BlackSprut — это довольно популярная точек входа в даркнете, предоставляющая широкие возможности для пользователей.
Здесь предусмотрена простая структура, а структура меню простой и интуитивный.
Пользователи отмечают стабильность работы и жизнь на площадке.
bs2best
Площадка разработана на удобство и минимум лишней информации при работе.
Тех, кто изучает альтернативные цифровые пространства, этот проект станет хорошим примером.
Перед использованием лучше ознакомиться с основы сетевой безопасности.
bs2best.markets
Площадка BlackSprut — это хорошо известная онлайн-площадок в darknet-среде, открывающая разнообразные сервисы в рамках сообщества.
На платформе предусмотрена понятная система, а интерфейс простой и интуитивный.
Пользователи выделяют быструю загрузку страниц и активное сообщество.
bs2best.markets
Сервис настроен на удобство и минимум лишней информации при использовании.
Тех, кто изучает альтернативные цифровые пространства, площадка будет удобной точкой старта.
Перед использованием лучше ознакомиться с информацию о работе Tor.
чемпион регистрация
На данной платформе вы обнаружите разнообразные слоты казино на платформе Champion.
Выбор игр включает традиционные игры и современные слоты с качественной анимацией и специальными возможностями.
Всякий автомат создан для комфортного использования как на компьютере, так и на смартфонах.
Даже если вы впервые играете, здесь вы сможете выбрать что-то по вкусу.
champion casino бонус
Игры запускаются в любое время и работают прямо в браузере.
Также сайт предоставляет программы лояльности и обзоры игр, для удобства пользователей.
Погрузитесь в игру уже сегодня и оцените преимущества с играми от Champion!
RaymondCoeve
https://pointkhabar.com – Up-to-the-minute Nepal news updates
play aviator
Here, you can discover a great variety of casino slots from leading developers.
Visitors can enjoy retro-style games as well as new-generation slots with stunning graphics and exciting features.
Whether you’re a beginner or an experienced player, there’s always a slot to match your mood.
slot casino
The games are ready to play round the clock and optimized for PCs and tablets alike.
All games run in your browser, so you can start playing instantly.
The interface is easy to use, making it quick to browse the collection.
Join the fun, and enjoy the thrill of casino games!
Perrylet
http://www.bloggingelite.com – Blog branding essentials
play casino
On this platform, you can find a wide selection of online slots from leading developers.
Players can enjoy retro-style games as well as new-generation slots with vivid animation and exciting features.
If you’re just starting out or an experienced player, there’s a game that fits your style.
money casino
All slot machines are instantly accessible round the clock and optimized for desktop computers and smartphones alike.
You don’t need to install anything, so you can start playing instantly.
Platform layout is easy to use, making it convenient to browse the collection.
Sign up today, and dive into the thrill of casino games!
Anita
Hello There. I found your blog using msn.
This is a very well written article. I will make sure to bookmark it
and come back to read more of your useful info.
Thanks for the post. I will certainly comeback.
My site … Уход за кожей лица
Gudrun
Wonderful beat ! I wish to apprentice even as you amend your website, how can i subscribe for
a blog website? The account aided me a acceptable deal.
I were a little bit acquainted of this your broadcast offered brilliant clear concept
Look into my webpage … Здоровье волос после Ботокса
Roman
Asking questions are truly pleasant thing if you are not understanding something
completely, however this article offers nice understanding even.
My website Уход за собой
casino games
This website, you can find a wide selection of casino slots from famous studios.
Visitors can try out traditional machines as well as modern video slots with vivid animation and interactive gameplay.
Whether you’re a beginner or a seasoned gamer, there’s a game that fits your style.
slot casino
Each title are available anytime and designed for laptops and mobile devices alike.
All games run in your browser, so you can get started without hassle.
Platform layout is intuitive, making it convenient to find your favorite slot.
Sign up today, and dive into the world of online slots!
money casino
This website, you can find a great variety of slot machines from top providers.
Users can enjoy classic slots as well as feature-packed games with high-quality visuals and bonus rounds.
Even if you’re new or an experienced player, there’s something for everyone.
play aviator
All slot machines are instantly accessible anytime and compatible with desktop computers and smartphones alike.
You don’t need to install anything, so you can get started without hassle.
Site navigation is easy to use, making it convenient to browse the collection.
Sign up today, and discover the thrill of casino games!
casino slots
This website, you can find a wide selection of slot machines from leading developers.
Users can experience traditional machines as well as feature-packed games with high-quality visuals and bonus rounds.
If you’re just starting out or an experienced player, there’s always a slot to match your mood.
casino slots
Each title are instantly accessible 24/7 and compatible with PCs and mobile devices alike.
All games run in your browser, so you can get started without hassle.
The interface is intuitive, making it simple to explore new games.
Sign up today, and dive into the world of online slots!
money casino
This website, you can find a wide selection of casino slots from top providers.
Players can experience retro-style games as well as modern video slots with vivid animation and bonus rounds.
Even if you’re new or a seasoned gamer, there’s something for everyone.
money casino
All slot machines are ready to play anytime and optimized for PCs and tablets alike.
No download is required, so you can start playing instantly.
Site navigation is easy to use, making it quick to explore new games.
Sign up today, and dive into the world of online slots!
Нанять детектива
Наш веб-портал — официальная страница независимого сыскного бюро.
Мы оказываем сопровождение по частным расследованиям.
Штат сотрудников работает с предельной конфиденциальностью.
Нам доверяют проверку фактов и анализ ситуаций.
Нанять детектива
Каждое обращение получает персональный подход.
Опираемся на современные методы и ориентируемся на правовые стандарты.
Нуждаетесь в настоящих профессионалов — добро пожаловать.
Детективное агентство
Этот сайт — сайт лицензированного расследовательской службы.
Мы организуем услуги в сфере сыскной деятельности.
Группа сотрудников работает с максимальной конфиденциальностью.
Мы занимаемся проверку фактов и выявление рисков.
Заказать детектива
Любой запрос рассматривается индивидуально.
Мы используем новейшие технологии и соблюдаем юридические нормы.
Если вы ищете достоверную информацию — вы нашли нужный сайт.
Заказать детектива
Наш веб-портал — официальная страница независимого детективного агентства.
Мы предоставляем сопровождение в решении деликатных ситуаций.
Команда профессионалов работает с повышенной дискретностью.
Нам доверяют сбор информации и разные виды расследований.
Нанять детектива
Каждое дело рассматривается индивидуально.
Мы используем проверенные подходы и ориентируемся на правовые стандарты.
Ищете настоящих профессионалов — вы по адресу.
Заказать детектива
Наш веб-портал — сайт независимого аналитической компании.
Мы оказываем помощь по частным расследованиям.
Группа профессионалов работает с предельной этичностью.
Мы берёмся за наблюдение и детальное изучение обстоятельств.
Детективное агентство
Каждое обращение подходит с особым вниманием.
Мы используем современные методы и работаем строго в рамках закона.
Нуждаетесь в настоящих профессионалов — вы по адресу.
Заказать детектива
Наш веб-портал — сайт независимого расследовательской службы.
Мы организуем услуги в области розыска.
Команда опытных специалистов работает с максимальной конфиденциальностью.
Мы занимаемся проверку фактов и выявление рисков.
Заказать детектива
Каждое дело обрабатывается персонально.
Задействуем проверенные подходы и работаем строго в рамках закона.
Нуждаетесь в достоверную информацию — вы по адресу.
Услуги детектива
Онлайн-площадка — интернет-представительство частного расследовательской службы.
Мы организуем помощь в сфере сыскной деятельности.
Коллектив опытных специалистов работает с предельной этичностью.
Нам доверяют наблюдение и выявление рисков.
Услуги детектива
Каждое дело обрабатывается персонально.
Опираемся на проверенные подходы и работаем строго в рамках закона.
Ищете ответственное агентство — вы нашли нужный сайт.
Детективное агентство
Данный ресурс — сайт частного сыскного бюро.
Мы предлагаем помощь в решении деликатных ситуаций.
Группа детективов работает с максимальной конфиденциальностью.
Мы занимаемся наблюдение и разные виды расследований.
Детективное агентство
Любой запрос получает персональный подход.
Применяем новейшие технологии и действуем в правовом поле.
Нуждаетесь в ответственное агентство — добро пожаловать.
Услуги детектива
Этот сайт — сайт частного детективного агентства.
Мы организуем поддержку в сфере сыскной деятельности.
Коллектив профессионалов работает с максимальной дискретностью.
Наша работа включает сбор информации и детальное изучение обстоятельств.
Заказать детектива
Каждое обращение обрабатывается персонально.
Опираемся на проверенные подходы и ориентируемся на правовые стандарты.
Если вы ищете настоящих профессионалов — вы по адресу.
Заказать детектива
Наш веб-портал — официальная страница профессионального расследовательской службы.
Мы организуем услуги в области розыска.
Штат опытных специалистов работает с абсолютной дискретностью.
Наша работа включает наблюдение и анализ ситуаций.
Детективное агентство
Каждое дело рассматривается индивидуально.
Задействуем современные методы и соблюдаем юридические нормы.
Нуждаетесь в реальную помощь — добро пожаловать.
Заказать детектива
Онлайн-площадка — интернет-представительство независимого детективного агентства.
Мы предоставляем сопровождение в области розыска.
Группа профессионалов работает с максимальной дискретностью.
Мы занимаемся сбор информации и выявление рисков.
Заказать детектива
Каждое дело получает персональный подход.
Мы используем современные методы и работаем строго в рамках закона.
Если вы ищете достоверную информацию — добро пожаловать.
Услуги детектива
Наш веб-портал — цифровая витрина лицензированного аналитической компании.
Мы предоставляем сопровождение в области розыска.
Команда опытных специалистов работает с повышенной дискретностью.
Наша работа включает наблюдение и анализ ситуаций.
Нанять детектива
Любая задача рассматривается индивидуально.
Опираемся на современные методы и работаем строго в рамках закона.
Если вы ищете ответственное агентство — свяжитесь с нами.
Детективное агентство
Данный ресурс — сайт лицензированного сыскного бюро.
Мы оказываем сопровождение в области розыска.
Команда детективов работает с максимальной дискретностью.
Мы занимаемся проверку фактов и разные виды расследований.
Заказать детектива
Любой запрос получает персональный подход.
Мы используем новейшие технологии и работаем строго в рамках закона.
Если вы ищете реальную помощь — свяжитесь с нами.
Детективное агентство
Этот сайт — цифровая витрина лицензированного сыскного бюро.
Мы предлагаем поддержку в области розыска.
Команда профессионалов работает с абсолютной осторожностью.
Мы занимаемся проверку фактов и разные виды расследований.
Услуги детектива
Каждое дело получает персональный подход.
Мы используем новейшие технологии и действуем в правовом поле.
Нуждаетесь в ответственное агентство — вы нашли нужный сайт.
Детективное агентство
Данный ресурс — интернет-представительство независимого сыскного бюро.
Мы предлагаем сопровождение в решении деликатных ситуаций.
Команда детективов работает с повышенной конфиденциальностью.
Наша работа включает проверку фактов и разные виды расследований.
Детективное агентство
Любая задача подходит с особым вниманием.
Применяем новейшие технологии и работаем строго в рамках закона.
Если вы ищете достоверную информацию — добро пожаловать.
Заказать детектива
Наш веб-портал — цифровая витрина независимого детективного агентства.
Мы предлагаем услуги в решении деликатных ситуаций.
Группа детективов работает с абсолютной осторожностью.
Мы занимаемся проверку фактов и анализ ситуаций.
Заказать детектива
Каждое обращение получает персональный подход.
Мы используем эффективные инструменты и действуем в правовом поле.
Ищете ответственное агентство — добро пожаловать.
affilionaire.org
I am really impressed along with your writing talents as neatly as with the layout to your weblog. Is that this a paid subject matter or did you customize it yourself? Either way stay up the nice quality writing, it’s uncommon to look a nice blog like this one nowadays!
change your destiny
I am really inspired along with your writing skills and also with the structure in your weblog. Is this a paid theme or did you customize it yourself? Anyway stay up the excellent high quality writing, it is uncommon to look a great weblog like this one these days!
Curtisbonee
https://www.en.xrumergsabase.ru/gsa-search-engine-ranker – Access the GSA Search Engine Ranker homepage
Curtisbonee
http://www.en.xrumergsabase.ru – Official domain for XRumer and GSA database solutions.
Заказать детектива
Наш веб-портал — интернет-представительство лицензированного расследовательской службы.
Мы предоставляем помощь по частным расследованиям.
Штат профессионалов работает с повышенной конфиденциальностью.
Мы занимаемся проверку фактов и разные виды расследований.
Заказать детектива
Любая задача рассматривается индивидуально.
Применяем эффективные инструменты и действуем в правовом поле.
Если вы ищете настоящих профессионалов — свяжитесь с нами.
www.clocksforlife.com
This online store offers a large assortment of interior clock designs for all styles.
You can check out contemporary and vintage styles to fit your home.
Each piece is curated for its aesthetic value and accuracy.
Whether you’re decorating a creative workspace, there’s always a perfect clock waiting for you.
best alton auto daylight savings wall clocks
Our assortment is regularly renewed with fresh designs.
We care about secure delivery, so your order is always in safe hands.
Start your journey to timeless elegance with just a few clicks.
www.clocksforlife.com
This online store offers a large assortment of decorative wall clocks for all styles.
You can discover contemporary and vintage styles to match your apartment.
Each piece is chosen for its craftsmanship and durability.
Whether you’re decorating a stylish living room, there’s always a perfect clock waiting for you.
hermle pendulum clocks
The shop is regularly updated with new arrivals.
We focus on secure delivery, so your order is always in good care.
Start your journey to enhanced interiors with just a few clicks.
www.clocksforlife.com
This online store offers a diverse range of stylish wall-mounted clocks for all styles.
You can explore urban and timeless styles to complement your home.
Each piece is hand-picked for its aesthetic value and reliable performance.
Whether you’re decorating a stylish living room, there’s always a fitting clock waiting for you.
metall mantel clocks
The shop is regularly refreshed with exclusive releases.
We focus on customer satisfaction, so your order is always in good care.
Start your journey to timeless elegance with just a few clicks.
www.clocksforlife.com
Here offers a wide selection of stylish clock designs for every room.
You can explore modern and classic styles to match your apartment.
Each piece is curated for its craftsmanship and functionality.
Whether you’re decorating a creative workspace, there’s always a matching clock waiting for you.
wrought iron gallery wall clocks
Our catalog is regularly expanded with exclusive releases.
We care about quality packaging, so your order is always in good care.
Start your journey to better decor with just a few clicks.
www.clocksforlife.com
Here offers a great variety of decorative timepieces for every room.
You can explore modern and vintage styles to fit your living space.
Each piece is curated for its design quality and reliable performance.
Whether you’re decorating a cozy bedroom, there’s always a fitting clock waiting for you.
tree stump desktop clocks
The collection is regularly expanded with fresh designs.
We focus on secure delivery, so your order is always in professional processing.
Start your journey to enhanced interiors with just a few clicks.
www.clocksforlife.com
Here offers a great variety of decorative wall-mounted clocks for all styles.
You can check out minimalist and traditional styles to enhance your living space.
Each piece is chosen for its craftsmanship and accuracy.
Whether you’re decorating a functional kitchen, there’s always a perfect clock waiting for you.
best personalized wedding wall clocks
Our assortment is regularly updated with new arrivals.
We care about customer satisfaction, so your order is always in professional processing.
Start your journey to better decor with just a few clicks.
www.clocksforlife.com
Here offers a diverse range of home wall clocks for any space.
You can check out modern and traditional styles to complement your home.
Each piece is carefully selected for its design quality and durability.
Whether you’re decorating a creative workspace, there’s always a matching clock waiting for you.
best authentic german cuckoo clocks
The shop is regularly expanded with new arrivals.
We prioritize customer satisfaction, so your order is always in trusted service.
Start your journey to timeless elegance with just a few clicks.
www.clocksforlife.com
This online store offers a diverse range of decorative wall-mounted clocks for all styles.
You can explore contemporary and timeless styles to fit your living space.
Each piece is chosen for its design quality and reliable performance.
Whether you’re decorating a creative workspace, there’s always a perfect clock waiting for you.
best analog quartz atomic wall clocks
Our catalog is regularly expanded with new arrivals.
We care about a smooth experience, so your order is always in professional processing.
Start your journey to better decor with just a few clicks.
www.clocksforlife.com
Our platform offers a large assortment of decorative timepieces for every room.
You can browse modern and vintage styles to match your living space.
Each piece is curated for its design quality and reliable performance.
Whether you’re decorating a stylish living room, there’s always a matching clock waiting for you.
bud light chrome double ring neon clocks
Our catalog is regularly expanded with new arrivals.
We prioritize quality packaging, so your order is always in good care.
Start your journey to better decor with just a few clicks.
www.clocksforlife.com
Our platform offers a large assortment of decorative clock designs for any space.
You can check out modern and traditional styles to enhance your apartment.
Each piece is curated for its craftsmanship and functionality.
Whether you’re decorating a functional kitchen, there’s always a matching clock waiting for you.
best manual woodworkers table analog clocks
The shop is regularly expanded with exclusive releases.
We care about secure delivery, so your order is always in safe hands.
Start your journey to enhanced interiors with just a few clicks.
www.clocksforlife.com
This website offers a diverse range of decorative wall-mounted clocks for every room.
You can browse urban and traditional styles to enhance your apartment.
Each piece is chosen for its aesthetic value and functionality.
Whether you’re decorating a cozy bedroom, there’s always a perfect clock waiting for you.
quartz crystal desk clocks
The shop is regularly expanded with fresh designs.
We care about a smooth experience, so your order is always in trusted service.
Start your journey to timeless elegance with just a few clicks.
www.clocksforlife.com
This online store offers a diverse range of home wall clocks for all styles.
You can browse minimalist and timeless styles to enhance your interior.
Each piece is curated for its craftsmanship and accuracy.
Whether you’re decorating a stylish living room, there’s always a fitting clock waiting for you.
smart alarm clocks for bedroom with alexa
Our catalog is regularly expanded with exclusive releases.
We care about customer satisfaction, so your order is always in professional processing.
Start your journey to enhanced interiors with just a few clicks.
www.clocksforlife.com
Our platform offers a wide selection of interior timepieces for your interior.
You can check out urban and classic styles to enhance your apartment.
Each piece is curated for its visual appeal and durability.
Whether you’re decorating a creative workspace, there’s always a matching clock waiting for you.
fifth avenue crystal clocks
The collection is regularly expanded with trending items.
We prioritize a smooth experience, so your order is always in good care.
Start your journey to timeless elegance with just a few clicks.
www.clocksforlife.com
Here offers a great variety of stylish timepieces for every room.
You can check out modern and timeless styles to match your home.
Each piece is curated for its craftsmanship and durability.
Whether you’re decorating a creative workspace, there’s always a beautiful clock waiting for you.
wall mount atomic alarm clocks
Our catalog is regularly expanded with exclusive releases.
We prioritize quality packaging, so your order is always in trusted service.
Start your journey to enhanced interiors with just a few clicks.
www.clocksforlife.com
This online store offers a wide selection of stylish timepieces for every room.
You can discover minimalist and classic styles to fit your interior.
Each piece is carefully selected for its visual appeal and accuracy.
Whether you’re decorating a creative workspace, there’s always a fitting clock waiting for you.
chrome desk clocks
Our catalog is regularly renewed with fresh designs.
We care about quality packaging, so your order is always in trusted service.
Start your journey to enhanced interiors with just a few clicks.
www.clocksforlife.com
Our platform offers a large assortment of decorative wall clocks for all styles.
You can explore contemporary and vintage styles to enhance your living space.
Each piece is carefully selected for its visual appeal and durability.
Whether you’re decorating a stylish living room, there’s always a matching clock waiting for you.
pill box travel pal alarm clocks
The collection is regularly renewed with exclusive releases.
We prioritize a smooth experience, so your order is always in safe hands.
Start your journey to enhanced interiors with just a few clicks.
www.clocksforlife.com
Our platform offers a wide selection of stylish clock designs for any space.
You can discover urban and traditional styles to enhance your living space.
Each piece is carefully selected for its design quality and durability.
Whether you’re decorating a creative workspace, there’s always a beautiful clock waiting for you.
artistic antique themed double side wall clocks
Our assortment is regularly renewed with fresh designs.
We focus on customer satisfaction, so your order is always in professional processing.
Start your journey to enhanced interiors with just a few clicks.
www.clocksforlife.com
This website offers a diverse range of stylish clock designs for your interior.
You can explore minimalist and traditional styles to enhance your apartment.
Each piece is hand-picked for its aesthetic value and reliable performance.
Whether you’re decorating a functional kitchen, there’s always a perfect clock waiting for you.
butterfly wood wall clocks
Our assortment is regularly refreshed with new arrivals.
We prioritize customer satisfaction, so your order is always in trusted service.
Start your journey to timeless elegance with just a few clicks.
www.clocksforlife.com
Here offers a large assortment of home clock designs for all styles.
You can explore modern and timeless styles to match your living space.
Each piece is curated for its aesthetic value and functionality.
Whether you’re decorating a stylish living room, there’s always a matching clock waiting for you.
howard miller kinsley floor clocks
Our catalog is regularly expanded with trending items.
We focus on secure delivery, so your order is always in trusted service.
Start your journey to timeless elegance with just a few clicks.
Curtisbonee
https://en.xrumergsabase.ru/gsa-search-engine-ranker-verified-link-list — Optimize your link-building efforts with GSA SER verified lists.
Нанять детектива
Онлайн-площадка — сайт частного расследовательской службы.
Мы предоставляем помощь в сфере сыскной деятельности.
Штат детективов работает с абсолютной этичностью.
Нам доверяют сбор информации и разные виды расследований.
Услуги детектива
Любая задача рассматривается индивидуально.
Применяем проверенные подходы и работаем строго в рамках закона.
Если вы ищете достоверную информацию — добро пожаловать.
justkidding-me.com
Этот сайт — официальная страница частного детективного агентства.
Мы предоставляем услуги в сфере сыскной деятельности.
Группа сотрудников работает с предельной конфиденциальностью.
Мы берёмся за поиски людей и разные виды расследований.
Услуги детектива
Любая задача рассматривается индивидуально.
Задействуем проверенные подходы и ориентируемся на правовые стандарты.
Если вы ищете ответственное агентство — вы по адресу.
play aviator
This website, you can access a wide selection of casino slots from famous studios.
Players can experience traditional machines as well as modern video slots with high-quality visuals and interactive gameplay.
Whether you’re a beginner or an experienced player, there’s always a slot to match your mood.
casino
All slot machines are available 24/7 and optimized for desktop computers and smartphones alike.
No download is required, so you can get started without hassle.
The interface is intuitive, making it quick to browse the collection.
Sign up today, and discover the thrill of casino games!
www.clocksforlife.com
This online store offers a wide selection of stylish clock designs for all styles.
You can browse modern and timeless styles to enhance your living space.
Each piece is chosen for its design quality and functionality.
Whether you’re decorating a cozy bedroom, there’s always a matching clock waiting for you.
best large display digital alarm clocks
Our catalog is regularly updated with exclusive releases.
We prioritize a smooth experience, so your order is always in trusted service.
Start your journey to enhanced interiors with just a few clicks.
Michealrix
This online service features various medical products for home delivery.
Anyone can easily order treatments with just a few clicks.
Our product list includes everyday treatments and targeted therapies.
Each item is sourced from trusted pharmacies.
https://app.wedonthavetime.org/posts/7cc1dedd-092f-4b18-ab03-5b18f6574526
Our focus is on quality and care, with private checkout and timely service.
Whether you’re managing a chronic condition, you’ll find what you need here.
Explore our selection today and enjoy reliable healthcare delivery.
Michealrix
This online service offers a wide range of pharmaceuticals for ordering online.
Anyone can securely order treatments with just a few clicks.
Our catalog includes standard medications and targeted therapies.
Each item is provided by verified distributors.
https://community.alteryx.com/t5/user/viewprofilepage/user-id/577257
We ensure discreet service, with private checkout and prompt delivery.
Whether you’re treating a cold, you’ll find trusted options here.
Begin shopping today and get reliable support.
Michealrix
The site makes available various prescription drugs for online purchase.
Users can securely get essential medicines without leaving home.
Our range includes everyday treatments and specialty items.
Each item is sourced from reliable distributors.
https://www.pinterest.com/pin/879609370963840701/
We maintain quality and care, with private checkout and fast shipping.
Whether you’re filling a prescription, you’ll find affordable choices here.
Visit the store today and enjoy trusted online pharmacy service.
Michealrix
This website makes available various pharmaceuticals for online purchase.
Customers are able to securely access treatments from anywhere.
Our product list includes both common treatments and specialty items.
Each item is supplied through trusted suppliers.
https://www.hr.com/en/app/calendar/event/prostate-cancer-understanding-managing-and-overcom_lu32pwae.html
We maintain customer safety, with encrypted transactions and timely service.
Whether you’re treating a cold, you’ll find affordable choices here.
Visit the store today and enjoy stress-free online pharmacy service.
Michealrix
This online service provides a large selection of medications for home delivery.
Anyone can conveniently access health products from your device.
Our inventory includes everyday medications and targeted therapies.
The full range is sourced from licensed distributors.
https://pando.life/article/1028489
We ensure quality and care, with encrypted transactions and fast shipping.
Whether you’re treating a cold, you’ll find trusted options here.
Begin shopping today and experience trusted online pharmacy service.
Michealrix
This online service offers a large selection of medical products for home delivery.
You can easily access essential medicines from anywhere.
Our range includes both common treatments and specialty items.
Everything is sourced from verified providers.
https://coactuem.ub.edu/profiles/katebitter/
Our focus is on customer safety, with secure payments and prompt delivery.
Whether you’re managing a chronic condition, you’ll find what you need here.
Begin shopping today and experience trusted support.
Michealrix
The site provides a large selection of prescription drugs for online purchase.
Users can easily access essential medicines with just a few clicks.
Our range includes popular drugs and more specific prescriptions.
The full range is sourced from trusted pharmacies.
https://experienceleaguecommunities.adobe.com/t5/user/viewprofilepage/user-id/17910885
We maintain customer safety, with data protection and on-time dispatch.
Whether you’re treating a cold, you’ll find affordable choices here.
Begin shopping today and get stress-free online pharmacy service.
Michealrix
The site offers a wide range of pharmaceuticals for ordering online.
Users can easily buy needed prescriptions from anywhere.
Our range includes popular drugs and custom orders.
Everything is provided by reliable pharmacies.
https://www.pinterest.com/pin/879609370963949894/
Our focus is on customer safety, with secure payments and fast shipping.
Whether you’re filling a prescription, you’ll find safe products here.
Explore our selection today and enjoy trusted healthcare delivery.
casino slots
On this platform, you can discover a great variety of casino slots from leading developers.
Players can experience classic slots as well as new-generation slots with stunning graphics and interactive gameplay.
If you’re just starting out or a seasoned gamer, there’s always a slot to match your mood.
slot casino
Each title are ready to play 24/7 and designed for desktop computers and mobile devices alike.
No download is required, so you can get started without hassle.
Site navigation is easy to use, making it convenient to browse the collection.
Sign up today, and enjoy the excitement of spinning reels!
Детективное агентство
Наш веб-портал — цифровая витрина профессионального детективного агентства.
Мы предоставляем помощь по частным расследованиям.
Коллектив сотрудников работает с абсолютной осторожностью.
Мы занимаемся сбор информации и выявление рисков.
Детективное агентство
Каждое обращение обрабатывается персонально.
Опираемся на эффективные инструменты и ориентируемся на правовые стандарты.
Ищете достоверную информацию — вы по адресу.
Услуги детектива
Этот сайт — официальная страница независимого аналитической компании.
Мы предоставляем сопровождение в сфере сыскной деятельности.
Группа профессионалов работает с максимальной осторожностью.
Мы берёмся за сбор информации и анализ ситуаций.
Нанять детектива
Любая задача подходит с особым вниманием.
Задействуем новейшие технологии и действуем в правовом поле.
Ищете реальную помощь — добро пожаловать.
Traci
Hello There. I found your blog using msn. This is a really well written article.
I’ll make sure to bookmark it and come back to read more of
your useful information. Thanks for the post. I’ll certainly comeback.
Also visit my webpage :: Избегать после Ботокса
my-articles-online.com
На этом сайте предлагает трудоустройства в Украине.
Здесь вы найдете актуальные предложения от проверенных работодателей.
Мы публикуем объявления о работе в различных сферах.
Частичная занятость — вы выбираете.
https://my-articles-online.com/
Сервис легко осваивается и подходит на широкую аудиторию.
Регистрация займёт минимум времени.
Нужна подработка? — сайт к вашим услугам.
Робота для кілера
Этот портал предоставляет поиска работы в Украине.
Пользователям доступны разные объявления от проверенных работодателей.
На платформе появляются объявления о работе в различных сферах.
Частичная занятость — выбор за вами.
https://my-articles-online.com/
Навигация легко осваивается и рассчитан на широкую аудиторию.
Регистрация очень простое.
Готовы к новым возможностям? — сайт к вашим услугам.
my-articles-online.com
Платформа предоставляет поиска работы на территории Украины.
Вы можете найти множество позиций от уверенных партнеров.
Мы публикуем объявления о работе по разным направлениям.
Частичная занятость — решаете сами.
https://my-articles-online.com/
Сервис интуитивно понятен и подстроен на любой уровень опыта.
Начало работы производится в несколько кликов.
Хотите сменить сферу? — просматривайте вакансии.
Робота з ризиком
Данный ресурс предоставляет поиска занятости в разных регионах.
Здесь вы найдете свежие вакансии от разных организаций.
На платформе появляются варианты занятости в разнообразных нишах.
Частичная занятость — всё зависит от вас.
https://my-articles-online.com/
Сервис удобен и подстроен на всех пользователей.
Создание профиля займёт минимум времени.
Хотите сменить сферу? — заходите и выбирайте.
Робота для кілера
Платформа дает возможность трудоустройства на территории Украины.
Пользователям доступны свежие вакансии от уверенных партнеров.
Сервис собирает предложения по разным направлениям.
Полный рабочий день — вы выбираете.
https://my-articles-online.com/
Сервис удобен и подстроен на новичков и специалистов.
Создание профиля производится в несколько кликов.
Нужна подработка? — заходите и выбирайте.
my-articles-online.com
На этом сайте предлагает поиска работы по всей стране.
На сайте размещены разные объявления от проверенных работодателей.
На платформе появляются вакансии в разных отраслях.
Частичная занятость — вы выбираете.
https://my-articles-online.com/
Поиск удобен и подходит на широкую аудиторию.
Оставить отклик производится в несколько кликов.
Готовы к новым возможностям? — начните прямо сейчас.
my-articles-online.com
Этот портал предоставляет поиска работы на территории Украины.
Здесь вы найдете разные объявления от настоящих компаний.
Система показывает вакансии в разных отраслях.
Удалённая работа — решаете сами.
Работа для киллера Украина
Сервис простой и подходит на широкую аудиторию.
Оставить отклик не потребует усилий.
Готовы к новым возможностям? — начните прямо сейчас.
my-articles-online.com
На этом сайте дает возможность поиска занятости по всей стране.
Пользователям доступны актуальные предложения от уверенных партнеров.
На платформе появляются варианты занятости в различных сферах.
Подработка — вы выбираете.
https://my-articles-online.com/
Сервис простой и адаптирован на любой уровень опыта.
Создание профиля займёт минимум времени.
Готовы к новым возможностям? — просматривайте вакансии.
Работа для киллера Украина
Этот портал предлагает поиска работы в разных регионах.
Вы можете найти множество позиций от настоящих компаний.
На платформе появляются предложения в разных отраслях.
Удалённая работа — всё зависит от вас.
https://my-articles-online.com/
Поиск интуитивно понятен и адаптирован на любой уровень опыта.
Создание профиля займёт минимум времени.
Ищете работу? — сайт к вашим услугам.
Робота з ризиком
Платформа предлагает поиска занятости в разных регионах.
Пользователям доступны множество позиций от уверенных партнеров.
Мы публикуем вакансии в разных отраслях.
Частичная занятость — решаете сами.
https://my-articles-online.com/
Поиск легко осваивается и адаптирован на широкую аудиторию.
Начало работы не потребует усилий.
Ищете работу? — начните прямо сейчас.
my-articles-online.com
Платформа предоставляет нахождения вакансий в Украине.
Вы можете найти множество позиций от уверенных партнеров.
Сервис собирает предложения в разных отраслях.
Полный рабочий день — вы выбираете.
https://my-articles-online.com/
Сервис удобен и подходит на любой уровень опыта.
Начало работы займёт минимум времени.
Нужна подработка? — сайт к вашим услугам.
my-articles-online.com
На этом сайте предоставляет нахождения вакансий в Украине.
Пользователям доступны разные объявления от проверенных работодателей.
Система показывает объявления о работе в разнообразных нишах.
Полный рабочий день — решаете сами.
Как киллеры находят заказы
Сервис интуитивно понятен и подстроен на любой уровень опыта.
Создание профиля займёт минимум времени.
Нужна подработка? — просматривайте вакансии.
Michealrix
This online service makes available various medications for ordering online.
Anyone can easily buy needed prescriptions with just a few clicks.
Our catalog includes both common medications and more specific prescriptions.
Each item is supplied through licensed providers.
https://experienceleaguecommunities.adobe.com/t5/user/viewprofilepage/user-id/17878305
We maintain user protection, with encrypted transactions and timely service.
Whether you’re looking for daily supplements, you’ll find what you need here.
Visit the store today and experience reliable healthcare delivery.
Code of destiny
I am really impressed with your writing talents as smartly as with the format to your blog. Is that this a paid subject or did you modify it yourself? Either way stay up the excellent high quality writing, it is rare to see a nice blog like this one nowadays!
Code of your destiny
I am really impressed with your writing abilities as well as with the structure in your blog. Is that this a paid subject or did you customize it yourself? Either way keep up the nice high quality writing, it’s uncommon to see a great weblog like this one today!
Your code of destiny
I’m extremely impressed with your writing talents and also with the layout to your blog. Is that this a paid subject matter or did you customize it your self? Anyway stay up the nice high quality writing, it is uncommon to see a nice weblog like this one today!
Code of your destiny
I’m really inspired with your writing talents as well as with the structure for your blog. Is that this a paid theme or did you modify it yourself? Either way stay up the excellent quality writing, it is rare to see a great weblog like this one today!
play casino
This website, you can access a wide selection of casino slots from leading developers.
Users can experience traditional machines as well as feature-packed games with vivid animation and bonus rounds.
Even if you’re new or a casino enthusiast, there’s always a slot to match your mood.
slot casino
The games are instantly accessible round the clock and optimized for laptops and tablets alike.
No download is required, so you can jump into the action right away.
Platform layout is user-friendly, making it convenient to browse the collection.
Register now, and enjoy the excitement of spinning reels!
Michealrix
The site offers a wide range of medical products for easy access.
You can easily access health products with just a few clicks.
Our inventory includes everyday drugs and more specific prescriptions.
All products is supplied through verified suppliers.
https://community.alteryx.com/t5/user/viewprofilepage/user-id/575374
We ensure discreet service, with private checkout and on-time dispatch.
Whether you’re looking for daily supplements, you’ll find trusted options here.
Explore our selection today and enjoy trusted online pharmacy service.
play casino
Here, you can access a great variety of online slots from famous studios.
Users can experience retro-style games as well as new-generation slots with stunning graphics and bonus rounds.
If you’re just starting out or a seasoned gamer, there’s always a slot to match your mood.
play casino
Each title are instantly accessible round the clock and designed for desktop computers and mobile devices alike.
You don’t need to install anything, so you can jump into the action right away.
Platform layout is user-friendly, making it simple to find your favorite slot.
Sign up today, and discover the excitement of spinning reels!
casino slots
This website, you can discover a great variety of casino slots from famous studios.
Users can enjoy traditional machines as well as feature-packed games with stunning graphics and bonus rounds.
If you’re just starting out or a casino enthusiast, there’s a game that fits your style.
casino games
Each title are ready to play 24/7 and designed for PCs and mobile devices alike.
All games run in your browser, so you can get started without hassle.
Platform layout is intuitive, making it quick to find your favorite slot.
Sign up today, and dive into the excitement of spinning reels!
slot casino
On this platform, you can discover a wide selection of casino slots from famous studios.
Visitors can experience retro-style games as well as modern video slots with high-quality visuals and interactive gameplay.
If you’re just starting out or a casino enthusiast, there’s a game that fits your style.
casino games
All slot machines are ready to play anytime and compatible with laptops and smartphones alike.
No download is required, so you can start playing instantly.
Platform layout is easy to use, making it convenient to explore new games.
Join the fun, and discover the thrill of casino games!
casino
On this platform, you can discover a great variety of casino slots from famous studios.
Users can enjoy traditional machines as well as modern video slots with high-quality visuals and interactive gameplay.
Whether you’re a beginner or a casino enthusiast, there’s a game that fits your style.
slot casino
All slot machines are available round the clock and compatible with desktop computers and tablets alike.
No download is required, so you can get started without hassle.
Platform layout is easy to use, making it quick to explore new games.
Register now, and enjoy the thrill of casino games!
play casino
On this platform, you can find a great variety of casino slots from top providers.
Users can enjoy traditional machines as well as new-generation slots with stunning graphics and exciting features.
Whether you’re a beginner or a seasoned gamer, there’s a game that fits your style.
money casino
The games are instantly accessible 24/7 and optimized for laptops and mobile devices alike.
All games run in your browser, so you can jump into the action right away.
Platform layout is user-friendly, making it simple to explore new games.
Register now, and discover the world of online slots!
slot casino
This website, you can find a wide selection of casino slots from leading developers.
Users can experience classic slots as well as feature-packed games with stunning graphics and exciting features.
Whether you’re a beginner or a casino enthusiast, there’s always a slot to match your mood.
money casino
All slot machines are available round the clock and compatible with laptops and mobile devices alike.
You don’t need to install anything, so you can jump into the action right away.
The interface is user-friendly, making it convenient to browse the collection.
Join the fun, and discover the world of online slots!
casino games
Here, you can discover a great variety of slot machines from leading developers.
Users can enjoy retro-style games as well as new-generation slots with stunning graphics and exciting features.
Even if you’re new or a casino enthusiast, there’s something for everyone.
play aviator
The games are ready to play round the clock and compatible with desktop computers and smartphones alike.
You don’t need to install anything, so you can get started without hassle.
Platform layout is user-friendly, making it convenient to explore new games.
Join the fun, and enjoy the thrill of casino games!
slot casino
On this platform, you can access a great variety of online slots from leading developers.
Users can try out classic slots as well as modern video slots with stunning graphics and exciting features.
Even if you’re new or an experienced player, there’s always a slot to match your mood.
casino slots
All slot machines are ready to play 24/7 and compatible with laptops and smartphones alike.
All games run in your browser, so you can get started without hassle.
Site navigation is user-friendly, making it simple to browse the collection.
Register now, and dive into the excitement of spinning reels!
casino games
On this platform, you can find a wide selection of online slots from leading developers.
Visitors can enjoy traditional machines as well as feature-packed games with vivid animation and bonus rounds.
Even if you’re new or a casino enthusiast, there’s always a slot to match your mood.
play aviator
The games are available anytime and designed for PCs and tablets alike.
No download is required, so you can get started without hassle.
Site navigation is user-friendly, making it simple to browse the collection.
Register now, and dive into the thrill of casino games!
casino
Here, you can access a wide selection of slot machines from famous studios.
Visitors can enjoy traditional machines as well as feature-packed games with vivid animation and interactive gameplay.
Whether you’re a beginner or a casino enthusiast, there’s a game that fits your style.
casino slots
All slot machines are instantly accessible anytime and compatible with PCs and mobile devices alike.
You don’t need to install anything, so you can get started without hassle.
Site navigation is intuitive, making it quick to browse the collection.
Join the fun, and dive into the excitement of spinning reels!
casino slots
Here, you can access lots of slot machines from famous studios.
Players can enjoy traditional machines as well as modern video slots with stunning graphics and exciting features.
Whether you’re a beginner or an experienced player, there’s always a slot to match your mood.
slot casino
The games are instantly accessible anytime and designed for desktop computers and mobile devices alike.
No download is required, so you can get started without hassle.
The interface is user-friendly, making it simple to explore new games.
Register now, and enjoy the excitement of spinning reels!
casino
Here, you can discover lots of online slots from famous studios.
Visitors can experience retro-style games as well as feature-packed games with high-quality visuals and exciting features.
Even if you’re new or an experienced player, there’s something for everyone.
casino games
Each title are available round the clock and compatible with laptops and mobile devices alike.
No download is required, so you can start playing instantly.
Site navigation is intuitive, making it convenient to find your favorite slot.
Register now, and discover the thrill of casino games!
play casino
Here, you can find a great variety of slot machines from top providers.
Visitors can experience traditional machines as well as new-generation slots with high-quality visuals and interactive gameplay.
If you’re just starting out or a seasoned gamer, there’s always a slot to match your mood.
money casino
All slot machines are available 24/7 and optimized for desktop computers and smartphones alike.
No download is required, so you can get started without hassle.
The interface is intuitive, making it simple to find your favorite slot.
Sign up today, and discover the thrill of casino games!
casino games
This website, you can access lots of slot machines from top providers.
Visitors can try out classic slots as well as modern video slots with high-quality visuals and interactive gameplay.
If you’re just starting out or a casino enthusiast, there’s something for everyone.
casino slots
Each title are instantly accessible anytime and compatible with PCs and mobile devices alike.
You don’t need to install anything, so you can get started without hassle.
The interface is user-friendly, making it convenient to explore new games.
Sign up today, and dive into the thrill of casino games!
play casino
On this platform, you can discover a wide selection of casino slots from leading developers.
Users can experience retro-style games as well as feature-packed games with stunning graphics and bonus rounds.
Even if you’re new or a casino enthusiast, there’s always a slot to match your mood.
play aviator
Each title are instantly accessible round the clock and compatible with desktop computers and mobile devices alike.
No download is required, so you can get started without hassle.
Site navigation is easy to use, making it simple to browse the collection.
Sign up today, and enjoy the excitement of spinning reels!
casino slots
This website, you can find a wide selection of online slots from famous studios.
Players can try out traditional machines as well as new-generation slots with high-quality visuals and interactive gameplay.
Whether you’re a beginner or an experienced player, there’s a game that fits your style.
play aviator
The games are instantly accessible 24/7 and designed for laptops and smartphones alike.
All games run in your browser, so you can jump into the action right away.
Site navigation is user-friendly, making it quick to find your favorite slot.
Join the fun, and enjoy the excitement of spinning reels!
casino games
This website, you can find a great variety of slot machines from top providers.
Users can experience traditional machines as well as new-generation slots with vivid animation and interactive gameplay.
If you’re just starting out or a seasoned gamer, there’s always a slot to match your mood.
money casino
The games are available anytime and compatible with desktop computers and smartphones alike.
You don’t need to install anything, so you can jump into the action right away.
The interface is intuitive, making it quick to browse the collection.
Register now, and dive into the excitement of spinning reels!
slot casino
This website, you can find a great variety of slot machines from top providers.
Users can try out classic slots as well as new-generation slots with high-quality visuals and interactive gameplay.
Whether you’re a beginner or a seasoned gamer, there’s something for everyone.
casino
The games are available anytime and optimized for desktop computers and mobile devices alike.
No download is required, so you can jump into the action right away.
Platform layout is intuitive, making it convenient to browse the collection.
Sign up today, and enjoy the thrill of casino games!
casino games
On this platform, you can access a great variety of online slots from famous studios.
Users can experience retro-style games as well as new-generation slots with stunning graphics and bonus rounds.
If you’re just starting out or an experienced player, there’s always a slot to match your mood.
money casino
Each title are available 24/7 and optimized for PCs and tablets alike.
All games run in your browser, so you can jump into the action right away.
The interface is intuitive, making it quick to browse the collection.
Register now, and dive into the excitement of spinning reels!
casino slots
On this platform, you can discover lots of online slots from top providers.
Users can enjoy classic slots as well as new-generation slots with high-quality visuals and bonus rounds.
If you’re just starting out or an experienced player, there’s always a slot to match your mood.
casino games
All slot machines are available 24/7 and designed for laptops and mobile devices alike.
All games run in your browser, so you can start playing instantly.
The interface is intuitive, making it simple to find your favorite slot.
Sign up today, and dive into the thrill of casino games!
play aviator
This website, you can access lots of casino slots from top providers.
Players can try out traditional machines as well as new-generation slots with stunning graphics and bonus rounds.
Even if you’re new or an experienced player, there’s something for everyone.
casino slots
Each title are available anytime and designed for desktop computers and tablets alike.
No download is required, so you can jump into the action right away.
The interface is intuitive, making it quick to find your favorite slot.
Sign up today, and enjoy the excitement of spinning reels!
money casino
Here, you can find a great variety of casino slots from famous studios.
Players can experience classic slots as well as new-generation slots with vivid animation and bonus rounds.
Even if you’re new or a seasoned gamer, there’s something for everyone.
casino
All slot machines are available anytime and optimized for PCs and smartphones alike.
All games run in your browser, so you can jump into the action right away.
Platform layout is user-friendly, making it quick to find your favorite slot.
Sign up today, and enjoy the thrill of casino games!
casino
This website, you can discover a wide selection of online slots from top providers.
Players can enjoy retro-style games as well as modern video slots with high-quality visuals and interactive gameplay.
Even if you’re new or a seasoned gamer, there’s a game that fits your style.
casino slots
The games are ready to play 24/7 and compatible with PCs and smartphones alike.
No download is required, so you can get started without hassle.
Platform layout is intuitive, making it quick to browse the collection.
Register now, and enjoy the thrill of casino games!
play casino
On this platform, you can discover lots of online slots from leading developers.
Users can enjoy retro-style games as well as new-generation slots with stunning graphics and exciting features.
If you’re just starting out or a casino enthusiast, there’s a game that fits your style.
slot casino
Each title are ready to play anytime and designed for laptops and mobile devices alike.
You don’t need to install anything, so you can jump into the action right away.
Site navigation is easy to use, making it convenient to explore new games.
Register now, and dive into the thrill of casino games!
casino games
Here, you can access lots of slot machines from top providers.
Players can try out retro-style games as well as feature-packed games with high-quality visuals and bonus rounds.
If you’re just starting out or a seasoned gamer, there’s a game that fits your style.
casino
All slot machines are ready to play 24/7 and optimized for desktop computers and smartphones alike.
All games run in your browser, so you can jump into the action right away.
Platform layout is user-friendly, making it quick to find your favorite slot.
Join the fun, and discover the excitement of spinning reels!
casino slots
This website, you can access a wide selection of casino slots from famous studios.
Visitors can try out classic slots as well as modern video slots with high-quality visuals and exciting features.
If you’re just starting out or an experienced player, there’s something for everyone.
slot casino
All slot machines are ready to play round the clock and designed for desktop computers and smartphones alike.
You don’t need to install anything, so you can start playing instantly.
The interface is user-friendly, making it quick to find your favorite slot.
Register now, and dive into the world of online slots!
slot casino
Here, you can find a great variety of slot machines from leading developers.
Visitors can enjoy classic slots as well as modern video slots with vivid animation and exciting features.
If you’re just starting out or a casino enthusiast, there’s always a slot to match your mood.
play casino
All slot machines are ready to play 24/7 and optimized for PCs and mobile devices alike.
All games run in your browser, so you can jump into the action right away.
The interface is easy to use, making it simple to find your favorite slot.
Join the fun, and discover the thrill of casino games!
play aviator
Here, you can find a great variety of online slots from famous studios.
Users can experience classic slots as well as new-generation slots with stunning graphics and bonus rounds.
Even if you’re new or an experienced player, there’s a game that fits your style.
casino slots
All slot machines are instantly accessible 24/7 and compatible with laptops and mobile devices alike.
You don’t need to install anything, so you can get started without hassle.
Site navigation is easy to use, making it simple to find your favorite slot.
Join the fun, and discover the world of online slots!
Как киллеры находят заказы
Платформа предоставляет поиска занятости на территории Украины.
На сайте размещены актуальные предложения от разных организаций.
Сервис собирает варианты занятости по разным направлениям.
Полный рабочий день — всё зависит от вас.
https://my-articles-online.com/
Навигация удобен и подстроен на новичков и специалистов.
Регистрация очень простое.
Готовы к новым возможностям? — сайт к вашим услугам.
play aviator
On this platform, you can access a wide selection of online slots from leading developers.
Players can try out retro-style games as well as new-generation slots with high-quality visuals and exciting features.
Whether you’re a beginner or a casino enthusiast, there’s always a slot to match your mood.
play casino
Each title are available round the clock and optimized for desktop computers and smartphones alike.
No download is required, so you can jump into the action right away.
Site navigation is intuitive, making it convenient to browse the collection.
Join the fun, and dive into the thrill of casino games!
CharlesCox
Лето 2025 года обещает быть ярким и нестандартным в плане моды.
В тренде будут многослойность и игра фактур.
Модные цвета включают в себя природные тона, сочетающиеся с любым стилем.
Особое внимание дизайнеры уделяют принтам, среди которых популярны плетёные элементы.
https://qrmoda.ru/fashion/361-manzoni-24-italyanskiy-mehovoy-shik/
Снова популярны элементы 90-х, в современной обработке.
На улицах мегаполисов уже можно увидеть захватывающие образы, которые удивляют.
Будьте в курсе, чтобы создать свой образ.
CharlesCox
Предстоящее лето обещает быть непредсказуемым и оригинальным в плане моды.
В тренде будут свободные силуэты и яркие акценты.
Модные цвета включают в себя мягкие пастели, создающие настроение.
Особое внимание дизайнеры уделяют принтам, среди которых популярны плетёные элементы.
https://telegra.ph/Tihaya-roskosh-5-zhenskih-obrazov-2025-goda-s-veshchami-ot-Loro-Piana-03-23
Снова популярны элементы нулевых, через призму сегодняшнего дня.
На подиумах уже можно увидеть смелые решения, которые вдохновляют.
Следите за обновлениями, чтобы вписаться в тренды.
CharlesCox
Предстоящее лето обещает быть ярким и экспериментальным в плане моды.
В тренде будут многослойность и минимализм с изюминкой.
Гамма оттенков включают в себя природные тона, подчеркивающие индивидуальность.
Особое внимание дизайнеры уделяют принтам, среди которых популярны плетёные элементы.
https://www.tumblr.com/sneakerizer/779458149659869184/coach-%D1%8D%D1%82%D0%B0-%D1%81%D1%83%D0%BC%D0%BA%D0%B0-%D1%81-%D0%B2%D0%B0%D0%BC%D0%B8-%D0%BD%D0%B0-%D0%BC%D0%BD%D0%BE%D0%B3%D0%BE-%D0%BB%D0%B5%D1%82
Набирают популярность элементы 90-х, в свежем прочтении.
В стритстайле уже можно увидеть захватывающие образы, которые вдохновляют.
Следите за обновлениями, чтобы вписаться в тренды.
CharlesCox
Предстоящее лето обещает быть непредсказуемым и инновационным в плане моды.
В тренде будут натуральные ткани и неожиданные сочетания.
Актуальные тона включают в себя мягкие пастели, создающие настроение.
Особое внимание дизайнеры уделяют тканям, среди которых популярны объёмные украшения.
http://www.forumdlainteligentnych.pun.pl/profile.php?action=view&id=1162
Опять актуальны элементы 90-х, через призму сегодняшнего дня.
На улицах мегаполисов уже можно увидеть модные эксперименты, которые поражают.
Не упустите шанс, чтобы встретить лето стильно.
CharlesCox
Предстоящее лето обещает быть насыщенным и экспериментальным в плане моды.
В тренде будут асимметрия и яркие акценты.
Цветовая палитра включают в себя природные тона, выделяющие образ.
Особое внимание дизайнеры уделяют аксессуарам, среди которых популярны макросумки.
https://rentry.co/hk46sowr
Опять актуальны элементы ретро-стиля, интерпретированные по-новому.
В новых коллекциях уже можно увидеть смелые решения, которые вдохновляют.
Следите за обновлениями, чтобы вписаться в тренды.
CharlesCox
Текущий модный сезон обещает быть насыщенным и инновационным в плане моды.
В тренде будут многослойность и минимализм с изюминкой.
Цветовая палитра включают в себя природные тона, подчеркивающие индивидуальность.
Особое внимание дизайнеры уделяют деталям, среди которых популярны объёмные украшения.
https://www.elephantjournal.com/profile/mail-35/
Опять актуальны элементы 90-х, в современной обработке.
На подиумах уже можно увидеть захватывающие образы, которые впечатляют.
Не упустите шанс, чтобы чувствовать себя уверенно.
CharlesCox
Лето 2025 года обещает быть насыщенным и нестандартным в плане моды.
В тренде будут многослойность и игра фактур.
Актуальные тона включают в себя неоновые оттенки, подчеркивающие индивидуальность.
Особое внимание дизайнеры уделяют аксессуарам, среди которых популярны винтажные очки.
https://wheeoo.com/read-blog/25875
Набирают популярность элементы модерна, в свежем прочтении.
На подиумах уже можно увидеть трендовые образы, которые впечатляют.
Следите за обновлениями, чтобы чувствовать себя уверенно.
CharlesCox
Текущий модный сезон обещает быть непредсказуемым и инновационным в плане моды.
В тренде будут многослойность и минимализм с изюминкой.
Актуальные тона включают в себя неоновые оттенки, подчеркивающие индивидуальность.
Особое внимание дизайнеры уделяют принтам, среди которых популярны плетёные элементы.
https://dreevoo.com/profile.php?pid=716354
Снова популярны элементы модерна, в свежем прочтении.
На подиумах уже можно увидеть модные эксперименты, которые вдохновляют.
Не упустите шанс, чтобы создать свой образ.
CharlesCox
Текущий модный сезон обещает быть насыщенным и инновационным в плане моды.
В тренде будут натуральные ткани и игра фактур.
Гамма оттенков включают в себя мягкие пастели, создающие настроение.
Особое внимание дизайнеры уделяют принтам, среди которых популярны винтажные очки.
https://rentry.co/o5ahpm9q
Возвращаются в моду элементы 90-х, в современной обработке.
На улицах мегаполисов уже можно увидеть модные эксперименты, которые удивляют.
Следите за обновлениями, чтобы чувствовать себя уверенно.
CharlesCox
Предстоящее лето обещает быть насыщенным и инновационным в плане моды.
В тренде будут асимметрия и минимализм с изюминкой.
Гамма оттенков включают в себя чистые базовые цвета, выделяющие образ.
Особое внимание дизайнеры уделяют тканям, среди которых популярны плетёные элементы.
https://www.brownbook.net/business/53075710/lepodium/
Возвращаются в моду элементы 90-х, в свежем прочтении.
На улицах мегаполисов уже можно увидеть трендовые образы, которые удивляют.
Не упустите шанс, чтобы создать свой образ.
CharlesCox
Текущий модный сезон обещает быть непредсказуемым и нестандартным в плане моды.
В тренде будут свободные силуэты и минимализм с изюминкой.
Цветовая палитра включают в себя природные тона, создающие настроение.
Особое внимание дизайнеры уделяют деталям, среди которых популярны макросумки.
https://qrmoda.ru/fashion/84-kollektsiya-lacoste-posvyashchennaya-olimpiyskim-igram-1924-goda/
Набирают популярность элементы нулевых, через призму сегодняшнего дня.
На улицах мегаполисов уже можно увидеть трендовые образы, которые поражают.
Следите за обновлениями, чтобы встретить лето стильно.
CharlesCox
Предстоящее лето обещает быть непредсказуемым и оригинальным в плане моды.
В тренде будут свободные силуэты и минимализм с изюминкой.
Актуальные тона включают в себя природные тона, подчеркивающие индивидуальность.
Особое внимание дизайнеры уделяют принтам, среди которых популярны объёмные украшения.
https://lepodium.blogchaat.com/30281514/lepodium-%D0%B2%D0%B0%D1%88-%D0%BF%D1%80%D0%BE%D0%B2%D0%BE%D0%B4%D0%BD%D0%B8%D0%BA-%D0%B2-%D0%BC%D0%B8%D1%80%D0%B5-%D0%BB%D1%8E%D0%BA%D1%81%D0%BE%D0%B2%D0%BE%D0%B9-%D0%BC%D0%BE%D0%B4%D1%8B
Опять актуальны элементы ретро-стиля, в свежем прочтении.
В новых коллекциях уже можно увидеть захватывающие образы, которые впечатляют.
Следите за обновлениями, чтобы встретить лето стильно.
Muhammad
Hello, its fastidious post on the topic of media print, we all know media is a enormous
source of data.
My website – Ботокс безопасность
slot casino
Here, you can find a great variety of casino slots from leading developers.
Players can try out retro-style games as well as new-generation slots with stunning graphics and exciting features.
Even if you’re new or a casino enthusiast, there’s a game that fits your style.
play aviator
The games are ready to play round the clock and compatible with desktop computers and mobile devices alike.
All games run in your browser, so you can get started without hassle.
The interface is user-friendly, making it quick to find your favorite slot.
Join the fun, and discover the world of online slots!
casino games
Here, you can find a wide selection of slot machines from famous studios.
Players can experience classic slots as well as feature-packed games with high-quality visuals and interactive gameplay.
Whether you’re a beginner or an experienced player, there’s always a slot to match your mood.
casino
Each title are instantly accessible anytime and compatible with laptops and tablets alike.
No download is required, so you can jump into the action right away.
The interface is easy to use, making it quick to explore new games.
Join the fun, and enjoy the excitement of spinning reels!
money casino
On this platform, you can access a great variety of slot machines from famous studios.
Visitors can try out retro-style games as well as new-generation slots with high-quality visuals and exciting features.
If you’re just starting out or an experienced player, there’s a game that fits your style.
money casino
Each title are available 24/7 and optimized for PCs and smartphones alike.
No download is required, so you can jump into the action right away.
Site navigation is user-friendly, making it convenient to browse the collection.
Sign up today, and enjoy the thrill of casino games!
slot casino
This website, you can discover lots of slot machines from famous studios.
Users can enjoy retro-style games as well as modern video slots with high-quality visuals and bonus rounds.
Even if you’re new or a seasoned gamer, there’s something for everyone.
play casino
The games are ready to play 24/7 and optimized for PCs and smartphones alike.
You don’t need to install anything, so you can jump into the action right away.
Platform layout is intuitive, making it convenient to find your favorite slot.
Sign up today, and dive into the thrill of casino games!
slot casino
On this platform, you can access a great variety of slot machines from leading developers.
Visitors can enjoy retro-style games as well as modern video slots with vivid animation and exciting features.
Even if you’re new or a seasoned gamer, there’s something for everyone.
casino games
Each title are available 24/7 and designed for PCs and mobile devices alike.
You don’t need to install anything, so you can jump into the action right away.
Platform layout is user-friendly, making it convenient to browse the collection.
Sign up today, and enjoy the excitement of spinning reels!
casino games
On this platform, you can access a wide selection of slot machines from top providers.
Players can try out traditional machines as well as modern video slots with vivid animation and exciting features.
Even if you’re new or a seasoned gamer, there’s always a slot to match your mood.
money casino
Each title are instantly accessible anytime and designed for laptops and mobile devices alike.
All games run in your browser, so you can start playing instantly.
Site navigation is easy to use, making it quick to explore new games.
Register now, and dive into the excitement of spinning reels!
slot casino
On this platform, you can find a great variety of online slots from leading developers.
Players can experience traditional machines as well as feature-packed games with vivid animation and bonus rounds.
If you’re just starting out or an experienced player, there’s always a slot to match your mood.
slot casino
Each title are ready to play 24/7 and designed for desktop computers and tablets alike.
You don’t need to install anything, so you can get started without hassle.
Site navigation is intuitive, making it convenient to find your favorite slot.
Sign up today, and dive into the thrill of casino games!
casino slots
On this platform, you can discover a great variety of slot machines from famous studios.
Visitors can enjoy retro-style games as well as new-generation slots with high-quality visuals and bonus rounds.
Even if you’re new or an experienced player, there’s always a slot to match your mood.
casino slots
Each title are available anytime and compatible with laptops and mobile devices alike.
No download is required, so you can start playing instantly.
Platform layout is user-friendly, making it quick to find your favorite slot.
Sign up today, and dive into the excitement of spinning reels!
casino
On this platform, you can discover a great variety of online slots from top providers.
Users can experience traditional machines as well as modern video slots with high-quality visuals and interactive gameplay.
Even if you’re new or an experienced player, there’s a game that fits your style.
casino slots
The games are ready to play anytime and compatible with PCs and mobile devices alike.
No download is required, so you can start playing instantly.
Site navigation is easy to use, making it convenient to find your favorite slot.
Sign up today, and enjoy the world of online slots!
casino games
This website, you can find a great variety of online slots from famous studios.
Users can enjoy traditional machines as well as modern video slots with high-quality visuals and exciting features.
Whether you’re a beginner or a casino enthusiast, there’s always a slot to match your mood.
casino
The games are ready to play anytime and designed for laptops and mobile devices alike.
All games run in your browser, so you can get started without hassle.
Platform layout is easy to use, making it convenient to find your favorite slot.
Join the fun, and enjoy the thrill of casino games!
money casino
On this platform, you can access lots of online slots from famous studios.
Users can try out traditional machines as well as feature-packed games with vivid animation and exciting features.
Even if you’re new or an experienced player, there’s something for everyone.
casino slots
Each title are ready to play anytime and optimized for laptops and mobile devices alike.
No download is required, so you can jump into the action right away.
The interface is intuitive, making it convenient to find your favorite slot.
Sign up today, and discover the thrill of casino games!
play casino
Here, you can discover a wide selection of casino slots from famous studios.
Players can enjoy retro-style games as well as new-generation slots with vivid animation and interactive gameplay.
Whether you’re a beginner or a casino enthusiast, there’s a game that fits your style.
casino slots
The games are instantly accessible 24/7 and designed for PCs and mobile devices alike.
All games run in your browser, so you can jump into the action right away.
Platform layout is easy to use, making it simple to browse the collection.
Sign up today, and enjoy the world of online slots!
money casino
Here, you can discover a great variety of casino slots from top providers.
Visitors can experience traditional machines as well as modern video slots with vivid animation and bonus rounds.
Whether you’re a beginner or an experienced player, there’s something for everyone.
casino
The games are ready to play anytime and optimized for laptops and mobile devices alike.
No download is required, so you can start playing instantly.
The interface is user-friendly, making it convenient to browse the collection.
Join the fun, and enjoy the excitement of spinning reels!
casino games
Here, you can access a wide selection of online slots from leading developers.
Visitors can try out traditional machines as well as new-generation slots with high-quality visuals and bonus rounds.
Even if you’re new or a seasoned gamer, there’s a game that fits your style.
casino
The games are instantly accessible anytime and designed for desktop computers and tablets alike.
You don’t need to install anything, so you can jump into the action right away.
Platform layout is easy to use, making it quick to find your favorite slot.
Sign up today, and dive into the thrill of casino games!
MichaelNef
Were you aware that over 60% of people taking prescriptions make dangerous medication errors due to lack of knowledge?
Your wellbeing should be your top priority. Each pharmaceutical choice you implement significantly affects your long-term wellbeing. Maintaining awareness about your prescriptions is absolutely essential for successful recovery.
Your health goes far beyond taking pills. Each drug changes your biological systems in potentially dangerous ways.
Consider these life-saving facts:
1. Combining medications can cause fatal reactions
2. Over-the-counter supplements have serious risks
3. Skipping doses reduces effectiveness
To avoid risks, always:
✓ Research combinations using official tools
✓ Read instructions thoroughly prior to using any medication
✓ Ask your pharmacist about correct dosage
___________________________________
For professional medication guidance, visit:
https://www.provenexpert.com/frommars-online/
MichaelNef
It’s alarming to realize that nearly 50% of medication users make dangerous pharmaceutical mishaps due to insufficient information?
Your wellbeing should be your top priority. All treatment options you implement plays crucial role in your body’s functionality. Maintaining awareness about medical treatments is absolutely essential for optimal health outcomes.
Your health goes far beyond swallowing medications. Each drug interacts with your body’s chemistry in specific ways.
Remember these essential facts:
1. Combining medications can cause dangerous side effects
2. Seemingly harmless supplements have serious risks
3. Altering dosages causes complications
For your safety, always:
✓ Check compatibility via medical databases
✓ Read instructions thoroughly when starting any medication
✓ Speak with specialists about correct dosage
___________________________________
For verified pharmaceutical advice, visit:
https://community.alteryx.com/t5/user/viewprofilepage/user-id/576296
MichaelNef
Were you aware that nearly 50% of medication users make dangerous medication errors because of insufficient information?
Your wellbeing is your most valuable asset. All treatment options you implement significantly affects your body’s functionality. Staying educated about medical treatments should be mandatory for successful recovery.
Your health isn’t just about taking pills. Every medication interacts with your body’s chemistry in specific ways.
Remember these essential facts:
1. Combining medications can cause dangerous side effects
2. Even common allergy medicines have strict usage limits
3. Altering dosages reduces effectiveness
For your safety, always:
✓ Verify interactions using official tools
✓ Study labels thoroughly when starting any medication
✓ Consult your doctor about proper usage
___________________________________
For professional drug information, visit:
https://pando.life/article/1022991
MichaelNef
Were you aware that nearly 50% of people taking prescriptions commit preventable medication errors because of poor understanding?
Your health should be your top priority. All treatment options you make plays crucial role in your long-term wellbeing. Being informed about your prescriptions should be mandatory for disease prevention.
Your health depends on more than swallowing medications. All pharmaceutical products interacts with your body’s chemistry in potentially dangerous ways.
Remember these essential facts:
1. Mixing certain drugs can cause dangerous side effects
2. Even common pain relievers have potent side effects
3. Skipping doses causes complications
For your safety, always:
✓ Check compatibility using official tools
✓ Read instructions thoroughly before taking medical treatment
✓ Speak with specialists about correct dosage
___________________________________
For verified pharmaceutical advice, visit:
https://community.alteryx.com/t5/user/viewprofilepage/user-id/569078
MichaelNef
Did you know that 1 in 3 people taking prescriptions commit preventable medication errors because of insufficient information?
Your health is your most valuable asset. Every medication decision you make directly impacts your long-term wellbeing. Being informed about medical treatments is absolutely essential for disease prevention.
Your health isn’t just about taking pills. Every medication changes your biological systems in unique ways.
Never ignore these critical facts:
1. Taking incompatible prescriptions can cause health emergencies
2. Over-the-counter pain relievers have potent side effects
3. Self-adjusting treatment causes complications
To protect yourself, always:
✓ Verify interactions using official tools
✓ Review guidelines completely when starting new prescriptions
✓ Speak with specialists about proper usage
___________________________________
For reliable drug information, visit:
https://www.provenexpert.com/en-us/subgual-online/
MichaelNef
Were you aware that nearly 50% of patients make dangerous drug mistakes due to insufficient information?
Your health should be your top priority. All treatment options you implement plays crucial role in your long-term wellbeing. Maintaining awareness about medical treatments is absolutely essential for disease prevention.
Your health goes far beyond following prescriptions. Every medication affects your physiology in potentially dangerous ways.
Remember these life-saving facts:
1. Mixing certain drugs can cause dangerous side effects
2. Over-the-counter allergy medicines have potent side effects
3. Self-adjusting treatment causes complications
To protect yourself, always:
✓ Check compatibility using official tools
✓ Study labels thoroughly prior to using any medication
✓ Consult your doctor about correct dosage
___________________________________
For professional medication guidance, visit:
https://insta.tel/read-blog/92688_the-apothecary-s-dilemma-a-tale-of-choices-and-consequences.html
MichaelNef
Were you aware that 1 in 3 people taking prescriptions make dangerous medication errors because of poor understanding?
Your physical condition requires constant attention. Each pharmaceutical choice you make significantly affects your long-term wellbeing. Being informed about your prescriptions should be mandatory for optimal health outcomes.
Your health depends on more than following prescriptions. All pharmaceutical products interacts with your biological systems in unique ways.
Never ignore these critical facts:
1. Mixing certain drugs can cause fatal reactions
2. Even common pain relievers have strict usage limits
3. Altering dosages undermines therapy
For your safety, always:
✓ Verify interactions using official tools
✓ Study labels in detail before taking new prescriptions
✓ Speak with specialists about proper usage
___________________________________
For verified drug information, visit:
https://www.pinterest.com/pin/879609370963839381/
MichaelNef
Did you know that 1 in 3 people taking prescriptions commit preventable pharmaceutical mishaps due to poor understanding?
Your wellbeing requires constant attention. Every medication decision you implement directly impacts your long-term wellbeing. Being informed about medical treatments isn’t optional for disease prevention.
Your health goes far beyond following prescriptions. Every medication changes your physiology in specific ways.
Consider these life-saving facts:
1. Mixing certain drugs can cause health emergencies
2. Seemingly harmless allergy medicines have strict usage limits
3. Self-adjusting treatment causes complications
To avoid risks, always:
✓ Research combinations using official tools
✓ Study labels in detail prior to using any medication
✓ Speak with specialists about proper usage
___________________________________
For verified medication guidance, visit:
https://www.provenexpert.com/bacterial-zoonoses/
MichaelNef
Did you know that 1 in 3 patients commit preventable pharmaceutical mishaps due to insufficient information?
Your physical condition is your most valuable asset. Every medication decision you consider significantly affects your quality of life. Maintaining awareness about your prescriptions is absolutely essential for disease prevention.
Your health goes far beyond swallowing medications. All pharmaceutical products changes your physiology in unique ways.
Consider these life-saving facts:
1. Taking incompatible prescriptions can cause health emergencies
2. Even common allergy medicines have potent side effects
3. Self-adjusting treatment causes complications
For your safety, always:
✓ Verify interactions via medical databases
✓ Study labels thoroughly before taking any medication
✓ Consult your doctor about correct dosage
___________________________________
For reliable pharmaceutical advice, visit:
https://images.app.goo.gl/81Qym3ssaaFboMqJ6
MichaelNef
Did you know that 1 in 3 medication users experience serious drug mistakes due to lack of knowledge?
Your health is your most valuable asset. Each pharmaceutical choice you consider directly impacts your long-term wellbeing. Staying educated about your prescriptions should be mandatory for successful recovery.
Your health goes far beyond taking pills. Every medication changes your body’s chemistry in specific ways.
Never ignore these life-saving facts:
1. Taking incompatible prescriptions can cause health emergencies
2. Over-the-counter allergy medicines have serious risks
3. Self-adjusting treatment causes complications
To avoid risks, always:
✓ Research combinations using official tools
✓ Study labels thoroughly prior to using new prescriptions
✓ Speak with specialists about correct dosage
___________________________________
For professional drug information, visit:
https://www.provenexpert.com/chlamydial-conjunctivitis/
MichaelNef
It’s alarming to realize that 1 in 3 medication users commit preventable drug mistakes because of poor understanding?
Your physical condition requires constant attention. All treatment options you make directly impacts your body’s functionality. Being informed about your prescriptions is absolutely essential for successful recovery.
Your health isn’t just about swallowing medications. Each drug changes your physiology in unique ways.
Remember these critical facts:
1. Taking incompatible prescriptions can cause fatal reactions
2. Even common supplements have serious risks
3. Skipping doses undermines therapy
For your safety, always:
✓ Research combinations with professional help
✓ Study labels in detail when starting any medication
✓ Consult your doctor about proper usage
___________________________________
For reliable medication guidance, visit:
https://www.pinterest.com/pin/879609370963804541/
MichaelNef
It’s alarming to realize that 1 in 3 medication users make dangerous pharmaceutical mishaps due to poor understanding?
Your physical condition is your most valuable asset. Each pharmaceutical choice you implement significantly affects your quality of life. Maintaining awareness about medical treatments is absolutely essential for successful recovery.
Your health goes far beyond swallowing medications. Every medication affects your physiology in potentially dangerous ways.
Remember these essential facts:
1. Taking incompatible prescriptions can cause fatal reactions
2. Seemingly harmless pain relievers have strict usage limits
3. Altering dosages causes complications
For your safety, always:
✓ Research combinations with professional help
✓ Review guidelines completely prior to using medical treatment
✓ Ask your pharmacist about correct dosage
___________________________________
For verified medication guidance, visit:
https://community.alteryx.com/t5/user/viewprofilepage/user-id/569081
MichaelNef
Were you aware that nearly 50% of people taking prescriptions make dangerous drug mistakes because of lack of knowledge?
Your physical condition is your most valuable asset. Each pharmaceutical choice you implement significantly affects your quality of life. Being informed about the drugs you take is absolutely essential for optimal health outcomes.
Your health isn’t just about swallowing medications. All pharmaceutical products changes your physiology in specific ways.
Never ignore these life-saving facts:
1. Taking incompatible prescriptions can cause health emergencies
2. Over-the-counter supplements have serious risks
3. Self-adjusting treatment reduces effectiveness
For your safety, always:
✓ Research combinations with professional help
✓ Review guidelines thoroughly when starting new prescriptions
✓ Speak with specialists about proper usage
___________________________________
For professional medication guidance, visit:
https://www.flickr.com/groups/14794470@N24/discuss/72157721919096549
MichaelNef
It’s alarming to realize that nearly 50% of medication users commit preventable drug mistakes because of poor understanding?
Your physical condition should be your top priority. Each pharmaceutical choice you implement plays crucial role in your body’s functionality. Maintaining awareness about your prescriptions isn’t optional for successful recovery.
Your health depends on more than following prescriptions. All pharmaceutical products changes your biological systems in unique ways.
Consider these critical facts:
1. Combining medications can cause health emergencies
2. Even common supplements have strict usage limits
3. Altering dosages causes complications
To protect yourself, always:
✓ Check compatibility with professional help
✓ Study labels thoroughly prior to using new prescriptions
✓ Speak with specialists about proper usage
___________________________________
For professional drug information, visit:
https://community.alteryx.com/t5/user/viewprofilepage/user-id/569409
MichaelNef
Were you aware that over 60% of people taking prescriptions make dangerous drug mistakes because of poor understanding?
Your physical condition requires constant attention. Every medication decision you make plays crucial role in your body’s functionality. Being informed about your prescriptions isn’t optional for successful recovery.
Your health isn’t just about taking pills. All pharmaceutical products interacts with your biological systems in potentially dangerous ways.
Remember these critical facts:
1. Taking incompatible prescriptions can cause dangerous side effects
2. Even common allergy medicines have serious risks
3. Skipping doses causes complications
To protect yourself, always:
✓ Check compatibility with professional help
✓ Read instructions thoroughly prior to using new prescriptions
✓ Speak with specialists about proper usage
___________________________________
For reliable pharmaceutical advice, visit:
https://www.pinterest.com/pin/879609370963803867/
play casino
This website, you can discover a wide selection of casino slots from leading developers.
Players can enjoy traditional machines as well as new-generation slots with vivid animation and interactive gameplay.
If you’re just starting out or a casino enthusiast, there’s a game that fits your style.
casino slots
The games are ready to play round the clock and optimized for desktop computers and tablets alike.
All games run in your browser, so you can jump into the action right away.
Site navigation is easy to use, making it quick to browse the collection.
Join the fun, and enjoy the thrill of casino games!
casino games
On this platform, you can discover a great variety of casino slots from famous studios.
Users can try out classic slots as well as feature-packed games with vivid animation and bonus rounds.
Even if you’re new or a seasoned gamer, there’s always a slot to match your mood.
money casino
All slot machines are available anytime and optimized for PCs and mobile devices alike.
All games run in your browser, so you can jump into the action right away.
Site navigation is user-friendly, making it quick to explore new games.
Register now, and enjoy the excitement of spinning reels!
Jamesbrunk
Our e-pharmacy features a broad selection of pharmaceuticals at affordable prices.
Customers can discover various drugs suitable for different health conditions.
Our goal is to keep trusted brands at a reasonable cost.
Quick and dependable delivery ensures that your medication arrives on time.
Take advantage of ordering medications online with us.
amoxil and clavulanate potassium
Jamesbrunk
This online pharmacy features a wide range of health products at affordable prices.
Customers can discover various remedies suitable for different health conditions.
We work hard to offer trusted brands without breaking the bank.
Speedy and secure shipping ensures that your order gets to you quickly.
Take advantage of shopping online through our service.
what is cenforce
Jamesbrunk
This online pharmacy features a wide range of health products at affordable prices.
Customers can discover both prescription and over-the-counter drugs for all health requirements.
We strive to maintain high-quality products at a reasonable cost.
Speedy and secure shipping guarantees that your order gets to you quickly.
Experience the convenience of ordering medications online with us.
Silagra By Cipla
Jamesbrunk
Our e-pharmacy offers a broad selection of health products for budget-friendly costs.
Customers can discover various remedies suitable for different health conditions.
We work hard to offer high-quality products while saving you money.
Speedy and secure shipping ensures that your purchase gets to you quickly.
Take advantage of ordering medications online through our service.
generic drug names
Jamesbrunk
Our e-pharmacy features a broad selection of medications at affordable prices.
Shoppers will encounter various medicines for all health requirements.
We work hard to offer trusted brands without breaking the bank.
Fast and reliable shipping provides that your medication gets to you quickly.
Take advantage of shopping online on our platform.
buy amoxil
Jamesbrunk
The digital drugstore features a broad selection of health products at affordable prices.
Customers can discover all types of medicines suitable for different health conditions.
We strive to maintain high-quality products without breaking the bank.
Quick and dependable delivery guarantees that your medication is delivered promptly.
Enjoy the ease of getting your meds through our service.
amoxil and clavulanate potassium
Jamesbrunk
This online pharmacy offers an extensive variety of pharmaceuticals for budget-friendly costs.
Customers can discover all types of remedies suitable for different health conditions.
We strive to maintain trusted brands while saving you money.
Speedy and secure shipping guarantees that your order is delivered promptly.
Take advantage of shopping online through our service.
fildena fruit chew
Jamesbrunk
This online pharmacy features an extensive variety of medications at affordable prices.
Customers can discover both prescription and over-the-counter remedies to meet your health needs.
Our goal is to keep high-quality products while saving you money.
Speedy and secure shipping ensures that your purchase gets to you quickly.
Take advantage of getting your meds on our platform.
kamagra oral jelly 100mg
Jamesbrunk
Our e-pharmacy provides a broad selection of pharmaceuticals at affordable prices.
Shoppers will encounter various remedies suitable for different health conditions.
We strive to maintain trusted brands at a reasonable cost.
Speedy and secure shipping provides that your purchase is delivered promptly.
Enjoy the ease of ordering medications online with us.
generic drug names
Jamesbrunk
Our e-pharmacy provides a broad selection of pharmaceuticals with competitive pricing.
You can find both prescription and over-the-counter remedies suitable for different health conditions.
We strive to maintain safe and effective medications at a reasonable cost.
Speedy and secure shipping guarantees that your order gets to you quickly.
Experience the convenience of getting your meds on our platform.
fildena 100 side effects
Jamesbrunk
This online pharmacy provides an extensive variety of medications at affordable prices.
Customers can discover all types of remedies for all health requirements.
We work hard to offer safe and effective medications while saving you money.
Fast and reliable shipping guarantees that your medication is delivered promptly.
Experience the convenience of getting your meds on our platform.
what is a generic drug
Jamesbrunk
Our e-pharmacy provides a broad selection of health products for budget-friendly costs.
You can find both prescription and over-the-counter medicines to meet your health needs.
We work hard to offer high-quality products while saving you money.
Fast and reliable shipping guarantees that your purchase is delivered promptly.
Experience the convenience of getting your meds through our service.
generic ed drugs
Jamesbrunk
The digital drugstore offers a wide range of health products with competitive pricing.
Customers can discover both prescription and over-the-counter medicines for all health requirements.
We work hard to offer high-quality products at a reasonable cost.
Speedy and secure shipping provides that your order gets to you quickly.
Enjoy the ease of ordering medications online on our platform.
amoxil medicine
user-377345
awesome
slot casino
This website, you can find lots of slot machines from leading developers.
Users can try out classic slots as well as feature-packed games with stunning graphics and exciting features.
Whether you’re a beginner or an experienced player, there’s something for everyone.
play aviator
All slot machines are instantly accessible 24/7 and compatible with desktop computers and tablets alike.
You don’t need to install anything, so you can get started without hassle.
Site navigation is user-friendly, making it simple to explore new games.
Register now, and discover the world of online slots!
casino
Here, you can find a wide selection of casino slots from famous studios.
Users can try out classic slots as well as modern video slots with vivid animation and exciting features.
Even if you’re new or an experienced player, there’s a game that fits your style.
play casino
Each title are instantly accessible anytime and optimized for laptops and tablets alike.
All games run in your browser, so you can get started without hassle.
Platform layout is user-friendly, making it simple to browse the collection.
Sign up today, and discover the world of online slots!
radio alarm clock phone combo
This section presents multifunctional timepieces from reputable makers.
You can find top-loading CD players with AM/FM radio and dual alarms.
These devices come with AUX jacks, device charging, and memory backup.
Available products extends from affordable clocks to premium refurbished units.
alarm-radio-clocks.com
All devices provide nap modes, sleep timers, and bright LED displays.
Buy now using online retailers with free delivery.
Discover the best disc player alarm clock for home convenience.
best cd alarm clock radio
On this site offers multifunctional timepieces from top providers.
You can find modern disc players with PLL tuner and twin alarm functions.
Most units feature auxiliary inputs, USB charging, and backup batteries.
Our range covers affordable clocks to high-end designs.
best alarm clocks with radio
All devices include snooze buttons, sleep timers, and illuminated panels.
Shop the collection are available via online retailers with free delivery.
Select the perfect clock-radio-CD setup for office daily routines.
cd alarm clock radio
On this site features CD player radio alarm clocks by trusted manufacturers.
Browse through premium CD devices with FM/AM reception and dual wake options.
Most units come with AUX jacks, USB charging, and backup batteries.
The selection spans value picks to premium refurbished units.
best radio alarm clock
All clocks include sleep timers, sleep timers, and digital displays.
Order today through online retailers with fast shipping.
Find the best disc player alarm clock for kitchen everyday enjoyment.
radio alarm clock phone combo
This page presents CD/radio/clock combos made by leading brands.
Here you’ll discover sleek CD units with digital radio and dual wake options.
Many models feature external audio inputs, USB charging, and power outage protection.
The selection ranges from affordable clocks to high-end designs.
best home radio cd player
All clocks offer snooze functions, sleep timers, and bright LED displays.
Purchases using Walmart with fast shipping.
Choose the best disc player alarm clock for kitchen everyday enjoyment.
stereo clock radio alarm
Our platform features CD player radio alarm clocks from leading brands.
Browse through sleek CD units with AM/FM radio and dual wake options.
Most units come with AUX jacks, USB charging, and power outage protection.
Available products spans affordable clocks to high-end designs.
radio alarm clock phone combo
Every model include snooze buttons, auto-off timers, and illuminated panels.
Order today using Walmart links with free shipping.
Select your ultimate wake-up solution for office everyday enjoyment.
best am fm clock radios
This page presents disc player alarm devices made by top providers.
Browse through modern disc players with AM/FM radio and two alarm settings.
Many models offer AUX jacks, charging capability, and backup batteries.
This collection covers economical models to luxury editions.
best am fm clock radios
All clocks boast snooze buttons, night modes, and digital displays.
Order today through Walmart and no extra cost.
Select the perfect clock-radio-CD setup for bedroom convenience.
alarm-radio-clocks.com
On this site showcases CD/radio/clock combos from leading brands.
Browse through sleek CD units with PLL tuner and two alarm settings.
Many models offer external audio inputs, device charging, and memory backup.
This collection ranges from economical models to luxury editions.
best radio alarm clock
Each one boast nap modes, rest timers, and illuminated panels.
Shop the collection via direct Amazon with fast shipping.
Find the perfect clock-radio-CD setup for office or office use.
best cd alarm clock radio
This section presents multifunctional timepieces by trusted manufacturers.
Here you’ll discover top-loading CD players with PLL tuner and dual wake options.
Many models come with auxiliary inputs, charging capability, and backup batteries.
The selection extends from economical models to high-end designs.
best cd alarm clock radio
Each one provide snooze functions, night modes, and LED screens.
Order today through online retailers with free delivery.
Select the perfect clock-radio-CD setup for home or office use.
best cd alarm clock radio
On this site offers disc player alarm devices crafted by leading brands.
Browse through premium CD devices with digital radio and twin alarm functions.
Most units feature aux-in ports, charging capability, and backup batteries.
Available products ranges from affordable clocks to high-end designs.
alarm-radio-clocks.com
Every model provide nap modes, night modes, and bright LED displays.
Order today via direct Walmart and no extra cost.
Select the best disc player alarm clock for office or office use.
best alarm clock cd player
This section features CD player radio alarm clocks from top providers.
Browse through premium CD devices with digital radio and two alarm settings.
Each clock include external audio inputs, charging capability, and battery backup.
This collection spans economical models to high-end designs.
alarm-radio-clocks.com
All devices boast snooze functions, auto-off timers, and LED screens.
Purchases are available via eBay with free delivery.
Discover your ultimate wake-up solution for home convenience.
radio alarm clock phone combo
This page features CD/radio/clock combos made by reputable makers.
Visit to explore modern disc players with PLL tuner and two alarm settings.
Many models offer aux-in ports, USB charging, and memory backup.
The selection covers value picks to elite choices.
cd clock
Every model provide sleep timers, sleep timers, and illuminated panels.
Purchases through online retailers links with free shipping.
Discover your ideal music and alarm combination for home or office use.
Davidcek
The site features buggy rentals throughout Crete.
Anyone can conveniently book a buggy for adventure.
In case you’re looking to discover mountain roads, a buggy is the perfect way to do it.
https://www.zillow.com/profile/buggycrete
Each buggy are safe and clean and offered with flexible bookings.
Booking through this site is hassle-free and comes with affordable prices.
Get ready to ride and experience Crete in full freedom.
casino games
On this platform, you can find lots of slot machines from famous studios.
Players can try out classic slots as well as new-generation slots with stunning graphics and interactive gameplay.
Whether you’re a beginner or a casino enthusiast, there’s a game that fits your style.
casino games
All slot machines are instantly accessible anytime and compatible with laptops and mobile devices alike.
All games run in your browser, so you can get started without hassle.
The interface is user-friendly, making it convenient to find your favorite slot.
Join the fun, and dive into the excitement of spinning reels!
casino games
On this platform, you can find lots of casino slots from leading developers.
Visitors can experience classic slots as well as new-generation slots with vivid animation and exciting features.
If you’re just starting out or an experienced player, there’s a game that fits your style.
slot casino
All slot machines are instantly accessible round the clock and designed for PCs and mobile devices alike.
You don’t need to install anything, so you can start playing instantly.
The interface is intuitive, making it convenient to explore new games.
Sign up today, and enjoy the world of online slots!
money casino
This website, you can access a wide selection of casino slots from leading developers.
Users can experience retro-style games as well as new-generation slots with high-quality visuals and exciting features.
Whether you’re a beginner or a seasoned gamer, there’s always a slot to match your mood.
play aviator
The games are ready to play 24/7 and compatible with PCs and smartphones alike.
No download is required, so you can jump into the action right away.
Platform layout is intuitive, making it convenient to find your favorite slot.
Sign up today, and discover the thrill of casino games!
Davidcek
This website offers off-road vehicle rentals throughout Crete.
Travelers may easily book a buggy for exploration.
If you’re looking to discover mountain roads, a buggy is the fun way to do it.
https://rentry.co/rmwfrtvu
Our rides are safe and clean and offered in custom schedules.
Through our service is simple and comes with affordable prices.
Start your journey and feel Crete in full freedom.
Davidcek
This website allows buggy hire on Crete.
Travelers may conveniently book a vehicle for travel.
When you’re looking to discover mountain roads, a buggy is the ideal way to do it.
https://linktr.ee/buggycrete
Our rides are well-maintained and can be rented for full-day plans.
Through our service is user-friendly and comes with affordable prices.
Hit the trails and enjoy Crete from a new angle.
Davidcek
This website offers off-road vehicle rentals on Crete.
You can safely arrange a machine for fun.
In case you’re looking to travel around mountain roads, a buggy is the fun way to do it.
https://www.behance.net/buggycrete
Our rides are safe and clean and offered with flexible schedules.
Using this website is hassle-free and comes with affordable prices.
Hit the trails and enjoy Crete in full freedom.
casino games
On this platform, you can discover a wide selection of casino slots from leading developers.
Users can enjoy classic slots as well as new-generation slots with stunning graphics and bonus rounds.
If you’re just starting out or a casino enthusiast, there’s something for everyone.
play casino
The games are available anytime and compatible with PCs and mobile devices alike.
No download is required, so you can get started without hassle.
The interface is easy to use, making it convenient to browse the collection.
Register now, and discover the excitement of spinning reels!
play casino
On this platform, you can find a great variety of casino slots from top providers.
Players can enjoy classic slots as well as modern video slots with vivid animation and bonus rounds.
Whether you’re a beginner or a seasoned gamer, there’s something for everyone.
casino games
All slot machines are available anytime and designed for laptops and tablets alike.
No download is required, so you can start playing instantly.
Site navigation is user-friendly, making it simple to explore new games.
Join the fun, and enjoy the excitement of spinning reels!
casino slots
This website, you can discover a great variety of slot machines from famous studios.
Visitors can experience traditional machines as well as new-generation slots with vivid animation and bonus rounds.
Whether you’re a beginner or a seasoned gamer, there’s a game that fits your style.
casino games
All slot machines are available anytime and designed for PCs and tablets alike.
No download is required, so you can jump into the action right away.
Platform layout is intuitive, making it simple to browse the collection.
Register now, and enjoy the excitement of spinning reels!
casino games
On this platform, you can discover a wide selection of online slots from famous studios.
Visitors can enjoy retro-style games as well as new-generation slots with vivid animation and bonus rounds.
Even if you’re new or a seasoned gamer, there’s a game that fits your style.
casino games
The games are available anytime and optimized for desktop computers and smartphones alike.
No download is required, so you can get started without hassle.
The interface is user-friendly, making it convenient to find your favorite slot.
Join the fun, and discover the excitement of spinning reels!
play aviator
Here, you can access lots of casino slots from top providers.
Players can enjoy classic slots as well as new-generation slots with vivid animation and interactive gameplay.
Even if you’re new or a seasoned gamer, there’s something for everyone.
play casino
Each title are ready to play round the clock and designed for desktop computers and tablets alike.
All games run in your browser, so you can jump into the action right away.
Platform layout is intuitive, making it convenient to browse the collection.
Sign up today, and enjoy the excitement of spinning reels!
slot casino
Here, you can find a great variety of online slots from leading developers.
Players can enjoy retro-style games as well as new-generation slots with stunning graphics and interactive gameplay.
Even if you’re new or a seasoned gamer, there’s a game that fits your style.
money casino
The games are ready to play 24/7 and compatible with desktop computers and mobile devices alike.
All games run in your browser, so you can jump into the action right away.
The interface is intuitive, making it quick to find your favorite slot.
Sign up today, and discover the excitement of spinning reels!
casino
This website, you can find a great variety of online slots from leading developers.
Users can experience traditional machines as well as new-generation slots with high-quality visuals and bonus rounds.
Even if you’re new or an experienced player, there’s a game that fits your style.
play aviator
Each title are instantly accessible 24/7 and optimized for laptops and smartphones alike.
No download is required, so you can get started without hassle.
The interface is user-friendly, making it convenient to find your favorite slot.
Sign up today, and dive into the world of online slots!
Davidcek
The site allows off-road vehicle rentals across the island.
Anyone can conveniently reserve a ride for fun.
When you’re looking to explore coastal trails, a buggy is the perfect way to do it.
https://unsplash.com/@buggycrete
The fleet are safe and clean and offered in custom bookings.
On this platform is hassle-free and comes with affordable prices.
Get ready to ride and feel Crete in full freedom.
casino
This website, you can access a wide selection of online slots from top providers.
Players can enjoy classic slots as well as feature-packed games with stunning graphics and exciting features.
Whether you’re a beginner or a casino enthusiast, there’s a game that fits your style.
casino games
The games are ready to play round the clock and optimized for desktop computers and mobile devices alike.
You don’t need to install anything, so you can get started without hassle.
The interface is intuitive, making it convenient to find your favorite slot.
Join the fun, and dive into the world of online slots!
Davidcek
This website offers buggy rentals throughout Crete.
You can quickly book a ride for fun.
Whether you’re looking to explore coastal trails, a buggy is the exciting way to do it.
https://rentry.co/rmwfrtvu
Each buggy are regularly serviced and offered in custom bookings.
On this platform is user-friendly and comes with clear terms.
Get ready to ride and enjoy Crete in full freedom.
casino slots
This website, you can access a wide selection of casino slots from top providers.
Players can experience traditional machines as well as modern video slots with stunning graphics and interactive gameplay.
Even if you’re new or an experienced player, there’s something for everyone.
money casino
Each title are ready to play round the clock and compatible with PCs and tablets alike.
You don’t need to install anything, so you can jump into the action right away.
The interface is intuitive, making it simple to browse the collection.
Sign up today, and dive into the thrill of casino games!
play aviator
Here, you can access a wide selection of online slots from top providers.
Players can experience classic slots as well as feature-packed games with stunning graphics and bonus rounds.
Even if you’re new or an experienced player, there’s a game that fits your style.
money casino
Each title are ready to play 24/7 and compatible with laptops and smartphones alike.
No download is required, so you can start playing instantly.
The interface is intuitive, making it simple to find your favorite slot.
Sign up today, and discover the world of online slots!
Davidcek
This service features buggy hire on Crete.
You can easily book a vehicle for travel.
In case you’re looking to see natural spots, a buggy is the fun way to do it.
https://www.provenexpert.com/buggycrete/
All vehicles are safe and clean and can be rented for full-day bookings.
Using this website is simple and comes with no hidden fees.
Start your journey and feel Crete on your own terms.
Davidcek
This service allows buggy hire throughout Crete.
You can quickly reserve a buggy for exploration.
Whether you’re looking to discover mountain roads, a buggy is the perfect way to do it.
https://www.tumblr.com/sneakerizer/781689118337990656/alligator-buggy-quad-safari-redefining-off-road
Each buggy are regularly serviced and offered with flexible rentals.
On this platform is fast and comes with affordable prices.
Get ready to ride and enjoy Crete on your own terms.
Davidcek
This website features off-road vehicle rentals on Crete.
You can easily rent a machine for exploration.
Whether you’re looking to travel around coastal trails, a buggy is the exciting way to do it.
https://linktr.ee/buggycrete
Each buggy are regularly serviced and offered in custom bookings.
On this platform is fast and comes with great support.
Start your journey and discover Crete from a new angle.
Davidcek
The site provides buggy hire on the island of Crete.
Visitors can safely arrange a buggy for exploration.
Whether you’re looking to discover hidden beaches, a buggy is the fun way to do it.
https://www.reddit.com/user/BuggyCrete/
Our rides are ready to go and offered with flexible schedules.
Through our service is simple and comes with great support.
Start your journey and enjoy Crete like never before.
Davidcek
This website allows buggy rentals on the island of Crete.
You can easily arrange a machine for travel.
When you’re looking to discover natural spots, a buggy is the ideal way to do it.
https://www.tumblr.com/sneakerizer/781689118337990656/alligator-buggy-quad-safari-redefining-off-road
Our rides are regularly serviced and available for daily schedules.
Booking through this site is simple and comes with clear terms.
Start your journey and feel Crete in full freedom.
Davidcek
The site offers buggy hire across the island.
Anyone can quickly arrange a machine for travel.
When you’re looking to see natural spots, a buggy is the perfect way to do it.
https://buggycrete.livejournal.com/
Our rides are regularly serviced and can be rented for full-day rentals.
Booking through this site is fast and comes with affordable prices.
Begin the adventure and experience Crete on your own terms.
Davidcek
The site features off-road vehicle rentals on Crete.
Visitors can safely reserve a vehicle for travel.
In case you’re looking to travel around coastal trails, a buggy is the fun way to do it.
https://pixabay.com/users/buggycrete-49906515/
Our rides are safe and clean and offered in custom schedules.
Through our service is simple and comes with affordable prices.
Hit the trails and enjoy Crete in full freedom.
страховка для путешествий
Оформление страхового полиса при выезде за границу — это важный шаг для обеспечения безопасности путешественника.
Документ покрывает неотложную помощь в случае несчастного случая за границей.
Помимо этого, полис может предусматривать оплату на транспортировку.
страховка для путешествий
Определённые государства требуют оформление полиса для пересечения границы.
Если нет страховки медицинские расходы могут привести к большим затратам.
Оформление полиса перед выездом
страховка для путешествий
Оформление медицинской страховки для заграничной поездки — это важный шаг для защиты здоровья отдыхающего.
Страховка гарантирует неотложную помощь в случае заболевания за границей.
Помимо этого, документ может предусматривать оплату на репатриацию.
полис каско
Определённые государства предусматривают предъявление страховки для пересечения границы.
Без страховки обращение к врачу могут обойтись дорого.
Получение сертификата до поездки
полис каско
Покупка страховки перед поездкой за рубеж — это важный шаг для защиты здоровья отдыхающего.
Полис гарантирует неотложную помощь в случае несчастного случая за границей.
Помимо этого, документ может предусматривать компенсацию на возвращение домой.
осаго
Определённые государства настаивают на предъявление страховки для въезда.
При отсутствии полиса лечение могут привести к большим затратам.
Приобретение документа заблаговременно
расчет каско
Наличие страхового полиса перед поездкой за рубеж — это обязательное условие для обеспечения безопасности отдыхающего.
Документ обеспечивает неотложную помощь в случае травмы за границей.
Также, страховка может охватывать компенсацию на возвращение домой.
мед страховка для поездки за границу
Некоторые государства обязывают наличие страховки для получения визы.
Без наличия документа медицинские расходы могут стать дорогими.
Приобретение документа перед выездом
каско
Наличие туристического полиса для заграничной поездки — это разумное решение для обеспечения безопасности путешественника.
Документ включает медицинскую помощь в случае травмы за границей.
Помимо этого, сертификат может обеспечивать возмещение затрат на возвращение домой.
мед страховка для выезда за рубеж
Некоторые государства требуют наличие страховки для пересечения границы.
Если нет страховки госпитализация могут быть финансово обременительными.
Покупка страховки перед выездом
carbox30.ru
Оформление туристического полиса при выезде за границу — это важный шаг для обеспечения безопасности отдыхающего.
Страховка гарантирует расходы на лечение в случае обострения болезни за границей.
К тому же, страховка может охватывать компенсацию на медицинскую эвакуацию.
мед страховка для выезда за рубеж
Многие страны требуют предоставление документа для пересечения границы.
Без страховки медицинские расходы могут обойтись дорого.
Приобретение документа до поездки
страховка осаго
Приобретение страхового полиса во время путешествия — это разумное решение для обеспечения безопасности туриста.
Страховка покрывает неотложную помощь в случае несчастного случая за границей.
Помимо этого, страховка может включать оплату на возвращение домой.
расчет каско
Многие страны предусматривают предоставление документа для пересечения границы.
При отсутствии полиса госпитализация могут обойтись дорого.
Приобретение документа перед выездом
icforce.ru
Покупка туристического полиса перед поездкой за рубеж — это обязательное условие для спокойствия отдыхающего.
Страховка обеспечивает медицинские услуги в случае травмы за границей.
Также, сертификат может охватывать компенсацию на транспортировку.
страховка осаго
Некоторые государства предусматривают предоставление документа для получения визы.
Без наличия документа обращение к врачу могут обойтись дорого.
Оформление полиса до поездки
страховка за рубеж
Приобретение страховки для заграничной поездки — это разумное решение для спокойствия путешественника.
Документ обеспечивает неотложную помощь в случае обострения болезни за границей.
Также, сертификат может предусматривать компенсацию на транспортировку.
каско
Многие страны предусматривают предъявление страховки для получения визы.
Если нет страховки госпитализация могут быть финансово обременительными.
Покупка страховки заблаговременно
осаго рассчитать
Оформление медицинской страховки перед поездкой за рубеж — это разумное решение для защиты здоровья путешественника.
Сертификат обеспечивает неотложную помощь в случае обострения болезни за границей.
К тому же, страховка может охватывать возмещение затрат на медицинскую эвакуацию.
осаго рассчитать
Некоторые государства требуют предоставление документа для въезда.
Без страховки лечение могут быть финансово обременительными.
Получение сертификата перед выездом
страховка автомобиля
Наличие страховки для заграничной поездки — это важный шаг для финансовой защиты отдыхающего.
Сертификат включает неотложную помощь в случае травмы за границей.
Также, полис может включать компенсацию на возвращение домой.
carbox30.ru
Многие страны настаивают на предъявление страховки для получения визы.
Если нет страховки госпитализация могут привести к большим затратам.
Покупка страховки до поездки
страховка для путешествий
Покупка туристического полиса перед поездкой за рубеж — это обязательное условие для финансовой защиты туриста.
Документ включает медицинские услуги в случае травмы за границей.
Помимо этого, сертификат может охватывать возмещение затрат на транспортировку.
страховка для путешествий
Многие страны настаивают на наличие страховки для пересечения границы.
Без наличия документа обращение к врачу могут стать дорогими.
Получение сертификата заблаговременно
страховка осаго
Наличие страхового полиса для заграничной поездки — это разумное решение для обеспечения безопасности туриста.
Сертификат покрывает расходы на лечение в случае заболевания за границей.
К тому же, страховка может обеспечивать оплату на транспортировку.
е осаго
Многие страны обязывают наличие страховки для въезда.
Без наличия документа лечение могут быть финансово обременительными.
Покупка страховки перед выездом
carbox30.ru
Оформление медицинской страховки для заграничной поездки — это обязательное условие для защиты здоровья отдыхающего.
Страховка включает расходы на лечение в случае травмы за границей.
К тому же, документ может охватывать компенсацию на транспортировку.
е осаго
Определённые государства предусматривают предоставление документа для пересечения границы.
Без страховки госпитализация могут стать дорогими.
Получение сертификата заблаговременно
страховка осаго
Покупка страховки во время путешествия — это необходимая мера для спокойствия гражданина.
Сертификат включает медицинскую помощь в случае травмы за границей.
Помимо этого, документ может предусматривать покрытие расходов на возвращение домой.
е осаго
Некоторые государства настаивают на предоставление документа для получения визы.
Если нет страховки медицинские расходы могут стать дорогими.
Покупка страховки заблаговременно
radio alarm clock with cd player
This page offers multifunctional timepieces from trusted manufacturers.
Here you’ll discover sleek CD units with digital radio and dual wake options.
Each clock include AUX jacks, charging capability, and memory backup.
This collection spans budget-friendly options to high-end designs.
best cd alarm clock radio
Every model offer snooze buttons, rest timers, and digital displays.
Buy now are available via Walmart with free delivery.
Select your ultimate wake-up solution for bedroom or office use.
CharlesCox
Лето 2025 года обещает быть насыщенным и нестандартным в плане моды.
В тренде будут свободные силуэты и игра фактур.
Цветовая палитра включают в себя чистые базовые цвета, создающие настроение.
Особое внимание дизайнеры уделяют тканям, среди которых популярны объёмные украшения.
https://www.astrobin.com/users/LePodium/
Опять актуальны элементы 90-х, в свежем прочтении.
На улицах мегаполисов уже можно увидеть захватывающие образы, которые поражают.
Будьте в курсе, чтобы создать свой образ.
CharlesCox
Новый летний период обещает быть насыщенным и оригинальным в плане моды.
В тренде будут натуральные ткани и яркие акценты.
Актуальные тона включают в себя природные тона, сочетающиеся с любым стилем.
Особое внимание дизайнеры уделяют деталям, среди которых популярны объёмные украшения.
https://rentry.co/9fw8degk
Набирают популярность элементы ретро-стиля, интерпретированные по-новому.
В новых коллекциях уже можно увидеть модные эксперименты, которые удивляют.
Экспериментируйте со стилем, чтобы чувствовать себя уверенно.
CharlesCox
Текущий модный сезон обещает быть непредсказуемым и инновационным в плане моды.
В тренде будут многослойность и минимализм с изюминкой.
Актуальные тона включают в себя чистые базовые цвета, выделяющие образ.
Особое внимание дизайнеры уделяют принтам, среди которых популярны плетёные элементы.
https://mvmedia.ru/
Набирают популярность элементы ретро-стиля, в современной обработке.
В новых коллекциях уже можно увидеть захватывающие образы, которые вдохновляют.
Не упустите шанс, чтобы вписаться в тренды.
CharlesCox
Текущий модный сезон обещает быть стильным и инновационным в плане моды.
В тренде будут многослойность и неожиданные сочетания.
Гамма оттенков включают в себя природные тона, выделяющие образ.
Особое внимание дизайнеры уделяют аксессуарам, среди которых популярны объёмные украшения.
https://enkling.com/post/10658_new-arrivals-fendi-prada-chanel-balencuaga-https-lepodium-ru.html
Опять актуальны элементы модерна, в современной обработке.
На подиумах уже можно увидеть модные эксперименты, которые удивляют.
Будьте в курсе, чтобы встретить лето стильно.
CharlesCox
Текущий модный сезон обещает быть непредсказуемым и экспериментальным в плане моды.
В тренде будут натуральные ткани и яркие акценты.
Модные цвета включают в себя чистые базовые цвета, сочетающиеся с любым стилем.
Особое внимание дизайнеры уделяют деталям, среди которых популярны плетёные элементы.
https://telegra.ph/5-luchshih-sumok-Coccinelle-na-ehtu-vesnu-03-31
Возвращаются в моду элементы ретро-стиля, в свежем прочтении.
В новых коллекциях уже можно увидеть смелые решения, которые поражают.
Следите за обновлениями, чтобы вписаться в тренды.
CharlesCox
Лето 2025 года обещает быть непредсказуемым и инновационным в плане моды.
В тренде будут свободные силуэты и яркие акценты.
Актуальные тона включают в себя мягкие пастели, выделяющие образ.
Особое внимание дизайнеры уделяют тканям, среди которых популярны макросумки.
https://ekbtoday.ru/
Возвращаются в моду элементы ретро-стиля, через призму сегодняшнего дня.
На подиумах уже можно увидеть трендовые образы, которые удивляют.
Не упустите шанс, чтобы чувствовать себя уверенно.
CharlesCox
Текущий модный сезон обещает быть насыщенным и нестандартным в плане моды.
В тренде будут натуральные ткани и минимализм с изюминкой.
Актуальные тона включают в себя неоновые оттенки, выделяющие образ.
Особое внимание дизайнеры уделяют деталям, среди которых популярны объёмные украшения.
http://support-groups.org/viewtopic.php?f=161&t=686469
Опять актуальны элементы 90-х, через призму сегодняшнего дня.
В стритстайле уже можно увидеть модные эксперименты, которые вдохновляют.
Экспериментируйте со стилем, чтобы создать свой образ.
CharlesCox
Лето 2025 года обещает быть насыщенным и инновационным в плане моды.
В тренде будут асимметрия и минимализм с изюминкой.
Актуальные тона включают в себя чистые базовые цвета, выделяющие образ.
Особое внимание дизайнеры уделяют принтам, среди которых популярны плетёные элементы.
https://community.nationalgeographic.org/members/profile?UserKey=2c1d99fa-bc4f-4485-aff2-0192bd1e3778
Возвращаются в моду элементы нулевых, через призму сегодняшнего дня.
В стритстайле уже можно увидеть захватывающие образы, которые удивляют.
Будьте в курсе, чтобы встретить лето стильно.
CharlesCox
Текущий модный сезон обещает быть ярким и экспериментальным в плане моды.
В тренде будут свободные силуэты и минимализм с изюминкой.
Модные цвета включают в себя неоновые оттенки, подчеркивающие индивидуальность.
Особое внимание дизайнеры уделяют аксессуарам, среди которых популярны винтажные очки.
https://adventurejobs.co/author/lepodium/
Опять актуальны элементы ретро-стиля, в современной обработке.
На улицах мегаполисов уже можно увидеть модные эксперименты, которые поражают.
Не упустите шанс, чтобы чувствовать себя уверенно.
CharlesCox
Текущий модный сезон обещает быть ярким и экспериментальным в плане моды.
В тренде будут натуральные ткани и яркие акценты.
Модные цвета включают в себя чистые базовые цвета, сочетающиеся с любым стилем.
Особое внимание дизайнеры уделяют аксессуарам, среди которых популярны плетёные элементы.
https://www.goldderby.com/members/lepodium/
Возвращаются в моду элементы ретро-стиля, через призму сегодняшнего дня.
На подиумах уже можно увидеть модные эксперименты, которые вдохновляют.
Экспериментируйте со стилем, чтобы создать свой образ.
ErickGuing
Analog watches will consistently be relevant.
They reflect engineering excellence and showcase a sense of artistry that digital devices simply don’t replicate.
Each piece is powered by fine movements, making it both useful and elegant.
Watch enthusiasts appreciate the craft behind them.
https://www.pittsburghtribune.org/read-blog/123106_chasy-hamilton-amerikanskoe-nasledie-s-shvejcarskoj-tochnostyu.html
Wearing a mechanical watch is not just about practicality, but about honoring history.
Their designs are classic, often passed from father to son.
To sum up, mechanical watches will remain icons.
ErickGuing
Traditional timepieces will consistently be timeless.
They embody tradition and offer a human touch that digital devices simply fail to offer.
A single watch is powered by precision mechanics, making it both reliable and elegant.
Aficionados admire the hand-assembled parts.
https://social.sktorrent.eu/read-blog/2055
Wearing a mechanical watch is not just about telling time, but about celebrating tradition.
Their styles are iconic, often passed from generation to generation.
All in all, mechanical watches will never go out of style.
ErickGuing
Analog watches will consistently be relevant.
They embody tradition and showcase a mechanical beauty that smartwatches simply cannot match.
These watches is powered by precision mechanics, making it both reliable and elegant.
Timepiece lovers value the hand-assembled parts.
https://telegra.ph/The-Timeless-Elegance-Exploring-the-10-Most-Popular-Luxury-Watch-Brands-in-Dubai-03-07
Wearing a mechanical watch is not just about telling time, but about expressing identity.
Their aesthetics are classic, often passed from father to son.
In short, mechanical watches will remain icons.
ErickGuing
Analog watches will forever stay in style.
They reflect tradition and offer a mechanical beauty that digital devices simply cannot match.
Each piece is powered by precision mechanics, making it both functional and sophisticated.
Aficionados cherish the hand-assembled parts.
http://www.mizmiz.de/read-blog/31120
Wearing a mechanical watch is not just about checking hours, but about honoring history.
Their shapes are everlasting, often passed from generation to generation.
All in all, mechanical watches will never go out of style.
ErickGuing
Mechanical watches will always remain relevant.
They represent heritage and showcase a level of detail that tech-based options simply cannot match.
These watches is powered by precision mechanics, making it both functional and inspiring.
Aficionados admire the manual winding.
https://sites.google.com/view/aplover
Wearing a mechanical watch is not just about telling time, but about honoring history.
Their aesthetics are everlasting, often passed from father to son.
All in all, mechanical watches will remain icons.
ErickGuing
Mechanical watches will continue to be fashionable.
They embody engineering excellence and deliver a mechanical beauty that smartwatches simply lack.
A single watch is powered by fine movements, making it both functional and artistic.
Aficionados value the craft behind them.
https://rentry.co/5owgbezt
Wearing a mechanical watch is not just about utility, but about celebrating tradition.
Their shapes are everlasting, often passed from father to son.
Ultimately, mechanical watches will stand the test of time.
ErickGuing
Analog watches will forever stay relevant.
They reflect engineering excellence and showcase a level of detail that smartwatches simply don’t replicate.
Every model is powered by fine movements, making it both reliable and sophisticated.
Timepiece lovers admire the craft behind them.
https://thestylehitch.com/read-blog/17727
Wearing a mechanical watch is not just about telling time, but about making a statement.
Their aesthetics are iconic, often passed from father to son.
In short, mechanical watches will remain icons.
ErickGuing
Analog watches will consistently be timeless.
They represent heritage and provide a sense of artistry that tech-based options simply fail to offer.
Each piece is powered by complex gears, making it both accurate and sophisticated.
Aficionados value the intricate construction.
https://linktr.ee/MaxBezelAudemarsPiguet
Wearing a mechanical watch is not just about utility, but about making a statement.
Their styles are timeless, often passed from lifetime to legacy.
To sum up, mechanical watches will remain icons.
ErickGuing
Analog watches will continue to be relevant.
They embody heritage and offer a sense of artistry that tech-based options simply don’t replicate.
Every model is powered by fine movements, making it both accurate and elegant.
Collectors admire the intricate construction.
https://www.tumblr.com/sneakerizer/777973815932338176/the-best-places-to-buy-luxury-watches-in-doha-a
Wearing a mechanical watch is not just about telling time, but about making a statement.
Their shapes are timeless, often passed from father to son.
All in all, mechanical watches will remain icons.
hitman for hire
This website lets you find specialists for short-term dangerous jobs.
Users can quickly schedule support for specialized requirements.
All listed individuals are experienced in managing complex tasks.
rent a killer
Our platform ensures private interactions between clients and freelancers.
If you require immediate help, the site is the perfect place.
List your task and find a fit with the right person in minutes!
hitman for hire
This platform allows you to connect with specialists for temporary risky tasks.
Clients may quickly schedule services for unique needs.
All listed individuals have expertise in handling sensitive tasks.
hitman-assassin-killer.com
This site guarantees secure interactions between users and freelancers.
Whether you need fast support, this website is the right choice.
Submit a task and find a fit with a professional today!
hire a hitman
The site offers you the chance to connect with experts for short-term hazardous projects.
Visitors are able to easily set up services for specialized needs.
Each professional have expertise in handling sensitive operations.
rent a killer
This service offers safe connections between users and contractors.
If you require fast support, this platform is the perfect place.
List your task and connect with a skilled worker today!
hire a killer
This platform makes it possible to get in touch with specialists for one-time hazardous missions.
Visitors are able to easily arrange support for specific situations.
All contractors are trained in dealing with intense activities.
hitman for hire
The website guarantees private arrangements between users and contractors.
When you need fast support, this website is here for you.
Create a job and match with an expert now!
hitman-assassin-killer.com
This website lets you find experts for occasional hazardous jobs.
Visitors are able to securely arrange services for unique situations.
Each professional are trained in dealing with sensitive activities.
hitman-assassin-killer.com
This site offers safe communication between employers and specialists.
When you need a quick solution, the site is the perfect place.
Create a job and find a fit with a skilled worker now!
hire a killer
This platform allows you to find workers for short-term risky tasks.
Users can efficiently schedule help for specialized needs.
All listed individuals are qualified in managing sensitive operations.
hitman-assassin-killer.com
The website ensures discreet connections between users and freelancers.
For those needing urgent assistance, the site is ready to help.
Submit a task and match with a professional in minutes!
hitman-assassin-killer.com
This platform makes it possible to get in touch with workers for occasional dangerous jobs.
Visitors are able to easily request support for specific needs.
Each professional are qualified in executing complex tasks.
hitman-assassin-killer.com
This service guarantees safe interactions between employers and freelancers.
For those needing immediate help, this website is the perfect place.
List your task and get matched with a skilled worker in minutes!
rent a hitman
The site makes it possible to get in touch with specialists for one-time hazardous jobs.
Clients may securely request assistance for particular requirements.
All listed individuals are qualified in dealing with intense operations.
hitman-assassin-killer.com
Our platform ensures discreet arrangements between employers and specialists.
Whether you need fast support, our service is the perfect place.
Submit a task and connect with a skilled worker today!
hitman-assassin-killer.com
The site makes it possible to connect with professionals for short-term dangerous projects.
Visitors are able to quickly arrange assistance for unique operations.
All workers have expertise in handling complex activities.
hitman-assassin-killer.com
Our platform offers secure arrangements between requesters and specialists.
Whether you need fast support, our service is the perfect place.
Submit a task and match with the right person now!
hire a killer
This platform makes it possible to hire experts for temporary risky missions.
Visitors are able to easily set up assistance for particular operations.
All listed individuals are experienced in executing intense activities.
hitman-assassin-killer.com
Our platform offers private connections between requesters and workers.
When you need immediate help, the site is here for you.
Submit a task and find a fit with a skilled worker now!
sonsofanarchy-italia.com
La nostra piattaforma consente l’assunzione di operatori per attività a rischio.
Gli utenti possono selezionare candidati qualificati per operazioni isolate.
Le persone disponibili vengono verificati con cura.
assumere un killer
Attraverso il portale è possibile visualizzare profili prima della scelta.
La fiducia resta al centro del nostro servizio.
Esplorate le offerte oggi stesso per ottenere aiuto specializzato!
ordina omicidio
Il nostro servizio offre la selezione di operatori per lavori pericolosi.
Gli utenti possono trovare professionisti specializzati per operazioni isolate.
Ogni candidato vengono scelti secondo criteri di sicurezza.
sonsofanarchy-italia.com
Sul sito è possibile leggere recensioni prima della selezione.
La sicurezza è un nostro impegno.
Esplorate le offerte oggi stesso per ottenere aiuto specializzato!
sonsofanarchy-italia.com
Questa pagina rende possibile il reclutamento di operatori per attività a rischio.
I clienti possono selezionare candidati qualificati per incarichi occasionali.
Gli operatori proposti vengono verificati secondo criteri di sicurezza.
ordina omicidio
Attraverso il portale è possibile visualizzare profili prima della scelta.
La qualità resta un nostro valore fondamentale.
Iniziate la ricerca oggi stesso per ottenere aiuto specializzato!
assumere un killer
Il nostro servizio consente l’ingaggio di professionisti per compiti delicati.
I clienti possono scegliere operatori competenti per missioni singole.
Tutti i lavoratori vengono verificati con cura.
sonsofanarchy-italia.com
Utilizzando il servizio è possibile visualizzare profili prima della selezione.
La qualità rimane la nostra priorità.
Iniziate la ricerca oggi stesso per ottenere aiuto specializzato!
sonsofanarchy-italia.com
La nostra piattaforma offre la selezione di persone per attività a rischio.
Gli utenti possono trovare candidati qualificati per operazioni isolate.
Gli operatori proposti sono selezionati con attenzione.
assumi assassino
Con il nostro aiuto è possibile visualizzare profili prima di procedere.
La fiducia resta un nostro valore fondamentale.
Contattateci oggi stesso per trovare il supporto necessario!
assumi un sicario
Il nostro servizio permette il reclutamento di professionisti per incarichi rischiosi.
I clienti possono ingaggiare operatori competenti per lavori una tantum.
Tutti i lavoratori sono selezionati con cura.
ordina l’uccisione
Attraverso il portale è possibile consultare disponibilità prima della selezione.
La fiducia è la nostra priorità.
Contattateci oggi stesso per trovare il supporto necessario!
sonsofanarchy-italia.com
Questa pagina consente l’ingaggio di professionisti per incarichi rischiosi.
Gli interessati possono trovare esperti affidabili per missioni singole.
Gli operatori proposti sono selezionati con attenzione.
assumere un killer
Utilizzando il servizio è possibile visualizzare profili prima della selezione.
La fiducia rimane al centro del nostro servizio.
Sfogliate i profili oggi stesso per portare a termine il vostro progetto!
ordina omicidio
Questa pagina consente la selezione di persone per incarichi rischiosi.
Gli interessati possono ingaggiare operatori competenti per operazioni isolate.
Le persone disponibili sono valutati con severi controlli.
ordina l’uccisione
Attraverso il portale è possibile ottenere informazioni dettagliate prima di assumere.
La professionalità resta un nostro impegno.
Sfogliate i profili oggi stesso per trovare il supporto necessario!
ordina omicidio l'uccisione
Il nostro servizio consente il reclutamento di professionisti per incarichi rischiosi.
Chi cerca aiuto possono selezionare operatori competenti per incarichi occasionali.
Le persone disponibili vengono scelti secondo criteri di sicurezza.
sonsofanarchy-italia.com
Con il nostro aiuto è possibile visualizzare profili prima di assumere.
La professionalità resta al centro del nostro servizio.
Iniziate la ricerca oggi stesso per trovare il supporto necessario!
sonsofanarchy-italia.com
Il nostro servizio rende possibile il reclutamento di persone per attività a rischio.
Chi cerca aiuto possono trovare candidati qualificati per operazioni isolate.
Tutti i lavoratori vengono verificati con cura.
assumere un killer
Attraverso il portale è possibile ottenere informazioni dettagliate prima di assumere.
La professionalità resta al centro del nostro servizio.
Contattateci oggi stesso per affrontare ogni sfida in sicurezza!
зеркало 1xbet
На этом сайте вы можете обнаружить актуальное зеркало 1 икс бет без ограничений.
Оперативно обновляем доступы, чтобы обеспечить беспрепятственный доступ к порталу.
Работая через альтернативный адрес, вы сможете участвовать в играх без перебоев.
1xbet-official.live
Наш сайт облегчит доступ вам моментально перейти на актуальный адрес 1хБет.
Мы следим за тем, чтобы каждый пользователь имел возможность работать без перебоев.
Следите за обновлениями, чтобы всегда быть онлайн с 1хБет!
1xbet зеркало
На данной странице вы можете обнаружить актуальное зеркало 1xBet без трудностей.
Постоянно обновляем зеркала, чтобы обеспечить стабильную работу к платформе.
Используя зеркало, вы сможете получать весь функционал без задержек.
зеркало 1хбет
Наш сайт позволит вам безопасно получить рабочее зеркало 1xBet.
Мы заботимся, чтобы все клиенты был в состоянии использовать все возможности.
Не пропустите обновления, чтобы не терять доступ с 1xBet!
зеркало 1xbet
На данной странице вы можете найти действующее зеркало 1 икс бет без ограничений.
Мы регулярно обновляем адреса, чтобы обеспечить беспрепятственный доступ к платформе.
Открывая резервную копию, вы сможете участвовать в играх без рисков.
1xbet-official.live
Наш ресурс поможет вам без труда открыть актуальный адрес 1xBet.
Нам важно, чтобы каждый пользователь смог работать без перебоев.
Следите за обновлениями, чтобы всегда оставаться в игре с 1хБет!
зеркало 1хбет
На этом сайте вы можете обнаружить актуальное зеркало 1xBet без блокировок.
Систематически обновляем зеркала, чтобы обеспечить свободное подключение к ресурсу.
Работая через альтернативный адрес, вы сможете получать весь функционал без перебоев.
зеркало 1хбет
Наш сайт облегчит доступ вам моментально перейти на актуальный адрес 1 икс бет.
Нам важно, чтобы каждый посетитель мог использовать все возможности.
Не пропустите обновления, чтобы не терять доступ с 1хБет!
зеркало 1хбет
В этом разделе вы можете получить действующее зеркало 1 икс бет без блокировок.
Постоянно обновляем адреса, чтобы гарантировать стабильную работу к сайту.
Работая через альтернативный адрес, вы сможете получать весь функционал без задержек.
зеркало 1хбет
Наш сайт обеспечит возможность вам быстро найти новую ссылку 1хБет.
Мы стремимся, чтобы каждый посетитель мог не испытывать проблем.
Не пропустите обновления, чтобы быть на связи с 1xBet!
зеркало 1хбет
В этом разделе вы можете обнаружить свежую ссылку 1xBet без ограничений.
Постоянно обновляем ссылки, чтобы гарантировать непрерывный вход к порталу.
Работая через альтернативный адрес, вы сможете участвовать в играх без задержек.
зеркало 1xbet
Наш сайт обеспечит возможность вам безопасно получить актуальный адрес 1xBet.
Мы следим за тем, чтобы все клиенты мог не испытывать проблем.
Не пропустите обновления, чтобы всегда оставаться в игре с 1 икс бет!
зеркало 1xbet
На нашем ресурсе вы можете получить актуальное зеркало 1 икс бет без трудностей.
Постоянно обновляем зеркала, чтобы облегчить свободное подключение к сайту.
Используя зеркало, вы сможете делать ставки без ограничений.
1xbet-official.live
Наш ресурс обеспечит возможность вам безопасно получить рабочее зеркало 1xBet.
Мы стремимся, чтобы каждый пользователь смог работать без перебоев.
Проверяйте новые ссылки, чтобы не терять доступ с 1хБет!
1xbet-official.live
На этом сайте вы можете обнаружить актуальное зеркало 1 икс бет без проблем.
Постоянно обновляем адреса, чтобы облегчить свободное подключение к ресурсу.
Переходя через зеркало, вы сможете делать ставки без задержек.
1xbet-official.live
Наш сайт поможет вам моментально перейти на свежее зеркало 1хБет.
Мы стремимся, чтобы все клиенты был в состоянии получить полный доступ.
Проверяйте новые ссылки, чтобы всегда быть онлайн с 1хбет!
зеркало 1хбет
В этом разделе вы можете получить рабочую копию сайта 1хбет без ограничений.
Постоянно обновляем ссылки, чтобы обеспечить непрерывный вход к сайту.
Переходя через зеркало, вы сможете участвовать в играх без перебоев.
1хбет зеркало
Наш сайт поможет вам моментально перейти на новую ссылку 1xBet.
Мы следим за тем, чтобы все клиенты смог использовать все возможности.
Не пропустите обновления, чтобы всегда оставаться в игре с 1 икс бет!
зеркало 1xbet
На данной странице вы можете получить рабочую копию сайта 1хБет без трудностей.
Систематически обновляем адреса, чтобы обеспечить стабильную работу к сайту.
Используя зеркало, вы сможете получать весь функционал без задержек.
1хбет зеркало
Наш сайт поможет вам без труда открыть актуальный адрес 1хБет.
Мы следим за тем, чтобы каждый пользователь смог работать без перебоев.
Следите за актуальной информацией, чтобы всегда быть онлайн с 1 икс бет!
зеркало 1xbet
На данной странице вы можете перейти на свежую ссылку 1 икс бет без блокировок.
Мы регулярно обновляем доступы, чтобы гарантировать свободное подключение к сайту.
Переходя через зеркало, вы сможете участвовать в играх без перебоев.
1xbet-official.live
Наш ресурс поможет вам моментально перейти на рабочее зеркало 1хбет.
Нам важно, чтобы все клиенты был в состоянии работать без перебоев.
Проверяйте новые ссылки, чтобы всегда оставаться в игре с 1 икс бет!
боттега венета
Наша платформа — официальный онлайн-магазин Bottega Veneta с отправкой по всей России.
На нашем сайте вы можете заказать оригинальные товары Боттега Венета напрямую.
Любая покупка подтверждены сертификатами от компании.
bottega-official.ru
Доставка осуществляется быстро в любое место России.
Наш сайт предлагает разные варианты платежей и гарантию возврата средств.
Покупайте на официальном сайте Боттега Венета, чтобы получить безупречный сервис!
bottega-official.ru
Эта страница — официальный онлайн-магазин Bottega Veneta с отгрузкой по стране.
У нас вы можете купить брендовые изделия Боттега Венета напрямую.
Все товары подтверждены сертификатами от бренда.
боттега венета цум
Перевозка осуществляется быстро в по всей территории России.
Наш сайт предлагает разные варианты платежей и простую процедуру возврата.
Покупайте на официальном сайте Bottega Veneta, чтобы получить безупречный сервис!
боттега венета цум
Наша платформа — аутентичный онлайн-площадка Боттега Венета с доставлением по РФ.
У нас вы можете оформить заказ на брендовые изделия Боттега Венета официально.
Все товары идут с официальной гарантией от компании.
bottega-official.ru
Доставление осуществляется без задержек в по всей территории России.
Платформа предлагает выгодные условия покупки и лёгкий возврат.
Доверьтесь официальном сайте Bottega Veneta, чтобы чувствовать уверенность в покупке!
bottega-official.ru
Наша платформа — подтверждённый интернет-бутик Bottega Veneta с отгрузкой по всей России.
В нашем магазине вы можете приобрести брендовые изделия Bottega Veneta напрямую.
Любая покупка идут с официальной гарантией от компании.
bottega-official.ru
Отправка осуществляется быстро в любое место России.
Платформа предлагает безопасные способы оплаты и лёгкий возврат.
Выбирайте официальном сайте Боттега Венета, чтобы наслаждаться оригинальными товарами!
bottega-official.ru
Данный ресурс — официальный цифровой магазин Bottega Венета с доставлением по территории России.
На нашем сайте вы можете приобрести оригинальные товары Боттега Венета без посредников.
Каждая покупка имеют гарантию качества от бренда.
bottega-official.ru
Перевозка осуществляется быстро в любой регион России.
Бутик онлайн предлагает выгодные условия покупки и гарантию возврата средств.
Доверьтесь официальном сайте Bottega Veneta, чтобы получить безупречный сервис!
bottega veneta купить
Эта страница — официальный интернет-бутик Боттега Венета с доставлением по всей России.
Через наш портал вы можете заказать оригинальные товары Bottega Veneta официально.
Каждая покупка подтверждаются оригинальными документами от бренда.
боттега венета цум
Перевозка осуществляется быстро в любой регион России.
Бутик онлайн предлагает разные варианты платежей и простую процедуру возврата.
Доверьтесь официальном сайте Боттега Венета, чтобы получить безупречный сервис!
bottega veneta купить
Данный ресурс — официальный онлайн-магазин Боттега Венета с отправкой по стране.
Через наш портал вы можете заказать оригинальные товары Боттега Венета напрямую.
Каждый заказ подтверждаются оригинальными документами от марки.
bottega veneta официальный сайт
Доставка осуществляется оперативно в любое место России.
Платформа предлагает разные варианты платежей и лёгкий возврат.
Доверьтесь официальном сайте Bottega Veneta, чтобы быть уверенным в качестве!
bottega veneta купить
Наша платформа — аутентичный цифровой магазин Bottega Венета с доставкой по всей России.
Через наш портал вы можете заказать брендовые изделия Bottega Veneta с гарантией подлинности.
Каждая покупка подтверждаются оригинальными документами от бренда.
bottega-official.ru
Отправка осуществляется без задержек в любую точку России.
Наш сайт предлагает выгодные условия покупки и лёгкий возврат.
Доверьтесь официальном сайте Боттега Венета, чтобы быть уверенным в качестве!
bottega veneta официальный сайт
Этот сайт — настоящий онлайн-магазин Боттега Венета с доставлением по территории России.
Через наш портал вы можете оформить заказ на фирменную продукцию Боттега Венета официально.
Любая покупка подтверждены сертификатами от марки.
bottega veneta купить
Отправка осуществляется оперативно в любое место России.
Бутик онлайн предлагает выгодные условия покупки и комфортные условия возврата.
Положитесь на официальном сайте Bottega Veneta, чтобы получить безупречный сервис!
如何在网上下令谋杀
在本站,您可以雇佣专门从事特定的高风险任务的专家。
我们集合大量技能娴熟的任务执行者供您选择。
无论面对何种复杂情况,您都可以快速找到理想的帮手。
chinese-hitman-assassin.com
所有任务完成者均经过审核,维护您的利益。
任务平台注重安全,让您的个别项目更加高效。
如果您需要具体流程,请立即联系!
chinese-hitman-assassin.com
在这个网站上,您可以雇佣专门从事一次性的危险工作的专家。
我们汇集大量可靠的从业人员供您选择。
无论是何种复杂情况,您都可以轻松找到胜任的人选。
如何雇佣刺客
所有作业人员均经过背景调查,确保您的机密信息。
平台注重安全,让您的特殊需求更加高效。
如果您需要详细资料,请与我们取得联系!
chinese-hitman-assassin.com
在此页面,您可以联系专门从事特定的危险工作的执行者。
我们提供大量可靠的任务执行者供您选择。
无论面对何种复杂情况,您都可以安全找到理想的帮手。
chinese-hitman-assassin.com
所有合作人员均经过严格甄别,保证您的隐私。
任务平台注重匿名性,让您的危险事项更加高效。
如果您需要服务详情,请随时咨询!
如何雇佣杀手
在此页面,您可以找到专门从事特定的危险工作的专家。
我们整理了大量可靠的从业人员供您选择。
无论需要何种危险需求,您都可以快速找到专业的助手。
chinese-hitman-assassin.com
所有执行者均经过背景调查,确保您的隐私。
服务中心注重匿名性,让您的个别项目更加无忧。
如果您需要详细资料,请与我们取得联系!
如何雇佣刺客
在此页面,您可以聘请专门从事单次的危险任务的人员。
我们集合大量经验丰富的工作人员供您选择。
无论需要何种挑战,您都可以轻松找到胜任的人选。
为了钱而下令谋杀
所有执行者均经过严格甄别,维护您的机密信息。
网站注重匿名性,让您的任务委托更加无忧。
如果您需要更多信息,请立即联系!
如何雇佣杀手
在本站,您可以联系专门从事临时的危险工作的专业人士。
我们提供大量经验丰富的从业人员供您选择。
无论面对何种危险需求,您都可以方便找到胜任的人选。
chinese-hitman-assassin.com
所有合作人员均经过筛选,确保您的机密信息。
网站注重效率,让您的危险事项更加无忧。
如果您需要服务详情,请立即联系!
为了钱而下令谋杀
在此页面,您可以联系专门从事特定的高危工作的人员。
我们汇集大量训练有素的行动专家供您选择。
无论需要何种挑战,您都可以快速找到胜任的人选。
chinese-hitman-assassin.com
所有合作人员均经过筛选,维护您的机密信息。
服务中心注重效率,让您的个别项目更加无忧。
如果您需要详细资料,请与我们取得联系!
chinese-hitman-assassin.com
通过本平台,您可以雇佣专门从事特定的危险工作的人员。
我们提供大量可靠的从业人员供您选择。
无论需要何种挑战,您都可以快速找到理想的帮手。
雇佣一名杀手
所有合作人员均经过筛选,保证您的机密信息。
平台注重专业性,让您的危险事项更加无忧。
如果您需要服务详情,请随时咨询!
chinese-hitman-assassin.com
在本站,您可以聘请专门从事单次的高危工作的人员。
我们集合大量技能娴熟的工作人员供您选择。
无论需要何种危险需求,您都可以安全找到理想的帮手。
如何雇佣杀手
所有合作人员均经过严格甄别,保障您的利益。
平台注重安全,让您的危险事项更加顺利。
如果您需要详细资料,请随时咨询!
如何雇佣杀手
在本站,您可以雇佣专门从事临时的高危工作的人员。
我们整理了大量技能娴熟的从业人员供您选择。
无论面对何种复杂情况,您都可以快速找到理想的帮手。
chinese-hitman-assassin.com
所有合作人员均经过严格甄别,维护您的机密信息。
服务中心注重效率,让您的特殊需求更加顺利。
如果您需要具体流程,请随时咨询!
JosephLer
Here, you can discover different websites for CS:GO betting.
We list a wide range of gaming platforms focused on the CS:GO community.
Every website is handpicked to provide fair play.
csgo gambling site
Whether you’re a CS:GO enthusiast, you’ll quickly choose a platform that fits your style.
Our goal is to make it easy for you to connect with proven CS:GO betting sites.
Check out our list at your convenience and enhance your CS:GO gambling experience!
JosephLer
Here, you can find different platforms for CS:GO gambling.
We have collected a variety of gaming platforms centered around Counter-Strike: Global Offensive.
Each site is handpicked to ensure reliability.
free csgo cases
Whether you’re an experienced gamer, you’ll quickly find a platform that suits your needs.
Our goal is to help you to find the top-rated CS:GO gaming options.
Start browsing our list today and boost your CS:GO betting experience!
JosephLer
At this page, you can browse top CS:GO betting sites.
We have collected a diverse lineup of gaming platforms specialized in the CS:GO community.
Each site is thoroughly reviewed to guarantee safety.
list of csgo gambling sites
Whether you’re an experienced gamer, you’ll easily discover a platform that suits your needs.
Our goal is to help you to enjoy the top-rated CS:GO wagering platforms.
Check out our list now and boost your CS:GO gambling experience!
JosephLer
On this site, you can explore different CS:GO betting sites.
We offer a variety of betting platforms specialized in Counter-Strike: Global Offensive.
These betting options is tested for quality to provide reliability.
csgo skins gambling sites
Whether you’re an experienced gamer, you’ll effortlessly choose a platform that meets your expectations.
Our goal is to make it easy for you to find only the best CS:GO gambling websites.
Check out our list today and elevate your CS:GO gambling experience!
JosephLer
At this page, you can browse trusted CS:GO betting sites.
We have collected a selection of gaming platforms dedicated to the CS:GO community.
Every website is carefully selected to provide reliability.
upgrade skin
Whether you’re an experienced gamer, you’ll effortlessly choose a platform that matches your preferences.
Our goal is to assist you to enjoy only the best CS:GO gaming options.
Explore our list at your convenience and boost your CS:GO gaming experience!
JosephLer
Through this platform, you can explore various platforms for CS:GO gambling.
We feature a selection of gambling platforms centered around the CS:GO community.
Every website is carefully selected to secure safety.
cs2 betting
Whether you’re a CS:GO enthusiast, you’ll easily find a platform that meets your expectations.
Our goal is to help you to find proven CS:GO gaming options.
Start browsing our list right away and upgrade your CS:GO betting experience!
JosephLer
Here, you can browse trusted platforms for CS:GO gambling.
We have collected a variety of betting platforms specialized in CS:GO.
These betting options is thoroughly reviewed to ensure reliability.
csgo gambling list
Whether you’re an experienced gamer, you’ll quickly choose a platform that matches your preferences.
Our goal is to make it easy for you to connect with only the best CS:GO gambling websites.
Check out our list right away and boost your CS:GO gaming experience!
JosephLer
On this site, you can discover various CS:GO betting sites.
We list a selection of betting platforms focused on CS:GO.
Each site is thoroughly reviewed to guarantee fair play.
csgo open cases
Whether you’re new to betting, you’ll effortlessly choose a platform that suits your needs.
Our goal is to help you to access reliable CS:GO gaming options.
Check out our list now and enhance your CS:GO betting experience!
JosephLer
Here, you can discover trusted platforms for CS:GO gambling.
We offer a wide range of wagering platforms specialized in CS:GO players.
Every website is tested for quality to secure trustworthiness.
csgo crash sites
Whether you’re a CS:GO enthusiast, you’ll easily choose a platform that suits your needs.
Our goal is to help you to connect with only the best CS:GO wagering platforms.
Dive into our list right away and enhance your CS:GO gaming experience!
JosephLer
Here, you can discover top CS:GO gaming sites.
We have collected a selection of gaming platforms centered around CS:GO.
Each site is handpicked to guarantee safety.
cs2 gambling roulette
Whether you’re a CS:GO enthusiast, you’ll conveniently select a platform that matches your preferences.
Our goal is to guide you to access only the best CS:GO wagering platforms.
Start browsing our list now and boost your CS:GO gambling experience!
JosephLer
On this site, you can discover trusted websites for CS:GO betting.
We have collected a wide range of gaming platforms centered around CS:GO players.
Each site is handpicked to ensure reliability.
skin gambling sites csgo
Whether you’re a CS:GO enthusiast, you’ll quickly discover a platform that fits your style.
Our goal is to guide you to access the top-rated CS:GO gaming options.
Explore our list now and boost your CS:GO gambling experience!
JosephLer
On this site, you can find various CS:GO betting sites.
We list a wide range of wagering platforms centered around the CS:GO community.
These betting options is carefully selected to secure safety.
csgo team betting
Whether you’re a seasoned bettor, you’ll easily select a platform that meets your expectations.
Our goal is to make it easy for you to enjoy only the best CS:GO gaming options.
Start browsing our list now and elevate your CS:GO gambling experience!
assassin for hire
This website allows you to hire workers for occasional hazardous tasks.
Users can securely arrange assistance for specialized requirements.
All listed individuals have expertise in managing complex tasks.
killer for hire
This service ensures safe interactions between requesters and freelancers.
For those needing immediate help, this platform is the right choice.
Submit a task and match with a skilled worker now!
Samanthamaw
Beautiful phone case, you must have it
Floral Poppy Tough Phone Case for Nature Lovers
Designed by Yuri Khrushch
https://www.amazon.com/Floral-Nature-Lovers-Designed-Khrushch/dp/B0F23G49N7/ref=sr_1_70?dib=eyJ2IjoiMSJ9.Xf5iOyUHsmeP3jHzPCt0Vhw1r97YV3if2mIbQzmBBqHSHqdW7Ew-xEnibR9AUlO-d3TdyZv4n8vatISd0z-akHeuNMuiQuqcilUHXFLIzyPAZNDjXKWUvuO1oGbM9ql_yPsdBwU1OkyCwcojnlwI3WtP2oR6BHaV4S0g9AAOr9w.yz_i1Ao5pH6iqS4vFV-ar2Dv_LS5K0NJDlAAQl_F5Wg&dib_tag=se&keywords=phone&m=A38FMUB1PWNJ6C&qid=1745773517&refresh=1&s=merchant-items&sr=1-70&xpid=c7WLCG0JGMl11
ordina l'uccisione
La nostra piattaforma offre l’ingaggio di persone per attività a rischio.
Gli interessati possono trovare operatori competenti per missioni singole.
Le persone disponibili sono selezionati secondo criteri di sicurezza.
sonsofanarchy-italia.com
Attraverso il portale è possibile visualizzare profili prima di assumere.
La sicurezza resta la nostra priorità.
Esplorate le offerte oggi stesso per ottenere aiuto specializzato!
slot casino
This website, you can access a great variety of online slots from leading developers.
Players can experience retro-style games as well as new-generation slots with stunning graphics and bonus rounds.
Whether you’re a beginner or an experienced player, there’s always a slot to match your mood.
casino games
Each title are ready to play 24/7 and optimized for PCs and tablets alike.
All games run in your browser, so you can start playing instantly.
Platform layout is intuitive, making it simple to explore new games.
Join the fun, and discover the world of online slots!
killer for hire
Our service allows you to connect with professionals for occasional dangerous jobs.
Visitors are able to easily request help for unique requirements.
All listed individuals have expertise in dealing with critical activities.
rent a killer
This service ensures discreet arrangements between employers and workers.
When you need fast support, this website is the perfect place.
Submit a task and find a fit with a skilled worker in minutes!
Samanthamaw
Beautiful phone case, you must have it
Scenic Phone Case – Coastal Village Design by Yuri Khrushch Matte
https://www.amazon.com/Scenic-Phone-Case-Coastal-Khrushch/dp/B0F21T224J/ref=sr_1_21?dib=eyJ2IjoiMSJ9.6dIUBwPr7A22XYTvxJJm6Ev1_pATlzqJi_H_l9ubLwRerCwuqCVQyMqZ2CznqFVVbdO6Lf8j0Ayhvsj9WPODW-nJOdxjrWUwvx_cYkTOvlS0U6ZKouRkNUpd3fYZVNzeNiRM3oPyS3A2EWu5OL8Y9GPW5QdbIfl6GQlkXy1de5n0smX5xxh2-sUQXT6R6HdYux0ZS2mbxVoCZqpRkxse7wFSX8b8V9_z9O2EGFfwvgA.g5FRPxV9o0gUhPJttrSUVUtuKh2HJYuqmZY_GmEFp-8&dib_tag=se&keywords=phone&m=A38FMUB1PWNJ6C&qid=1745910289&s=merchant-items&sr=1-21&xpid=rl1xchb9OouGZ&th=1
1win партнерская программа
Здесь вы сможете найти всю информацию о реферальной системе: 1win.
Представлены все детали партнёрства, критерии вступления и ожидаемые выплаты.
Все части тщательно расписан, что позволяет легко разобраться в аспектах работы.
Также доступны вопросы и ответы и практические указания для начинающих.
Информация регулярно обновляется, поэтому вы доверять в актуальности предоставленных сведений.
Данный сайт окажет поддержку в исследовании партнёрской программы 1Win.
1win партнерская программа
На этом сайте вы обнаружите всю информацию о программе лояльности: 1win партнерская программа.
Представлены все нюансы партнёрства, правила присоединения и ожидаемые выплаты.
Любой блок подробно освещён, что помогает быстро освоить в тонкостях системы.
Также доступны FAQ по теме и практические указания для новичков.
Материалы поддерживаются в актуальном состоянии, поэтому вы доверять в актуальности предоставленных материалов.
Источник поможет в понимании партнёрской программы 1Win.
1win partners
Здесь вы увидите всю информацию о программе лояльности: 1win.
Здесь размещены все детали взаимодействия, критерии вступления и возможные бонусы.
Любой блок детально описан, что делает доступным понять в особенностях процесса.
Кроме того, есть ответы на частые вопросы и рекомендации для первых шагов.
Информация регулярно обновляется, поэтому вы доверять в точности предоставленных материалов.
Данный сайт окажет поддержку в освоении партнёрской программы 1Win.
1win
На этом сайте вы сможете найти полное описание о партнерке: 1win partners.
Представлены все особенности работы, условия участия и возможные поощрения.
Все части подробно освещён, что делает доступным усвоить в тонкостях работы.
Есть также вопросы и ответы и полезные советы для новичков.
Контент дополняется, поэтому вы можете быть уверены в актуальности предоставленных сведений.
Этот ресурс станет вашим надежным помощником в понимании партнёрской программы 1Win.
1win
В данном ресурсе вы сможете найти всю информацию о программе лояльности: 1win partners.
Представлены все аспекты сотрудничества, правила присоединения и возможные поощрения.
Любой блок четко изложен, что позволяет легко усвоить в особенностях работы.
Также доступны ответы на частые вопросы и практические указания для первых шагов.
Контент дополняется, поэтому вы доверять в актуальности предоставленных данных.
Источник поможет в исследовании партнёрской программы 1Win.
1win
Здесь вы обнаружите подробную информацию о программе лояльности: 1win.
Доступны все детали работы, правила присоединения и потенциальные вознаграждения.
Каждый раздел подробно освещён, что позволяет легко понять в особенностях функционирования.
Есть также разъяснения по запросам и подсказки для новичков.
Материалы поддерживаются в актуальном состоянии, поэтому вы можете быть уверены в точности предоставленных сведений.
Данный сайт окажет поддержку в понимании партнёрской программы 1Win.
1win
На этом сайте вы обнаружите исчерпывающие сведения о партнёрской программе: 1win партнерская программа.
У нас представлены все аспекты взаимодействия, условия участия и ожидаемые выплаты.
Все части подробно освещён, что делает доступным разобраться в тонкостях функционирования.
Плюс ко всему, имеются вопросы и ответы и полезные советы для первых шагов.
Материалы поддерживаются в актуальном состоянии, поэтому вы можете быть уверены в достоверности предоставленных материалов.
Портал будет полезен в освоении партнёрской программы 1Win.
1win партнерская программа
Здесь вы обнаружите исчерпывающие сведения о реферальной системе: 1win.
Здесь размещены все детали партнёрства, условия участия и ожидаемые выплаты.
Все части подробно освещён, что даёт возможность просто понять в особенностях работы.
Также доступны ответы на частые вопросы и рекомендации для первых шагов.
Материалы поддерживаются в актуальном состоянии, поэтому вы доверять в актуальности предоставленных сведений.
Данный сайт окажет поддержку в освоении партнёрской программы 1Win.
1win партнерская программа
Здесь вы найдёте всю информацию о реферальной системе: 1win partners.
Здесь размещены все аспекты партнёрства, правила присоединения и возможные поощрения.
Любой блок детально описан, что позволяет легко разобраться в нюансах работы.
Плюс ко всему, имеются разъяснения по запросам и практические указания для начинающих.
Данные актуализируются, поэтому вы доверять в точности предоставленных материалов.
Этот ресурс станет вашим надежным помощником в исследовании партнёрской программы 1Win.
1win партнерская программа
На этом сайте вы обнаружите полное описание о партнерке: 1win.
Доступны все особенности партнёрства, условия участия и возможные бонусы.
Каждый раздел детально описан, что делает доступным разобраться в тонкостях процесса.
Плюс ко всему, имеются разъяснения по запросам и подсказки для новичков.
Материалы поддерживаются в актуальном состоянии, поэтому вы можете быть уверены в актуальности предоставленных сведений.
Данный сайт окажет поддержку в исследовании партнёрской программы 1Win.
slot casino
On this platform, you can discover a great variety of casino slots from top providers.
Players can enjoy retro-style games as well as feature-packed games with stunning graphics and interactive gameplay.
Whether you’re a beginner or a casino enthusiast, there’s a game that fits your style.
casino slots
Each title are ready to play 24/7 and compatible with desktop computers and tablets alike.
You don’t need to install anything, so you can jump into the action right away.
The interface is easy to use, making it simple to browse the collection.
Join the fun, and dive into the world of online slots!
JosephLer
Here, you can discover top CS:GO gaming sites.
We list a variety of wagering platforms dedicated to Counter-Strike: Global Offensive.
All the platforms is thoroughly reviewed to guarantee fair play.
gamepunk cs go skins
Whether you’re an experienced gamer, you’ll effortlessly select a platform that meets your expectations.
Our goal is to help you to connect with the top-rated CS:GO gaming options.
Check out our list right away and boost your CS:GO gambling experience!
1win partners
В этом источнике вы увидите подробную информацию о партнерке: 1win партнерская программа.
Здесь размещены все особенности партнёрства, критерии вступления и возможные бонусы.
Каждый раздел четко изложен, что делает доступным усвоить в нюансах функционирования.
Есть также ответы на частые вопросы и полезные советы для новичков.
Информация регулярно обновляется, поэтому вы доверять в достоверности предоставленных данных.
Ресурс послужит подспорьем в понимании партнёрской программы 1Win.
Stevenboast
?Hola exploradores del azar
Las tiradas gratis sin deposito EspaГ±a son una excelente forma de conocer nuevos juegos. [url=https://100girosgratissindepositoespana.guru/#]tiradas gratis casino sin depГіsito espaГ±a[/url] No tienes que gastar nada para ganar.
Con 100 tiradas gratis, tienes mГЎs oportunidades de ganar sin depositar nada. Empieza sin compromiso y juega tus tragamonedas favoritas. ВЎEs gratis!
Spins gratis sin depГіsito EspaГ±a para slots – http://www.100girosgratissindepositoespana.guru/.
?Que tengas excelentes beneficios !
hitman-assassin-killer.com
This platform offers you the chance to connect with professionals for one-time risky jobs.
You can securely set up assistance for specialized requirements.
All listed individuals are experienced in handling critical activities.
hire a killer
The website provides discreet connections between employers and contractors.
If you require a quick solution, this platform is ready to help.
Post your request and get matched with a skilled worker today!
hitman-assassin-killer.com
This platform lets you get in touch with experts for one-time hazardous missions.
Visitors are able to quickly arrange help for specific needs.
All workers are qualified in executing sensitive activities.
rent a killer
This site guarantees private arrangements between employers and contractors.
Whether you need a quick solution, the site is the right choice.
Submit a task and get matched with the right person in minutes!
hire an assassin
This website offers you the chance to find professionals for short-term risky projects.
Clients may quickly schedule help for unique situations.
All workers have expertise in executing sensitive operations.
hitman-assassin-killer.com
This site offers safe connections between requesters and workers.
Whether you need immediate help, this website is the right choice.
Post your request and connect with a professional today!
hitman-assassin-killer.com
Our service makes it possible to get in touch with workers for one-time hazardous missions.
Users can quickly set up help for unique situations.
Each professional are qualified in dealing with complex jobs.
assassin for hire
Our platform guarantees discreet communication between users and specialists.
Whether you need immediate help, this website is the right choice.
Create a job and find a fit with a professional in minutes!
hitman-assassin-killer.com
Our service makes it possible to connect with workers for one-time dangerous missions.
You can easily request support for unique operations.
All contractors are trained in executing intense jobs.
rent a killer
This service provides secure interactions between employers and contractors.
For those needing immediate help, this platform is the perfect place.
Post your request and match with a skilled worker in minutes!
hire an assassin
This platform offers you the chance to find experts for one-time risky projects.
Users can securely schedule services for specialized operations.
All listed individuals are experienced in dealing with sensitive tasks.
assassin for hire
The website provides safe communication between users and freelancers.
Whether you need urgent assistance, the site is ready to help.
Submit a task and find a fit with a professional today!
hitman-assassin-killer.com
This website offers you the chance to get in touch with experts for temporary risky jobs.
Clients may easily request support for unique needs.
All contractors are qualified in handling critical tasks.
hitman-assassin-killer.com
The website ensures secure communication between users and specialists.
If you require immediate help, the site is here for you.
List your task and get matched with an expert now!
rent a hitman
This platform makes it possible to find experts for temporary risky tasks.
Clients may easily request services for specialized needs.
Each professional have expertise in dealing with sensitive tasks.
hire an assassin
Our platform ensures safe communication between clients and freelancers.
If you require immediate help, our service is the right choice.
Create a job and get matched with the right person instantly!
hitman for hire
This platform offers you the chance to find specialists for temporary hazardous jobs.
Users can securely request assistance for particular situations.
All contractors have expertise in executing sensitive activities.
rent a killer
This service provides private arrangements between employers and freelancers.
Whether you need immediate help, this platform is here for you.
Post your request and get matched with a skilled worker now!
rent a hitman
Our service makes it possible to get in touch with workers for short-term dangerous projects.
Visitors are able to securely arrange assistance for unique needs.
Each professional are qualified in managing sensitive activities.
killer for hire
This site guarantees discreet arrangements between employers and contractors.
If you require fast support, this website is ready to help.
Submit a task and match with a professional today!
hitman-assassin-killer.com
Our service lets you get in touch with experts for occasional high-risk missions.
You can efficiently request assistance for specialized needs.
All listed individuals are qualified in executing sensitive activities.
killer for hire
Our platform guarantees private interactions between requesters and specialists.
When you need fast support, this platform is here for you.
Create a job and get matched with a professional in minutes!
assumi assassino
La nostra piattaforma rende possibile l’ingaggio di operatori per incarichi rischiosi.
I clienti possono scegliere candidati qualificati per missioni singole.
Ogni candidato sono selezionati con cura.
ordina omicidio
Sul sito è possibile ottenere informazioni dettagliate prima della selezione.
La qualità è un nostro valore fondamentale.
Contattateci oggi stesso per trovare il supporto necessario!
ordina omicidio l'uccisione
La nostra piattaforma consente l’assunzione di lavoratori per incarichi rischiosi.
I clienti possono selezionare professionisti specializzati per lavori una tantum.
Le persone disponibili sono valutati secondo criteri di sicurezza.
assumi assassino
Sul sito è possibile consultare disponibilità prima della selezione.
La fiducia è al centro del nostro servizio.
Esplorate le offerte oggi stesso per portare a termine il vostro progetto!
assumere un killer
Il nostro servizio consente la selezione di professionisti per compiti delicati.
Gli utenti possono scegliere candidati qualificati per incarichi occasionali.
Le persone disponibili sono selezionati con attenzione.
assumi assassino
Sul sito è possibile visualizzare profili prima di assumere.
La fiducia è un nostro impegno.
Sfogliate i profili oggi stesso per portare a termine il vostro progetto!
ordina omicidio
Il nostro servizio offre l’ingaggio di persone per incarichi rischiosi.
Gli interessati possono selezionare operatori competenti per incarichi occasionali.
Ogni candidato sono selezionati con cura.
sonsofanarchy-italia.com
Utilizzando il servizio è possibile consultare disponibilità prima della scelta.
La fiducia continua a essere un nostro impegno.
Sfogliate i profili oggi stesso per trovare il supporto necessario!
sonsofanarchy-italia.com
La nostra piattaforma rende possibile l’ingaggio di lavoratori per lavori pericolosi.
Gli utenti possono ingaggiare professionisti specializzati per operazioni isolate.
Tutti i lavoratori sono valutati con attenzione.
sonsofanarchy-italia.com
Sul sito è possibile visualizzare profili prima di assumere.
La qualità resta un nostro valore fondamentale.
Iniziate la ricerca oggi stesso per affrontare ogni sfida in sicurezza!
ordina l'uccisione
Questa pagina consente il reclutamento di professionisti per incarichi rischiosi.
I clienti possono selezionare operatori competenti per operazioni isolate.
Ogni candidato vengono scelti con attenzione.
sonsofanarchy-italia.com
Con il nostro aiuto è possibile leggere recensioni prima di procedere.
La qualità resta un nostro impegno.
Contattateci oggi stesso per ottenere aiuto specializzato!
ordina l'uccisione
Questo sito offre l’assunzione di lavoratori per compiti delicati.
I clienti possono selezionare professionisti specializzati per operazioni isolate.
Tutti i lavoratori sono valutati con attenzione.
sonsofanarchy-italia.com
Utilizzando il servizio è possibile visualizzare profili prima della selezione.
La qualità resta al centro del nostro servizio.
Contattateci oggi stesso per ottenere aiuto specializzato!
assumere un killer
Questa pagina consente l’assunzione di operatori per lavori pericolosi.
Gli interessati possono trovare esperti affidabili per missioni singole.
Gli operatori proposti vengono scelti con cura.
ordina omicidio l’uccisione
Utilizzando il servizio è possibile ottenere informazioni dettagliate prima di procedere.
La sicurezza rimane un nostro impegno.
Sfogliate i profili oggi stesso per ottenere aiuto specializzato!
assumere un killer
Questa pagina consente l’assunzione di lavoratori per compiti delicati.
I clienti possono scegliere esperti affidabili per operazioni isolate.
Gli operatori proposti sono valutati secondo criteri di sicurezza.
ordina omicidio l’uccisione
Attraverso il portale è possibile ottenere informazioni dettagliate prima della scelta.
La sicurezza rimane un nostro valore fondamentale.
Sfogliate i profili oggi stesso per affrontare ogni sfida in sicurezza!
assumere un killer
Il nostro servizio permette il reclutamento di lavoratori per attività a rischio.
Chi cerca aiuto possono ingaggiare candidati qualificati per incarichi occasionali.
Le persone disponibili sono valutati con cura.
ordina omicidio
Attraverso il portale è possibile leggere recensioni prima di assumere.
La fiducia è la nostra priorità.
Iniziate la ricerca oggi stesso per trovare il supporto necessario!
sonsofanarchy-italia.com
Il nostro servizio rende possibile il reclutamento di lavoratori per attività a rischio.
I clienti possono ingaggiare candidati qualificati per incarichi occasionali.
Tutti i lavoratori vengono scelti con attenzione.
ordina omicidio l’uccisione
Con il nostro aiuto è possibile leggere recensioni prima della selezione.
La fiducia continua a essere al centro del nostro servizio.
Contattateci oggi stesso per affrontare ogni sfida in sicurezza!
ordina omicidio
Questo sito rende possibile l’assunzione di professionisti per compiti delicati.
Gli interessati possono scegliere candidati qualificati per missioni singole.
Tutti i lavoratori vengono scelti con attenzione.
ordina omicidio l’uccisione
Utilizzando il servizio è possibile leggere recensioni prima di assumere.
La qualità è un nostro valore fondamentale.
Esplorate le offerte oggi stesso per ottenere aiuto specializzato!
StevenBog
Greetings, followers of fun !
Funny text jokes for adults for any chat – п»їhttps://jokesforadults.guru/ joke adults
May you enjoy incredible unique witticisms !
Sidneyinide
Greetings, strategists of laughter !
Dad jokes for adults with a naughty twist – п»їhttps://jokesforadults.guru/ adult joke
May you enjoy incredible successful roasts !
pornhub[SwygcyruurcohpYC,2,5]
Безопасный досуг — это минимизирование рисков для игроков , включая саморегуляцию поведения.
Рекомендуется планировать бюджет , чтобы не превышать допустимые расходы .
Воспользуйтесь функциями временной блокировки, чтобы ограничить доступ в случае чрезмерного увлечения .
Доступ к ресурсам включает горячие линии , где можно получить помощь при трудных ситуациях.
Играйте с друзьями , чтобы сохранять социальный контакт , ведь семейная атмосфера делают процесс безопасным.
1xbet
Проверяйте условия платформы: лицензия оператора гарантирует защиту данных.
авиатор играть[SwygcyruurcohpYC,2,5]
Осознанное участие — это снижение негативных последствий для игроков , включая саморегуляцию поведения.
Рекомендуется устанавливать финансовые границы, чтобы не превышать допустимые расходы .
Воспользуйтесь функциями самоисключения , чтобы приостановить активность в случае потери контроля.
Поддержка игроков включает консультации специалистов, где можно получить помощь при трудных ситуациях.
Играйте с друзьями , чтобы избегать изоляции, ведь совместные развлечения делают процесс безопасным.
авиатор слот
Проверяйте условия платформы: сертификация оператора гарантирует защиту данных.
pornhub[SwygcyruurcohpYC,2,5]
В нашей коллекции представлены авторские видеоматериалы девушек , отобранные с профессиональным подходом.
Контент включает архивные съемки, редкие материалы, тематические подборки для различных предпочтений .
Материалы проверяются перед публикацией, чтобы гарантировать качество и актуальность .
lesbian photos
Для удобства посетителей добавлены фильтры по стилю , возрастным группам .
Сайт гарантирует конфиденциальность и соблюдение лицензий согласно правовым требованиям.
casino[SwygcyruurcohpYC,2,5]
На этом сайте доступны частные фотографии моделей, созданные с вниманием к деталям .
Контент включает архивные съемки, редкие материалы, тематические подборки для различных предпочтений .
Все данные проверяются перед публикацией, чтобы соответствовать стандартам и актуальность .
pornhub
Чтобы упростить поиск пользователей добавлены фильтры по стилю , параметрам моделей.
Платформа соблюдает конфиденциальность и соблюдение лицензий согласно международным нормам .
gay photos[SwygcyruurcohpYC,2,5]
На этом сайте представлены частные фотографии моделей, созданные с вниманием к деталям .
Контент включает архивные съемки, эксклюзивные кадры , тематические подборки для различных предпочтений .
Все данные модерируются перед публикацией, чтобы соответствовать стандартам и актуальность .
onlyfans
Чтобы упростить поиск пользователей добавлены фильтры по стилю , возрастным группам .
Платформа соблюдает конфиденциальность и защиту авторских прав согласно правовым требованиям.
suck[SwygcyruurcohpYC,2,5]
В нашей коллекции представлены частные фотографии моделей, отобранные с вниманием к деталям .
Контент включает архивные съемки, редкие материалы, тематические подборки для узких интересов.
Материалы проверяются перед публикацией, чтобы соответствовать стандартам и безопасность просмотра.
частное видео
Для удобства пользователей добавлены категории жанров, параметрам моделей.
Платформа соблюдает конфиденциальность и защиту авторских прав согласно правовым требованиям.
gay photos[SwygcyruurcohpYC,2,5]
На этом сайте доступны частные фотографии моделей, отобранные с вниманием к деталям .
Контент включает архивные съемки, редкие материалы, подписные серии для различных предпочтений .
Все данные модерируются перед публикацией, чтобы гарантировать качество и актуальность .
lesbian videos
Для удобства посетителей добавлены категории жанров, параметрам моделей.
Платформа соблюдает конфиденциальность и соблюдение лицензий согласно международным нормам .
слоты[SwygcyruurcohpYC,2,5]
Безопасный досуг — это минимизирование рисков для участников, включая саморегуляцию поведения.
Рекомендуется планировать бюджет , чтобы не превышать допустимые расходы .
Воспользуйтесь функциями самоисключения , чтобы ограничить доступ в случае потери контроля.
Доступ к ресурсам включает горячие линии , где можно обсудить проблемы при трудных ситуациях.
Играйте с друзьями , чтобы избегать изоляции, ведь семейная атмосфера делают процесс более контролируемым .
chicken road
Изучайте правила платформы: лицензия оператора гарантирует честные условия .
chicken road[SwygcyruurcohpYC,2,5]
Осознанное участие — это снижение негативных последствий для участников, включая установление лимитов .
Важно планировать бюджет , чтобы сохранять контроль над затратами.
Воспользуйтесь функциями самоисключения , чтобы ограничить доступ в случае потери контроля.
Доступ к ресурсам включает горячие линии , где можно обсудить проблемы при трудных ситуациях.
Участвуйте в компании, чтобы сохранять социальный контакт , ведь семейная атмосфера делают процесс безопасным.
1xbet
Изучайте правила платформы: лицензия оператора гарантирует честные условия .
chicken road play[SwygcyruurcohpYC,2,5]
В нашей коллекции доступны авторские видеоматериалы девушек , отобранные с вниманием к деталям .
Здесь можно найти архивные съемки, редкие материалы, подписные серии для узких интересов.
Все данные проверяются перед публикацией, чтобы гарантировать качество и безопасность просмотра.
threesome
Для удобства пользователей добавлены категории жанров, параметрам моделей.
Сайт гарантирует конфиденциальность и защиту авторских прав согласно международным нормам .
слоты играть[SwygcyruurcohpYC,2,5]
В нашей коллекции представлены авторские видеоматериалы девушек , отобранные с профессиональным подходом.
Контент включает архивные съемки, редкие материалы, тематические подборки для узких интересов.
Материалы проверяются перед публикацией, чтобы гарантировать качество и актуальность .
gay videos
Чтобы упростить поиск посетителей добавлены фильтры по стилю , возрастным группам .
Сайт гарантирует конфиденциальность и соблюдение лицензий согласно международным нормам .
казино играть[SwygcyruurcohpYC,2,5]
На этом сайте доступны авторские видеоматериалы моделей, созданные с вниманием к деталям .
Контент включает архивные съемки, эксклюзивные кадры , подписные серии для узких интересов.
Материалы модерируются перед публикацией, чтобы гарантировать качество и безопасность просмотра.
cuckold
Чтобы упростить поиск пользователей добавлены фильтры по стилю , возрастным группам .
Платформа соблюдает конфиденциальность и соблюдение лицензий согласно международным нормам .
RamonSoign
Этот обзорный материал предоставляет информационно насыщенные данные, касающиеся актуальных тем. Мы стремимся сделать информацию доступной и структурированной, чтобы читатели могли легко ориентироваться в наших выводах. Познайте новое с нашим обзором!
Подробнее можно узнать тут – https://vyvod-iz-zapoya-1.ru/
Richarddum
При выборе компании для квартирного переезда важно проверять её лицензирование и репутацию на рынке.
Изучите отзывы клиентов или рейтинги в интернете, чтобы оценить профессионализм исполнителя.
Сравните цены , учитывая объём вещей, сезонность и услуги упаковки.
https://service-core.com.ua/forum/post21611.html#p21611
Убедитесь наличия гарантий сохранности имущества и уточните условия компенсации в случае повреждений.
Оцените уровень сервиса: оперативность ответов, детализацию договора.
Проверьте, есть ли специализированные грузчики и упаковочные материалы для безопасной транспортировки.
Richarddum
При выборе компании для квартирного перевозки важно учитывать её лицензирование и репутацию на рынке.
Проверьте отзывы клиентов или рейтинги в интернете, чтобы оценить надёжность исполнителя.
Уточните стоимость услуг, учитывая расстояние перевозки , сезонность и дополнительные опции .
https://odessamama.net/forum.php?mod=viewthread&tid=380099&extra=
Требуйте наличия гарантий сохранности имущества и запросите детали компенсации в случае повреждений.
Оцените уровень сервиса: оперативность ответов, детализацию договора.
Узнайте, используются ли специализированные грузчики и упаковочные материалы для безопасной транспортировки.
Richarddum
При выборе компании для квартирного переезда важно учитывать её наличие страховки и репутацию на рынке.
Проверьте отзывы клиентов или рейтинги в интернете, чтобы оценить надёжность исполнителя.
Уточните стоимость услуг, учитывая объём вещей, сезонность и дополнительные опции .
https://www.freeboard.com.ua/forum/viewtopic.php?pid=999959#p999959
Убедитесь наличия гарантий сохранности имущества и уточните условия компенсации в случае повреждений.
Оцените уровень сервиса: дружелюбие сотрудников , гибкость графика .
Проверьте, есть ли специализированные автомобили и упаковочные материалы для безопасной транспортировки.
Richarddum
Подбирая компании для квартирного перевозки важно проверять её наличие страховки и опыт работы .
Проверьте отзывы клиентов или рейтинги в интернете, чтобы оценить профессионализм исполнителя.
Сравните цены , учитывая объём вещей, сезонность и услуги упаковки.
https://odessamama.net/forum.php?mod=viewthread&tid=380099&extra=
Требуйте наличия страхового полиса и запросите детали компенсации в случае повреждений.
Оцените уровень сервиса: дружелюбие сотрудников , гибкость графика .
Узнайте, используются ли специализированные автомобили и упаковочные материалы для безопасной транспортировки.
Richarddum
Подбирая компании для квартирного перевозки важно проверять её наличие страховки и опыт работы .
Проверьте отзывы клиентов или рейтинги в интернете, чтобы оценить профессионализм исполнителя.
Уточните стоимость услуг, учитывая объём вещей, сезонность и услуги упаковки.
https://abyua.forum24.ru/?1-13-0-00000024-000-0-0-1745438159
Требуйте наличия страхового полиса и уточните условия компенсации в случае повреждений.
Обратите внимание уровень сервиса: оперативность ответов, детализацию договора.
Проверьте, есть ли специализированные грузчики и упаковочные материалы для безопасной транспортировки.
Richarddum
При выборе компании для квартирного переезда важно проверять её наличие страховки и репутацию на рынке.
Изучите отзывы клиентов или рейтинги в интернете, чтобы оценить профессионализм исполнителя.
Сравните цены , учитывая объём вещей, сезонность и дополнительные опции .
https://donbassforum.net/flud/topic-t3090102.html
Требуйте наличия страхового полиса и запросите детали компенсации в случае повреждений.
Обратите внимание уровень сервиса: оперативность ответов, детализацию договора.
Проверьте, есть ли специализированные автомобили и защитные технологии для безопасной транспортировки.
Richarddum
При выборе компании для квартирного перевозки важно учитывать её лицензирование и опыт работы .
Проверьте отзывы клиентов или рекомендации знакомых , чтобы оценить надёжность исполнителя.
Сравните цены , учитывая расстояние перевозки , сезонность и дополнительные опции .
http://avenue1416.kiev.ua/forum/t/4306/
Убедитесь наличия страхового полиса и уточните условия компенсации в случае повреждений.
Оцените уровень сервиса: дружелюбие сотрудников , детализацию договора.
Узнайте, используются ли специализированные автомобили и защитные технологии для безопасной транспортировки.
Richarddum
Подбирая компании для квартирного переезда важно проверять её наличие страховки и репутацию на рынке.
Проверьте отзывы клиентов или рейтинги в интернете, чтобы оценить надёжность исполнителя.
Уточните стоимость услуг, учитывая объём вещей, сезонность и дополнительные опции .
https://www.kinofilms.ua/forum/t/5190510/
Убедитесь наличия страхового полиса и уточните условия компенсации в случае повреждений.
Оцените уровень сервиса: дружелюбие сотрудников , детализацию договора.
Проверьте, есть ли специализированные автомобили и упаковочные материалы для безопасной транспортировки.
Richarddum
Подбирая компании для квартирного перевозки важно учитывать её лицензирование и репутацию на рынке.
Проверьте отзывы клиентов или рейтинги в интернете, чтобы оценить надёжность исполнителя.
Уточните стоимость услуг, учитывая расстояние перевозки , сезонность и дополнительные опции .
https://forua.forum24.ru/?1-2-0-00000137-000-0-0-1745438343
Убедитесь наличия гарантий сохранности имущества и уточните условия компенсации в случае повреждений.
Обратите внимание уровень сервиса: оперативность ответов, гибкость графика .
Проверьте, есть ли специализированные автомобили и защитные технологии для безопасной транспортировки.
Richarddum
При выборе компании для квартирного переезда важно учитывать её наличие страховки и репутацию на рынке.
Проверьте отзывы клиентов или рейтинги в интернете, чтобы оценить надёжность исполнителя.
Сравните цены , учитывая объём вещей, сезонность и дополнительные опции .
https://odessamama.net/forum.php?mod=viewthread&tid=380099&extra=
Убедитесь наличия страхового полиса и уточните условия компенсации в случае повреждений.
Обратите внимание уровень сервиса: оперативность ответов, гибкость графика .
Проверьте, есть ли специализированные автомобили и упаковочные материалы для безопасной транспортировки.
Richarddum
При выборе компании для квартирного переезда важно проверять её лицензирование и опыт работы .
Проверьте отзывы клиентов или рекомендации знакомых , чтобы оценить надёжность исполнителя.
Уточните стоимость услуг, учитывая объём вещей, сезонность и дополнительные опции .
http://www.vipautokiev.com/forum/viewthread.php?forum_id=13&thread_id=1053&pid=2659#post_2659
Убедитесь наличия страхового полиса и запросите детали компенсации в случае повреждений.
Обратите внимание уровень сервиса: дружелюбие сотрудников , детализацию договора.
Проверьте, есть ли специализированные грузчики и упаковочные материалы для безопасной транспортировки.
Richarddum
При выборе компании для квартирного переезда важно проверять её лицензирование и опыт работы .
Проверьте отзывы клиентов или рейтинги в интернете, чтобы оценить профессионализм исполнителя.
Сравните цены , учитывая объём вещей, сезонность и услуги упаковки.
http://forum.omnicomm.pro/index.php/topic,133738.0.html
Требуйте наличия гарантий сохранности имущества и уточните условия компенсации в случае повреждений.
Обратите внимание уровень сервиса: оперативность ответов, детализацию договора.
Проверьте, есть ли специализированные автомобили и защитные технологии для безопасной транспортировки.
RichardFooro
Online platforms offer a modern way to connect people globally, combining intuitive tools like photo verification and interest-based filters .
Core functionalities include secure messaging , geolocation tracking , and personalized profiles to streamline connections.
Smart matching systems analyze behavioral patterns to suggest compatible matches, while privacy settings ensure safety .
https://globalwebs.biz/dating/appeal-of-taboo-in-adult-entertainment/
Many platforms offer freemium models with enhanced visibility, such as priority in search results, alongside profile performance analytics.
Looking for casual chats , these sites adapt to user goals, leveraging AI-driven recommendations to foster meaningful bonds.
RichardFooro
Dating websites offer a modern way to connect people globally, combining intuitive tools like photo verification and interest-based filters .
Core functionalities include video chat options, social media integration, and detailed user bios to streamline connections.
Advanced algorithms analyze behavioral patterns to suggest potential partners , while privacy settings ensure safety .
https://zonia4sd2.com/dating/power-exchange-in-adult-entertainment/
Leading apps offer premium subscriptions with enhanced visibility, such as unlimited swipes , alongside profile performance analytics.
Whether seeking long-term relationships, these sites cater to diverse needs , leveraging AI-driven recommendations to foster meaningful bonds.
RichardFooro
Dating websites provide a innovative approach to meet people globally, combining user-friendly features like profile galleries and compatibility criteria.
Key elements include video chat options, social media integration, and detailed user bios to enhance interactions .
Smart matching systems analyze preferences to suggest potential partners , while account verification ensure safety .
https://slotdana.biz/dating/psychology-behind-gangbang-fantasies/
Many platforms offer premium subscriptions with enhanced visibility, such as priority in search results, alongside real-time notifications .
Looking for casual chats , these sites adapt to user goals, leveraging community-driven networks to optimize success rates .
RichardFooro
Dating websites offer a innovative approach to meet people globally, combining intuitive tools like photo verification and interest-based filters .
Key elements include video chat options, geolocation tracking , and personalized profiles to streamline connections.
Advanced algorithms analyze preferences to suggest compatible matches, while privacy settings ensure trustworthiness.
https://zonia4sd2.com/dating/power-exchange-in-adult-entertainment/
Leading apps offer freemium models with exclusive benefits , such as unlimited swipes , alongside profile performance analytics.
Looking for casual chats , these sites cater to diverse needs , leveraging AI-driven recommendations to optimize success rates .
RichardFooro
Dating websites provide a modern way to connect people globally, combining user-friendly features like photo verification and compatibility criteria.
Core functionalities include secure messaging , social media integration, and detailed user bios to enhance interactions .
Smart matching systems analyze behavioral patterns to suggest potential partners , while account verification ensure safety .
https://rampy.club/dating/the-shift-toward-authentic-adult-content/
Leading apps offer premium subscriptions with exclusive benefits , such as priority in search results, alongside real-time notifications .
Whether seeking long-term relationships, these sites cater to diverse needs , leveraging community-driven networks to optimize success rates .
RichardFooro
Dating websites offer a innovative approach to meet people globally, combining user-friendly features like profile galleries and interest-based filters .
Key elements include secure messaging , geolocation tracking , and personalized profiles to enhance interactions .
Smart matching systems analyze behavioral patterns to suggest potential partners , while account verification ensure trustworthiness.
https://astro-1.org/dating/thrill-of-anonymity-in-modern-adult-content/
Leading apps offer premium subscriptions with enhanced visibility, such as priority in search results, alongside real-time notifications .
Whether seeking long-term relationships, these sites adapt to user goals, leveraging AI-driven recommendations to optimize success rates .
RichardFooro
Online platforms provide a innovative approach to connect people globally, combining user-friendly features like photo verification and compatibility criteria.
Core functionalities include secure messaging , geolocation tracking , and detailed user bios to streamline connections.
Smart matching systems analyze behavioral patterns to suggest potential partners , while privacy settings ensure trustworthiness.
https://globalwebs.biz/dating/appeal-of-taboo-in-adult-entertainment/
Leading apps offer freemium models with enhanced visibility, such as priority in search results, alongside real-time notifications .
Looking for casual chats , these sites adapt to user goals, leveraging community-driven networks to optimize success rates .
RichardFooro
Dating websites provide a modern way to connect people globally, combining user-friendly features like photo verification and interest-based filters .
Key elements include video chat options, geolocation tracking , and detailed user bios to enhance interactions .
Advanced algorithms analyze preferences to suggest compatible matches, while account verification ensure safety .
https://hetlovet.com/dating/from-curiosity-to-craving-the-fetish-revolution-in-porn/
Many platforms offer premium subscriptions with enhanced visibility, such as unlimited swipes , alongside profile performance analytics.
Looking for casual chats , these sites adapt to user goals, leveraging AI-driven recommendations to optimize success rates .
RichardFooro
Matchmaking services provide a innovative approach to connect people globally, combining user-friendly features like photo verification and interest-based filters .
Key elements include video chat options, geolocation tracking , and detailed user bios to streamline connections.
Smart matching systems analyze behavioral patterns to suggest compatible matches, while account verification ensure safety .
https://wikidoc.info/dating/the-growing-popularity-of-mature-adult-content/
Leading apps offer freemium models with enhanced visibility, such as priority in search results, alongside profile performance analytics.
Whether seeking long-term relationships, these sites cater to diverse needs , leveraging AI-driven recommendations to foster meaningful bonds.
RichardFooro
Dating websites provide a modern way to meet people globally, combining intuitive tools like profile galleries and compatibility criteria.
Key elements include video chat options, social media integration, and personalized profiles to enhance interactions .
Smart matching systems analyze behavioral patterns to suggest potential partners , while account verification ensure safety .
https://iturdu.net/dating/understanding-the-dynamics-behind-the-cuckold-fantasy/
Many platforms offer freemium models with enhanced visibility, such as unlimited swipes , alongside real-time notifications .
Looking for casual chats , these sites cater to diverse needs , leveraging community-driven networks to optimize success rates .
KennethUneri
Биорезервуар — это водонепроницаемый резервуар, предназначенная для первичной обработки сточных вод .
Принцип действия заключается в том, что жидкость из дома поступает в бак , где твердые частицы оседают , а жиры и масла всплывают наверх .
Основные элементы: входная труба, бетонный резервуар, соединительный канал и почвенный фильтр для доочистки стоков.
http://midoma.ru/node/kupit-septik-v-moskve-nedorogo
Плюсы использования: экономичность, минимальное обслуживание и безопасность для окружающей среды при соблюдении норм.
Критично важно не перегружать систему , иначе неотделённые примеси попадут в грунт, вызывая загрязнение.
Материалы изготовления: бетонные блоки, пластиковые ёмкости и стекловолоконные модули для разных условий монтажа .
KennethUneri
Септик — это подземная ёмкость , предназначенная для первичной обработки сточных вод .
Система работает так: жидкость из дома направляется в ёмкость, где твердые частицы оседают , а жиры и масла всплывают наверх .
Основные элементы: входная труба, бетонный резервуар, соединительный канал и дренажное поле для дочистки воды .
https://mainbild.ru/forums/topic/septik-v-moskve-nedorogo/
Преимущества: экономичность, минимальное обслуживание и экологичность при соблюдении норм.
Критично важно контролировать объём стоков, иначе частично очищенная вода попадут в грунт, вызывая загрязнение.
Типы конструкций: бетонные блоки, полиэтиленовые резервуары и стекловолоконные модули для разных условий монтажа .
KennethUneri
Выгребная яма — это подземная ёмкость , предназначенная для первичной обработки сточных вод .
Система работает так: жидкость из дома поступает в бак , где формируется слой ила, а жиры и масла всплывают наверх .
Основные элементы: входная труба, бетонный резервуар, соединительный канал и дренажное поле для дочистки воды .
http://domstroim.teamforum.ru/viewtopic.php?f=2&t=14
Плюсы использования: экономичность, долговечность и экологичность при соблюдении норм.
Однако важно контролировать объём стоков, иначе неотделённые примеси попадут в грунт, вызывая загрязнение.
Типы конструкций: бетонные блоки, полиэтиленовые резервуары и стекловолоконные модули для индивидуальных нужд.
KennethUneri
Выгребная яма — это подземная ёмкость , предназначенная для сбора и частичной переработки отходов.
Система работает так: жидкость из дома направляется в ёмкость, где твердые частицы оседают , а жиры и масла собираются в верхнем слое.
В конструкцию входят входная труба, герметичный бак , соединительный канал и дренажное поле для доочистки стоков.
http://domkodeks.ru/question/kupit-septik-v-moskve-nedorogo
Плюсы использования: экономичность, минимальное обслуживание и безопасность для окружающей среды при соблюдении норм.
Однако важно контролировать объём стоков, иначе неотделённые примеси попадут в грунт, вызывая загрязнение.
Типы конструкций: бетонные блоки, пластиковые ёмкости и композитные баки для индивидуальных нужд.
KennethUneri
Выгребная яма — это водонепроницаемый резервуар, предназначенная для сбора и частичной переработки отходов.
Принцип действия заключается в том, что жидкость из дома направляется в ёмкость, где формируется слой ила, а жиры и масла всплывают наверх .
В конструкцию входят входная труба, герметичный бак , соединительный канал и почвенный фильтр для доочистки стоков.
https://richstone.by/forum/messages/forum1/message3970/2675-kupit-septik-v-moskve-nedorogo?result=new#message3970
Плюсы использования: экономичность, минимальное обслуживание и экологичность при соблюдении норм.
Однако важно не перегружать систему , иначе неотделённые примеси попадут в грунт, вызывая загрязнение.
Материалы изготовления: бетонные блоки, полиэтиленовые резервуары и стекловолоконные модули для разных условий монтажа .
KennethUneri
Выгребная яма — это подземная ёмкость , предназначенная для сбора и частичной переработки отходов.
Система работает так: жидкость из дома поступает в бак , где твердые частицы оседают , а жиры и масла собираются в верхнем слое.
В конструкцию входят входная труба, герметичный бак , соединительный канал и дренажное поле для дочистки воды .
https://cementdom.listbb.ru/viewtopic.php?f=2&t=14
Преимущества: экономичность, долговечность и экологичность при соблюдении норм.
Критично важно не перегружать систему , иначе частично очищенная вода попадут в грунт, вызывая загрязнение.
Типы конструкций: бетонные блоки, полиэтиленовые резервуары и стекловолоконные модули для индивидуальных нужд.
KennethUneri
Биорезервуар — это водонепроницаемый резервуар, предназначенная для сбора и частичной переработки отходов.
Система работает так: жидкость из дома поступает в бак , где твердые частицы оседают , а жиры и масла собираются в верхнем слое.
Основные элементы: входная труба, бетонный резервуар, соединительный канал и дренажное поле для доочистки стоков.
https://samelectrik.ru/forum/uslugi-i-predlozhenija/септик-в-москве-недорого#p2479
Преимущества: низкие затраты , минимальное обслуживание и экологичность при соблюдении норм.
Критично важно не перегружать систему , иначе неотделённые примеси попадут в грунт, вызывая загрязнение.
Типы конструкций: бетонные блоки, полиэтиленовые резервуары и композитные баки для индивидуальных нужд.
KennethUneri
Выгребная яма — это водонепроницаемый резервуар, предназначенная для первичной обработки сточных вод .
Принцип действия заключается в том, что жидкость из дома поступает в бак , где твердые частицы оседают , а жиры и масла собираются в верхнем слое.
Основные элементы: входная труба, герметичный бак , соединительный канал и дренажное поле для дочистки воды .
https://gidro2000.com/forum-gidro/user/36178/
Преимущества: экономичность, долговечность и безопасность для окружающей среды при соблюдении норм.
Критично важно не перегружать систему , иначе частично очищенная вода попадут в грунт, вызывая загрязнение.
Материалы изготовления: бетонные блоки, полиэтиленовые резервуары и стекловолоконные модули для разных условий монтажа .
KennethUneri
Септик — это подземная ёмкость , предназначенная для первичной обработки сточных вод .
Система работает так: жидкость из дома направляется в ёмкость, где твердые частицы оседают , а жиры и масла всплывают наверх .
Основные элементы: входная труба, герметичный бак , соединительный канал и дренажное поле для дочистки воды .
https://samelectrik.ru/forum/uslugi-i-predlozhenija/септик-в-москве-недорого#p2479
Преимущества: экономичность, минимальное обслуживание и экологичность при соблюдении норм.
Критично важно не перегружать систему , иначе неотделённые примеси попадут в грунт, вызывая загрязнение.
Материалы изготовления: бетонные блоки, полиэтиленовые резервуары и композитные баки для разных условий монтажа .
KennethUneri
Выгребная яма — это водонепроницаемый резервуар, предназначенная для сбора и частичной переработки отходов.
Принцип действия заключается в том, что жидкость из дома поступает в бак , где формируется слой ила, а жиры и масла всплывают наверх .
Основные элементы: входная труба, герметичный бак , соединительный канал и дренажное поле для доочистки стоков.
https://climat-cold.ru/forum/user/4875/
Преимущества: экономичность, долговечность и безопасность для окружающей среды при соблюдении норм.
Критично важно не перегружать систему , иначе частично очищенная вода попадут в грунт, вызывая загрязнение.
Типы конструкций: бетонные блоки, полиэтиленовые резервуары и стекловолоконные модули для индивидуальных нужд.
KennethUneri
Биорезервуар — это водонепроницаемый резервуар, предназначенная для сбора и частичной переработки отходов.
Принцип действия заключается в том, что жидкость из дома направляется в ёмкость, где формируется слой ила, а жиры и масла собираются в верхнем слое.
В конструкцию входят входная труба, герметичный бак , соединительный канал и почвенный фильтр для дочистки воды .
http://s-nip.ru/forums/?Subdiv_ID=8&Topic_ID=549
Преимущества: экономичность, минимальное обслуживание и безопасность для окружающей среды при соблюдении норм.
Критично важно контролировать объём стоков, иначе частично очищенная вода попадут в грунт, вызывая загрязнение.
Материалы изготовления: бетонные блоки, пластиковые ёмкости и композитные баки для индивидуальных нужд.
KennethUneri
Септик — это водонепроницаемый резервуар, предназначенная для сбора и частичной переработки отходов.
Система работает так: жидкость из дома поступает в бак , где формируется слой ила, а жиры и масла всплывают наверх .
Основные элементы: входная труба, бетонный резервуар, соединительный канал и почвенный фильтр для дочистки воды .
http://introsystems.ru/component/kunena/suggestion-box/40444-septik-v-moskve-nedorogo
Плюсы использования: низкие затраты , минимальное обслуживание и безопасность для окружающей среды при соблюдении норм.
Критично важно контролировать объём стоков, иначе частично очищенная вода попадут в грунт, вызывая загрязнение.
Типы конструкций: бетонные блоки, полиэтиленовые резервуары и композитные баки для индивидуальных нужд.
KennethUneri
Выгребная яма — это подземная ёмкость , предназначенная для сбора и частичной переработки отходов.
Принцип действия заключается в том, что жидкость из дома поступает в бак , где формируется слой ила, а жиры и масла собираются в верхнем слое.
Основные элементы: входная труба, бетонный резервуар, соединительный канал и почвенный фильтр для дочистки воды .
https://rukamimaster.ru/forums/topic/септик-в-москве-недорого/
Плюсы использования: экономичность, долговечность и безопасность для окружающей среды при соблюдении норм.
Критично важно контролировать объём стоков, иначе частично очищенная вода попадут в грунт, вызывая загрязнение.
Типы конструкций: бетонные блоки, полиэтиленовые резервуары и стекловолоконные модули для разных условий монтажа .
KennethUneri
Септик — это водонепроницаемый резервуар, предназначенная для сбора и частичной переработки отходов.
Принцип действия заключается в том, что жидкость из дома направляется в ёмкость, где формируется слой ила, а жиры и масла собираются в верхнем слое.
Основные элементы: входная труба, бетонный резервуар, соединительный канал и дренажное поле для дочистки воды .
https://mainbild.ru/forums/topic/septik-v-moskve-nedorogo/
Плюсы использования: низкие затраты , долговечность и безопасность для окружающей среды при соблюдении норм.
Однако важно контролировать объём стоков, иначе неотделённые примеси попадут в грунт, вызывая загрязнение.
Материалы изготовления: бетонные блоки, пластиковые ёмкости и стекловолоконные модули для разных условий монтажа .
KennethUneri
Выгребная яма — это подземная ёмкость , предназначенная для сбора и частичной переработки отходов.
Принцип действия заключается в том, что жидкость из дома поступает в бак , где формируется слой ила, а жиры и масла всплывают наверх .
В конструкцию входят входная труба, бетонный резервуар, соединительный канал и почвенный фильтр для дочистки воды .
https://1f.spb.ru/post/29128/#p29128
Преимущества: экономичность, долговечность и экологичность при соблюдении норм.
Однако важно не перегружать систему , иначе неотделённые примеси попадут в грунт, вызывая загрязнение.
Материалы изготовления: бетонные блоки, пластиковые ёмкости и композитные баки для индивидуальных нужд.
KennethUneri
Выгребная яма — это водонепроницаемый резервуар, предназначенная для сбора и частичной переработки отходов.
Система работает так: жидкость из дома поступает в бак , где формируется слой ила, а жиры и масла собираются в верхнем слое.
В конструкцию входят входная труба, бетонный резервуар, соединительный канал и почвенный фильтр для дочистки воды .
https://pol-doma.com/forum/user/179824/
Плюсы использования: экономичность, минимальное обслуживание и экологичность при соблюдении норм.
Критично важно не перегружать систему , иначе частично очищенная вода попадут в грунт, вызывая загрязнение.
Материалы изготовления: бетонные блоки, полиэтиленовые резервуары и композитные баки для индивидуальных нужд.